Innovative cutting fluids and their key role in making medical implants
Lubrication goes without saying in the automotive and other heavy industry. But did you know that lubricants also play a key role in manufacturing high-tech products, including medical implants?
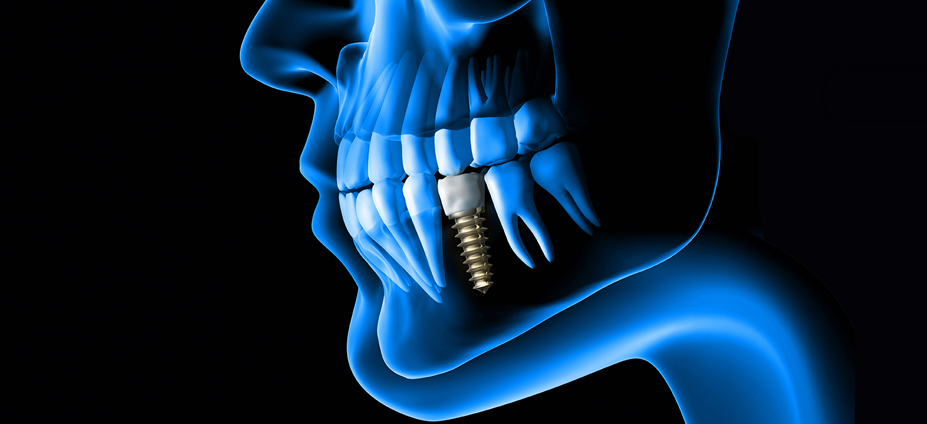
Medical devices are a fast-growing industry. This is largely because we are living longer and are more aware of health issues. The rapid population growth on emerging markets around the world is also increasing demand for medical devices. The recent growth in the industry would not have been possible without modern specialised production technology. This is also where lubricants come in. FUCHS Lubricants has been developing innovative products for the medical devices industry for over 10 years, including cutting fluids for the manufacture of implants.
Tough requirements
Cutting fluids used in the medical devices sector are subject to a whole range of requirements. Alongside stainless steel, the industry increasingly uses titanium and cobalt alloys in the production of implants. These are materials with superior strength, but this very strength complicates the various chip-forming processes in production, such as drilling and milling. This calls for sophisticated engineering of the highest level, also when it comes to the cutting fluid.
To meet the challenges of this kind of hard-to-machine materials, FUCHS specialists have developed unique solutions for each process or area of use. Quality is extremely important.
“We take each customer’s specific requirements with us into the lab,” explains Frank Thomas, Head of Development for non water-miscible cutting and quenching fluids. “For this highly sensitive sector, we check the raw materials meticulously and conduct rigorous tests. This assures the highest possible safety for manufacturers and users.”
Magnesium is the future
As medical devices move into the future, researchers and developers are quick to highlight magnesium alloys. This is because magnesium screws and plates can be fully broken down in the human body. This could mean that in the future, a broken leg may need nothing more than one surgical procedure. This is a technology that presents great possibilities.
“As well as being degradable in the body, magnesium also has weight advantages and is simpler to machine,” says Kenneth Borin, Product Manager Metalworking, FUCHS Nordic. “Today magnesium is used in the manufacture of prototypes and models where minimising weight is important, for example. The automotive industry has also long used magnesium, such as in alloy wheels in motor racing.”
When it comes to weight, there is quite a difference between magnesium and other materials. For instance, magnesium is 33% lighter than aluminium and a full 75% lighter than steel.
“One application that could increase in the future is magnesium components for electric vehicles, where low weight is likely to be ever more important to manufacturers,” Kenneth concludes.
Read more about cutting fluids here.
All articles
Stay updated
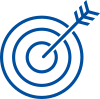
Blog: Smart Lubrication
Smart Lubrication is a blog where we share our common knowledge about lubricants and lubrication.
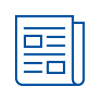
Newsletter
Read or subscribe to our bi-monthly newsletter.