Rationalise your compressed air processes and reap the benefits
Do you use compressed air anywhere in your business? If you work in industry, the answer is most probably yes. Around 70% of industrial companies in Europe use compressed air in some part of their operation. That’s so much, that roughly 10% of all industrial electricity is used just to generate compressed air. In Europe alone. But this is a figure that can be reduced…
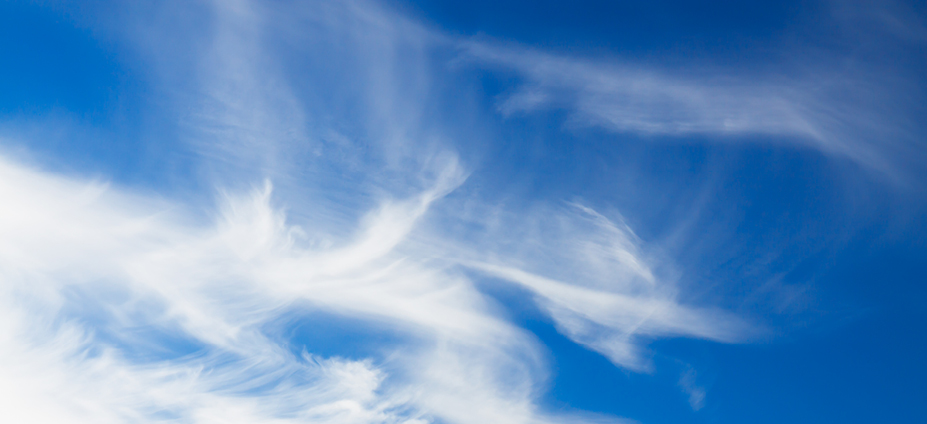
With so many users of compressed air, many could gain by overhauling their systems and their usage – whether the compressed air is used to blow clean, inflate, cool, move, lift or generate any other kind of movement.
AN INEFFICIENT PROCESS
The production of compressed air is an extremely inefficient process. In fact, as little as 5–6% of the ingoing energy actually results in usable compressed air. It’s quite simply one of the most expensive and energy-consuming systems used by man. Moreover, up to half of all compressed air production is unnecessary, since it never gets used. It normally disappears due to unnecessarily high pressure, incorrect use or leakage. Waste like this costs money.
AN EXPENSIVE PROCESS
Producing one cubic metre of compressed air per minute per year costs almost DKK 70,000. This means that one tiny leak 1 mm in diameter risks costing a company around DKK 5,000 a year.
BENEFIT FROM ONGOING CHECKS
Generally speaking, there is a lot to gain by continually checking your systems and how they are used, to ensure they are not leaking and the pressure is no higher than necessary. But you will also benefit by being aware that the way you use your compressed air also has an impact on your finances and the environment. Do you know where and how much compressed air you use, how your systems work and how this affects your bottom line and carbon footprint?
MODERN COMPRESSOR OILS SAVE BOTH MONEY AND THE ENVIRONMENT
Having a well-lubricated system with no leaks or unnecessarily high pressure is a simple way to save energy – which in turn reduces costs and carbon dioxide emissions. Many companies use a mineral oil-based compressor oil out of habit, and are not aware of the benefits of upgrading to a synthetic oil. These include a longer life and therefore longer intervals between oil changes. Benefits like this help to reduce costs for maintenance work and lubricant purchases.
INTERESTED IN FINDING OUT MORE?
You can read more about our special lubricants here, specially designed to meet the high safety demands of the food industry, for instance. And of course you are always welcome to contact us.
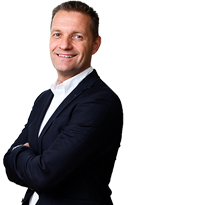
This might also interest you
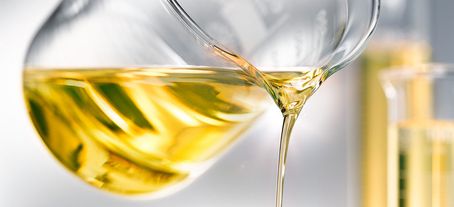
Choose the right viscosity – save energy, money and the environment
In my job, I visit a great many industrial companies every year, in different sectors. One thing I’ve noticed is that most of them still use older types of lubricant of unnecessarily high viscosity. Few seem to know that the right viscosity is the simplest key to greater energy efficiency. Do you know what viscosity you have in your machines?
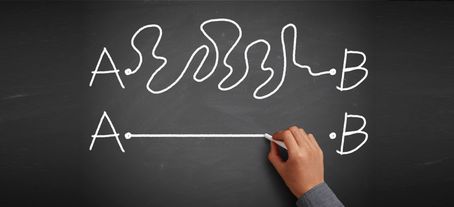
Four rules of thumb in lubrication – your shortcut to savings!
Every little helps, as they say. And this is certainly true of maintenance costs. Because making many minor improvements in your lubrication maintenance adds up to major savings. These minor measures may be many, but that doesn’t mean they’re complicated. I like to sum it up into four rules of thumb, which makes it all a whole lot easier.
All blog posts
Subscribe
Only available in Danish.
Smart Lubrication
Smart Lubrication is a blog from FUCHS where we share our common knowledge about lubricants and lubrication.