What are cutting fluids made of?
Metalworking fluids can be divided into water-miscible fluids (emulsions, semi-synthetics and synthetics) and neat oils.
Water-miscible cutting fluids
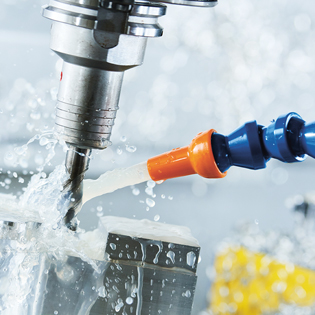
Emulsions are the most common type of cutting fluid today. An emulsion is made by adding a concentrate to water to form a milky product. The appearance of an emulsion varies with the type of product and the size of the oil drops. Larger oil drops give a more cream-like colour, while smaller drops give a more transparent emulsion that looks like very low-fat milk.
There are also concentrates that contain no oil; these give a transparent emulsion and are called synthetics.
Cutting fluid concentrates are comprised of base oil, esters and fatty acids, emulsifiers, rust protection, pH-regulating additives, biocides and anti-foaming agents. The properties of the emulsion can be altered and varied by changing the levels of the constituent components. The products are normally used at a concentration of 4–10%. Water-miscible cutting fluids have excellent cooling capacity. In industry, the need for products with good cooling capacity has increased. This is because new machines run at higher speeds, which generates more heat.
Water-miscible cutting fluids are cheap compared to straight cutting oils. The drawback of water-miscible cutting fluids is that they have to be checked frequently to make sure the concentration is right. If the wrong concentration is in the system the result is lower productivity, corrosion problems, and possibly also bacterial growth.
Emulsion – structure
- Base – Mineral oil, esters
- Emulsifier/tenside – Sulphonates, soaps, synthetic tensides
- Corrosion protection – Sulphonates, soaps, amines, fatty acid amides
- pH regulators – Alkylamines
- Wear protection – Mineral oil, esters, sulphur/phosphorus compounds
- Biocides – Not common today
- Anti-foaming agents – Silicon oils, wax emulsions, calcium compounds
Synthetics have the same structure as emulsions, with one exception: they do not have mineral oil as the base.
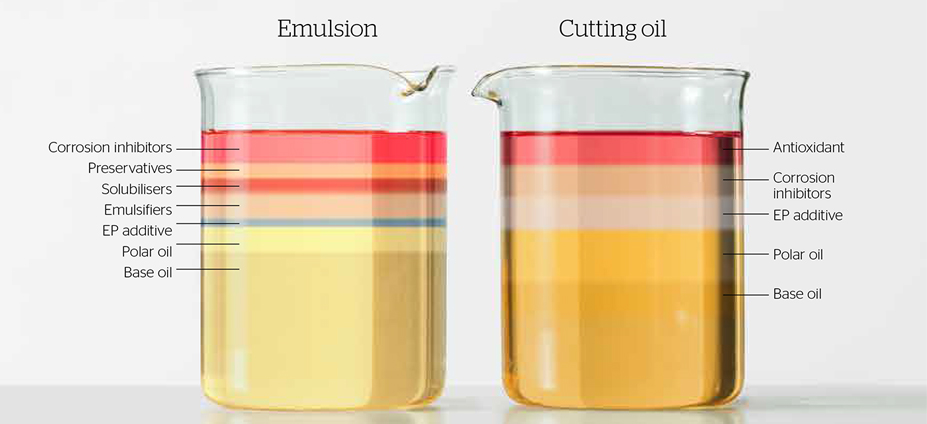
Cutting oils
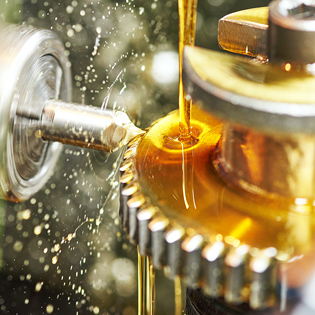
This type of product is not mixed with water, but is applied directly. Neat cutting oils are primarily used when good lubricating properties are required, such as in deep-hole drilling, threading and reaming.
Cutting oils have different viscosities, base oils and additives depending on the processes and which metals are being machined. Mineral oils, synthetic oils, white oils and esters are used as base oils. ‘Fatty oils’ are also often added (such as vegetable oils, animal oils or esters) to protect against wear. EP additives are also sometimes used (e.g. sulphur, phosphorus or chlorine). This type of fluid has better lubricating properties than the water-miscible ones, but has less of a cooling effect. Neat oils vary from the technically simple to some highly sophisticated formulations.
One drawback of cutting oils that contain active sulphur additives is that they can discolour yellow metals.
Normally, this type of product provides excellent corrosion protection.
Lubricating additives
There are two main types of additives: anti-wear (or ‘polar’) additives, and extreme pressure (or EP) additives.
Anti-wear (polar) additives
- Fatty acid
- Ester
- Polyglycol
Extreme pressure/high-temperature (EP) additives
- Phosphate
- Chlorine (not as widely used nowadays for environmental reasons)
- Sulphur
Anti-wear additives
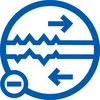
When component surfaces come into light contact with each other (mixed lubrication), the wear can be limited using surfactant additives. These additives form a membrane on the surfaces that slide against one another. A typical product that has an anti-wear additive is hydraulic oil.
The process
- In mixed and boundary lubrication, the metal surfaces rub against each other.
The result
- Wear, leading to a shorter life span.
The additive’s function
- Forms a protective coating on the metal surfaces, thus reducing wear.
Extreme pressure (EP) additives
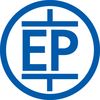
When component surfaces come into frequent contact with each other under heavy loads (boundary lubrication), heat is generated.
Extreme pressure additives, which have the ability to form chemical compounds in the contact surface at high temperatures, can be used to reduce harmful wear. Cutting oils for tougher machining in steel, aluminium and titanium almost always have some kind of EP additive.
The process
- The metal surfaces rub heavily against each other under heavy loads.
- The kinetic energy is converted into a dramatic rise in temperature in the contact points.
- The metals are welded together and the material gradually comes loose.
The result
- A shortened tool life and more rejected machined parts.
The additive’s function
- As the temperature rises in the contact between die and work piece, the additive is activated and provides a protective chemical film that prevents welding.
Learn more about cutting fluids
Downloads
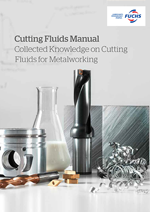
Handbook
Collected Knowledge on Cutting Fluids for Metalworking
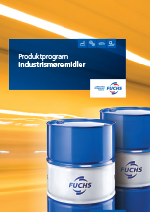
Product program
Our complete product program for industrial applications (in Norwegian).