Aerospace
Innovative metalworking fluids for aerospace machining
Quality precision machining of aerospace components requires high performance specialist coolants. At FUCHS, we understand the unique challenges of aerospace machining and dedicate our expertise to ensuring our cutting fluids deliver competitive advantage to your production.
We research, develop and manufacture bespoke machining fluids – technology that is approved for use by leading manufacturers and available globally via the FUCHS organisation.
Premium quality water miscible coolant solutions are just part of the FUCHS portfolio. FUCHS offers customers a full line supply service for all coolant and lubricant demands. Included within our metalworking fluid portfolio are innovative solutions to meet the highly sophisticated demands of the aerospace industry, designed with the expertise of our aerospace group and approved by leading manufacturers.
Our lubricant solutions to the specific requirements of aerospace manufacturing
Structures
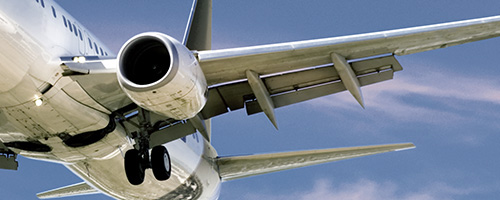
Materials used in the manufacture of ribs, stringers, spars and bulkheads are becoming more exotic. Utilised for their strength to weight ratio, these materials create unique demands on the cutting fluids, which FUCHS’ technology addresses head on.
FUCHS is able to offer specialist cutting fluid solutions providing optimum efficiency, from the initial bulk metal removal through to the high speed machining of thin wall components.
Engines
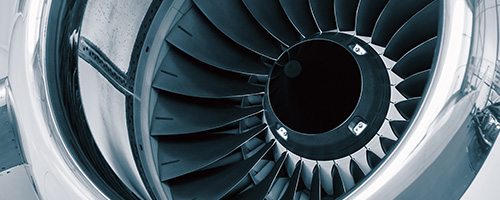
Aerospace engine machining requires unsurpassed accuracy, precision and quality. Through many years of partnership with leading global engine producers, we are able to supply innovative coolant solutions for all key components and substrates in the modern jet engine.
Turbine blade grinding, blisk milling and super-finishing are just some of the applications for which FUCHS can provide specialist coolant technology.
Landing gear
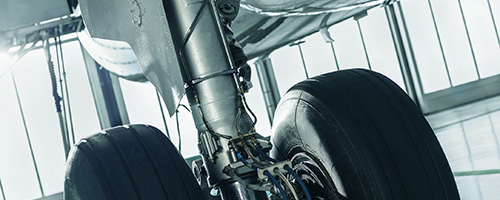
Modern landing gear uses high strength sophisticated materials (such as Titan 5-5-5-3 ) in its manufacture. These are increasingly difficult to machine and create unique demands on the coolant.
Only by working with OEM manufacturers, machine tool builders and tooling suppliers is FUCHS able to understand the full parameters of the operation and to develop build coolants capable of matching the production demands of the customer.
