5S – a system for securing lubrication maintenance
Securing lubrication maintenance is a key component of Preventive Maintenance (PM). It also reduces the risk of operational disruptions and unplanned stoppages. And when people, machines and production resources work together optimally, quality and productivity increase.
A shortcut to good order
One shortcut to good lubrication maintenance is the 5S method originally developed by Toyota.
- 5S is based on five phases, all of which focus on ensuring good order in the workplace: Sort, Set in Order, Shine, Standardize and Sustain.
- 5S raises lubrication to new levels and ensures a working PM system. .
- 5S can be used as a practical checklist focusing on everyday maintenance issues, where your lubricant supplier can also provide support and make sure that the proper procedures are in place.
1. SORT – provides clarity and frees up space
A workplace usually has many different lubricants. Conduct a full review and get rid of any unnecessary ones. Ask your lubricant supplier for help. Sorting provides clarity and frees up space. This makes handling easier, saves time, and reduces the risk of mistakes and incorrect mixtures. There’s also money to be saved. An uncontrolled range of products is more expensive to administer, stock and handle generally.
Sort by…
- getting rid of products that are no longer used
- getting rid of products in the existing range that do roughly the same thing
- getting rid of lubrication equipment that is damaged or not up to scratch for some other reason
2. SET IN ORDER – the right thing in the right place
Focus on good order. Anything that’s necessary should be easily accessible and have a set place. The right thing in the right place makes handling cleaner and more reliable. It also makes sure that maintenance is not person-dependent, since it makes it easy for everyone to do the right thing. Cleaner handling of lubricants keeps dirt and wear particles away from the machinery. It reduces the risk of operational disruptions.
Set in Order by…
- having a dedicated lubricant store
- labelling equipment and products so that everyone knows what’s what
- giving each type of grease its own sprayer and each oil its own can
- making sure that oil refill containers are sealed to keep dust and dirt out
3. SHINE – nice and clean
No maintenance work can succeed without cleaning. Keeping a nice, clean workplace increases well-being and ensures a safer working environment. Also, a clean, tidy store contains no contaminated lubricants, which can increase wear and lead to machine disruptions.
Shine by…
- preventing spillage using absorption materials and oil collectors
- cleaning around lubrication points and in the oil store
- cleaning and tidying a little every day, and doing a main clean once a week
- setting a standard and making sure it’s on the checklist
4. STANDARDIZE – supporting procedures
Standardize procedures and decide where, when and how things should be done. Also ask your lubricant supplier for help in producing well-documented supporting procedures. This makes sure that nothing is forgotten, and that important tasks are carried out correctly. It also establishes a historical record of what has been done. This makes life easier in the event of sudden problems, but also in work on continuous improvements.
Standardize by…
- making a to-do list for support and continuity, e.g. in oil changes, analyses, machine care and cleaning
- having control procedures to assure work on labelling, cleaning and good order
- including the measures in lists/standards in maintenance systems or in Excel so they are easy to find, follow and update
5. SUSTAIN – follow up and improve
Last but not least, it is important to sustain work on Sort, Set in Order, Shine and Standardize to make sure it is up to scratch. Follow-up is important since it also lays the foundation for new, gradual improvements to 5S work.
Sustain by…
- drawing up checklists for all 5S work, ensuring that good order is maintained and can be gradually improved
- carrying out regular audits/inspection patrols, and recording them with text and images
- making sure that the follow-up results are concrete and discussed with everyone who works with lubrication maintenance
- motivating those who work with 5S, and emphasising that each individual is vital in assuring a good end result
- highlighting the benefits, and the fact that systematic maintenance leads to a cleaner, safer, more efficient workplace
For further information about 5S and Preventive Maintenance, please contact us.
All tips and advice
Need help?
If you have any questions or need help in any way, please feel free to contact us.
More tips from our blog
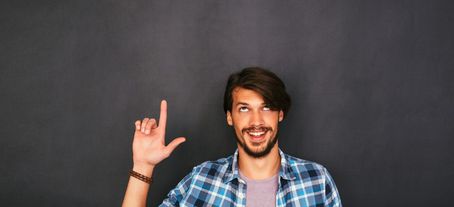
»Did you know…? Tips for smarter lubrication«
More efficient, simpler, cheaper, or just better generally. In this blog we offer some useful tips on technology, lubrication procedures and products. We call it ‘Did you know…?’, and one thing all the tips have in common is that they pave the way for smarter lubrication.
»Four rules of thumb in lubrication – your shortcut to savings!«
Every little helps, as they say. And this is certainly true of maintenance costs. Because making many minor improvements in your lubrication maintenance adds up to major savings. These minor measures may be many, but that doesn’t mean they’re complicated. I like to sum it up into four rules of thumb, which makes it all a whole lot easier.