SELECT HARVESTS
FUCHS Lubricates Almond Processor’s Global Growth
As the country’s largest almond producer, maximising uptime of its fleet of more than 800 farm machines is mission critical for Select Harvests' Operations & Maintenance Manager Mick Puleio. Puleio – who joined the ASX-listed company two years ago – is responsible for overseeing acquisitions and maintenance of a large mixed fleet comprising tractors, ATV’s, telehandlers, sprayers and specialised harvesters across more than 9,262 hectares (22,886 acres) of company owned and leased almond orchards located in Victoria, South Australia and NSW. He also oversees a central workshop, including machinery overhaul centre, as well as a warehouse that stocks all spare parts and consumables.
For Select Harvests, timing is crucial to maximising crop yield processed at its state-of-the-art processing facility at Carina West in Victoria, which has the capacity to process more than 30,000 metric tonnes (MT) of almonds in peak season for in-shell, kernel and value-added product sold both locally and globally. Harvest – which hit a record 28,250 MT in 2021 – occurs between February and April, when the nut is at an acceptable moisture level. Mechanical harvesting requires orchard floors to be clear of large weeds and swept of all foreign material. Shakers are used to vibrate the tree trunk, so the fruit (hull, shell and nut) falls to the orchard floor. After drying, they are swept into rows and picked up ready for storage.
“Everything is about timing, getting sprays on during the growing season, keeping the weeds out, etc. And coming into harvest we need to beat the weather … what makes us different to California (the world’s largest almond producer, accounting for 79 per cent of production in 2002/21) is they don’t see a lot of rain events. Here we’re getting a lot of rain events. “Machinery upkeep is therefore critical; the longer [the almonds] are on the ground, the more chance they have of rotting. It’s why we need to keep maintenance programs up to speed. And it’s why we choose certain products such as FUCHS,” he explains.
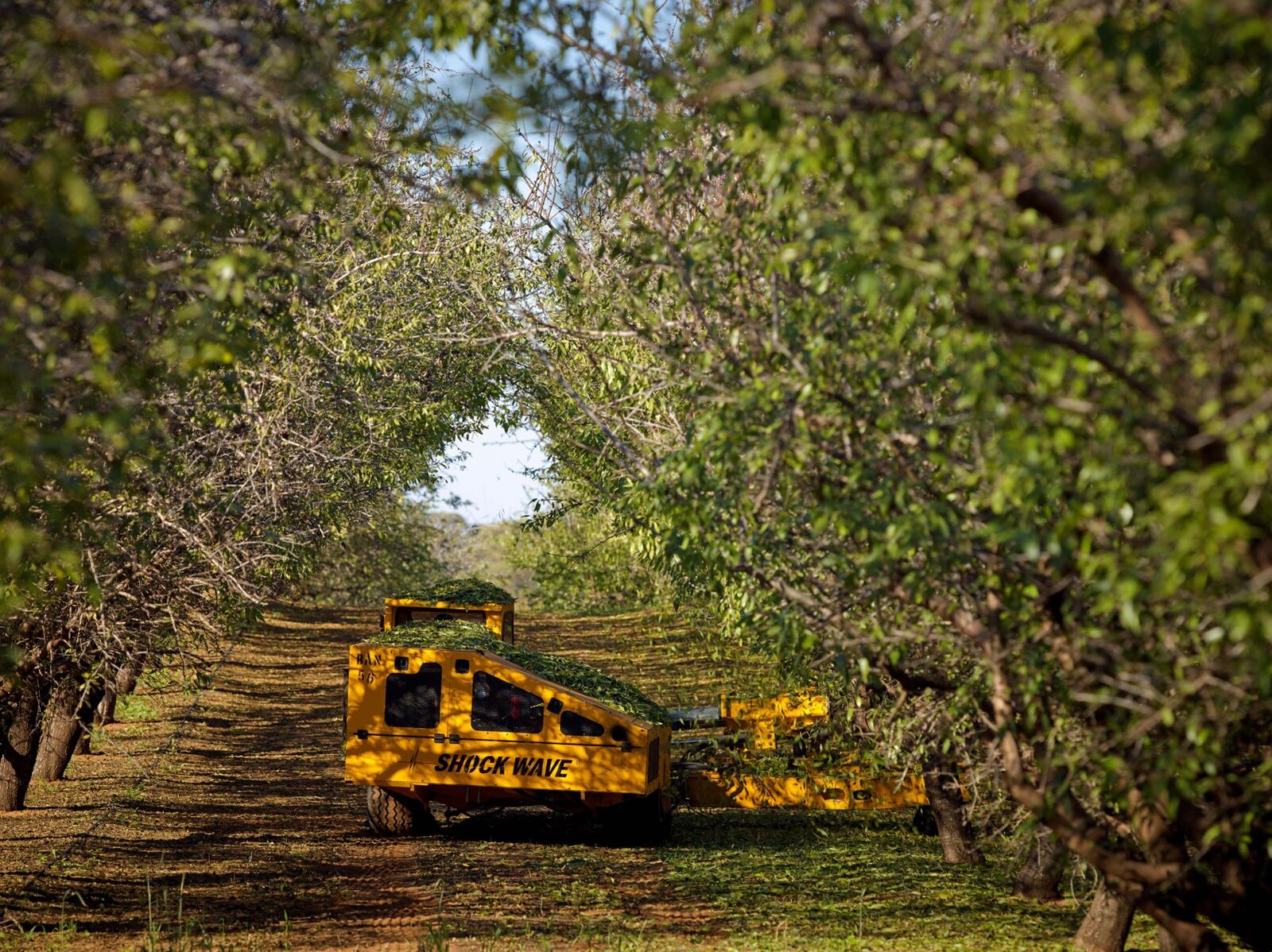
Select Harvests' specialised harvesting equipment require a new generation of higher-performing diesel engine oils
