Greases for Machine Tools
In general, the most important lubrication points for lubrication applications in machine tools can be divided into the following areas:
• Spindle bearings,
• Chucks
• Transmissions.
Grease lubrication for spindle bearings
Because of the high risk and the significant blow of the mechanical parts, a level of major requirement is present for the choice of these greases:
• High load resistance and high wear resistance
• Centrifugal hold and at very high speeds
• Effective corrosion protection for long component life
• High resistance to coolant (especially with open bearings)
• High adhesiveness due to tightness
Due to these high stresses, especially with respect to lifetime lubrication and very high speeds, FUCHS recommends the use of a low viscosity synthetic oil based grease specially developed for this purpose and validated in original equipment by a manufacturer. large number of machine and user builder: RENOLIT HI-SPEEED 2
Chuck greases
Mandrel greases are subject to special requirements. Indeed, you must ensure a safe separation of friction antagonists to avoid frictional corrosion, but also ensure a constant clamping force and thus ensure contact between parts.
In addition, these greases must have good resistance to cutting fluids because of the metal working environment in which they are used, and this, in order not to be washed out after a short period of time.
Our references to this post are:
RENOLIT CHUCK PASTE is specifically developed and approved for this use. (95% of uses)
RENOLIT PASTE PW is specially designed for extreme constraints for which RENOLIT CHUCK PASTE is no longer sufficient. (5% of uses)
Gear greases
1. Lubrication of the crankcase
In it, one or more gears dive into a crankcase comparable to the oil sump. Excess grease entrained is rejected on the housing housing wall where it is again available for lubrication.
2. Adhesive lubrication
With this principle, the grease used is much more consistent and adheres to the gears. The excess grease is not ejected but pushed out of the lubrication point and remains in close proximity to it. In this case, constructive measures must be taken to ensure that the grease can be returned to the lubrication point during downtime and that it does not run out in the long term.
3. Lubrication via a centralized lubrication system
Here, the grease required for lubrication is transported from a central tank to the various lubrication points. Excess grease is removed, as when crankcase lubrication, but it is lost here and is no longer available for lubrication.
When this solution is present in the field of metalworking, then the different cutting lubricants can enter the gear. The grease must withstand these environments and also offer good protection against corrosion.
Reducer greases are selected according to the respective requirements for speed and load of the gearbox. At higher speeds, greases with low viscosity oils are used. As the speed decreases or the load increases, the grease is used with a corresponding viscosity of the base oil.
The use of greases with too high and unsuitable base oil viscosity can lead to overheating.
• If the viscosity of the base oil is too high, the internal resistance of the grease to the movement is too high and yield losses result in very often a significant increase in temperature and premature wear.
• If the viscosity is too low, the separation effect of the lubricating film is insufficient and the metal friction also causes heat and wear.
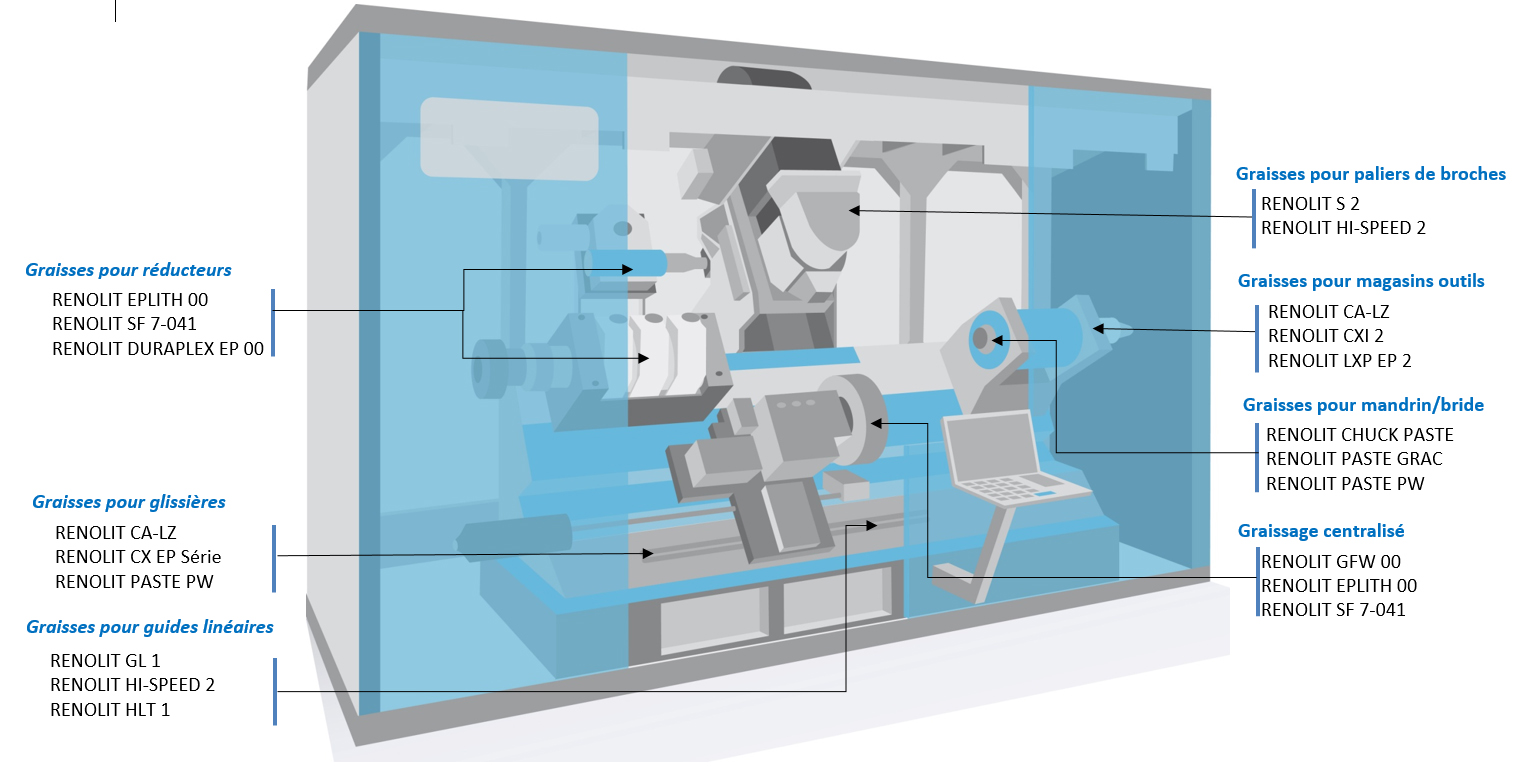
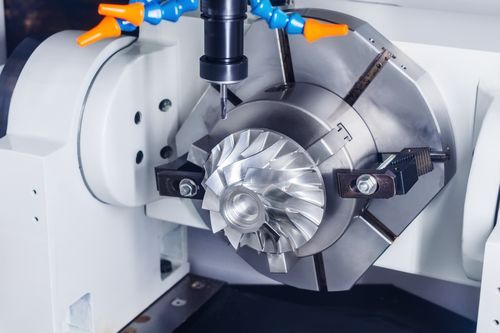