Semiconductor Greases and Oils
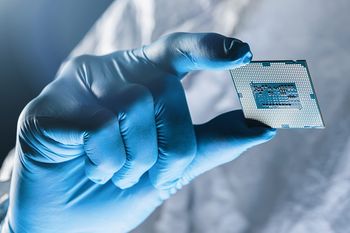
The semiconductor industry is booming. The increased demand for semiconductor products such as microprocessors, memory chips and flat panel displays has been driven by the emergence of next-generation technologies including 5G, Internet of Things (IoT), artificial intelligence (AI), electrified vehicles, connected medical devices, industrial robots, and many more. These technically sophisticated applications often call for faster processing speeds and lower power consumption, requiring more complex fabrication processes. Fabrication precision is now down to sub 10-nanometer level for many processes, meaning even the smallest contaminants can result in product defects and yield loss. These systems must operate reliably to meet demands.
Lubricants are required to ensure the functionality of fabrication and processing equipment, but the wrong lubricant may result in unscheduled down time and contamination. Maintenance and downtime are expensive. Lubricants protect against friction and wear to extend component life and ensure that the systems operate reliably. Lubricant outgassing and particle generation can contaminate fab equipment and products, negatively impacting product quality and yields. To avoid these issues, it is critical to select high performance specialty greases with low outgassing and low particle generation properties.
Semiconductor manufacturing and processing equipment often operate at high temperatures and under vacuum, thus requiring high performance lubricants that will protect their linear guides and slides, bearings, ball and lead screws, and seals against wear.
Advantages of Semiconductor Greases and Oils
NyeTorr®, NyeClean® and NyeVac® are specialty lubricants formulated specifically for Semiconductor fabrication and processing equipment. These low outgassing semiconductor lubricants are chemically stable even when exposed to process gasses, making them the first choice of leading Semicon equipment OEMs and fabricators.
Features & Benefits:
- Reduce friction & wear
- Extend component life
- Prevent contamination
- Withstand vacuum conditions
- Improve functionality & reliability
- Improve line yields
- Avoid latent defects
- Increase uptime
What Characteristics Should Be Considered When Selecting a Semicon Lubricant?
When a lubricant outgasses it releases condensable material that can contaminate wafers, processing equipment, and other sensitive components. Lubricant outgassing is measured in total mass loss (TML) and collected volatile condensable materials (CVCM) per ASTM E595. Nye’s lubricants fall well below the acceptable outgassing limits determined by the semiconductor industry, 1% or less for TML and 0.10% or less for CVCM. Nye can collect these condensable materials and conduct Residual Gas Analysis (RGA) to identify the materials shed from the lubricant into a system.
The term dynamic particle generation describes what happens when contaminants are created by being forced or expelled from a lubricated ball-screw, bearing, or gear system into the operating environment. These contaminants could include base oil constituents, thickener particles, additives, etc. and are freed from the grease through dynamic mechanical action whether it be rolling, sliding, or a combination of both. Engineers in Nye’s Application Development and Validation Test Lab developed a proprietary test method and apparatus that measures and quantifies particle generation under these dynamic conditions. Results from this test provide valuable data that can be used to inform the development of specialty lubricants with low particle generation.
A lubricant must be able to protect the mechanical components of fab equipment at high temperatures without evaporating. Outgassing is more likely to happen at high temperatures as vapor pressure increases. Many of Nye’s in-vacuum and cleanroom lubricants are formulated to perform at temperatures up to 250 °C.
Manufacturing equipment in vacuum and cleanroom environments are highly sensitive, where even microscopic particulates can cause product failure. The best way to ensure lubricant cleanliness is through ultrafiltration to eliminate microscopic particulates in a lubricant. Nye can ultrafilter grease and oil to eliminate possible contaminants for semiconductor applications.
All Nye products for the Semiconductor Industry use PTFE with levels of PFOA less than 0.1% by weight, in compliance with REACH guidelines and other international regulations. Although this work is not a measurement of each product's complete formulation, analysis indicates PTFE would be the most significant contributor to PFOA levels.
PFPE vs MAC lubricants
Both PFPE and MAC lubricants are recommended for vacuum environments because of their low vapor pressure, and low outgassing. PFPE lubricants offer better high temperature performance (up to 250° C) when compared to MAC lubricants (up to 150° C). Because of their unique additive packages, MAC lubricants provide better protection against wear when compared to PFPE lubricants. Both chemistries can be ultrafiltered, are compatible with plastics and elastomers, and comply with PFOA regulations.
NyeTorr vs NyeClean
NyeTorr® and NyeClean® products are chemically stable, non-toxic, low-vapor-pressure, synthetic lubricants for semiconductor components like bearings, linear guides, ball screws, and other sensitive mechanisms. NyeTorr® products are recommended for use in ultra-high vacuum applications exposed to high temperatures. NyeClean® products have good low particle generating properties and are recommended for cleanroom applications like back-end packaging where little or no vacuum is present.
