Connectors – Small but crucial components
You can find them everywhere. Connectors conduct electricity to your cordless drill, they transfer the signal that activates your car’s ABS system, and they’re even what make the servers work at data centres. Connectors are small components, but they play a key part in guaranteeing that electrical products and electronic systems work properly.
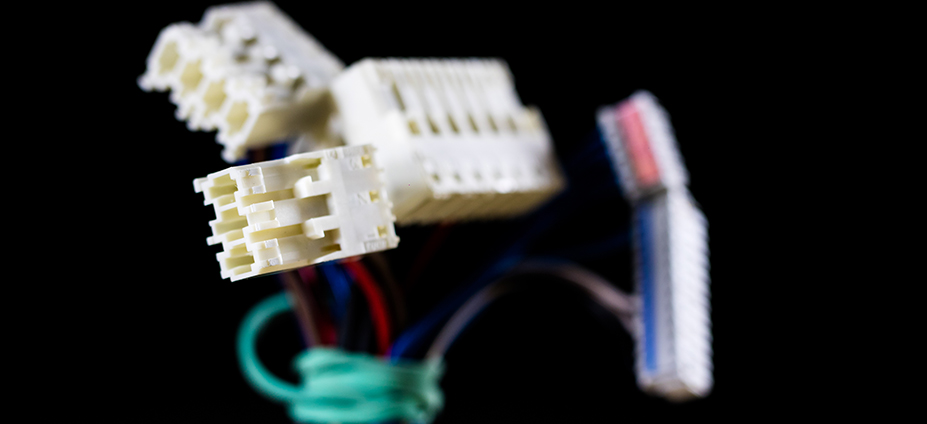
In an average car there are more than 700 connectors, dealing with thousands of individual electrical connections. Connectors have long served an important purpose by securing a reliable power supply to the different parts of a car such as the engine, headlights, brake lights, indicators, windscreen wipers and sound system. But with every new connector that’s needed in a vehicle, comes a potential new risk of malfunction. When it comes to driverless cars and electric vehicles (EVs), the consequences of these malfunctions can be far worse than the stereo going quiet. Today, connectors are critical components in transferring all kinds of electronic signals for computer control of safety functions, functions that have to work without interruption. This includes detecting pedestrians, warning when the vehicle is veering out of its lane, automatic emergency braking, identifying blind spots, and a wide array of other examples. EVs also need connectors for high voltage to transmit power between the battery and the electric motor.
Connectors must be reliable
Conventional mechanical and hydraulic systems are already being replaced by electronic control systems such as brake-by-wire and steer-by-wire. OEMs in the automotive industry must build up trust and keep consumers on board as the technology develops. When it comes to driverless vehicles, safety is of the utmost importance to motorists – and a key aspect of safety is making sure the connectors work reliably.
Any kind of fault in a connector can lead to anything from irritation and higher warranty costs to critical safety issues. Factors that can lead to connector malfunction are vibrations, water penetration, friction, corrosion and oxidation, and high insertion force. Thankfully, these very problems can be prevented using special lubricants for connectors.
Contact with the future
With FUCHS’ acquisition of Nye Lubricants in 2020, we now have a comprehensive range of lubricants specially designed for connectors. We also focus heavily on research in the field, as requirements from the industry are constantly changing. Connectors for EVs require lubricants with a different composition. Temperatures in electric vehicles are higher, the vehicles are used longer and they have more insertion points. Also, as automation systems in the industry evolve and become increasingly ‘smart’, more sensors and connectors are needed to ensure a seamless transfer of information. In developing lubricants for next generation technology, we must always consider all these trends in advance.
The functionality of Nye connector lubricants is backed by data collected in the ADVT (Application, Development, and Validation Test) laboratory, to ensure the devices are reliable and perform at the highest level. All the data is available to customers.
We have also developed test methods and testing equipment to measure parameters such as fretting wear, water resistance and dielectric performance. Validation tests are also conducted to make sure the products meet all the requirements for customer applications.
This might also interest you
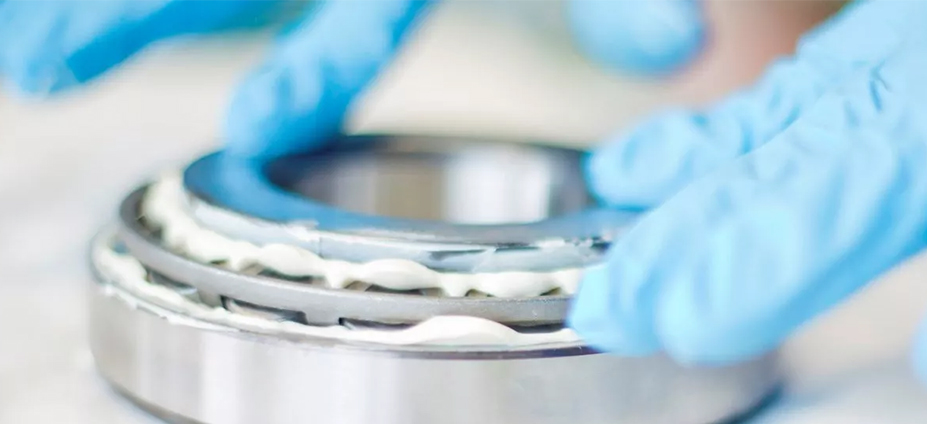
Special application lubricants
As an experienced manufacturer of high-performance lubricants, we know that it can feel daunting to find just the right lubricant to deal with extreme conditions, demands and certifications.
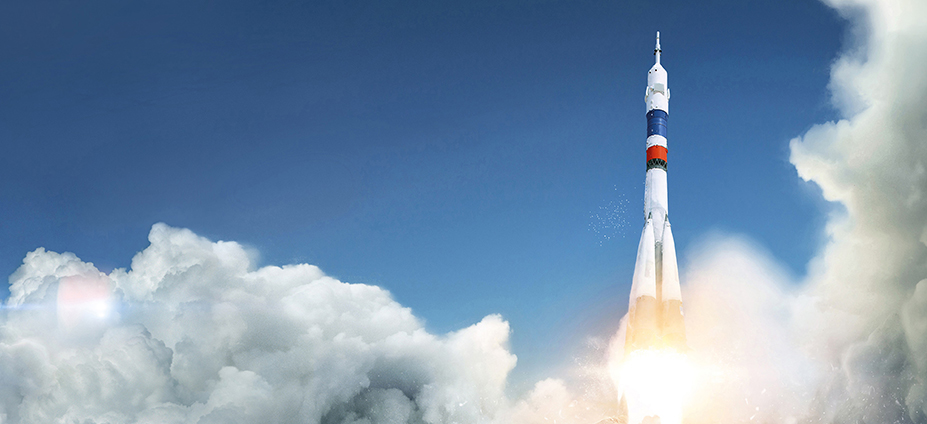
Innovation
For us, it is important to always move forward. The development is fast, and we want to be at the forefront when it comes to lubrication solutions of both today and the future.