Handling and maintenance of cutting fluids/systems
Clean the cutting oil system regularly
During Christmas or summer stoppages, pump the oil off and remove swarf and any other residues at the bottom of the tank. Clean the conveyor, tank and machine, and then filter the oil back into the system. You generally only need to fill with a small amount of new oil.
Clean the emulsion system with an effective system cleaner
The system cleaner is normally added 1-2 days before the fluid is to be changed. However, you can also use a higher concentration of cleaner over a shorter period of about 6-8 hours, as long as there are no operators working inside the machine. The approach you choose depends on the circumstances in production when the fluid is due for a change.
Next the system is emptied (including swarf and other impurities) and rinsed with water. Use a system cleaner only in conjunction with an emulsion change.
Disposing of used cutting fluid
Use a disposal method that has as low an impact on the environment as possible. Used emulsion can either be evaporated or splitted using acid. The emulsion should be evaporated to approximately 10% before being sent for disposal. When emulsion is splitted using acid, the oil phase is sent for disposal. The water phase is cleaned up and reused, or neutralised and sent to a treatment works if this is approved by the local authorities.
Mixing emulsion
The best results are always achieved using a mixer. To ensure a stable emulsion, concentrate must always be added into the water, rather than the other way around. This ensures the emulsification process is successful and the resulting emulsion is stable. If you add water into the concentrate there is a risk that the emulsion becomes inverted, which means there are water drops in oil rather than oil drops in water, and the emulsion will not work as intended.
Checking cutting fluids and system
Checking the concentration of the emulsion
The concentration of the emulsion must be kept at the right level if the emulsion is to work optimally.
- If the concentration is too high it will produce more mess, increase the risk of skin problems and also increase cutting fluid consumption.
- Too low a concentration can result in bacteria, mould infestations, corrosion, poor lubrication, and a reduced life span on the tools and system.
It is therefore important to regularly measure the concentration, ideally daily but at least once or twice a week.
How to measure the concentration
The concentration is measured either using a refractometer, which is easiest, or by titration.
Refractometer:
Reset the refractometer before use, with the same water used to dilute the cutting fluid.
The reading on the refractometer needs to be multiplied by a factor (Refractometer Index) which applies to the water-miscible cutting fluid being used. The factor is given in the product data sheet or a label on the packaging.
The refractometer measures the total oil content of the fluid, i.e. the reading on the refractometer will also include any oil that has leaked into the system. If it is hard to read the refractometer reading, this indicates that a fair amount of oil has leaked into the system.
Titration:
Unlike the refractometer, titration does not measure the oil content, but components in the cutting fluid. A fair amount of equipment is required, such as a burette, a conical flask, a weak hydrochloric acid solution (0.5 M HCl) and methyl orange as the indicator (alternatively a pH meter).
Concentration = Volume ml hydrochloric acid (HCl) used in titration x Factor for the specific cutting fluid.
Measuring the tramp oil:
The tramp oil content can be measured as follows:
Concentration (refractometer) – Concentration (titration) = Tramp oil content
Tramp oil is most easily removed using a skimmer or an oil separator.
Adjust the concentration as required after measurement. A weaker concentration of approximately 1–2% should normally be used for topping up the system.
Check the pH value
It’s important to keep an eye on the pH value in the system. If the pH decreases, you either have too low a concentration or a bacterial problem. In most cutting fluids, the pH should be at least 9.0. pH can either be checked using a pH meter or a pH stick.
pH-scale
Most cutting fluids have a pH of 9–9.6 but there are also products that have a lower pH during use.
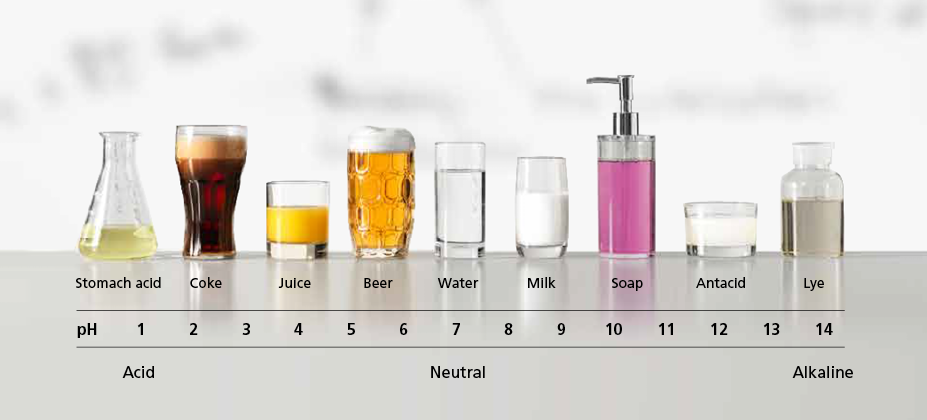
Measure the bacteria content in the emulsion
The problem with bacteria is that they eat the cutting fluid’s components and secrete acidic substances, which leads to a drop in pH and then to corrosion problems and bad odours. Bacteria breed quickly if they are able to infect the system, so it is important to measure the bacteria levels regularly, especially when the pH value decreases.
