Advanced technological requirements govern the oil’s formulation
Lubricant production and science go hand in hand. Through various basic components and advanced blends, products with unique properties are created, for instance when it comes to lubricating at different temperatures. At the same time, modern oils are often closely integrated with the engineering they lubricate.
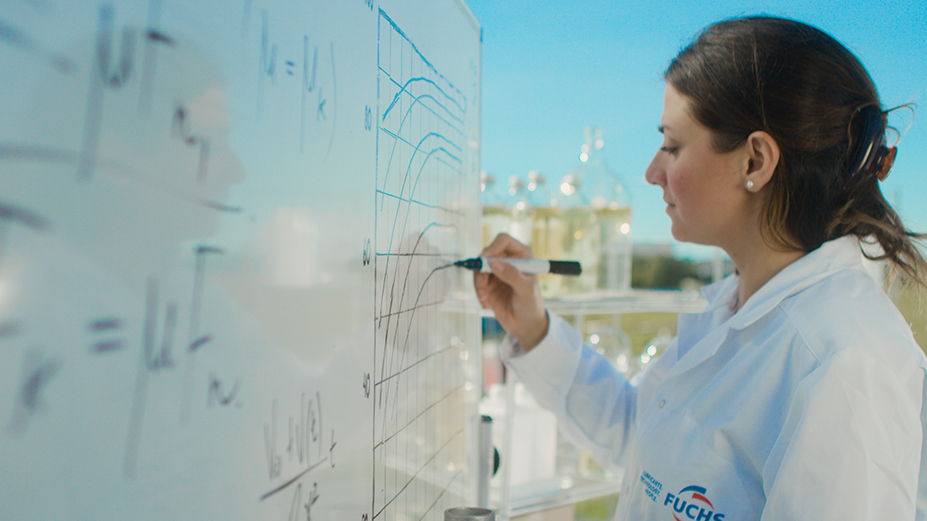
The field of science in question is called tribology, and is the study of lubrication, abrasion and friction. We produce the right lubricating oil for the right technology and as needs vary so much, there is a wide range of products: everything from engine, hydraulic and turbine oils to special products for wind power, forestry and agriculture, metalworking and the manufacturing industry. All with their own more or less unique blend.
THE BLEND IS CRUCIAL
At our lubricant production plant in Västerhaninge outside Stockholm, we work with around 750 products, and oils for vehicles and industry are the two largest areas. The work essentially revolves around the art of blending lubricating oils. All the raw materials are delivered ready to use to the plant, where they are blended to create the right oil.
Whatever application the oil will be used in, there are several common denominators for almost all lubricants, namely that the oil should cool, seal, keep clean and protect against rust. Another important aspect is how the friction is affected. The aim in an engine oil is usually to achieve low friction with adequate lubrication. This affects the blend that gives the oil its specific properties. Technology requirements have also become more advanced over the years and determine how an oil must be formulated to do its job.
TOUGHER REQUIREMENTS
A good example is the automotive industry, where emission requirements have increased dramatically. And when the conditions for vehicle manufacturers and their technologies change, the lubricating oils have to be adapted accordingly. Apart from lower emissions, the requirements also concern lower fuel consumption and longer replacement intervals, so the oil has to be able to function for longer than before.
Lubricating oils have always been important, but they have become even more important as demands on vehicle and machine manufacturers have increased. You could say that the oil has become an increasingly integrated part of the various applications that need lubricating. Developments are going the same way in industry too. As tools and machines become more advanced, the oil specifications have to be increasingly specialised.
