FUCHS Smart Services
There’s more to lubrication than just oil
FUCHS Smart Services bring far more to the table than “just” a product. Instead, we combine performance fluids, digital technologies and a wide range of services into customized solutions. Solutions that do not only fit your individual processes perfectly but strive for improvement – along every step of the way and beyond.
Pushing forward – with a reliable partner
At the very core of everything we do is a promise of reliability. We move your world – not just to keep things running at all times, but to improve your whole production process. To do so, we constantly look ahead and at the big picture. A holistic approach that encompasses ecological, social and economic aspects.
What drives our process
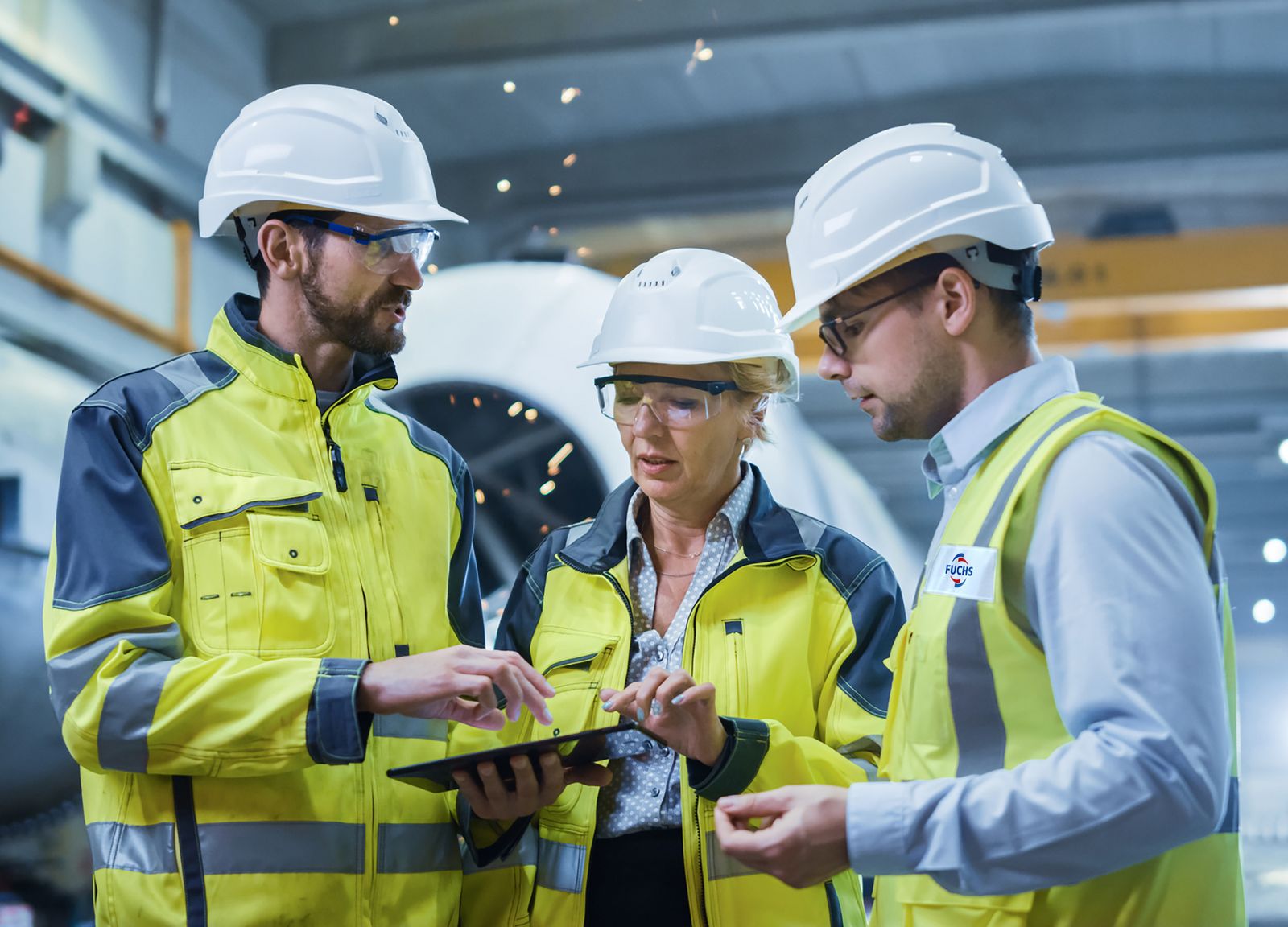
In order to move your world, we believe it‘s essential to become an integral part of it. Sharing not only data but also new ideas, technologies and processes. In turn, this allows us to integrate our expertise and tools into your business as well as your equipment. For example with experienced on-site technicians or remotely connected experts but also through ready-made sensor based solutions and sophisticated software for self-service. All to identify and prevent problems before they arise.
