UK Production
Our Stoke-on-Trent manufacturing plant has the capability to produce 90,000mt of lubricants annually, making FUCHS the largest lubricant manufacturer in the United Kingdom.
FUCHS UK is one of the most agile locations within the FUCHS Global Group thanks to our extensive production capabilities. Utilising many of our storage options and filling lines we are able to effectively meet market product demands with both bulk and small batch output options.
Our production site features the following manufacturing plants:
- Mineral oils
- Soluble oils
- Wire rope & glass lubricants
- Rust prevention lubricants
- Petroleum jelly
Discover more about the comprehensive range of lubricants FUCHS UK manufactures our Product Program page.
Our certified UK production facility boasts 291 storage vessels:
- 80 raw material vessels: 15-300mt
- 51 blending vessels: 1-60mt
- 160 finished material vessels: 3-30mt
Raw Material Warehouse
Our fully automated warehouse holds 3872 pallets to further extend our large raw material on-site holding. A paperless put-away process enhances our move towards sustainable manufacturing.
Finished Goods Warehouse
FUCHS UK has a SAP warehouse control system with 6500 pallet spaces available. On average we pack 995 orders each week.
Automated Filling Lines
Large investments have enabled FUCHS UK to expand our production capabilities to meet increased consumer demand, as well as facilitating our packaging improvements. We are proud of the ability to fill:
- 1L / 4L / 5L plastic bottles
- 20L plastic containers
- 60L / 205L barrels
- 1,000L IBCs
Our commitment to sustainable packaging has seen the installation of dedicated Lube Cube filling lines:
- 4L / 5L / 20L Lube Cubes
Bulk Storage & Distribution
Once blended, our products are transported to the production lines or to holding tanks/vessels for later use. These products are then retrieved for our filling lines or passed directly into bulk tankers for transportation to our customers.
FUCHS UK Certificates & Approvals
The FUCHS UK manufacturing site holds various recognised certifications.
We also pride ourselves on the high quality of our products and services which are shown through our registration with leading industry organisations.
FUCHS GROUP Investment in the UK
The FUCHS GROUP has invested heavily in the UK over recent years, from smart energy-saving lighting and production sensors to large fully automated warehouses.
See below for some of FUCHS UK's key investments:
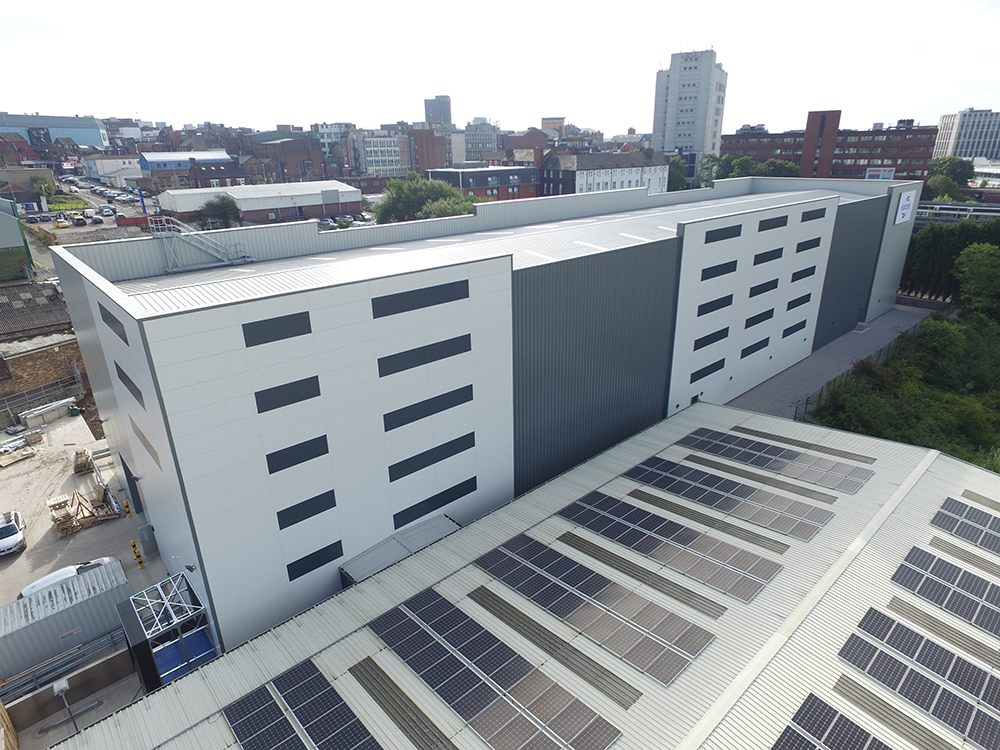
Construction of a £5m raw materials warehouse with 4,000 pallet spaces started in 2019 and opened fully, after delays due to COVID-19, in 2021. The fully automated High Bay warehouse significantly increases the amount of raw materials the business can store on-site. Its construction will also allow an existing building to become a specialist packaging warehouse.
