How about a health check?
Bearing in mind that most lubricant-related machine breakdowns are due to contaminated oil and poor filtering, it’s surprising that more people don’t check the oil in their systems – since the majority of these breakdowns could be avoided with regular oil analyses.
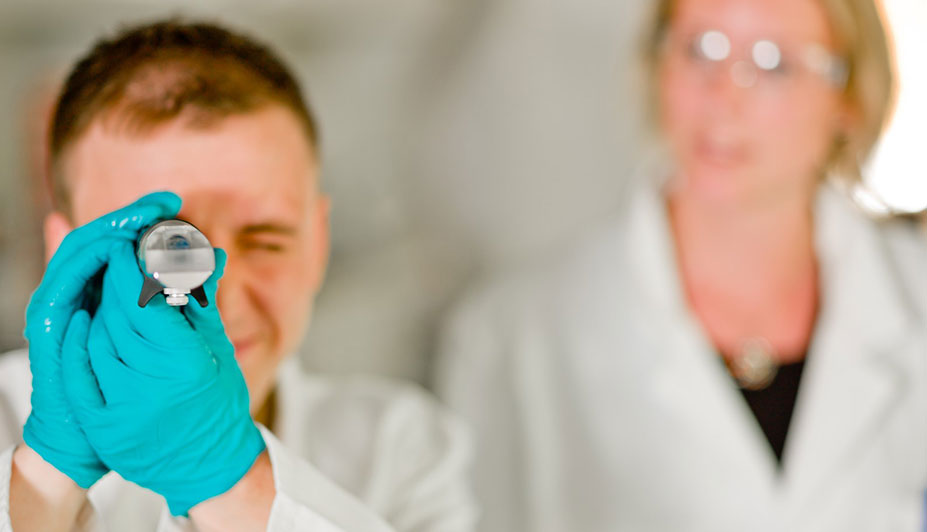
As humans we can only benefit from a health check every now and again, and the same is true of the machines, motors and engines we rely on. It is increasingly common today to check the oil and system status using oil analyses, but I also know that many companies don’t, and they would benefit greatly from analysing the oil in their systems.
WHAT DO YOU HAVE TO GAIN FROM OIL ANALYSES?
Keeping an eye on the state of your oil can be very profitable, partly because you can better plan maintenance and optimise the oil change interval, thus increasing operational reliability. This in turn can save a lot of money.
An oil analysis can provide invaluable information about the state of a machine, motor or engine. It not only reveals the condition of the oil and verifies that the filters are working properly; it can also indicate if there is any serious wear, what kind of wear it is, and where in the machine it is happening. Oil analyses can even provide an early warning in case there are contaminants in the oil that could cause problems in the future (such as wear, corrosion or jammed valves). Quite simply, an oil analysis leads to a more reliable, more predictable lubrication system.
THE IMPORTANCE OF CONTINUITY
Without a historical record it is very hard, and sometimes impossible, to know what has changed in a system compared to earlier when everything was running smoothly. And without such knowledge, you are essentially fumbling in the dark. So if oil analysis is important (also for us, who work with oil and help people sort out their problems), continuity is absolutely crucial.
While I do realise that an oil analysis might seem expensive, I also know that the costs could be significantly more if something goes wrong in the system. So my advice to you who ‘only’ want to know how your oil is doing, is to conduct an oil analysis at least once, and ideally twice, a year. If you want to know how your machine is doing, then do an analysis at least twice, and ideally four times, a year. A lot of companies neglect to address these issues, even though the machinery we’re talking about is incredibly expensive.
SMALLER SYSTEMS
If your systems are not large enough to make regular oil analyses financially viable, then at least regularly check the oil’s status yourself by looking and smelling – and of course checking all the filters. If you have large systems with many small components, such as individual gears for instance, you can reduce the number of analyses by selecting one unit to analyse regularly. This will give you a general idea of an appropriate drain and change interval for all the units in the system.
TO BEAR IN MIND WHEN SAMPLING
Something that is just as important as continuously analysing the oil, is to be consistent in the sampling procedure. Is the oil level normal? Has the oil circulated properly? Is the temperature normal for the system? If you take your samples from different places or at different times, you will get different results. And since the advantage of regular oil analyses is to be able to make comparisons over time, you must always follow exactly the same procedure. You should also be aware that it’s extremely easy to contaminate the sample during the sample-taking process.
- Take your oil sample from the same place and in the same way every time. The oil sample should be representative of the system, ideally taken from the pressure side of a main pipe.
- The oil sample should be at normal operating temperature (if possible).
- The oil level in the system should be normal.
- The sampling point must be clean. You can clear the end of the tap outlet by first emptying and discarding a small amount of oil.
- If you must use a suction pump – suck from the middle, never the bottom of the oil mass.
- Firstly, fill the sampling bottle with oil, and then empty it. Then fill it again and seal it, before sending it off for analysis.
INTERESTED IN FINDING OUT MORE ABOUT OIL ANALYSES?
Please contact us if you would like to know more about what oil analyses could mean for your process, assistance deciding which units are worth analysing, or to request an oil analysis.
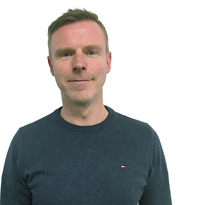
This might also interest you
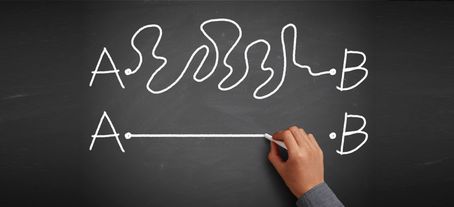
Four rules of thumb in lubrication – your shortcut to savings!
Every little helps, as they say. And this is certainly true of maintenance costs. Because making many minor improvements in your lubrication maintenance adds up to major savings. These minor measures may be many, but that doesn’t mean they’re complicated. I like to sum it up into four rules of thumb, which makes it all a whole lot easier.
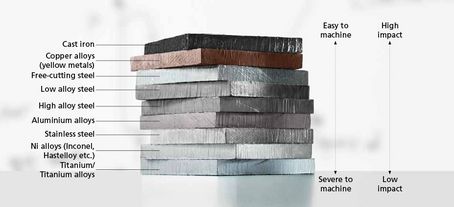
Tips for more efficient handling of cutting fluids
There are many benefits to be gained from streamlining the handling of cutting fluids, everything from fewer unplanned stoppages to a longer service life for tools and machines. Follow these tips and you’ll considerably increase your chances of keeping production at a consistent high level.
All blog posts
Subscribe
Available in Swedish only.
Smart Lubrication
Smart Lubrication is a blog from FUCHS where we share our common knowledge about lubricants and lubrication.