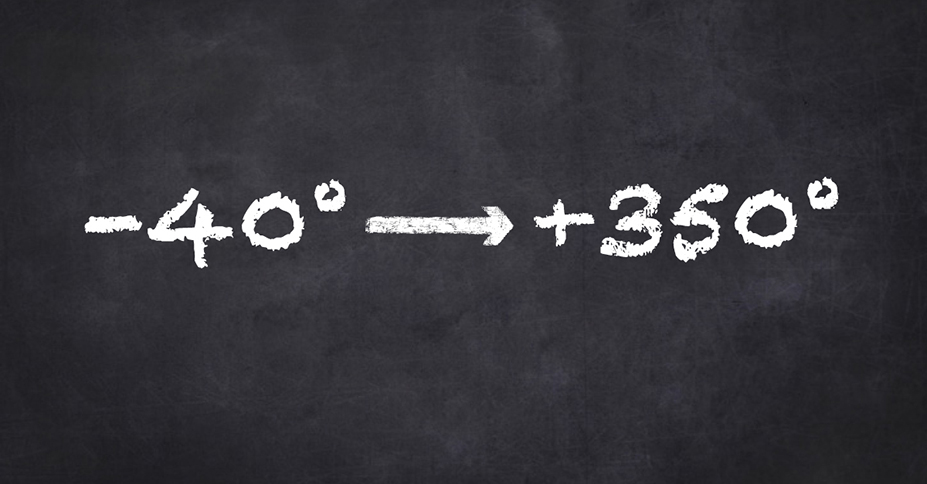
THREE MAIN COMPONENTS
Most lubricating oils are based on a few fundamental components. The first is the base oil, which comprises 60–90% of a typical lubricating oil. There are several classes of base oil, both mineral and synthetic oils, and the product achieves its basic performance properties via the right mix. The base oil affects the end product’s volatility and stability, but also its minimum flow properties, internal friction and how well it protects against corrosion. Synthetic base oil affords us broader options, and enables us to customise the product in more ways.
The next ingredient is the viscosity modifier. This influences the oil’s thickness and is designed to reduce its change in viscosity, even if the temperatures vary. And they do vary, a lot. Some engine oils need to withstand temperatures of between -40 and +350 degrees Celsius, while still retaining their lubricating properties.
And last but not least, various additives are blended into the oil. This is when it gains its final properties. The additives function as cleaners, contain antioxidants that affect service life and enable the oil to cope with friction and counteract abrasion more efficiently. In engine oils, the cleaning properties are particularly important. For industrial oils, it is particularly important for the additives to extend the service life of the oil and prevent seizure under high load.
THE RIGHT QUANTITY IN THE RIGHT ORDER
Most of the ingredients mixed into a lubricating oil are liquid. The volume of a blend tends to vary between 1 and 40 cubic metres, and the blending process itself takes between 12 and 48 hours.
For each lubricating oil, there is a recipe which specifies quantities, the order in which the ingredients are added, how long it should take and how high the temperature must be. A lubricating oil may contain anything from 2 to 22 ingredients. The blending order is important to avoid negative chemical reactions between ingredients. Certain additives must be added when the temperature is high, and others when it is lower.
FINAL QUALITY CONTROL
When the blend is ready, the oil is drained off and packed. The packaging may be anything from 1-litre bottles to 1,000-litre containers. Really large volumes of lubricating oil are delivered by tanker directly to a customer’s facility.
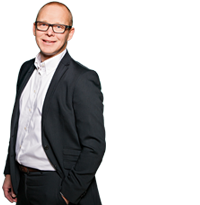
Before draining off and delivering an oil, we always take samples of every product to guarantee that the quality is right. The samples are tested according to various parameters and then stored in our archive for at least one year. Quality control is therefore the endpoint in an advanced blending process for a vast number of more or less customised lubricating oils.
Morten Herregården
This might also interest you
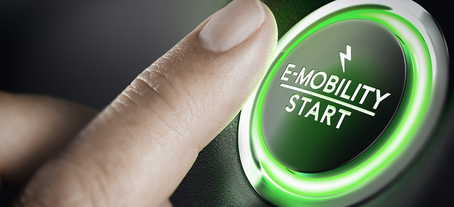
Electric cars – new technology calls for new lubrication
The market for electric cars is setting new records. It is redrawing the map in the automotive industry, but also affecting lubricant manufacturers and other suppliers to the industry. Read more about a changing industry, where technical solutions and attitudes towards mobility are currently being challenged.
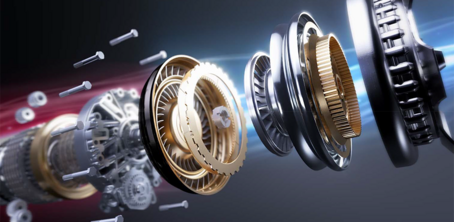
Why specially adapted ATF oils are important
Increasing demands on ever better fuel economy and lower greenhouse gas emissions are calling for more and more complex vehicle constructions. For automatic transmission vehicles, technical developments mean it’s more important than ever to choose the right ATF oil, to ensure the transmission works optimally its entire life.
All blog posts
Subscribe
Only available in Norwegian.
Smart Lubrication
Smart Lubrication is a blog from FUCHS where we share our common knowledge about lubricants and lubrication.