Bacteria is most easily measured using a dip slide. Bear in mind the results could take up to two days for bacteria, and up to four days for mould.
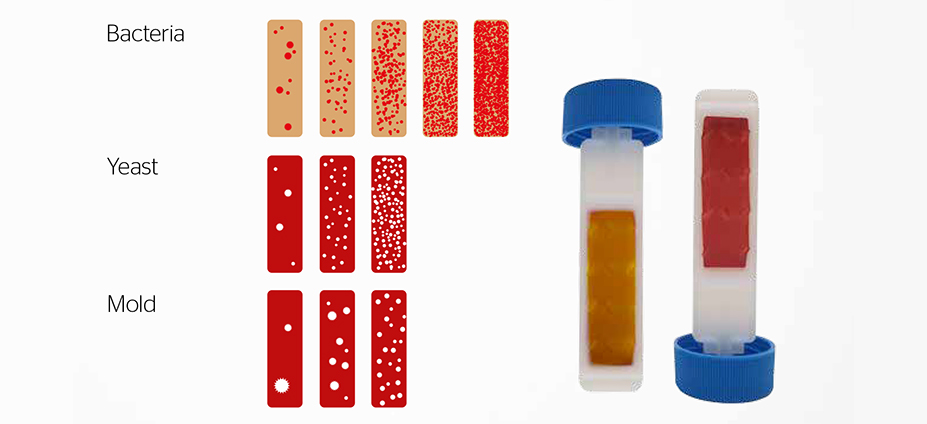
Contact us or follow the standard maintenance procedure if the pH falls below the recommended value, or if the bacteria content cannot be kept below 106 per ml.
Support products
Support products are used to maintain the performance of the cutting fluids and to rectify various kinds of problems.
System cleaners
A system cleaner is a water-soluble cleaner and dispersant for emulsions and solutions. System cleaners are only used in connection with a change of emulsion, rather than for regular emulsion maintenance. System cleaners kill bacterial and mould growth, and also loosen microbiological slime and sludge.
Biocides
Biocides can be used if severe problems with uncontrolled bacterial and mould growth appears.
Anti-foaming agents (antifoams)
Metalworking fluids do not normally produce any problems with foam. If foam does form, it is either due to a mechanical problem (e.g. the pump is sucking in air), or because the metalworking fluid has been contaminated with another liquid. Causes of foam problems could be soft water, too high an emulsion pressure, incorrect nozzles or system tanks that are too small.
Anti-foaming agents can be added to the cutting fluid in small amounts as a temporary measure, but it is important to identify and remedy the underlying cause of the foam. Otherwise the problem will soon reoccur.
pH-adjusters
Used to raise the pH of an emulsion. The pH should always be checked in connection with a production stoppage.
Page contents
Handling and maintenance of cutting fluids/systems
- Clean the cutting oil system regularly
- Clean the emulsion system with an effective system cleaner
- Disposing of used cutting fluid
- Mixing emulsion
Learn more about cutting fluids
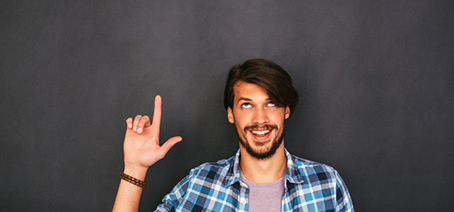
Tips and advice
Get more information in our blog post "Tips for more efficient handling of cutting fluids" and in the short article "Care for your cutting fluid before longer breaks".
Downloads
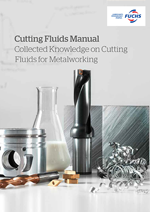
Handbook
Collected Knowledge on Cutting Fluids for Metalworking
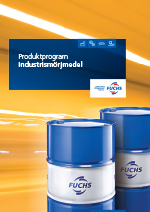
Product program
Our complete product program for industrial applications (in Swedish).