Connector greases from Nye Lubricants
Synthetic greases for electrical components
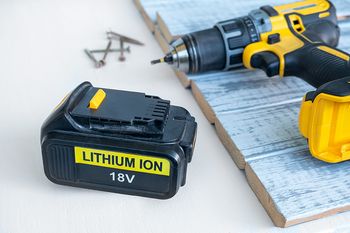
The number of electrical connectors and electronic circuits in devices such as cars, planes, appliances, industrial machinery, trucks or boats is continuously growing. Failure of these components, from short circuit to continuity loss, present a major concern as issues can vary from nuisance to increased warranty costs to critical safety problems. The constant exposure to moisture, corrosive environments, and vibration can also accelerate the failure or malfunction of components.
As the complexity of control systems increases, the number of pins on multi-pin connectors continues to grow. Mating multi-pin connectors often requires significant force – creating the potential for incomplete mating, as well as repetitive-motion injuries for assembly workers.
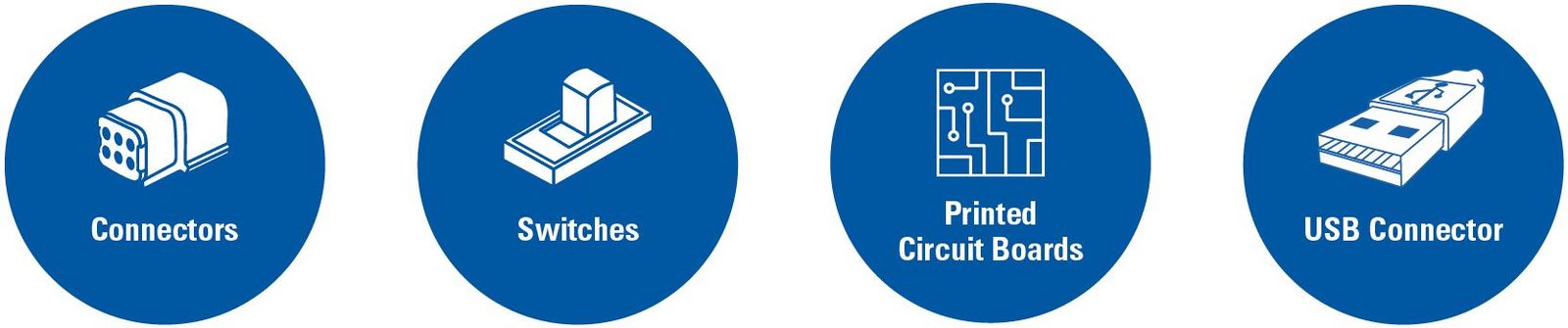
Why should electrical contacts be lubricated?
Reduction of friction
A thin film of lubricant can reduce mating force by as much as 80 percent, an important factor in connector assembly. For electronic connectors with dozens or even hundreds of pins, or for automotive connectors that are in hard-to-reach places, a low insertion force makes assembly more efficient and ensures solid connections.
Protection against oxidation
Lubricants guard against oxidation and the effects of harsh environments. With gold-plated connectors this means protection against substrate corrosion. Thin gold plating can be microscopically porous; and a thin film of lubricant can seal the pores, prevent substrate attack and assure low contact resistance.
Preventing fretting corrosion
In addition to atmospheric corrosion, tin/lead connectors are also subject to fretting corrosion, which is mainly caused by vibration and shock. Fretting corrosion continually exposes fresh layers of metal surface to oxidation. A lubricant film minimizes metal-to-metal contact during vibration, protecting the connector from metal wear.
Advantages of lubricating electrical components
- Extend functional life of components
- Improve reliability of connections
- Seal & protect from environmental elements
- Prevent fretting wear & corrosion
- Reduce insertion force
- Insulate against electrical short circuits
How to select your connector grease
Connector greases from Nye Lubricants are compatible with most materials used in connectors. They are designed for long-life and performance in high temperature and severe environments. Nye greases are available in a variety of packaging sizes for both high-volume production dispensing and small volume dispensing, such as field repair activities.
NyoGel 760G | Leading connector grease across several industries with specification at a wide-range of leading OEM's. Good fretting corrosion protection and dielectric isolation capabilities. Compatible with common connector materials.* |
Rheotemp 768G | Similar performance as NyoGel® 760G, with a higher maximum temperature capability of 175°C.* |
Rheotemp 769G | Formulated to offer outstanding dielectric performance, reduction of insertion force, and fretting wear protection.* |
Uniflor 8917 | Recommended for applications with high operating temperatures up to 225°C. Compatible with a wide range of plastics and elastomers. Excellent insertion force reduction. |
*contains UV dye for application validation
Overview of Nye connector greases
Product | Fretting Wear Protection | Dielectric Performance | Insertion Force Reduction | Water Resistance |
NyoGel 760G | good | good | good | excellent |
Rheotemp 768G | good | good | good | excellent |
Rheotemp 769G | excellent | excellent | good | excellent |
Uniflor 8917 | excellent | good | good | poor |