Geopolymer concrete – the cement-free alternative
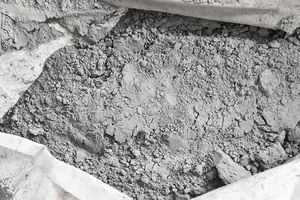
The construction industry is currently undergoing radical change. In order to meet the EU's climate targets, the industry is researching various ways in which CO2 emissions can be reduced.
The search for alternative binding agents for concrete to replace cement plays a central role. The production of this building material is particularly energy-intensive and it is also the most frequently used material worldwide. An environmentally friendly and equivalent alternative to cement would therefore be very important for climate protection.
A mixture of fly ash and granulated blast furnace slag, which forms a geopolymer binder in combination with an activator, has proven to be a particularly sustainable alternative to cement.
Avoiding cement not only saves emissions. The sustainable recycling of industrial waste products also protects the environment, as no alternative raw materials have to be mined. Since the use of geopolymer concrete does not entail any technical disadvantages, this cement-free alternative has proven to be very promising for the future.
In contrast to conventional concrete, no lime efflorescence occurs during precast production with geopolymer concrete. Only salt deposits can appear on the concrete surface, which are, however, easily soluble in water and disappear without leaving any residue after the first rainfall or washing. In addition, a high proportion of blast furnace slag can lead to a green discoloration of the precast concrete elements.
Sustainable construction – new challenges for precast concrete elements
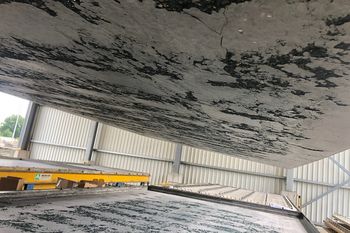
However, the use of sustainable concrete also brings new challenges for the precast concrete industry - especially when it comes to formwork.
This is because the cement-free composition of the concrete means that tried-and-tested release agents do not work as usual. Since no cement is used, a chemical reaction remains. The use of previous release agents therefore leads to an impairment of the quality of prefabricated concrete parts. This becomes clear in the formwork removal process due to (sometimes considerable) adhesives and adhesions.
The focus with geopolymer concrete is therefore on the physical separation of the prefabricated part from the formwork, which must be taken into account in the concrete release agent used.
Poor physical separation is to be expected, especially when using release agent emulsions, as the low oil content leads to an insufficient separation effect between concrete and formwork.
Release agents for geopolymer concrete

As an industry expert, FUCHS has already carried out several precast projects with geopolymer concrete, in which the concrete release agents used were able to achieve very good results.
It has been found that water-free and highly viscous release agents are particularly suitable both in precast concrete plants and on construction sites. Nevertheless, it is not possible to give a general recommendation for release agents when using geopolymer concrete. This is because several factors must always be taken into account when selecting a suitable release agent, including:
- The ratio between fly ash and granulated blast furnace slag
- The binder content of the concrete mix
- External environmental influences (e.g. room temperature or humidity)
- The material quality of the formwork used
In order to determine the best release agent for the production of your precast parts, preliminary tests with an experienced release agent specialist are always essential.
Your release agent partner for the concrete technology of tomorrow
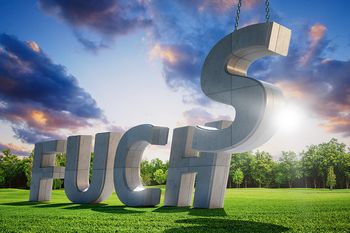
Of course, FUCHS doesn't just offer suitable release agent solutions for geopolymer concrete. No matter how the concrete composition develops in the future: We at FUCHS will provide the right concrete release agent for every new challenge or develop it together with our customers. We not only focus on the use of sustainable concrete alternatives - we also solve these challenges with our sustainable concrete release agents. Because sustainability and efficiency are not mutually exclusive at FUCHS.
What challenges can we solve for you?