PLANTOHYD ES – a new, biodegradable hydraulic fluid for the steel industry (and other hydraulics)
Swedish steel giant SSAB was phasing out coal from its steel operations, and also wanted to change to more environmentally sustainable lubricants – so they contacted FUCHS. The close partnership led to a unique, biodegradable hydraulic fluid for the steel industry and hydraulic systems.
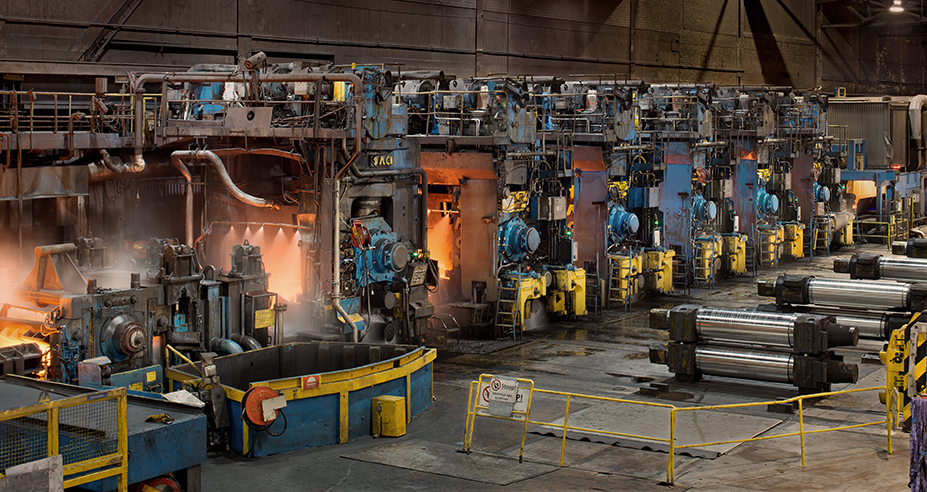
Lars Eriksson of Regional Sales for Industry at FUCHS Lubricants says that in some ways, the collaboration project began ten years ago, when SSAB turned to FUCHS after having problems with valve seizures in its servo systems, caused by varnish. These were huge, complex machines with high-pressure servo hydraulics, and varnish deposits were causing tiny valves to seize up, resulting in very costly downtime.
“We managed to resolve the initial concerns,” says Eriksson, “but the cost was high bearing in mind the size of the systems. Thanks to the fossil-free solution and our excellent collaboration, SSAB wanted to take a closer look at synthetic esters as well.
Goal: steel production with no environmental impact
Steel production is one of the most energy-demanding processes around. SSAB has always scored highly when talking about energy-guzzling industries – and they want to change that. They want to be responsible and are therefore focusing heavily on developing the operation in a more sustainable direction, partly by fuelling coal- and gas-fired blast furnaces with hydrogen instead. Producing steel with no environmental impact is just as much about continued survival and being able to attract the right kind of employees as it is about the benefits of selling ‘green’ steel.
“When SSAB asked us to help them further develop their lubricants, we asked them to write a wish list,” Eriksson explains. “And it turned out to be quite a list. The hydraulic fluid they wanted had to be biodegradable, free of zinc, and have a flashpoint over 220°C. It also had to be oxidation stable, energy saving and counteract varnish.”
There were products that could solve part of the problem but at too high a cost for such large systems, and without the necessary energy efficiency. SSAB were however prepared to accept a higher cost for a renewable, and thus more environmentally sustainable, product than for a mineral-based one – if in return it led to an energy reduction that could compensate for the extra cost within a reasonable time frame.
“I took the wish list to our R&D department and asked what we could do,” remembers Eriksson. “They developed a few product options and cost scenarios, and then we worked with SSAB to choose one of them as a test product. It was 85 per cent based on renewable raw materials, which made it a very interesting option for SSAB.”
But just an ‘eco-friendly’ solution was not enough for the steel company. They also needed to be able to go on managing varnish, for example, and to do everything they could to reduce their energy consumption.
“Before the first lubricant change we made sure to install temperature sensors, linked to a logging function, at various places in the system in order to measure energy consumption. We also performed several power measurements,” says Anders Lindblom, Head of Hydraulics at SSAB in Borlänge. “We then compared readings before and after the oil change, and could clearly see how the temperature and power consumption in the system had been reduced.”
The immediate energy saving was around 14%, and a few minor adjustments boosted it even more, with potential for up to 20%. Before changing lubricants, SSAB had to change servo valves every month due to varnish, leading to high repair costs. But now, almost three years later, they have only had to change the occasional valve.
The perfect cost-efficiency balance
After several years working closely on issues, tests and further development, FUCHS and SSAB have jointly developed a brand new product: PLANTOHYD ES. The key was finding the perfect trade-off between energy efficiency and cost. The solution rarely lies in ‘just’ resolving a problem. It’s also about doing so at a reasonable cost that works for the user in the long run. And the way to achieve this lies in close, honest relations.
“Thanks to FUCHS’ resources, with on-site personnel, keen interest and local R&D, we could continuously test our way to a tailor-made product that works optimally in our particular machines”, says Lindblom. “We are already seeing energy savings and lower CO2 emissions. So far we know that PLANTOHYD ES cleans, is renewable and energy efficient. We’re still testing the life span of the product as we’ve only been running it for just under three years, but the payback time is about two years so it looks quite promising.”
A versatile cutting-edge product for other applications too
What makes PLANTOHYD ES unique is its combination of energy efficiency and a gentle formula with a renewable raw material, and the fact that it dissolves varnish and other deposits in the system so well. It also has excellent adhesion. This means it forms a lubrication film more effectively, thus enabling lower viscosity. Since thinner lubricants use less energy to run the hydraulics, this leads to greater energy efficiency and therefore lower costs.
The high-tech hydraulic fluid PLANTOHYD ES is based on synthetic, biodegradable esters. The energy content of these synthetic esters makes the product oxidation stable with an extremely high flashpoint – in fact the temperature must be approaching 300°C before it burns, which is especially important in a ‘hot’ industry like steel. But thanks to its high viscosity index, PLANTOHYD ES also has excellent properties in low temperatures, making it just as suitable for stationary hydraulics as for mobile hydraulics in sensitive environments. Another positive is that it is miscible with most standard hydraulic fluids.
Although PLANTOHYD ES was developed to meet the specific demands of steel giant SSAB, this is an equally suitable product for other industries with advanced, sensitive hydraulic systems – especially ones that can see the potential of saving energy, want to resolve problems with varnish, and/or want to develop their production in a more sustainable direction – without compromising on function, performance or economy.
All articles
Do you want to know more?
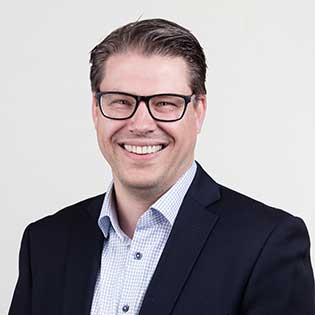
Tore Nilsen
Sales Director Industry
+47 412 33 745
tore.nilsen@fuchs.com
Lars Eriksson
Regional Sales Industry
+46 76 947 80 44
lars.eriksson@fuchs.com