How to choose the right cutting fluid?
One can generally base one’s choice of lubricant on norms, specifications and quality labels from machine manufacturers. However, norms and quality labels very rarely appear on cutting fluids. The choice of cutting fluid depends on the material being machined and the types of machine being used. Most machines work fine with both water-miscible cutting fluids and cutting oils, while others are more adapted to a type of product.
To choose the right cutting fluid, you must consider:
- The types of material being machined
- The type of machining
- The premises, environmental and health & safety aspects
Material
Cast iron and copper alloys are the easiest materials to machine. Cast iron contains graphite and copper which lubricate well by themselves, so very little extra lubrication is needed. Compare this to high alloy steel and aluminium alloys, which are harder to machine and need more advanced high lubricating products.
The material’s effect on the fluid
However, when we look at the material’s effect on the cutting fluid, cast iron and copper alloys form small metal particles during machining which can easily get stuck in nooks and crannies and make the machine dirty. There are therefore higher demands on the fluid’s cleaning properties when machining these materials.
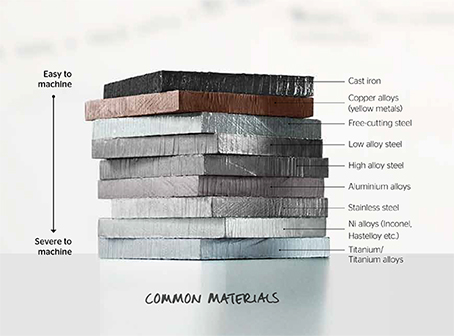
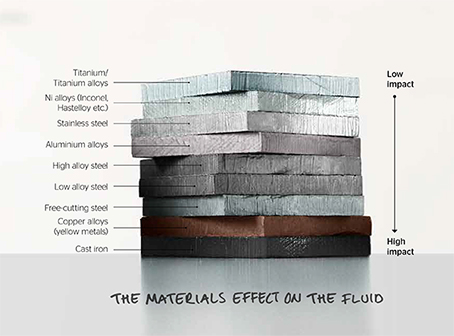
Advantages and drawbacks of different types of cutting fluids
Slow operation = high demands on lubrication = Cutting oil
Fast operation = high demands on cooling = Cutting emulsion
Cutting oil
Demands:
- High demands on lubrication
- High demands on surface finish
- Hard-to-machine materials
- “Maintenance free”
Examples:
- Grinding hard metals
- Deep-hole drilling
- Threading difficult materials
- Gear cutting
- Rotary table machines
Drawbacks:
- Worse cooling
- Mess in and around machines
- Fire risk
Cutting Emulsion – Water-Miscible Cutting Fluid
Demands:
- High demands on cooling
- High cutting speeds
- Most materials can be machined
Examples:
- Turning
- Milling
- Drilling
- Grinding
Drawbacks:
- Requires care/maintenance
- Systems need replacing
- Greater risk of allergies etc.
Properties | Cutting oil | Emulsion | Synthetic |
---|---|---|---|
Lubrication | +++ | ++ | - (++ = polymer) |
Cooling | - | ++ | +++ |
Cleaning | - | ++ | +++ |
Removal of swarf | ++ | ++ | (+) |
Corrosion protection | +++ | ++ | + |
Antibacterial | +++ | + | ++ |
Mould/fungi | +++ | ++ | + |
Comparison between cutting oil, emulsions and synthetics, where + means the product type is better suited to that particular property.
- Cutting oils provide the best lubrication and rust protection.
- Emulsions provide better lubrication and rust protection than synthetics.
- Synthetics have the best cooling and cleaning properties.
Optimisation of cutting fluids when circumstances change
It’s not always easy to find an optimum cutting fluid that works perfectly in several different types of operation and with widely varying materials. To make life easier for our customers, at FUCHS we have produced different additives to change the properties of our cutting fluids and adapt them to the customer’s specific production. One example is our lubricating additives, which increase the lubrication of the products should the customer change to a new material that is harder to machine. When the system is topped up with a lubricating additive, it becomes a more lubricating product without having to stop the machine and halt production.
Learn more about cutting fluids
Downloads
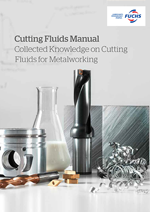
Handbook
Collected Knowledge on Cutting Fluids for Metalworking
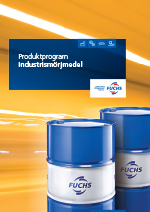
Product program
Our complete product program for industrial applications (in Swedish).