Select Harvests switched to FUCHS lubricants two years after Puleio joined the fast-growing business. Previously the company used a variety of brands. He made the decision to streamline to a single supplier. “There was too much variety. Once we put the tender out FUCHS were not only [price] competitive, but they ticked all the other boxes,” he says. "Quality [of the product] was [our] number one [requirement]. They also had a vast range of lubricants we required.” Importantly, Puleio points out that most of its specialised harvesting equipment is sourced out of California and compliant with Tier 4 emissions standards. These fuel-efficient diesel engines require a new generation of higher-performing diesel engine oils to protect them - CK-4 category oils. “When using certain machinery we need a certain grade of oil to meet the manufacturers’ specifications [for warranty purposes]. FUCHS gave us a 100 per cent guarantee to fully support us in this regard,” he says.
Select Harvests uses three FUCHS products: TITAN CARGO SAE 15W-40, a super high-performance engine oil especially suited to high-load commercial vehicle diesel engines, which carries many OEM approvals; RENOLIN B 68 HVI PLUS, a hydraulic and lubricating oil with a high viscosity index and additives to improve ageing stability, corrosion protection and wear protection during ambient temperatures; and ARGIFARM UTTO MP, which is a true multi-purpose oil for a vast range of farming equipment, suitable for use in transmissions and hydraulic systems with integrated wet brakes, clutches and differentials.
“The quality of their product and their service is second-to-none and the reliability of the brand is first-class,” Puleio says. “FUCHS is very price competitive, too, and they stand behind their product. In my time at Select Harvests we’ve never had a warranty problem against the oil but I know they back their product and their customer relationships are very important. “We’re putting FUCHS lubricants in 800 machines and 80 per cent of them would be running at the same time for anything up to four months at a time and we can do this because the product is reliable.” Customer service is also key, he adds. Puleio says the larger farms receive deliveries in 1,000-litre shuttles. Product is stored in the warehouse and generally ordered on a fortnightly basis.
“I’m in constant communication with Shane [Parker, FUCHS’ SA/NT Sales Manager] and this ensures they keep up with forecast deliveries,” he says.