Structural solutions
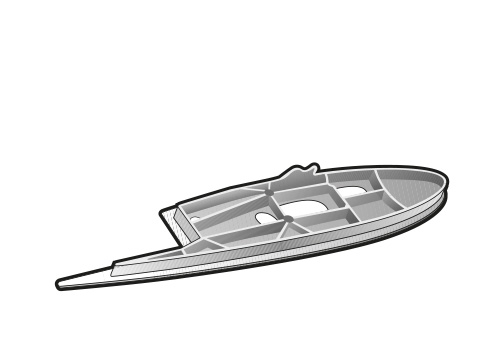
Wing rib
Material:
AL2024 and AL7075 aluminium alloy
Operation:
Rough milling with solid carbide endmill
Criterion:
Surface finish, metal removal rate
Recommendations:
ECOCOOL GLOBAL 1000
PLANTOCUT 22 SR
ECOCUT MIKRO PLUS 20
Concentration:
8–9%
Expected results:
Non-staining, increased tool life
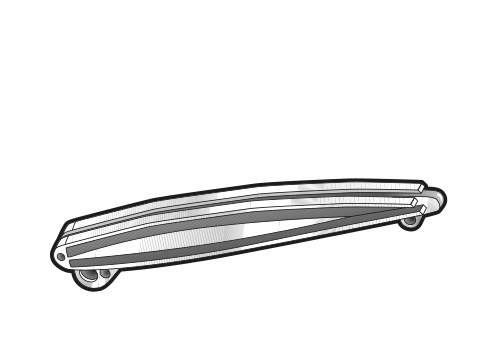
Flap track
Material:
Titanium alloy Ti6Al4V
Operation:
Helical side milling, roughing
Criterion:
Metal removal rate
Recommendations:
ECOCOOL GLOBAL 1000
ECOCOOL TN 2550
PLANTOCUT 22 SR
ECOCUT MIKRO PLUS 20
Concentration:
8–9%
Expected results:
Reduced cycle time, improved tool life
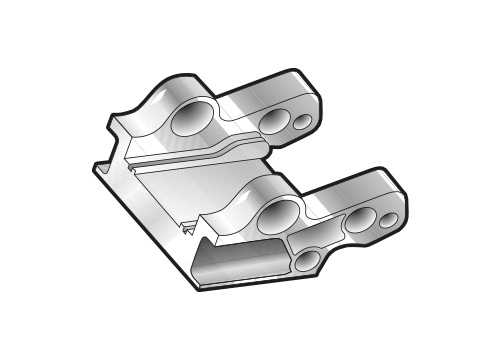
Engine mount
Material:
Titanium alloy Ti6Al4V
Operation:
Drilling and milling
Criterion:
Application security and productivity
Recommendations:
ECOCOOL GLOBAL 1000
ECOCOOL TN 2550
ECOCUT MIKRO PLUS 20
Concentration:
8–9%
Expected results:
Reduced cycle time, improved tool life
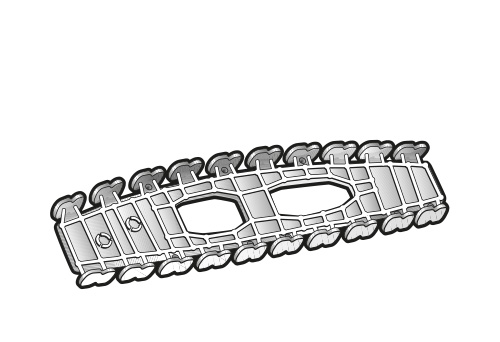
Wing spar
Material:
AL2024 and AL7075 aluminium alloy
Operation:
Rough milling, pocketing
Criterion:
Metal removal rate, productivity
Recommendations:
ECOCOOL GLOBAL 1000
ECOCOOL TN 2550
PLANTOCUT 22 SR
ECOCUT MIKRO PLUS 20
Concentration:
8–9%
Expected results:
Non-staining, increased tool life
Engine solutions
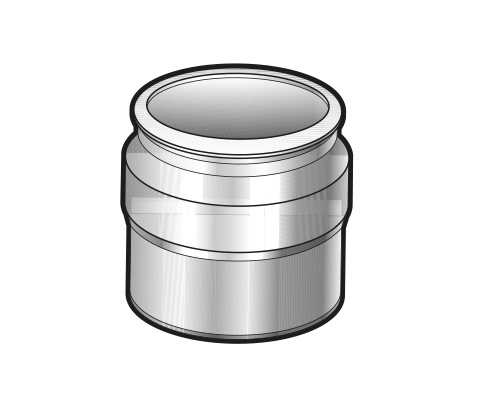
Front case
Material:
Inconel 718, Waspaloy
Operation:
Rough turning and finish top profile
Criterion:
Surface finish and dimensions
Recommendations:
ECOCOOL GLOBAL 1000
ECOCOOL NI 1000
Concentration:
8–9%
Expected results:
Fine finish, increased tool life
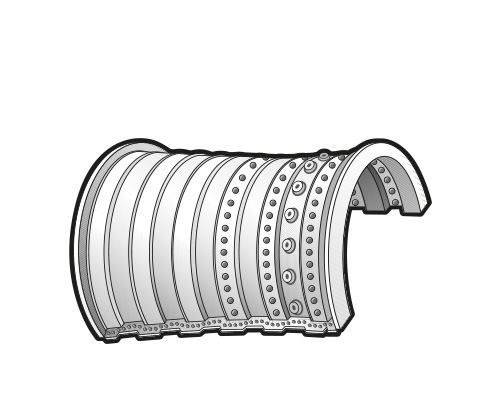
Engine case
Material:
Ti 6Al 4V, Waspaloy
Operation:
Rough milling
Criterion:
Metal removal