Product | Kinematic Viscosity @ 40°C | Vacuum Stability (ASTM E595) | Features |
NYECLEAN 5057 | 192 cSt | TML= 0.225 wt% CVCM= 0.054 wt% | Suggested alternative for discontinued legacy PFPE semiconductor greases. |
NYECLEAN 5097R | 140 cSt | TML= 0.441 wt% CVCM= 0.044 | Provides superior corrosion resistance and wear performance up to 180° C in environments where outgassing is not a concern. |
NYETORR 5300 | 140 cSt | TML= 0.320 wt% CVCM= 0.045 wt% | Industry standard PFPE vacuum grease. |
NYETORR 5300XP | 140 cSt | TML= 0.075 wt% CVCM= 0.018 wt% | Offers improved wear performance in high load applications. |
NYETORR 5350 | 152 cSt | TML=0.757 wt% CVCM=0.451 wt% | Suitable for low to moderate vacuum conditions with improved load and wear performance. |
NYETORR 6300 | 188 cSt | TML= 0.036 wt% CVCM= 0.006 wt% | Significantly lower outgassing rates. |
NYETORR 6300S | 188 cSt | TML= 0.012 wt% CVCM= 0.000 wt% | A soft grease used in applications that require lower viscous drag and torque resistance. |
NYETORR 6350EL | 200 cSt | TML = 0.060 wt% CVCM = 0.008 wt% | Offers Lube-For-Life performance in applications that require low outgassing and low torque. |
NYETORR 6370EL | 362 cSt | TML= 0.063 wt% CVCM= 0.001 wt% | Offers the longest life of any PFPE lubricant while providing superior corrosion and wear resistance. |
Product | Kinematic Viscosity @ 40°C | Vacuum Stability (ASTM E595) | Features |
NYETORR 5200 | 108 cSt | TML= 0.068 wt% CVCM= 0.007 wt% | Superior torque and anti-wear performance to extend component life. |
NYETORR 6200 | 108 cSt | TML= 0.058 wt% CVCM= 0.025 wt% | Superior outgassing and anti-wear performance. |
NYETORR 6200-FL | 108 cSt | TML=0.03 wt% CVCM=0.007 wt% | Excellent torque performance in low-speed dithering operations. |
Product | Kinematic Viscosity @ 40°C | Vacuum Stability (ASTM E595) | Features |
NYETORR 5301 | 140 cSt | TML= 0.230 wt% CVCM= 0.033 wt% | Base oil used in NyeTorr® 5300. |
NYETORR 6301 | 187 cSt | TML= 0.00 wt% CVCM= 0.000 wt% | Base oil used in NyeTorr® 6300. |
NYETORR 5361 | 192 cSt | TML= 0.03 wt% CVCM= 0.010 | Base oil used in NyeClean® 5057. |
NYETORR 6371 | 446 cSt | TML= 0.020 wt% CVCM= 0.002 wt% | Base oil used in NyeTorr® 6370EL. |
NYETORR 5381 | 809 cSt | TML= 0.070 wt% CVCM= 0.004 wt% | Used as a grease replacement for static seals where a degree of damping is needed. |
Product | Kinematic Viscosity @ 40°C | Vacuum Stability (ASTM E595) | Features |
NYETORR 5201 | 108 cSt | TML= 0.120 wt% CVCM= 0.013 wt% | Base oil used in NyeTorr® 5200. |
NYETORR 6201 | 108 cSt | TML= 0.110 wt% CVCM= 0.010 wt% | Base oil used in NyeTorr® 6200. |
SYNTHETIC OIL 3001A | 2082 cSt | TTML=0.100 wt% CVCM= 0.050wt% | An ultra-filtered oil for loaded applications requiring excellent film strength. |
Product | Kinematic Viscosity @ 40°C | Vacuum Stability (ASTM E595) | Features |
NYEVAC 9720 | 61 cSt | TML= 0.359 wt% CVCM= 0.023 wt% | Ester oil used in turbomolecular pumps. |
NYEVAC 9721 | 61 cSt | TML= 0.942 wt% CVCM= 0.467 wt% | An ester grease thickened with lithium soap for turbomolecular vacuum pump systems. |
NYEVAC 9724 | 61 cSt | TML= 0.279 wt% CVCM= 0.073 wt% | A very soft ester grease thickened with PTFE for turbomolecular vacuum pump systems. |
Testing & Manufacturing
The materials and manufacturing methods used to prepare a lubricant can impact lubricant cleanliness. At Nye, the raw materials are required to meet stringent quality standards. The in-vacuum lubricants are manufactured and packaged in ISO Class 8 and Class 7 certified clean rooms to ensure the products are suitable for your manufacturing environment.
All of Nye’s products can also be tested under vacuum and high temperatures in our Vacuum Aerospace Semiconductor Test (VAST) Laboratory. Tests performed under these simulated operating conditions provide the customers with accurate outgassing, particle generation, and other important performance data that help them select the right lubricant for their precision fab equipment and high-end manufacturing processes. Nye’s unique materials, such as Pennzane, and manufacturing methods, such as Ultrafiltration, have been proven to withstand the harshest conditions, on earth and in space, for nearly 50 years.
CONTACT US.
Click to book an appointment with Tina using the link above or alternativley send an email our team to enquire about our product ranges and services.
> Email: contact-uk@fuchs.com
WHO IS NYE?
NYE LUBRICANTS joined the FUCHS Group in 2020 and complements the portfolio with synthetic lubricants for special applications and markets.