WHAT MAKES A PRODUCT ENVIRONMENTALLY FRIENDLY?
Products should be environmentally friendly: cars, packaging, washing machines – and lubricants. One of the goals during production is to keep consumption of energy and raw materials as low as possible. However, is it only a good carbon footprint during the manufacturing process that counts when it comes to picking the best solution for the environment? We spoke to Stefan Fassbender, Director Components, Business Management EMEA – Fuel and Lubricant Solutions at BASF, and Wolfgang Bock, Head of Product Management Industrial Oils at FUCHS. The two of them believe the issue to be more complex.
Even though Stefan Fassbender and Wolfgang Bock work for two different companies, there is a clear rapport between them. They laugh and joke but never lose sight of their goal. “At the moment, evaluating the sustainability of products mainly focuses on production,” states Fassbender. “But this is only the half of it. We need a comprehensive analysis that looks at the environmental performance of a product across its entire lifetime, from manufacturing through use to disposal. We have now implemented this approach in a joint study with FUCHS. We want to set a new standard for the lubricant industry and to bring about a new way of thinking.”
LONGSTANDING DIALOG
FUCHS and BASF began an intensive dialog on the topic of sustainability back in 2015. “We have been buying additives for our lubricants from BASF for many years and cooperate closely for this reason alone. With the help of BASF's Sustainable Solution Steering® method, the BASF products are systematically examined in terms of sustainability for a whole range of markets and industries, and even we, as customers, are informed about potential risks – including those that affect evaluation and access with regard to the EU chemicals regulation REACH. This was the source of many intense discussions and led to close cooperation,” says Bock. “Regular conversations gradually gave rise to the idea of setting up a full-scale lifecycle analysis that stands up to scientific evaluation. The results should help us to reinforce our arguments for a comprehensive sustainability evaluation along the entire value chain with facts – for discussions with our customers, but also with associations and organizations.”
