Inspect and Analyse
Around 80% of all machine breakdowns are due to contaminated oil and poor filtering – but most of them could be avoided with regular checks in the form of analyses and other inspections of the oil and filters.
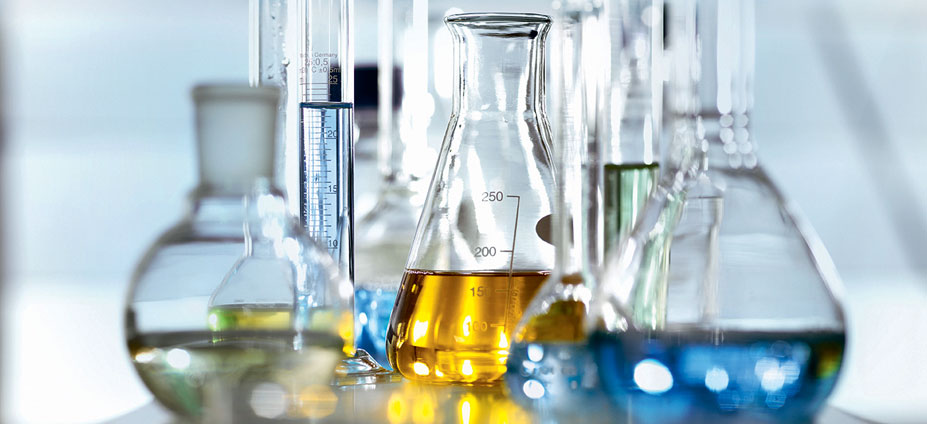
Visual inspection
In small systems it is not really financially viable to conduct regular lab analyses on the hydraulic oil, but doing a basic visual inspection every week (or a similar interval) will protect the system against disruptions, damage, and sudden unexpected stoppages.
Here is a useful chart for visual inspections:
The oil’s appearance | Possible cause | Action/recommendation |
---|---|---|
Light and clear | Normal | The oil can be used |
Turbid, unclear | The oil is contaminated with emulsified water | Analyse/change the oil |
Free (entrained) water | The system is contaminated with water | Drain the water |
Dark, smells burnt | The oil has oxidised | Analyse/change the oil |
Visible contaminants | Contaminants, wear particles | Analyse/change the oil/check filters |
Oil analysis
In large hydraulic plants, which often contain hundreds of litres of hydraulic oil, it is common to regularly check the status of the oil and the system via oil analyses.
An oil analysis can answer questions such as:
- What is the condition of the oil?
- Is there any severe wear?
- What type of wear?
- Where in the machine is the wear happening?
- Is the pipe system clean?
- Is filtration working as it should?
- Does the contaminant level in the oil risk causing problems in the future? E.g. wear, corrosion, jammed valves etc.
Regularly analysing the chemical and physical state of the oil makes it possible to identify machine problems before they grow too big, reduce down times, plan maintenance intervals, reduce maintenance costs and optimise oil drain intervals.
Troubleshooting in a hydraulic system
Troubleshooting | Possible cause |
---|---|
No movement on start-up |
|
Too slow movement |
|
Uneven movement |
|
Movement stops during operation |
|
Operating pressure too low |
|
Abnormal noise in the system |
|
Oil gets too hot |
|
Foaming oil |
|