Recommendations:
ECOCOOL GLOBAL 1000
ECOCOOL NI 1000
Concentration:
8–9%
Expected results:
Increased tool life
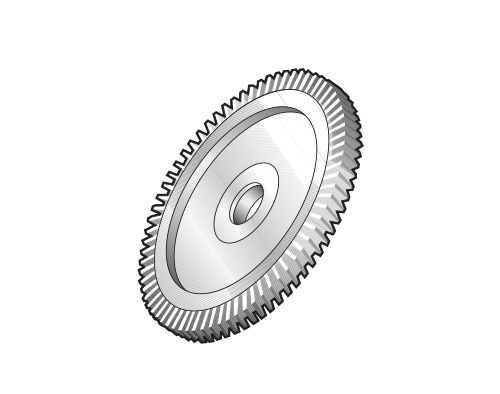
Blisk
Material:
Inconel 718 aged and hardened 48 HRc
Operation:
End milling, slotting
Criterion:
Surface finish
Recommendations:
ECOCOOL GLOBAL 1000
ECOCOOL NI 1000
Concentration:
8–9%
Expected results:
Non-staining, increased tool life
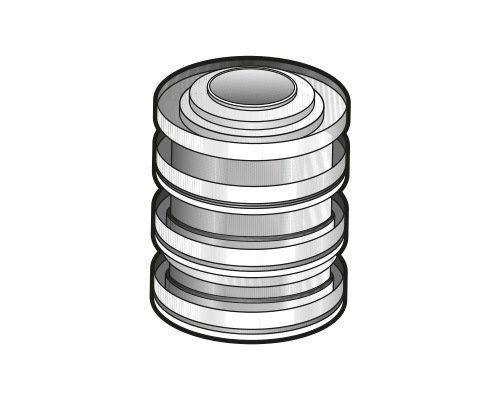
Hub
Material:
Inconel 718 forged
Operation:
Rough turn internal features
Criterion:
Reduce cycle time
Recommendations:
ECOCOOL GLOBAL 1000
ECOCOOL NI 1000
Concentration:
8–9%
Expected results:
Reduced cycle time, improved tool life
Landing gear solutions
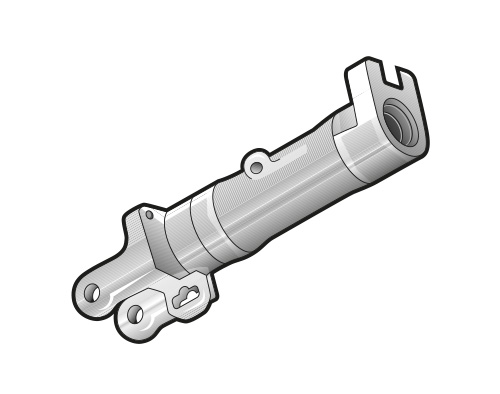
Slider
Material:
Ti 6Al 4V (Ti 6-4)
Operation:
Slotting
Criterion:
Metal removal rate, tool life
Recommendations:
ECOCOOL GLOBAL 1000
ECOCOOL TN 2550
Concentration:
8–9%
Expected results:
Increased metal removal rate vs tool life
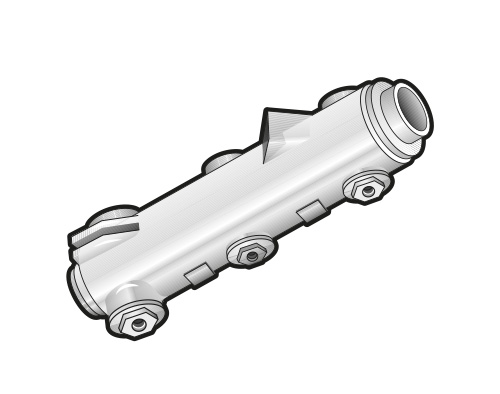
Truck beam
Material:
Ti 5Al 5Mo 5Al 3Cr (Ti 5-5-5-3)
Operation:
Rough milling by plunge contouring
Criterion:
Metal removal rate, tool life
Recommendations:
ECOCOOL GLOBAL 1000
ECOCOOL TN 2550
Concentration:
8–9%
Expected results:
Increased metal removal rate vs tool life
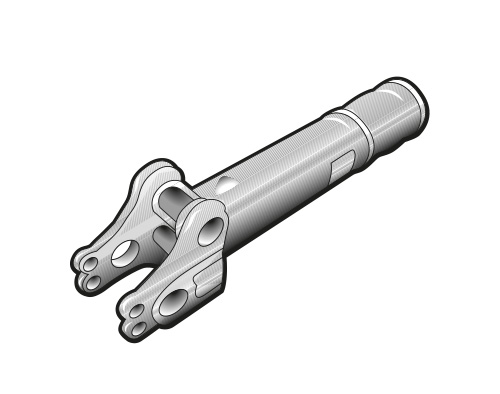
Links & braces
Material:
Ti 5Al 5Mo 5Al 3Cr (Ti 5-5-5-3)
Operation:
3D milling, roughing
Criterion:
Metal removal rate, tool life
Recommendations:
ECOCOOL GLOBAL 1000
ECOCOOL TN 2550
Concentration:
8–9%
Expected results:
Increased metal removal rate vs tool life
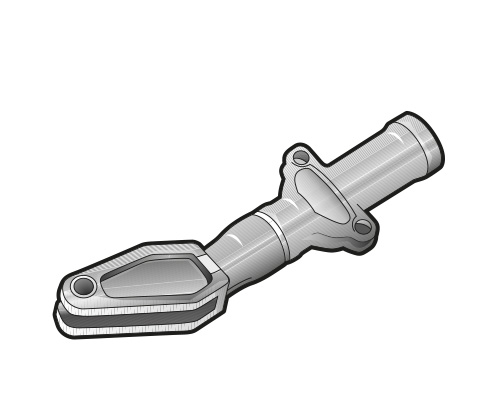
Links & braces
Material:
Ti 6Al 4V (Ti 6-4)
Operation:
Square shoulder milling
Criterion:
Metal removal rate, tool life
Recommendations:
ECOCOOL GLOBAL 1000