Mark Gray, Head of Operations said:
"We have an ambition to place FUCHS Lubricants at the forefront of R&D, manufacturing and distribution of lubricants in the UK. This raw materials warehouse represents a significant investment for the business, and a further step towards that goal. The warehouse includes sophisticated automation, which will future-proof the business and create cost-saving benefits.”
Two wire guided driverless Very Narrow Aisle trucks operate in the warehouse, benefitting from high travel and lift speeds, without operator intervention. The warehouse has a capacity of approximately 4,000 pallet spaces, with ability for automatic or manual storage place allocation. The high-tech Warehouse Control and Warehouse Management Systems streamline all processes, with benefits including goods receipt entry and booking, a paperless put away process, inventory support and batch traceability.
FUCHS UK has invested in multiple state of the art 4 axis robot arms for assistance with loading pallets directly from the filling lines.
By reducing the amount of required lifting there are obvious manual handling benefits. The Fanuc M410/185iC is capable of lifting 185kg at a reach of 3m (Specifications may differ between different robot arms set throughout the production warehouse).
A single robot arm can simultaneously collect boxes from multiple production lines, loading them neatly onto dedicated pallets for the AGVs to collect. Our range of robot arms operate between single and multiple tracks, collecting boxes of product and barrels.
These quicken palletising whilst keeping efficiency and accuracy at a high, repetitive level.