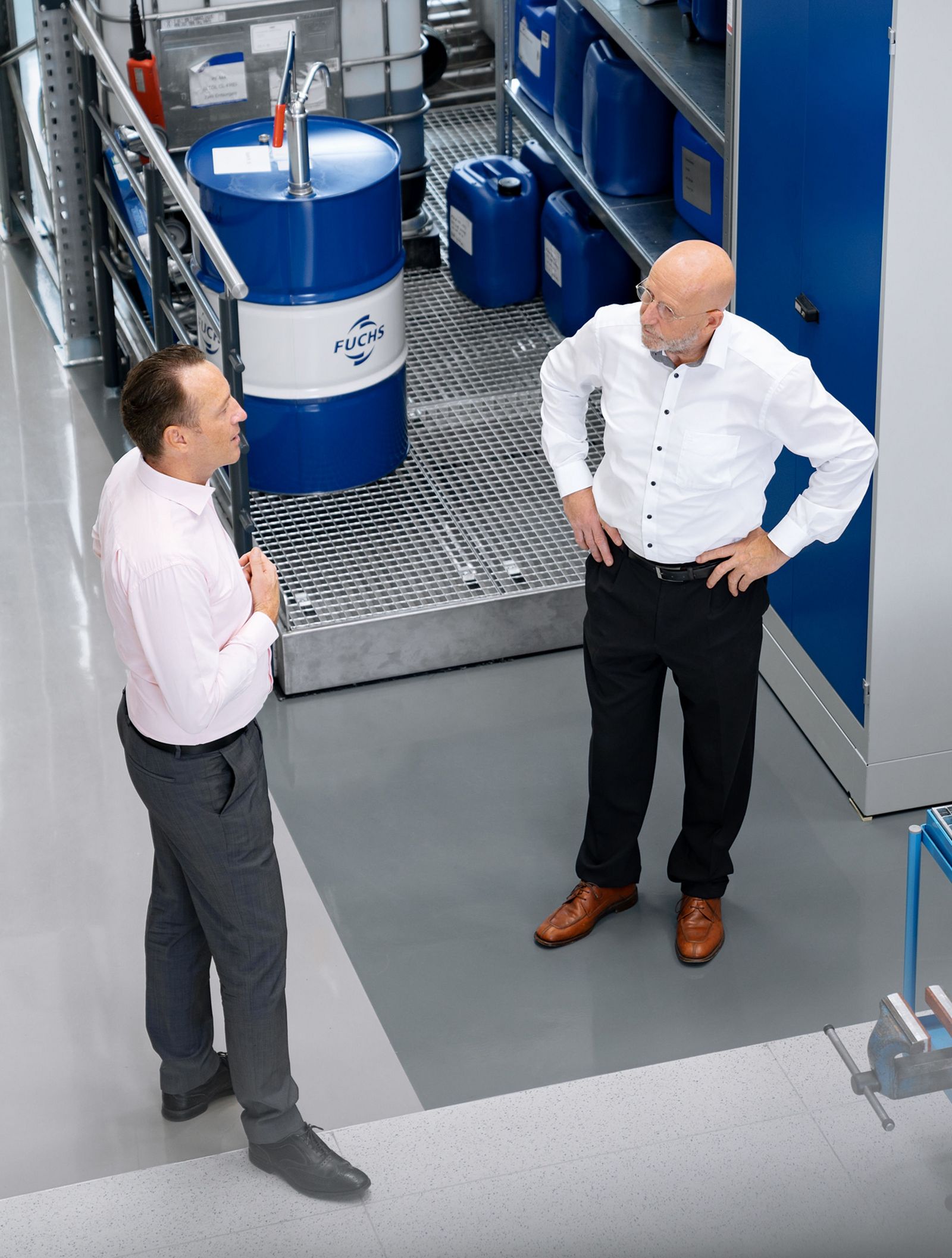
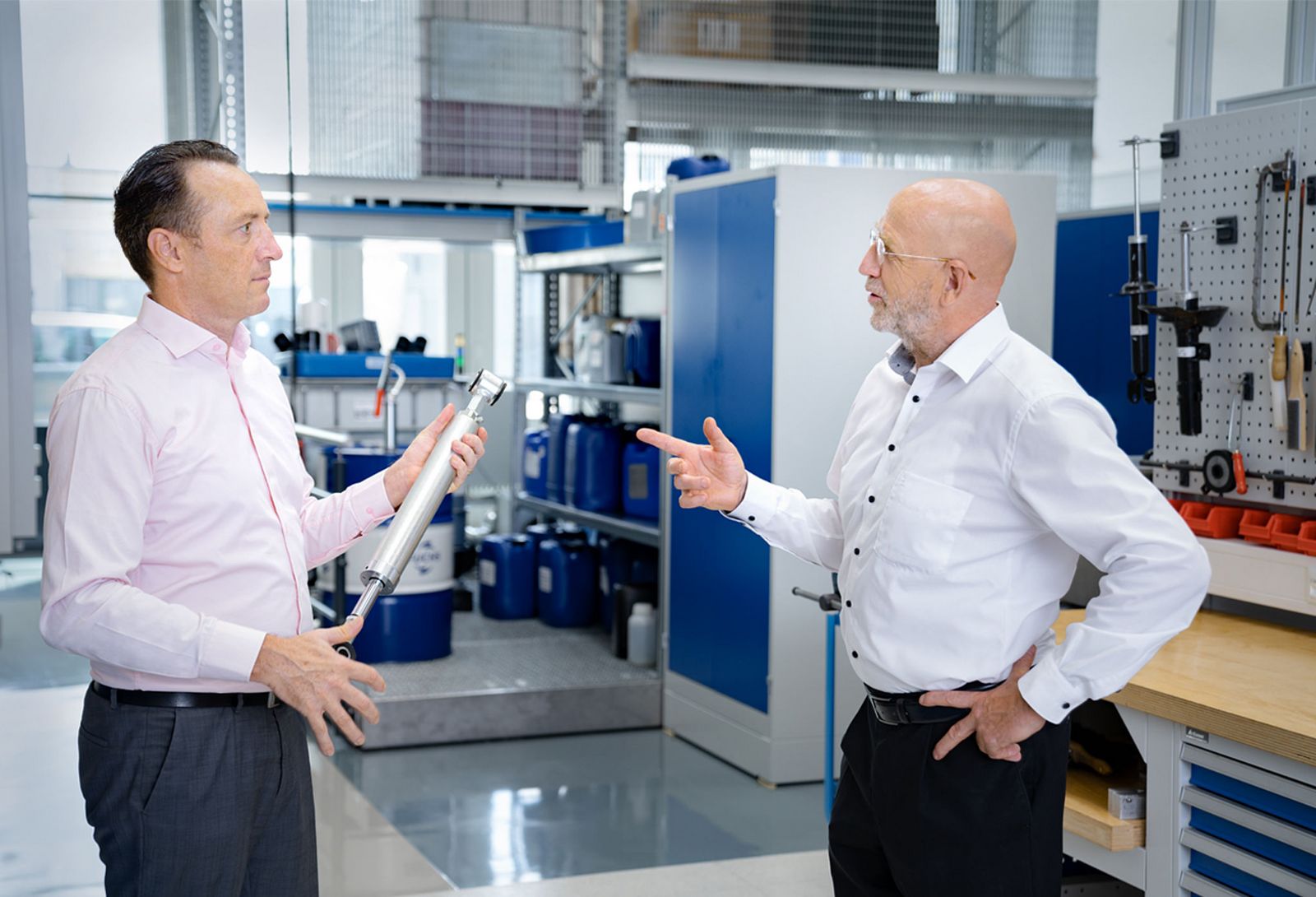
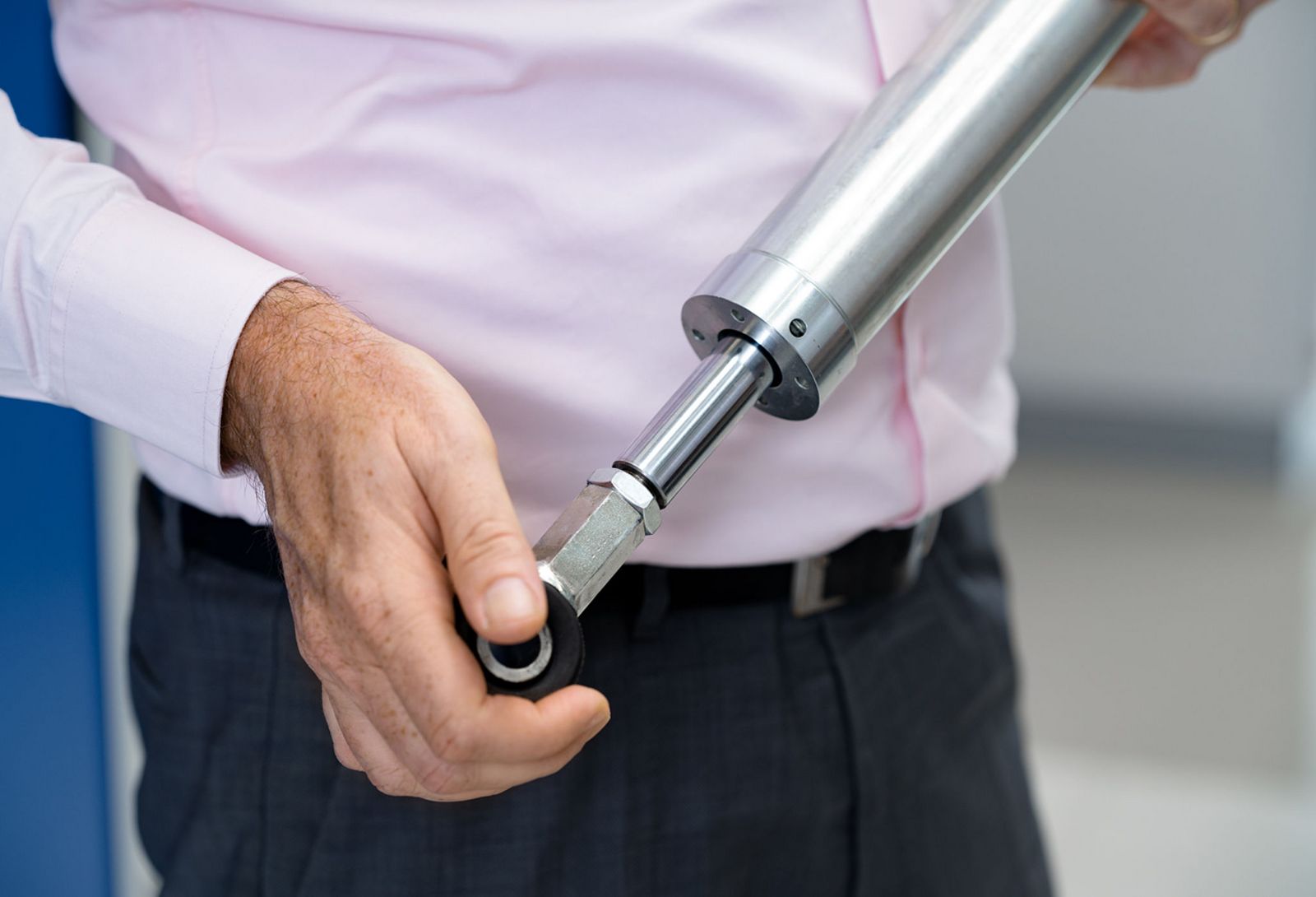
HYDRAULIC OILS UNDER SCRUTINY
The “environmental friendliness” of three FUCHS hydraulic oils which had been used for 8,000 hours in a crawler excavator were closely examined. The three products assessed were all mineral oil based and comprised of one standard monograde hydraulic oil, one standard multigrade hydraulic oil, and one premium multigrade hydraulic oil. “We are often asked why we performed the project on hydraulic fluids,” explains Bock. “First of all, these products are used for many different purposes and are clearly the number one among industrial oils. Another important point, however, was that our product range and the corresponding applications are closely geared to practical use and we already had indicative and comprehensive field data from earlier studies.” FUCHS contributed this data material to the study whilst BASF provided