Reduces your operating costs: innovative cooling lubricant and coordinated cleaner
Energy efficiency and environmental protection are the focus of metal processing companies
The use of innovative FUCHS cooling lubricant systems contributes significantly to the realisation of sustainable and cost-saving cooling lubricant concepts.
Many production processes include aluminium, grey cast iron and steel machining, but also materials such as Inconel, CFRP or titanium with their specific machining processes. In recent years, the production process has been optimised in many respects from the point of view of sustainability. A first approach to resource-conserving production is minimum quantity lubrication or dry machining, as these environmentally friendly processes only require very little cooling lubricant (coolant). A central coolant supply and disposal system is not necessary, which reduces the costs for maintenance, care, energy and disposal. Many large car manufacturers and some suppliers are already using this technology. Many users rely here on the proven FUCHS ECOCUT MIKRO series.
However, there are still limits in some manufacturing processes such as grinding or honing. In machining processes where the removal of chips, a high lubricating effect and heat dissipation are very important, machining oils and / or emulsions are mainly used. The focus here is on optimisation potential in existing systems, from the point of view of energy efficiency. Thus the use of innovative cooling lubricant systems can offer significant advantages when combined.
Innovative cooling lubricant systems
Numerous cleaning steps are necessary in the manufacturing process in order to meet the high requirements for component cleanliness. In addition to cleaning the workpieces from metal chips, the cleaning process must ensure that no machining oils from minimum quantity lubrication and oily metal machining are transferred to aqueous machining. This greatly shortens emulsion service life and makes emulsion analysis more difficult due to the constantly increasing oil content. The danger of rejects is growing. As the water-miscible cooling lubricants and the water-miscible detergent components are based on similar chemistry, a combination solution could be developed that the answer to that question.
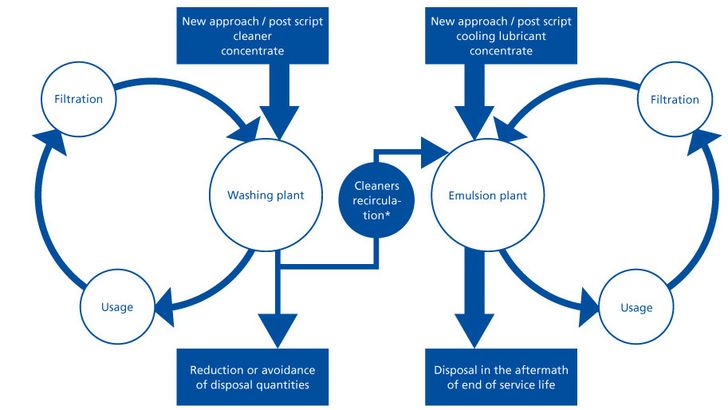
Many users are already using the ECOCOOL S - NDR concept from FUCHS, in which the cleaner is partially used in the emulsion production as a secondary water. This results in lower disposal and water follow-up costs and the coolant consumption can be reduced. Cleaners must be changed if the cleaning effect is no longer sufficient and/or the degree of soiling increases and no clean, high-quality parts leave the scrubber. This washing water, which is available for disposal, can be used in central and individually filled systems as an additive medium to compensate for water losses and also to support the pH stability and corrosion protection of the processing emulsion.
New ECOCOOL S - NDR system with recirculation
The requirements for a recyclable cleaner are very complex. It must have the following characteristics:
- Favourable foaming behaviour
- high washing effect
- high elastomer compatibility
- good material compatibility
- multiple usable in intermediate and final washers
- low operating temperature and
- good energy efficiency.
Heinz Gerhard Theis, head of R&D for metal-cutting at FUCHS, paid particular attention to the compatibility of the cleaner with the processing emulsion during the RRF return process. The success of the RRF concept lies in the concept of the cleaner. A cleaner was created by combining compatible ingredients such as the alkaline components, wetting agents and emulsifiers from the ECOCOOL product range from FUCHS, which meets the high requirements. In addition, the entire ECOCOOL product range is compatible, and the ECOCOOL S - NDR concept can also be extended to the water-miscible product portfolio of the German FUCHS cooling lubricants can be used.
Many advantages
Water-mixed ECOCOOL S - NDR, which is applied in 2 - 4 % in the washing plant, can be used after its service life (usually after 2 - 4 weeks) as an additive medium for aqueous production in the central supply or in individually filled machine tools. This recirculation has several advantages, e.g.
- less waste from the part washers,
- low water consumption,
- stabilisation of the machining emulsion,
- less cooling lubricant concentrate and readjustment additives and a
- longer service life of the machining emulsion.
Large automobile manufacturers and suppliers generate 3 to 5 times the amount of cleaner to be disposed of each year.
At the same time, 10 to 15 times the tank volume of the additional quantities (2 - 5 % fresh emulsion) in the plants are required annually to compensate for drag-out losses. The disposal and operating water costs can be significantly reduced by quasi-volume replacement of the additional quantities by the cleaning agent used for disposal.
In addition, practical experience has shown that by means of cleaner recirculation, the after-sales concentration of the fresh emulsion can be reduced to 1 - 1.5 % and thus additional cooling lubricant concentrate costs can be saved considerably.
Practical experience - ECOCOOL S - NDR Feedback (RRF)
Total circulation volume cooling lubricant 250 m³ 14 washing machines from 3 - 10 m³ with change interval washing machines 2 - 4 weeks
Categories | Savings/Year |
Old emulsion | 900 m³ |
KSS concentrate | 13.5 t |
Washing machine cleaner concentrate | 11.8 m³ |
Heat costs (reduction washing temperature) | 2,930 € |
Drinking water | 490 m³ |
Demineralised water | 450 m³ |
Total cost savings | 102,000 € |
Significantly lower process costs
The innovative FUCHS cleaner and recirculation concept makes a significant contribution to reducing costs. Lower cleaning temperatures, lower disposal quantities due to the use of the cleaner as a supplement, savings in fresh water, longer emulsion service lives and savings in cooling lubricant concentrate mean that the following can be achieved process costs can be significantly reduced. In addition, the environment also benefits and production becomes more sustainable.
Mobile filter system
For test purposes, a mobile filter system with integrated cooling lubricant tank can be provided.
Savings potentials - Innovative system - ECOCOOL S - NDR feedback (RRF) in the described practical example
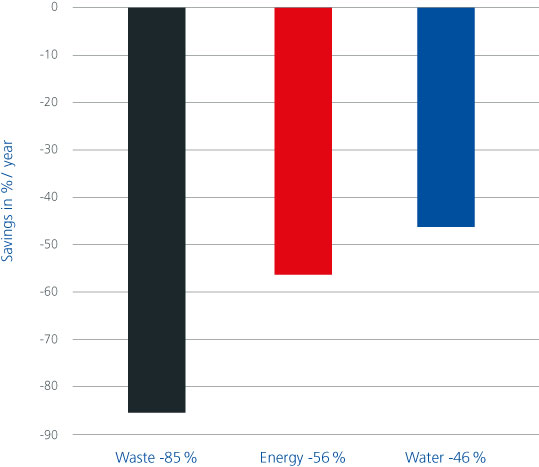