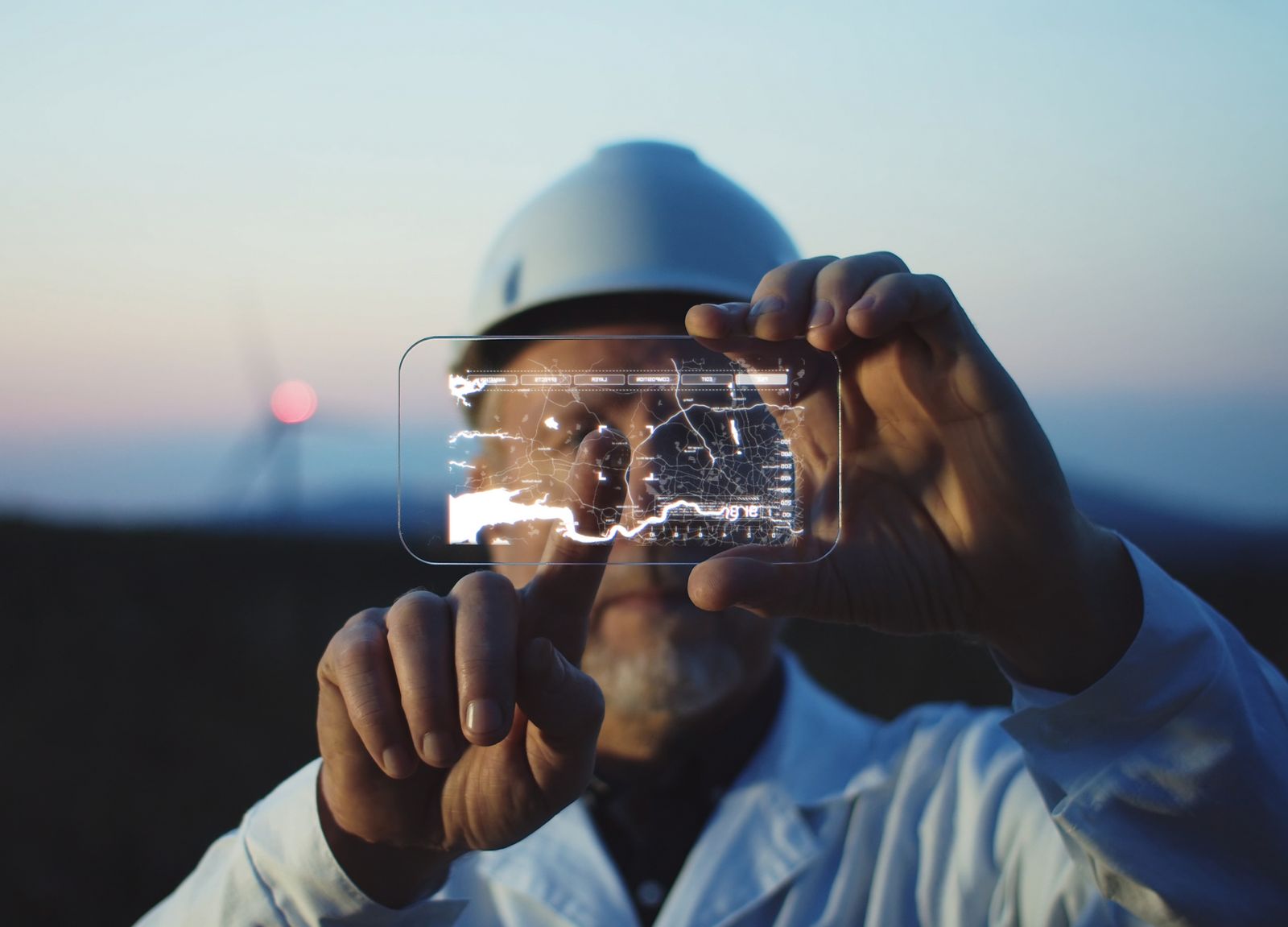
Transparency and insight are key to everything we do. Established with precise data and expert review, they allow us to identify untapped potentials – and work together more closely in order to achieve them – for example by monitoring the condition of products and machines or improving your processes.
