Reduced tooling and oil costs as plant moves to condition based management strategy
Industry: OEM Manufacturer of automotive components
Application: Chemical Process Management
Solution: FUCHS Smart Services
Limited resources make it difficult to isolate problems and find solutions. Our customer recognized this and brought in the FUCHS Service Team to focus on managing and maintaining the condition of their oil in their plant. We identified the factors that impacted performance, drove consumption, and ultimately led to waste generation. Although fluid condition improved dramatically in driving tool failures down, better resource management resulted in lower oil cost per part manufactured. In addition to those directly measured benefits, the most significant strategic advantage the plant realized was the time their technical resources now had time available to start improving their core processes.
Key Benefits
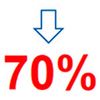
Reduction in fluid cost per piece
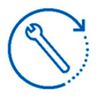
Significant reduction in reactive events leading to higher OEE
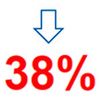
Reduction in total breakage
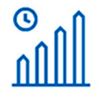
Sustainable continous improvement
Challenge
Several variables negatively impacting tool life made it difficult for this automotive parts manufacturer to determine true root cause. With so many potential sources for pre-mature tool breakage, the manufacturer´s technical resources were spread too thin, and the facility was caught containing issues instead of resolving them.
Solution
By letting FUCHS Service´s Team focus on maintaining oil condition within identified operating limits, the facility was able to take fluid condition variability out of the equation giving them the time they needed to be able to determine true root cause.
Results
By focusing CPM services on oil condition, tool breaks have gone from 4.4 breaks per 1000 Pcs, to 2.6 Breaks, representing a 38% improvement. Through testing and better utilization of on-site recycling technologies, not only did fluid performance improve, but we were able to reduce the fluid cost per part from 1,75€/piece to less than 0,50€/piece, a greater than 70% improvement in per piece costing.
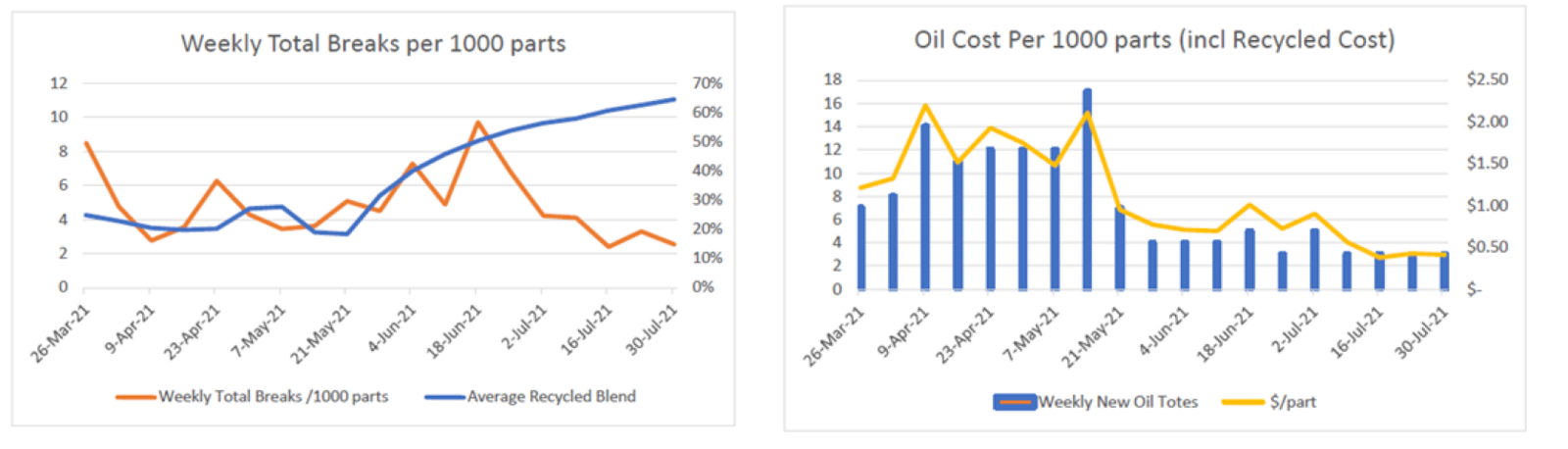
Controlling the KPI’s that impact performance
By implementing a robust fluid condition-based program, where we were sampling, analyzing, interpreting, and taking corrective action to keep their fluid KPI’s within identified operating limits, we were able to establish and maintain the capability of their process. By eliminating the variability that was a root cause to a significant % of their tool failures, they were able to start putting controls and identifying the other process variables that were impacting tool life.
Sustainable Continuous Improvement
The plant is now on a path to improve their process across the board. The FUCHS Service Team can focus our resources on the various fluid applications that negatively impact OEE, while the customer can focus on process improvement and waste reduction.
Do you need more info?
If you need help to improve your processes and want to know more about our services, don´t hesitate to ask for our expertise. We will be more than glad to help you focus on what is important for you.