Consider the whole process – from ingredient to packing
It is no great surprise that lubricants for use in food production come with extremely high safety requirements; consumer safety is, after all, paramount. Other sectors such as pharmaceuticals and cosmetics also place particular demands on special lubricants. In all cases it is vital to consider the whole process, from ingredient to final packing.
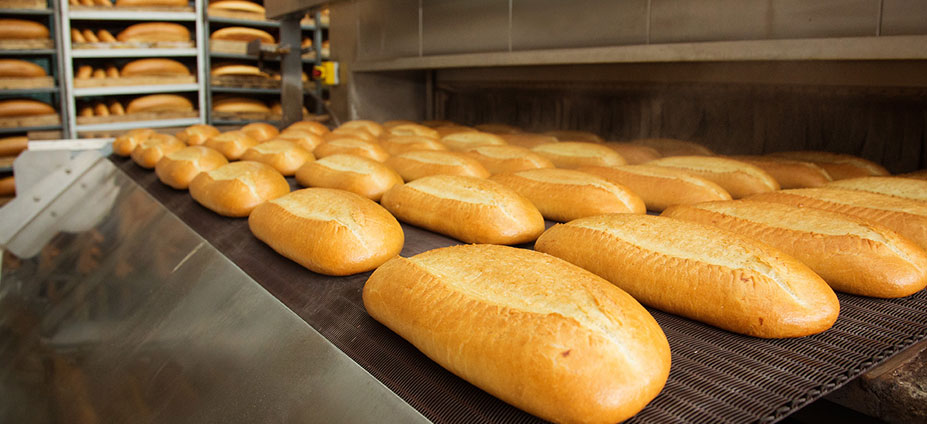
Industries that produce and handle products which people come into close contact with in various ways are subject to some very strict requirements, such as cleanliness. In food production, for instance, a safe production process is absolutely vital, from manufacturing and processing to bottling and packing. In broad terms, the more sensitive and demanding the process, the more important it is to use a suitable lubricant. Hazardous contaminants simply must not occur. And this is true whether production and handling relate to beverages, bread, dairy products, plants, meat, fish, poultry, animal feed… In fact anything that we as humans choose to eat ourselves or feed our pets and livestock.
DID YOU KNOW THAT OIL CAN BE PULLED ALONG WITH THE COMPRESSED AIR?
If your process requires special lubricants, such as ones approved for use with food, it is tremendously important also to understand the value of using these safe lubricants throughout the process. Since oil is virtually impossible to filter off completely, a little oil will always be pulled along in the compressed air from oil-lubricated compressors, for example. While the amounts in question are extremely small, this does make it vital to use food-grade lubricants also in compressors. Otherwise there is a risk that the compressed air (used e.g. for cleaning, crumb clearing, bag inflation or anything else) contaminates the results of all the previous clean parts in the process.
Similarly, also consider the environment around the compressor, as it is here that the machine sucks in all the air. Any spores, bacteria and so on that the compressor takes in will accompany the compressed air on its way out.
FOR US, IT’S ABOUT MORE THAN SAFETY
So, there’s a lot to consider when it comes to food production. And of course the lubricants not only need to meet high safety standards, they also have to deliver the best technical performance. And as if that wasn’t enough – did you know for example that when we develop products for the brewing industry, we conduct tests on how lubricants affect the head on a glass of beer? See our short film.
Read more about our special application lubricants here. If you need any help, please don’t hesitate to contact us.

This might also interest you

Rationalise your compressed air processes and reap the benefits
Do you use compressed air anywhere in your business? If you work in industry, the answer is most probably yes. Around 70% of industrial companies in Europe use compressed air in some part of their operation. That’s so much, that roughly 10% of all industrial electricity is used just to generate compressed air. In Europe alone. But this is a figure that can be reduced…
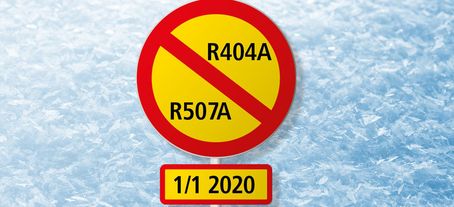
Better cooling with lower environmental impact
Gone are the days when we had to salt our food or cover it with ice blocks to make it keep longer. Nowadays, we take it for granted that we can keep food cold in the fridge at home or in the supermarket, and keep ourselves cool on hot days at work or in the car. However, these cooling systems have also come at a price, in the shape of environmental impact.
All blog posts
Subscribe
Available in Swedish only.
Smart Lubrication
Smart Lubrication is a blog from FUCHS where we share our common knowledge about lubricants and lubrication.