raw material data as well as the expertise and methodology for performing the eco-efficiency analysis. The combined support proved vital, as it was a huge challenge to prepare the data to meet the rigorous standards of a scientific study – and that was precisely the goal.
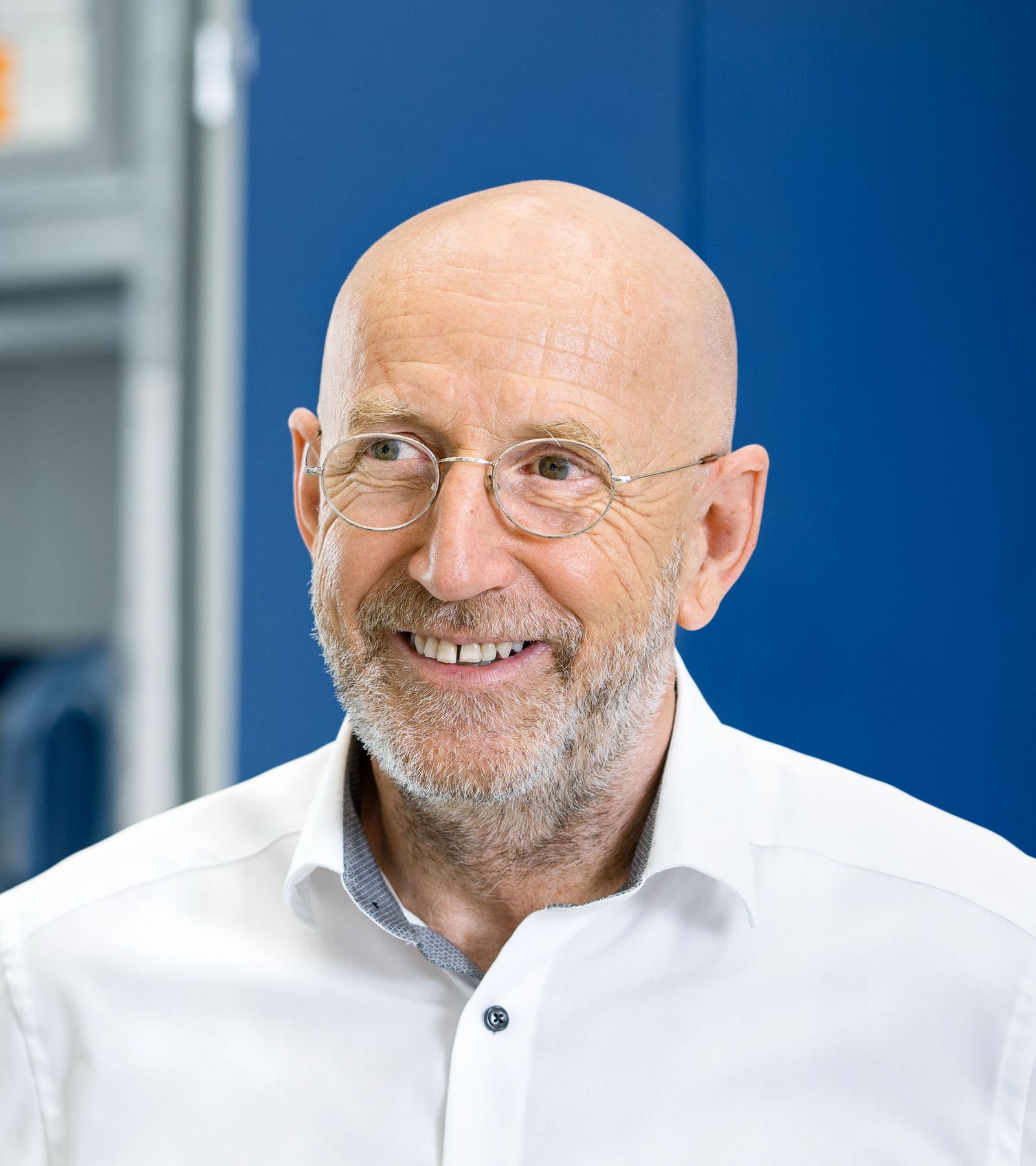
“Overall, premium fluids are by far the more environmentally friendly option.”
WOLFGANG BOCK, HEAD OF PRODUCT MANAGEMENT INDUSTRIAL OILS AT FUCHS
Fortunately, the data from the field studies proved feasible and the result was clear. “Obviously, a monograde hydraulic oil has the best carbon footprint in production, as it consists primarily of solvent raffinates/crude oils and its manufacture produces barely any emissions,” explains Fassbender. “Of course, it's a different story with high-grade products like high-performance hydraulic oils. Producing the required additives alone requires greater energy consumption. But what happens in the excavator? This is where the high-grade hydraulic oils perform better and ensure that the machine uses much less fuel, for example through