Cutting emulsion compared to cutting oils
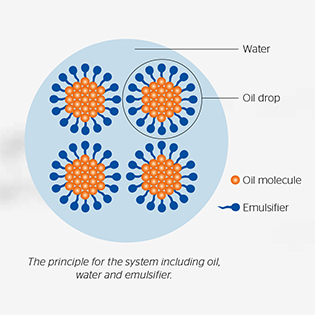
Cutting Emulsion – Water-Miscible Fluids
Emulsions (coarse emulsion, macroemulsion)
The most common fluids for metalworking are emulsions. An emulsion is made by mixing a concentrate into water, never the other way around. The concentrate consists of a mineral oil and possibly a synthetic ester, along with an emulsifier and other additives. When the concentrate is mixed with water, a milky-white emulsion is formed. The concentrate is mixed to different concentrations depending on the process and the metal. This type of product can vary from the technically relatively simple to a highly sophisticated formulation.
Semi-synthetic (microemulsions)
It is possible to vary the size of the oil drops using different types of emulsifiers in different quantities. It is therefore possible to produce emulsions with very small oil particles. Such emulsions are clearer than normal and are called semi-synthetics or microemulsions.
Synthetic fluids (solutions)
Synthetic fluids do not contain mineral oil but are often based on glycols. There are also synthetic fluids that do not contain any lubricating components. These are used as grinding fluids. Unlike emulsions, such liquids are entirely soluble in water, and the resultant solution is normally very clear and transparent.
Cutting oils – neat oils
Cutting neat oils are particularly stable. No further maintenance is generally needed other than filtering and centrifuging the fluid to remove swarf and impurities.
A straight cutting oil rarely has to be changed as it is normally used in the process as it follows the machined parts and swarf, so it constantly needs refilling. The exception is if the oil starts to oxidise, or if the levels of metal particles or sediment give rise to problems.
There is also an application method known as minimum lubrication, whereby a small amount of oil is sprayed into the air and then applied to the machining area under high pressure. The benefits are very low oil consumption and a reduced cleaning requirement. The drawbacks are swarf management and inadequate cooling. Consequently, minimum lubrication can only be used for certain processes and metals.
Learn more about cutting fluids
Downloads
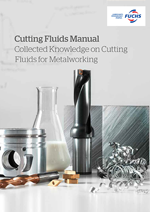
Handbook
Collected Knowledge on Cutting Fluids for Metalworking