Case: Cementa
“Without lubricants, the plant would grind to a halt!”
With thousands of tonnes of cement being produced every day and machines working under extremely tough conditions, Cementa has to know that everything is working as it should. Preventive maintenance with the right lubricants is a vital factor in keeping the plant running.
As a visitor to the Cementa site in Slite, it’s easy to feel small and insignificant. There are gigantic gravel pits with steep walls tens of metres high, and enormous, powerful machines that work round the clock to produce cement.
The company Cementa has a tradition of making cement since 1871. Although this long history is clearly visible in Slite, where beautiful old buildings have been preserved, today it is one of the most modern and environmentally sound cement works in Europe.
The plant has around 230 employees as well as 200 subcontractors. Cementa produces more than 7,000 tonnes of cement a day, which is a mind-boggling 2 million tonnes a year.
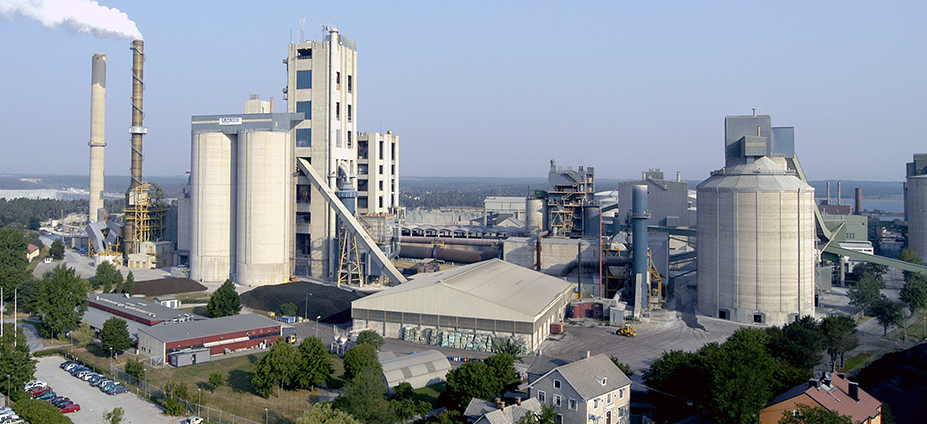
– “Our greatest challenge lies in keeping the plant up and running 24 hours a day, and maintaining high operational reliability. We do this with correct lubrication and good preventive work. The machines in the works are subject to heavy loads and high temperatures, so it’s vital that our lubricants are of high quality,” says Håkan Lindqvist, a mechanical engineer who knows Cementa inside-out after almost 30 years with the firm.
In 2014 Cementa starting working with FUCHS. The collaboration started out with a Plant Survey looking at all the plant’s machines and over 3,000 lubrications points.
– “We performed a meticulous survey at Cementa, looking closely at the entire plant and choosing the right lubricant for each individual lubrication point. After the survey, we were able to reduce the number of different products by more than 30%. Needless to say this saved Cementa a lot of money, not only in lower warehousing costs but also because there’s less risk of using the wrong product for the various lubrication points,” says Jan Alm, Application Engineer at FUCHS.
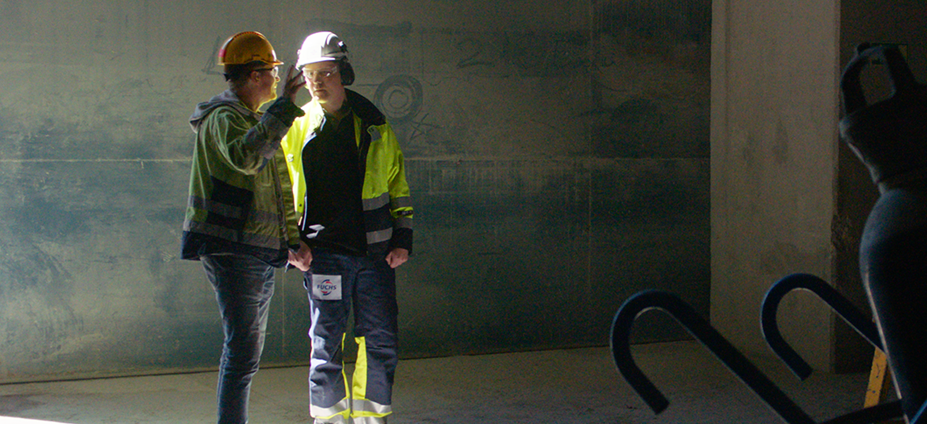
Plant Survey brings more benefits than just lower costs: it’s better for the environment, since products with a longer life reduce the volume of waste and the amount of transport to and from the plant. It also leads to greater efficiency.
– “After the Plant Survey, FUCHS put up signs at the various machines which show which lubricant to use. This is important for the lubrication staff and makes their job easier,” Håkan Lindqvist confirms.
To assure operational reliability, a force of 20 or so people at Cementa work in preventive maintenance daily, and five of them are lubrication staff. Making their job easier is an important aspect of the collaboration with FUCHS, who conducted the Plant Survey with the help of lubrication staff and other on-site personnel.
– “It’s important that we have a dialogue with the people who are out in the plant and know it best, and that’s the lubrication staff,” says Jan Alm.
But of course FUCHS’s service doesn’t stop after the Plant Survey; it is an ongoing feature of the collaboration. To keep an eye on how the machines and the lubricating oils are performing, FUCHS offers an oil analysis solution, whereby Cementa takes regular oil samples from important machines and sends them in. In return they get a report which shows how the machine and the oil are doing.
– “FUCHS have always provided excellent service. Our bulk products have a scanning system which senses when the lubricant is running out and places ongoing orders automatically,” says Lindqvist.
– “FUCHS’s expertise is very important to us. We’re in constant contact and they are often here visiting, so we can ask them for advice. We tour the plant together and if there’s a problem, we take a closer look at it. Without lubricants, the plant would grind to a halt!”
All customer cases
Case: Moelven
Good day-to-day dialogue – the key to stable collaboration
Case: Nynas
Oil switch brought record saving
Case: Scana Steel
Rapid assistance for Scana Steel Björneborg
Case: Cementa
"Without lubricants, the plant would grind to a halt!"
Case: ECOCOOL EAL
Quality and precision demand the right solution
Case: RENOLIT NOVAWAY
A less conventional solution that produces top results
Case: ECOCOOL BOOSTER L1
The right lubricant saved over SEK 795,000 a year
Case: Product development
Smart product development simplifies propeller replacement