reduced friction and increased pump efficiency. In addition, the service life of the premium fluids is far longer, which means that maintenance intervals can be further apart – that also requires significantly fewer fossil resources.” Bock sums up: “Overall, if you consider the entire lifetime, the premium fluids are by far the more environmentally friendly option.”
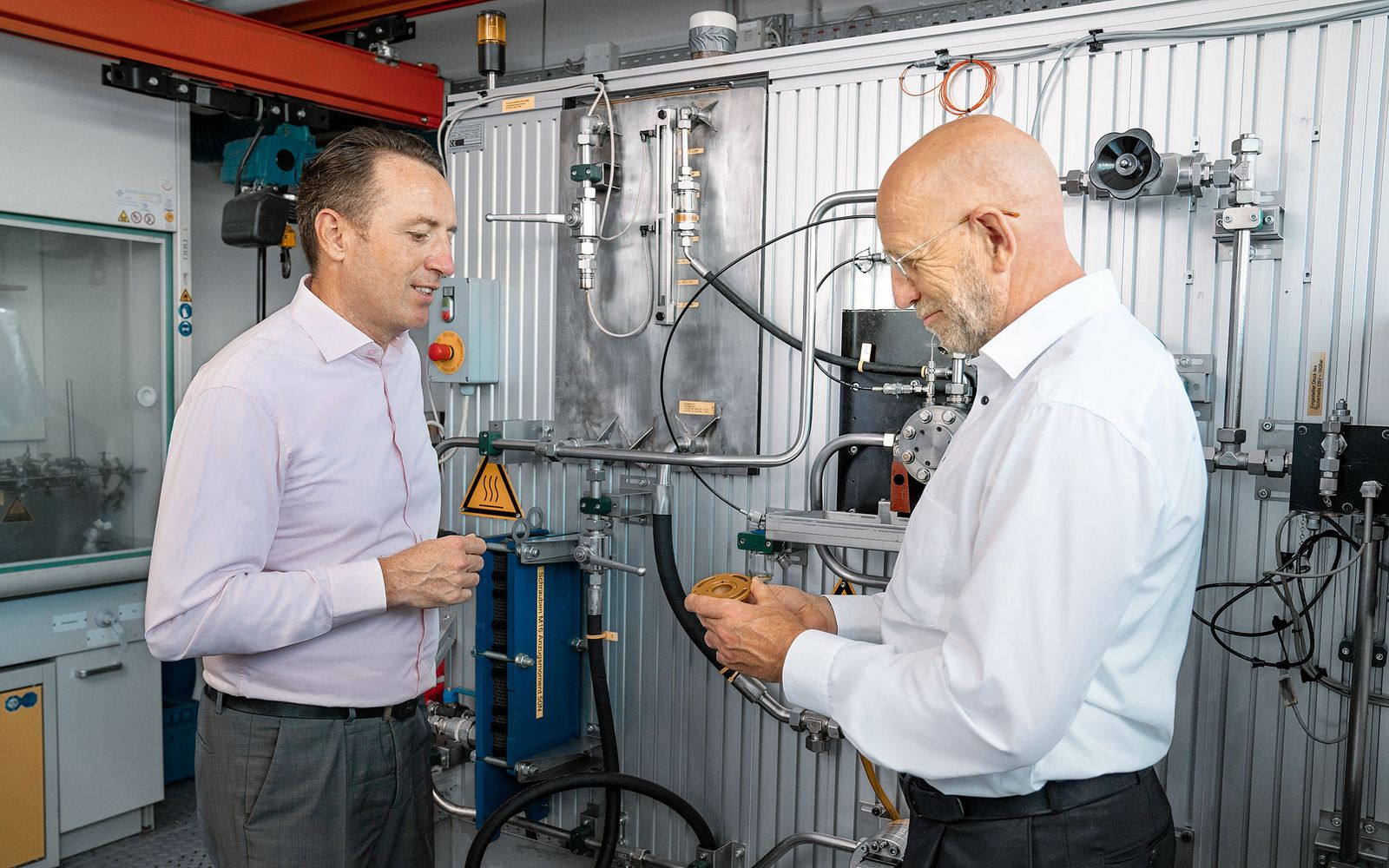
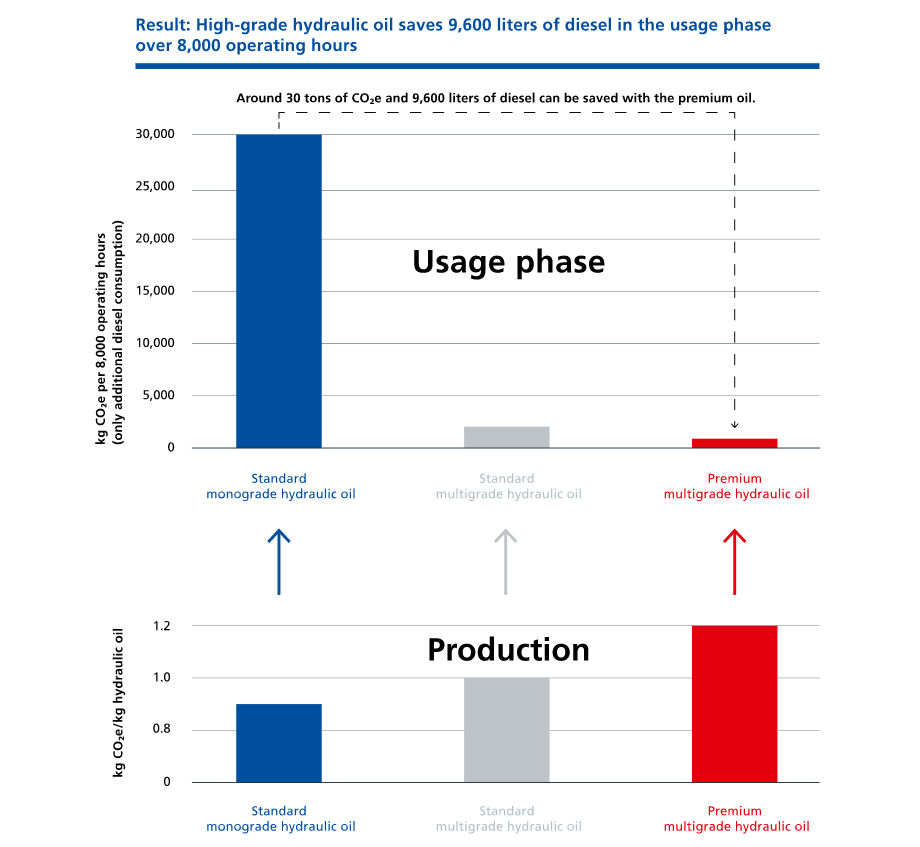
PREMIUM FLUID HAS THE EDGE
The figures from the study clearly prove this: Hydraulic oil consumption over the 8,000 operating hours dropped significantly due to the longer service life of the high-grade hydraulic oils – from 1,600 liters (standard monograde hydraulic oil) to 400 liters (premium fluid). More importantly using the premium multigrade hydraulic oil saved approximately 9,600 liters of diesel. That corresponds to a CO₂ equivalent of around 30 tons. “This improved not just the climate footprint but also the economic evaluation,” says Bock happily. “The costs for diesel fuel decreased by around 12,000 euros.”