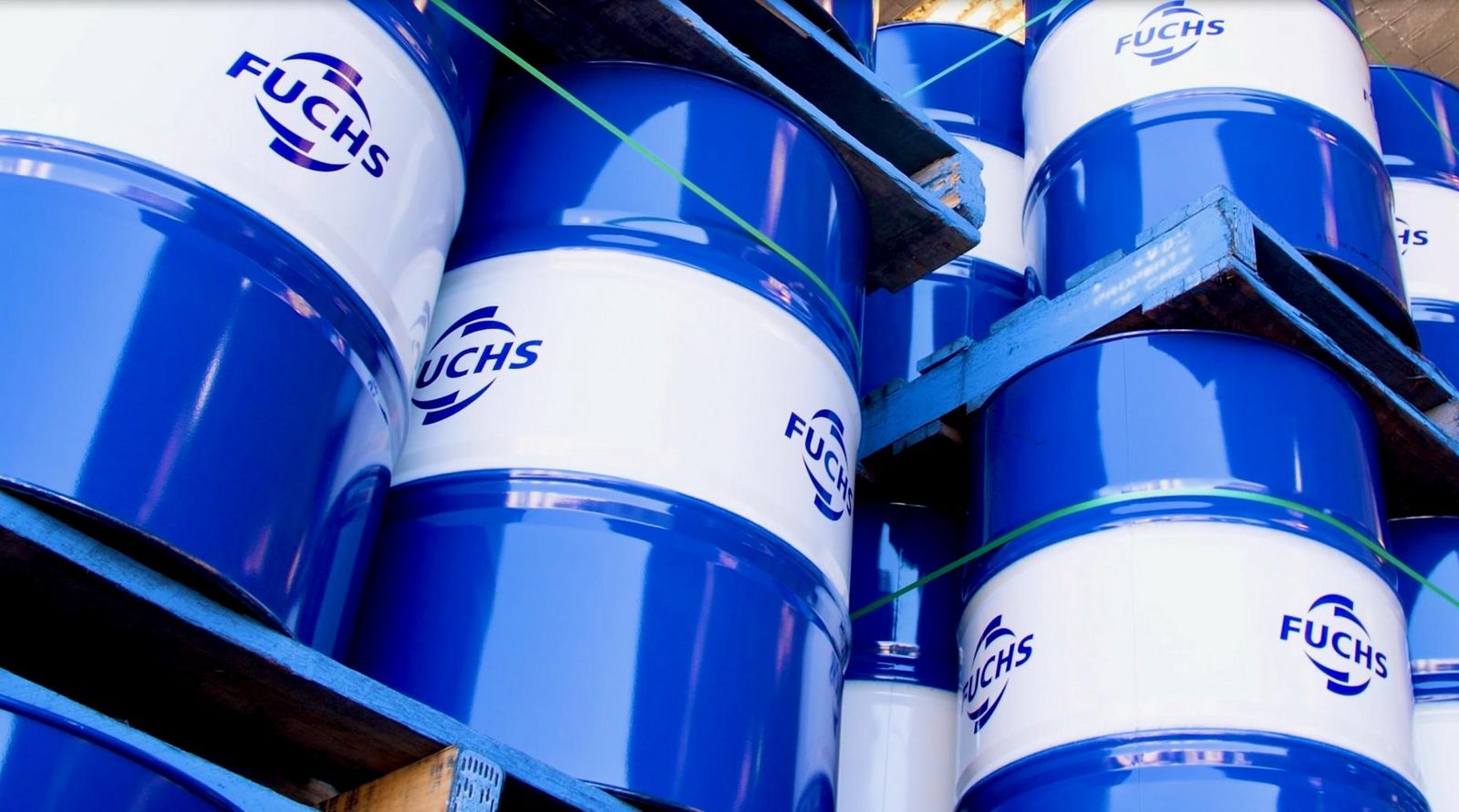
As the only major Australian lubricants company to still manufacture products locally, supporting “Australian made” was also an important consideration, Puleio adds. “From a business perspective we’re locally owned and operated, so the fact we’re supporting local businesses is something we pride ourselves on. To be able to support Australian-made products is huge,” he says. FUCHS Lubricants (Australasia) managing director Wayne Hoiles notes that while many of its competitors are moving overseas and are operating under an import model, “that’s not our strategy”.
After building and commissioning a state-of-the-art grease plant in Melbourne in 2009, and opening a regional Lubrication Laboratory and Technical Centre in 2011, in February 2018 FUCHS opened the doors of a 25,000-square-metre purpose-built plant in Beresfield [Newcastle], about 120km north-northeast of Sydney, to support business growth and customer service. “We need to have local infrastructure that can handle the requirements of Australia and New Zealand, so we are investing in infrastructure to provide a better service to our customers,” he says. “Our new site at Beresfield will allow us to increase the products and services we offer to our customers in this area as well as continue to distribute our products to other parts of Australia such as Queensland and Western Australia.”