ECOCOOL TN 2550
Concentration:
8–9%
Expected results:
Increased metal removal rate vs tool life
Coolants from FUCHS
We engage in application-oriented development directly at and in cooperation with the customer with the aim of adapting lubricants optimally to the process and machine-related requirements. In addition, great emphasis is placed on basis research in the FUCHS Group.
Our ultra-modern Technology Center at the headquarters in Mannheim coordinates the international network of experts, brings together expertise and supports knowledge transfer on global requirements.
Technology designed to assist with high metal removal rate whilst maximising tool life. Specifically designed for titanium and nickel based alloys.
Technology designed to withstand the pressures of high velocity coolant delivery. Designed to offer maximum tool life, suitable chip evacuation and machining accuracy on a wide range of difficult-to-machine substrates.
FUCHS’ coolant technology is approved by leading manufacturers globally including Boeing, Airbus, Rolls Royce and Pratt & Whitney, providing subcontractors with reassurance of quality and validity.
FUCHS’ product range includes minimum quantity lubricants for spray systems. Approved by aero manufacturers and equipment manufacturers.
Overview of relevant FUCHS coolants
Product | Boron-free | Emulsion / synthetic / MQL / neat oil | Nickel based- and titanium alloys | Aluminium alloys | Composites |
yes | emulsion | +++ | +++ | – | |
yes | emulsion | +++ | + | – | |
yes | emulsion | +++ | ++ | – | |
yes | synthetic | – | – | +++ | |
yes | neat oil | ++ | +++ | – | |
yes | MQL | ++ | +++ | – |
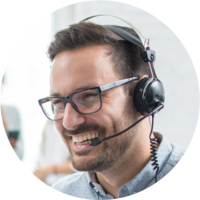
Any Questions?
Let us know how we can help you with your challenges. We will find a solution for you!