“The study is sure to get other companies in our industry into thinking differently,” says Fassbender. “The results are a complete turnaround from the usual way of seeing things. Ultimately, a product can be more environmentally friendly overall, although it is responsible for greater carbon emissions during production.” Bock, who agrees with Fassbender, adds: “For our customers, this means taking a completely different approach when it comes to the sustainability analysis of the products they purchase: Of course it would also be great if we could use this study to provide food for thought for the entire lubricant industry. We intend to bring up these issues in our work with associations, too. For example, FUCHS is currently actively supporting the foundation of a sustainability committee under the umbrella of the European lubricant association UEIL. Its purpose would be to develop standards and guidelines for sustainable lubricants.” The two managers are already considering other projects in the medium term. “It would be useful, for instance, to develop a similar analysis aimed at other lubricant groups,” is one idea. “Plus, besides this study on the mineral oil-based hydraulic fluids, it would no doubt be interesting to examine ester-based biodegradable hydraulic fluids as well. They have even less friction compared to mineral-oil based products and are proven to be biodegradable. Investigations with fluids like these would be very interesting, too.”
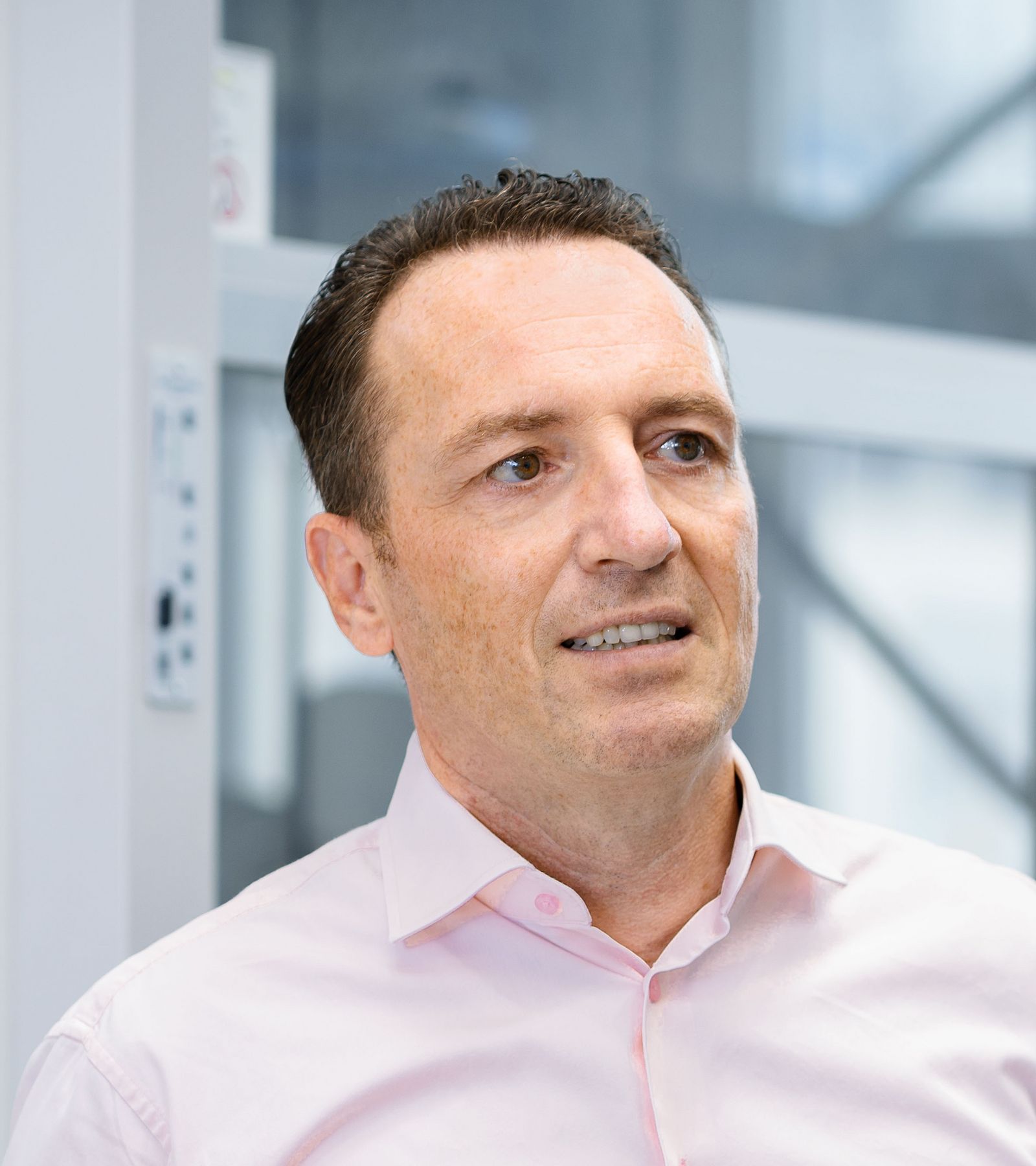
“The results of the study will get other companies in our industry into thinking differently.”
STEFAN FASSBENDER, DIRECTOR COMPONENTS BUSINESS MANAGEMENT EMEA – FUEL AND LUBRICANT SOLUTIONS AT BASF
ENVIRONMENTAL FOOTPRINTS FROM DIFFERENT PERSPECTIVES
- Gate2gate: In the gate-to-gate analysis, the environmental assessment is limited to procedures within the company, that is to say primarily the production of the finished products.
- Cradle2gate: In the cradle-to-gate analysis, the environmental assessment of production is evaluated including the raw materials.
- Cradle2grave: The cradle-to-grave approach analyzes the entire product life cycle, from raw materials extraction, through production and use, right up to disposal.
- Cradle2cradle: This approach looks at the entire value chain, from raw materials extraction, through their processing, on to the production of finished products, their useful life and disposal as well as a potential return to the material cycle via recycling – i.e. the circular economy.
ECO-EFFICIENCY ANALYSIS
Bringing economy and ecology into harmony is the goal of the eco-efficiency analysis. Products or procedures that provide the same customer benefit are compared here. A comprehensive examination is performed along the entire life cycle of the alternative solutions. In terms of environmental impact, e.g., the required raw materials, water and surface area are taken into account, as well as greenhouse gas emissions and the consequences of using the product in terms of acidification and ozone destruction. The eco-efficiency analysis is based on DIN EN ISO 14040 and 14044 for environmental evaluations. The ISO standard 14045 has been in place as the basis for the economic evaluation and the aggregation of the entire eco-efficiency analysis since 2012.