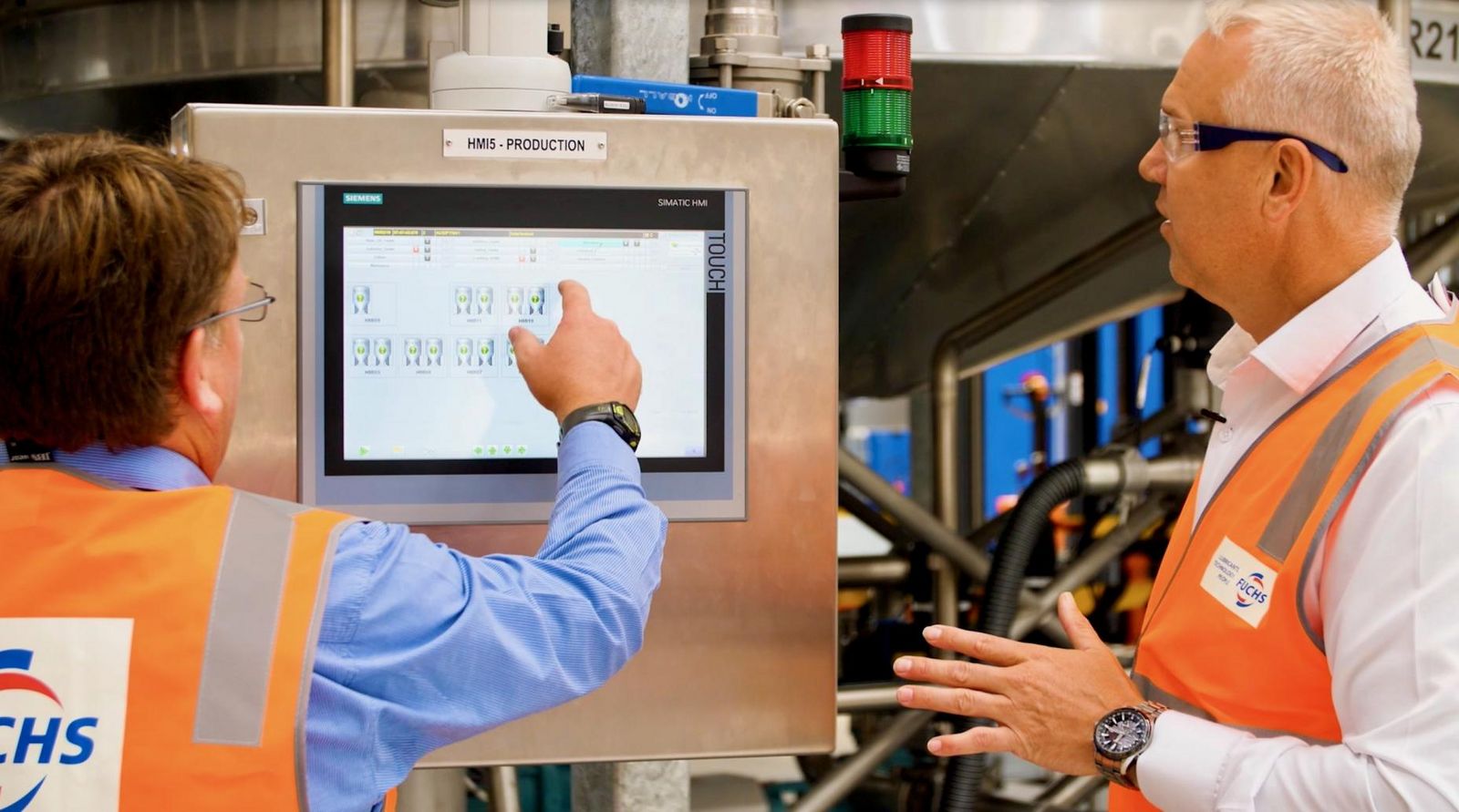
While that means the company is positioned to respond to the immediate needs of its customer, particularly in emergency situations, Hoiles says it also means jobs for Australians. Over 95 per cent of its products are made locally. “Beresfield will continue to house a range of our business functions including lubricant manufacturing, storage of bulk raw material, warehousing of finished product, a laboratory, and our sales and customer service department,” he says. To ensure the plant has the capacity to grow with the business, Beresfield has been built in a two-stage process, and it is upgradable at multiple levels. “We can increase the capacity of the plant at any point in time, and there is already space available for us to add new tanks or equipment along with an area that can double our warehouse space in the future,” Hoiles says
Source: farmbuy.com/post/fuchs-lubricantes-almond-porcessor-s-global-growth