Lubrication technicians – specialists with tremendous potential
They’re specialists, but their potential is rarely acknowledged. They’re the lubrication technicians, key players in all preventive maintenance. The right support can boost their efforts and lead to some genuinely vital results: fewer technical problems and breakdowns.
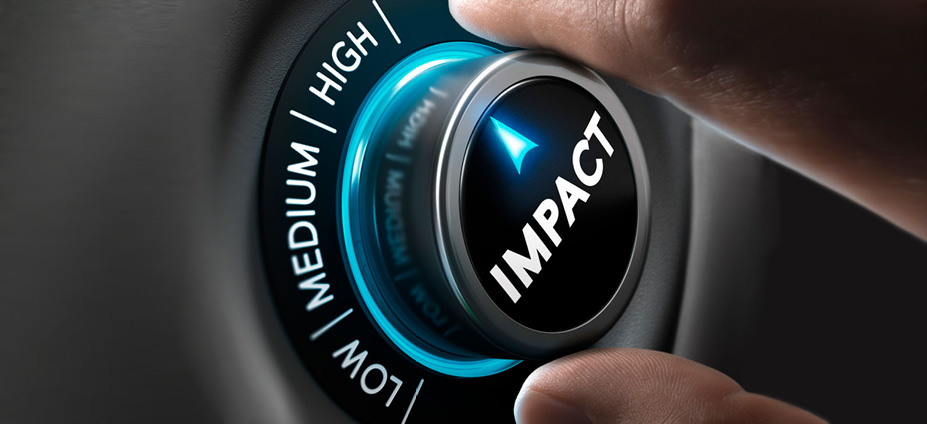
I have worked with maintenance in industry for a long time, and every year I visit a wide range of companies in different sectors. One thing I have noticed is the way companies view their lubrication technicians, by which I mean the people who take care of the actual day-to-day lubrication. Through their efforts, they play a key role in ensuring that the machinery keeps on working, and that the wheels of production keep on turning.
INVEST IN YOUR LUBRICATION TECHNICIANS
It seems to me that companies sometimes don’t realise the potential of this group. This potential is closely linked to preventive maintenance, which for me is completely dependent on two fundamental factors: clean & tidy, and lubrication. If these two factors are not in place, it is very difficult to work efficiently with preventive maintenance. There’s hardly any point in performing thermal imaging, inspections and vibration measurements if the lubrication isn’t up to scratch. So, this article contains a few tips to encourage companies to invest in their lubrication technicians – it definitely pays off, not least in fewer technical problems and breakdowns.
PROVIDE THE NECESSARY KNOWLEDGE
First off, make sure your lubrication staff have the knowledge and skills they need. Sometimes lubrication ends up being a routine task inherited from a predecessor, and often no one questions whether things could be done better or differently. The key here is to make sure that everyone involved knows the how and why of lubrication. Therefore, it’s important that this information is documented in the company, and that it’s maintained and updated as changes are made.
Also make sure that competence development is a regular occurrence, so that everyone’s knowledge is fresh and up to date. Send lubrication technicians on a course with a specialist company, or ask your lubricant supplier for some customised training. Another option may be to work with a large company. For instance, SKF hold courses on lubricating bearings.
MAKE THEM VISIBLE
Also, don’t forget day-to-day recognition and acknowledgement. Listen to the lubrication staff, give them a voice and let them have their say. They might for instance have an obvious place in the maintenance organisation, attending maintenance and technical meetings and sharing their knowledge and opinions. In many organisations, most of the information travels from the top down. There is a chance here to increase the flow from the bottom up – and in a crucial area that has a direct impact on the company’s productivity. This approach also sends out a clear signal that lubrication is a vital area.
THE RIGHT COMPENSATION – AND JOB CONTENT!
My third tip is about pay. In one company, I found out that the mechanics who repaired machinery earned more than the lubrication technicians. So the message there was that it’s worth more to repair broken machinery, than it is to maintain it and make sure it doesn’t break down in the first place. That’s backward thinking. Pay is an important carrot, and also increases the chances of recruiting good people. And speaking of recruitment and job content: consider whether the role of the lubrication staff can be expanded to include more aspects of preventive maintenance, such as vibration measurement or analyses of various kinds. Many people feel that this adds ‘status’ to the job, and it can be very positive for the employee and the company alike.
YOU MEAN THE TRIBOLOGISTS…?
Finally, I’d like to highlight a positive example from a sawmill I work with. They have given lubrication staff a higher status, bringing them into the maintenance organisation and thus tackling maintenance in a more holistic way. Feedback works better, and competence development also has a natural place on the agenda. And last but not least, they don’t call their lubrication technicians, lubrication technicians. They call them tribologists. If you happen to call them lubrication staff, straight away you’ll get corrected: “You mean the tribologists…?” Now that is an approach I can certainly get behind. So don’t wait around – invest in your lubrication technicians! Sorry, tribologists!
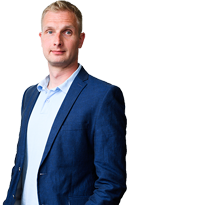
This might also interest you
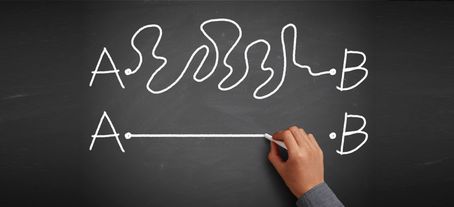
Four rules of thumb in lubrication – your shortcut to savings!
Every little helps, as they say. And this is certainly true of maintenance costs. Because making many minor improvements in your lubrication maintenance adds up to major savings. These minor measures may be many, but that doesn’t mean they’re complicated. I like to sum it up into four rules of thumb, which makes it all a whole lot easier.
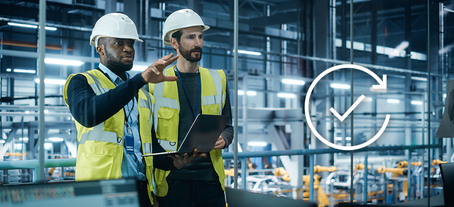
Ten tips that deliver big time
Store and use your lubricants correctly. You have so much to gain. And to help you, I’ve put together ten great practical tips. The little extra effort will pay for itself many times over, making your lubricant management easier, safer and smarter.
All blog posts
Subscribe
Available in Finnish only.
Smart Lubrication
Smart Lubrication is a blog from FUCHS where we share our common knowledge about lubricants and lubrication.