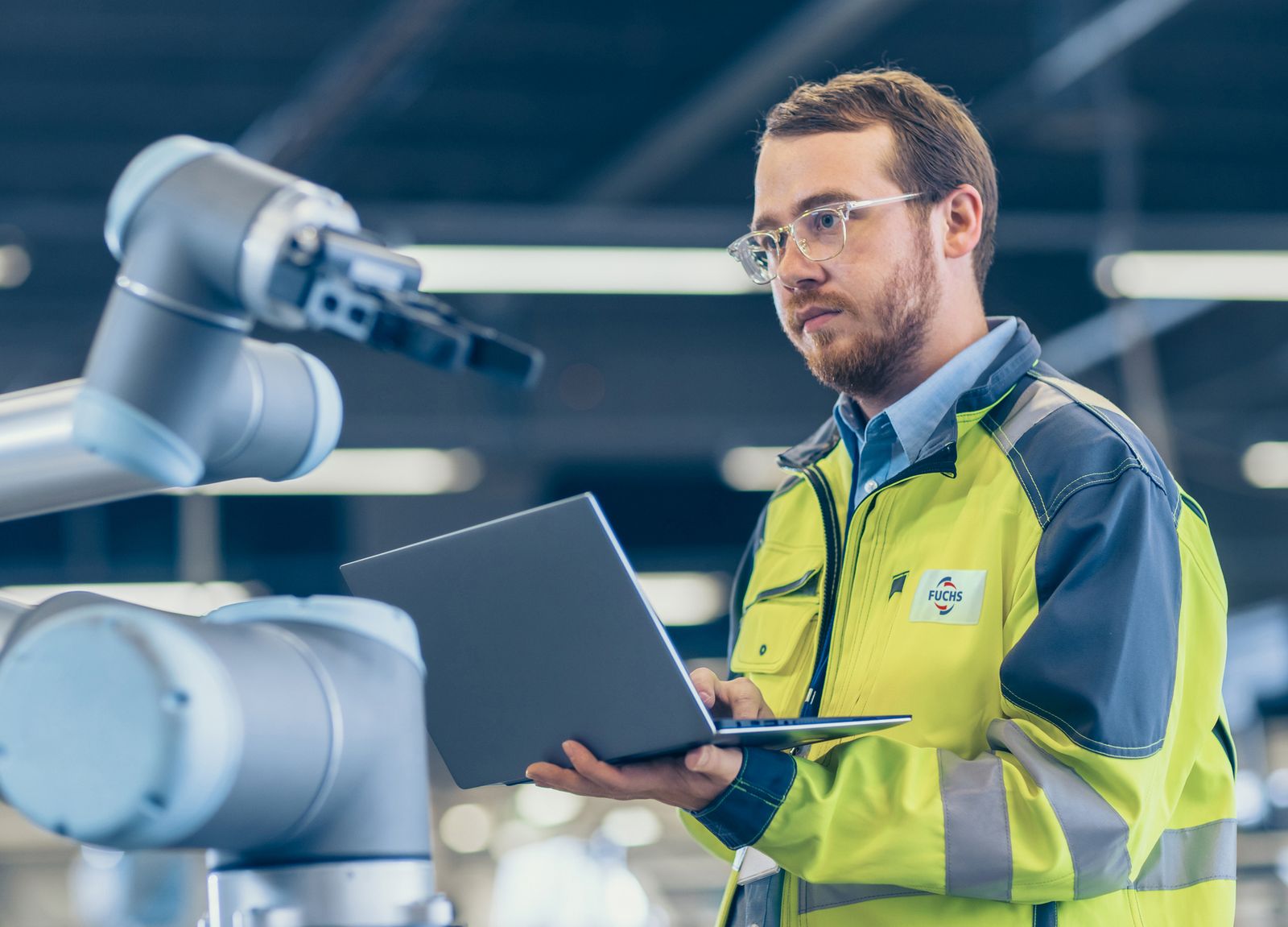
Maximum machine availability and minimized total cost of ownership are what we strive for. To achieve these goals, we leverage a solution-driven mindset and interdisciplinary expert knowledge along the entire lifecycle. An approach that enables us to take care of everything from air-leaks to zero-waste policies.
