Right cutting fluid – increased profitability
Cutting fluid is a good example of how a minor detail can make a major difference to the end result. The job of a cutting fluid is to cool, lubricate and remove metal particles, swarf and dirt from the machine. If it doesn’t do this the results are higher production costs, more unplanned stoppages and higher tool wear.
So choosing the right cutting fluid is important. But which is the right one? The answer is, it depends. The right cutting fluid is determined by factors such as material and working environment aspects, as well as the type of machining in question.
If you’re machining at low revolution speeds, for example grinding hard metals, deep-hole drilling or threading difficult materials, tooth machining or some other operation with high demands on surface finish, you will need a cutting oil. This will provide plenty of lubrication, as well as excellent swarf removal and corrosion protection.
If you’re machining at higher speeds, however, such as turning, milling or drilling, there are higher demands on cooling, so a water-miscible cutting fluid will be needed: an emulsion or a synthetic.
Change properties without changing fluids
A situation may occasionally arise where you quickly need a more lubricating product than the one you have. We offer an additive that increases lubrication in the existing fluid, so you don’t have to stop production to change fluid. This eliminates costly down time, as you can hold off changing to a more lubricating product at a more convenient time.
Care for your cutting fluid
However, having the right cutting fluid is not enough. You also need to look after it to make sure it lasts a long time. It’s important that both the concentration and the pH are at the right level, and this should be checked at least once a week. The fluid must also be kept clean and free of swarf and other impurities. Moreover, it is important to prevent the growth of bacteria. One of the simplest ways is to use a small aquarium pump that keeps the fluid moving. If you still have bacteria growth in the system, you may need to add a pH booster and a bactericide.
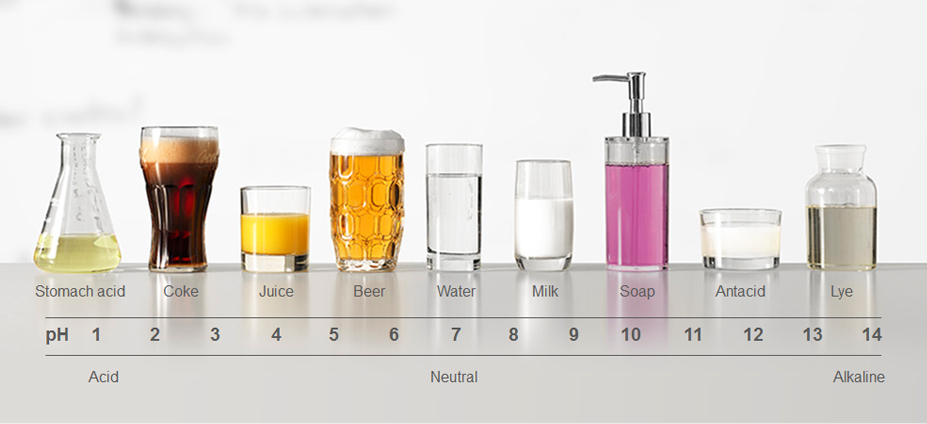
Right cutting fluid = increased efficiency
With the right product and the right checks, there is a lot to be gained. You can maintain a higher cutting speed and achieve better dimensional accuracy, improve swarf management and reduce energy consumption. You will also reduce wear and increase the useful life of your machines and tools. In addition you will have fewer rejects, and run a lower risk of breakdowns and costly stoppage problems. All of this contributes to higher profitability and a lower cost per produced part.
The proof
One case in point is a Polish company that makes aluminum components for the German automotive industry. They contacted us as their production staff were complaining of irritated airways and skin rash.
Following an inspection of the workplace, we recommended our CoolWay EAL cutting fluid. It is based on synthetic base oil and synthetic esters, and contains no volatile amines which can irritate the airways. The results exceeded expectations. The health and safety issues stopped, and the switch led to fewer stoppages and a decrease in tool costs of 50–70%. Cutting fluid consumption also fell by 25% compared to the competing product used previously.
The overall result was that all the components were half as expensive to manufacture; i.e. the cost per produced part fell by 50%.
How about your business?
We would love to help you optimize your processes. Please don’t hesitate to contact us.
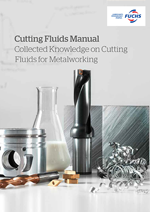
Handbook
Collected Knowledge on Cutting Fluids for Metalworking
Stay updated
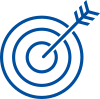
Blog: Smart Lubrication
Smart Lubrication is a blog where we share our common knowledge about lubricants and lubrication.
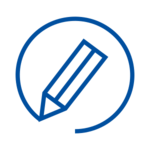
Articles
More in depth articles on current topics.
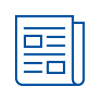
Newsletter
Read or subscribe to our bi-monthly newsletter.