What exactly is a grease?
A grease is like a sponge
A grease usually consists of three components. In a carefully controlled process, these components are combined in finely balanced proportions to produce a highperforming end product.
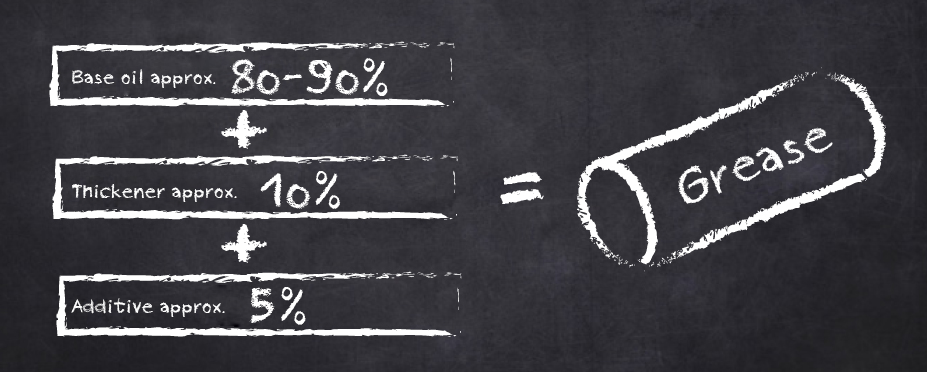
ASTM, the American Society for Testing and Materials, has defined a grease as: "A solid to semifluid product of dispersion of a thickening agent in liquid lubricant. Other ingredients imparting special properties may be included."
Another, simpler way to describe a grease is to think of it as a sponge. The thickener is the sponge and the base oil is the water. The thickener in the grease creates a matrix that keeps the base oil in place in a solid structure and gives the grease its consistency. When the grease is subjected to different operating conditions such as temperature, loads or shearing, a viscoelastic flow is created in it. The plasticity of the grease, its consistency, is generally given a number according to the NLGI grading system. Semifluid (00) to normal (2) are the most common.
Greases are is primarily used in ball and roller bearings, as well as slide bearings, gearboxes and open gears. Nowadays greases are also increasingly used in forest machines for central lubrication of the cutting bar and chain.
A grease stays put
A grease should reduce friction in areas where a lubricating oil would simply vanish. However, it should also seal and block, keeping water out and sealing against gas, for instance. Quite simply, it should be in place.
A grease should:
- Provide good lubrication, reduce friction and wear
- Seal the lubricated area to prevent dirt, water and pollutants getting in
- Protect against corrosion
- Remain in the lubricated area and not leak, drip or be dashed out
- Be compatible with the sealing material and other component materials it comes into contact with
- Not alter to either solidify or soften when the bearing is repeatedly worked mechanically during the lubrication interval
Base oils in greases
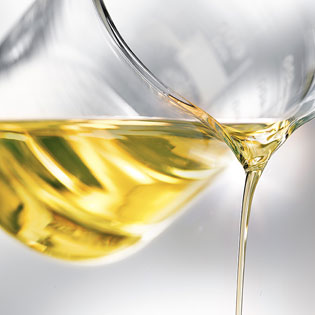
Since a grease is 80-90% base oil, the base oil is an important part of the end product. The choice of base oil has a great impact on the grease's performance. Mineral oils are the most common base oils used in greases. However, synthetic base oils can produce properties that mineral oils simply cannot.
Synthetic base oils are the optimal choice when a product is needed that has a broader temperature interval and greater chemical resistance. Synthetic base oils also have better electrical properties.
The use of greases based on synthetic base oils is increasing, even though they are often slightly more expensive. The higher cost is balanced out by the longer lubrication interval, improved performance and lower maintenance costs.
Some of the more common synthetic base oils are polyalphaolefin (PAO) and esters. Certain types of synthetic ester can be used advantageously in formulating biodegradable greases.
Some of the benefits of synthetic base oils:
- Low volatility
- Improved thermal and oxidative stability
- Higher viscosity index
- Improved fluidity at low temperatures
- Lower internal friction
- Better corrosion protection
- Contain no aromatic hydrocarbons
Thickener – The body of a grease
A grease's character is largely determined by the type of thickener used. The thickener is responsible for the structure that keeps the oil in place inside the grease. Properties such as mechanical stability, water
resistance, melting point, sealing capacity and re-lubrication interval are all attributable to the thickener.
Grease is usually made by saponifying fatty acids with metal hydroxides. However, there are also soap-free thickeners, such as those based on the NOVA technology. Thickeners can generally be divided into two main groups: soap-based and non soap-based thickeners, soap-based being the most widely used. Soap-based thickeners in turn can be divided into various subgroups depending on their chemical composition.
The properties of some common thickeners
The properties of some common thickeners | Water resistance | Thermal stability | Shearing stability | Load-bearing capacity |
---|---|---|---|---|
Lithium (Li) The vast majority of greases are based on lithium 12-hydroxystearate | * | * | * | * |
Lithium complex (LiX) Increasing in popularity compared to traditional Lithium-thickened grease. Broader area of application | * | *** | *** | ** |
Water-free calcium (CaH) Applications in wet environments. E.g. chassis lubrication | *** | * | ** | * |
Polyurea (PU) Excellent thermal stability. Lower corrosion-protecting and load-bearing capacity | * | *** | * | - |
Calcium sulfonate complex (CaSX) Excellent load-bearing capacity Part of the 'functional thickeners' group | *** | ** | *** | *** |
Lithium/Calcium complex (LiCaX) Excellent properties, e.g. lubrication of open gears Part of the 'functional thickeners' group | *** | *** | ** | *** |
In addition there are variations and other thickeners. We see great potential for the future and for best performance in the NOVA technology, as well as in functional soaps.
Water resistance | Low temperature properties | Additive response | Compatible with other greases | |
---|---|---|---|---|
The NOVA technology Read more about this here | ** | *** | *** | *** |
*** Excellent | ** Very good | * Good | - Poor
Additive enhances performance
Additives lend a special character to the grease in the form of targeted performance. The additives used in greases are very similar to those used in liquid lubricants.
Some common additives and their function:
- Antioxidants increase resistance to oxidation, lengthening the life of the grease
- Corrosion inhibitors protect against corrosion
- EP additive (Extreme Pressure) counteracts seizure under high pressure
- Anti-wear reduces friction and the risk of wear
- Paste lubricants, e.g. molybdenum disulphide and graphite, which protect against wear and reduce friction under heavy load and low speed
More about grease
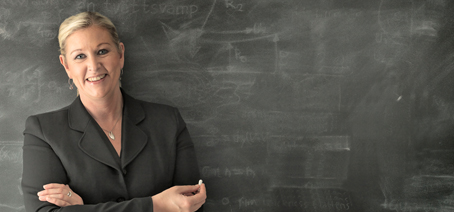
"Greases are high-tech"
"In many ways successful lubrication is more about knowledge than the actual lubricant. Machines are becoming increasingly complex, and they need to work smoothly without causing expensive downtime. Inadequate lubrication is the cause of most bearing damages. Our extensive work with varying applications has brought us in-depth knowledge, knowledge we are happy to share to prevent damage from arising. Recommending the right grease in demanding environments, varying temperatures and varying operating speed under heavy loads is all based on knowledge. At FUCHS Lubricants, we have the knowledge and of course the products to get the job done."
Maria Wilén, Product Manager Industry
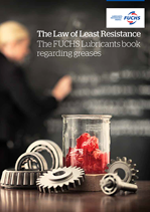
Handbook
The Law of Least Resistance - The FUCHS Lubricants book regarding greases.