The approach
FUCHS Smart Services bring far more to the table than “just” a product. Instead, we combine performance fluids, digital technologies and a wide range of services into customized solutions. This starts with an analysis of your situation and processes. Together, we then create a solution that perfectly matches your goals. This might be an individual product, services (such as training or maintenance), a digital solution, or everything together as a complete package.
Customized solution
Modular is our standard
Our solutions’ basic pieces are completely modular and can be combined freely to suit your specific situation and goals. Regardless of its constituents, your solution will always be based on the holistic FUCHS process.

Understand - Assess and Analyze
FUCHS works with customers to optimize lubrication applications that affect their manufacturing processes and evaluate new lubrication solutions. Their work helps manufacturers implement best practices. Our engineers specialize in Food Grade, Heavy Industrial, Metalworking and Metal forming sectors.
Our Food Industry specialists are trained to survey and perform risk assessment of lubrication critical control points. Our LCCP assessments include lubricant properties, type of maintenance and frequency, secure storage and dispensing in order to minimize potential risk.

Develop - Service Offerings
There’s more to lubrication than just oil! Proper fluid selection and application are critical to reducing total process costs. We use a data-driven approach to select products that will optimize performance in your application while reducing fluid and waste costs. Our team also helps determine the appropriate fluid application to support your process.
The In-Process Product Management (GPP®) laboratory is part of after-sales service at FUCHS Spain, where samples of in-service products are analysed. This analysis is important for preventing potential failures, maintaining the service life of the fluid and detecting anomalies in the fluid and associated equipment.
The products analysed include those intended for machining, whether oils or water-soluble fluids.
We help to identify wasted resources and to design and implement a customized solution focused on optimizing fluid usage and disposal. We design customized on-site recycling solutions that help facilities maintain fluid quality while reducing process costs and achieving their sustainability goals.

Manage - Implement and Operate
CPM is a carefully managed, structured system of operations in which all aspects and consequences of fluid usage are monitored and assessed.
Open gear applications are always among the most critical lubrication points. In addition to manufacturing a wide range of lubricant solutions customized to open gears, FUCHS experts offer routine inspection to ensure trouble-free operation and confirm maintenance program effectiveness.

Optimize - Finetune and Reuse
A dedicated application engineering department pools the experience gained from thousands of customer use cases and close cooperation with the product management departments and research and development.
The lubrication processes are assessed in a well-founded technical manner, allowing problem solutions and optimizations to be developed in a focused way. The measures developed are supported in trials and continuous operation and are surveyed and controlled with the help of monitoring solutions.
The optimization check offers the possibility to analyze defined questions regarding the use of lubricants in a well-founded manner. The process is analyzed, key figures are derived and evaluated. This results in actions to achieve optimizations.
In this way, contributions are made to sustainability and CO2 reduction, to effort and cost savings and to the improvement of TCO. Finally, safety is improved by compliance with environmental and occupational health and safety regulations.
Manage options
Manage options
No matter the circumstances you operate in or the challenges you face – we’ll find a suitable way to deliver our services, tools and lubricants. In order to facilitate this level of customization, the options to implement your solution range from one time visits – for instance to set up a piece of technology – to more long-term support. For example, the continuous remote analysis of your lubricants condition or the on-site management of stocks and waste.
Digital solution
Information as a service
Data collection, integration and aggregation
Software as a service
Information access, visualization and analysis
Management as a service
Remote service and on-site management support