3D printing – new technology that presents a challenge
Metalworking is a major area for lubrication – and also one undergoing major changes! To follow the development of metalworking – such a powerful and precision-led field – and also watching it evolve so dramatically as it’s challenged by new 3D printing technology, is fascinating indeed.
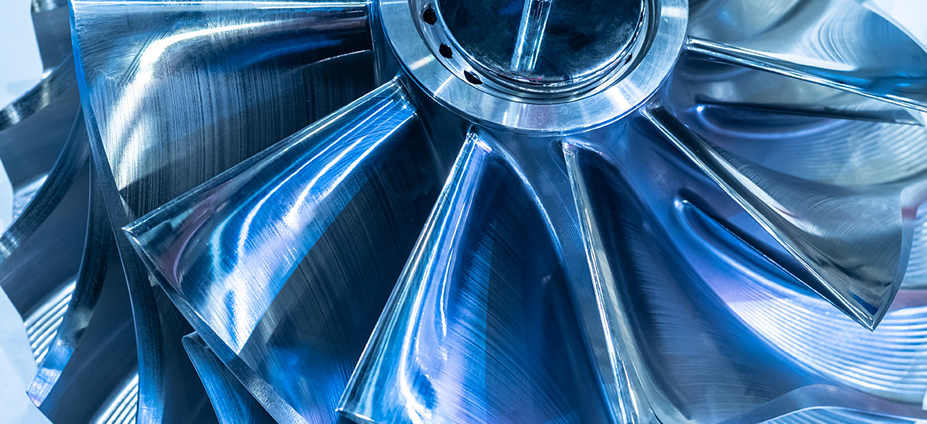
3D printing has become particularly important in aviation, more so than in any other sector of industry. The most important reason is the production rate. Compared to the automotive industry, for example, aviation produces only small quantities. While the two main manufacturers of commercial aircraft, Boeing and Airbus, jointly produced 1,600 aircraft in 2018, the automotive industry made roughly 80 million cars worldwide. Aircraft are large, complex systems, and production takes great care, which in turn takes time. This makes is possible for the relatively slow processes of 3D printers to come into their own.
As a supplier to the aviation industry, this is an incredibly exciting development to monitor at close hand. American engine manufacturer GE Aviation, for instance, has built a new turboprop turbine. Not only is the turbine soon to be used in light aircraft, it’s also a technical accomplishment that is likely to serve as a role model for other aircraft too. So why is this? It is comprised of just 12 components, all made in a 3D printer. In conventional manufacturing processes, turbine production normally involves 855 individual parts, according to GE. They have also been able to lower the turboprop turbine’s overall weight by around 5%, while also reducing fuel consumption by up to 20%. With excellent test-rig performance like this, it’s no surprise that the new GE turbine will soon be used in test flights.
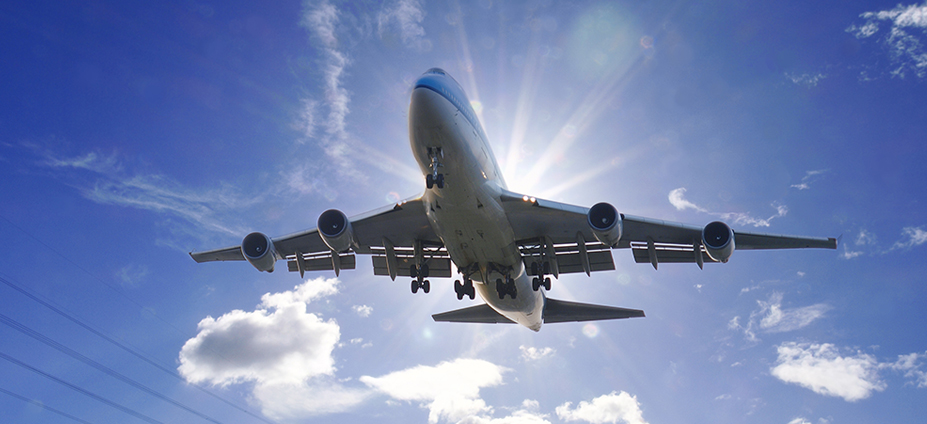
Working with metalworking fluids as I do, perhaps I ought to be worried about the progress of this technology, but in fact I’m not. For us at FUCHS, this is not a competitor, but more a complement to our customers. I find it fascinating to follow developments.
Obviously it’s an advantage for the aviation industry to be able to eliminate certain stages of production that are necessary in traditional metalworking, while also using less of expensive raw materials. But the increased use of 3D printing in aviation doesn’t mean the end for metalworking, and metalworking fluids will be needed also in the future.
3D printing is a comparatively slow process. The raw materials in metal 3D printing are generally raw metals in the form of powder or wire, which are melted by laser to apply layers until the end product has been formed. The process permits design and production of complex geometries and multifunctional parts. Personally I find the multifunctionality one of the most impressive innovations, as previously each component could only have one function.
It is already clear that a lot can be done with 3D printing, and there will of course be more in the future. Forecasts from consultancy firm PwC Strategy suggest that the global market for 3D-printed products and techniques in industry is likely to grow between 13% and 23% a year up to 2030.
Despite the success of 3D technology, classic metalworking will still be a key process in the years to come. Because even though 3D printing is winning market share and can be used to produce more and more complex parts, it cannot (yet) post-treat with micrometre precision and include the necessary surface treatments. Metalworking is a precision job that almost always requires milling, reaming, drilling and grinding – that all have to be done to very fine tolerances. The metal parts have to be worked precisely and fit perfectly, especially in industries like aviation with its extremely strict quality standards.
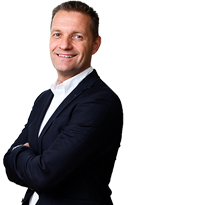
This might also interest you?
Innovative cutting fluids and their key role in making medical implants
Lubrication goes without saying in the automotive and other heavy industry. But did you know that lubricants also play a key role in manufacturing high-tech products, including medical implants?
Microbiology – a weapon in the war against contaminants
Bacteria that contaminate cutting fluid systems disrupt production and cause problems in the working environment. The FUCHS microbiology lab has developed a ‘toolbox’ that tests cutting fluid resistance in a more intelligent way, making development more accurate and more closely customised.
All blog posts
Subscribe
Only available in Danish.
Collected Knowledge on Cutting Fluids for Metalworking
With the right cutting fluid you can reduce the number of unplanned stoppages and increase the life of both the tool and the cutting fluid. This means you can increase capacity utilization, thereby reducing the cost per produced unit.
Smart Lubrication
Smart Lubrication is a blog from FUCHS where we share our common knowledge about lubricants and lubrication.