Safety for our staff is key and therefore all robot arms are surrounded by fencing and light gates to ensure our improved production is kept safe for everyone.
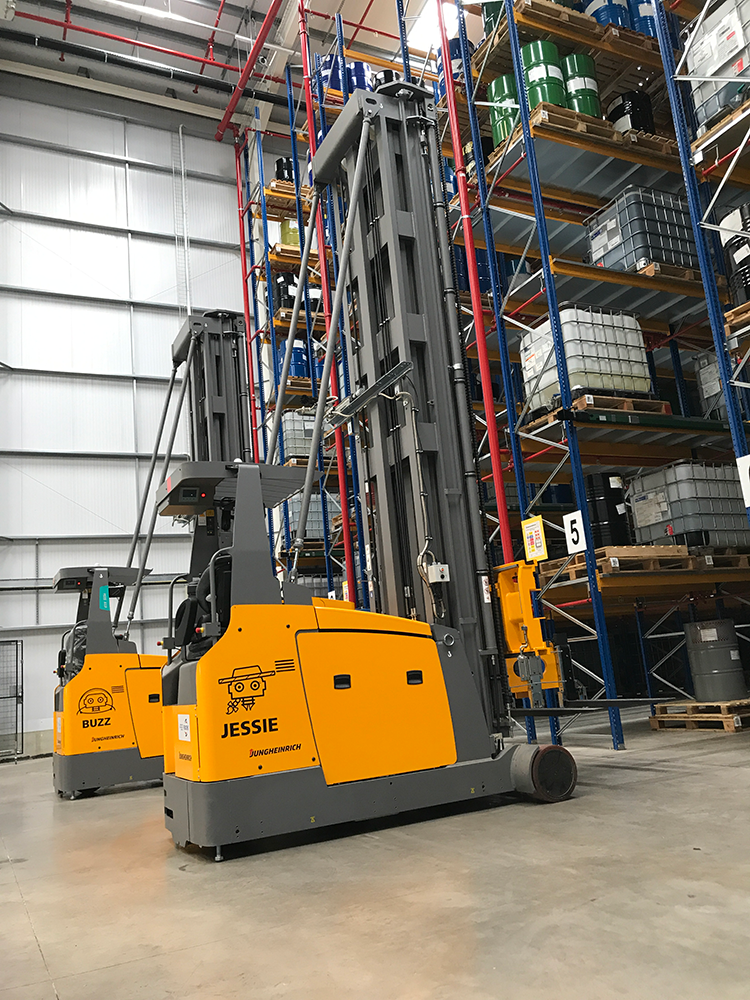
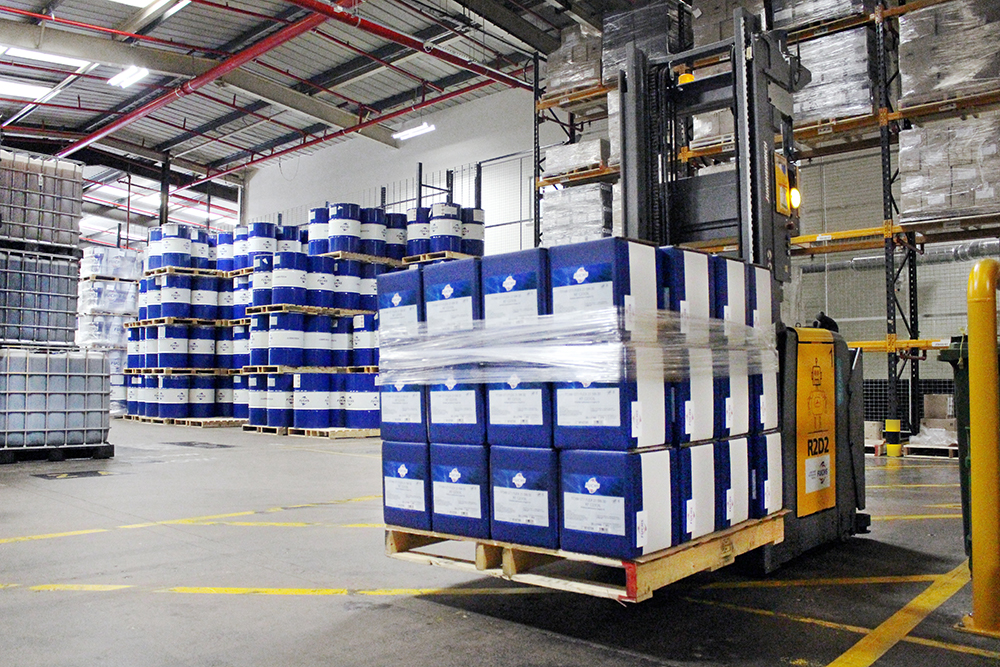
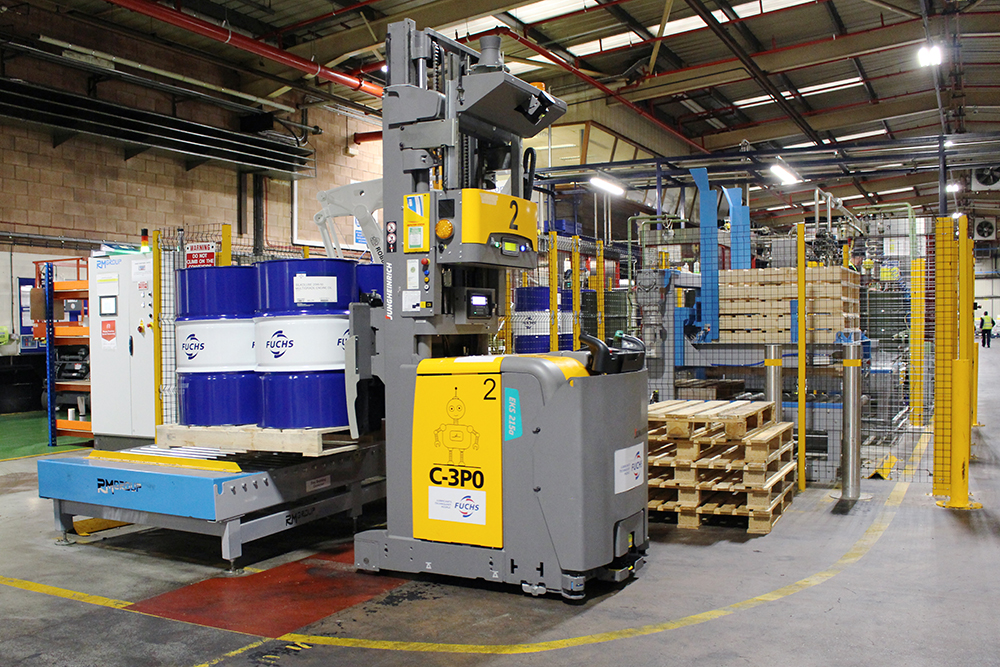
FUCHS UK now operates numerous automatic guided vehicles (AGVs) in both our raw material warehouse and our manufacturing plant.
These vehicles are similar to forklifts however they are driverless and therefore move along pre-programmed routes automatically when triggered i.e. when a raw material is requested or once a pallet has been fully loaded and requires moving into stock.
AVGs are self charging and can operate accuratly 24/7 to remove any unnecessary stockpiling.
Sensors on each vehicle ensure the travelled routes remain safe for workers and visitors to the site - In fact we have seen no AGV related injuries since they were introduced in 2018.
Addressing the route of our products across our manufacturing site, FUCHS UK invested in better links between our various warehouses.
Raw materials arrive on site at our automated Raw Material Warehouse. From here, products are either stored or passed to a conveyor which transports the pallet down to our empty packaging warehouse where they are then transported via another converyor lift to our production warehouse.
This conveyor system moves products from warehouse to warehouse withour the need for moving outdoors (Risking exposure to elements or damage), a factor which controls the high quality of our materials.
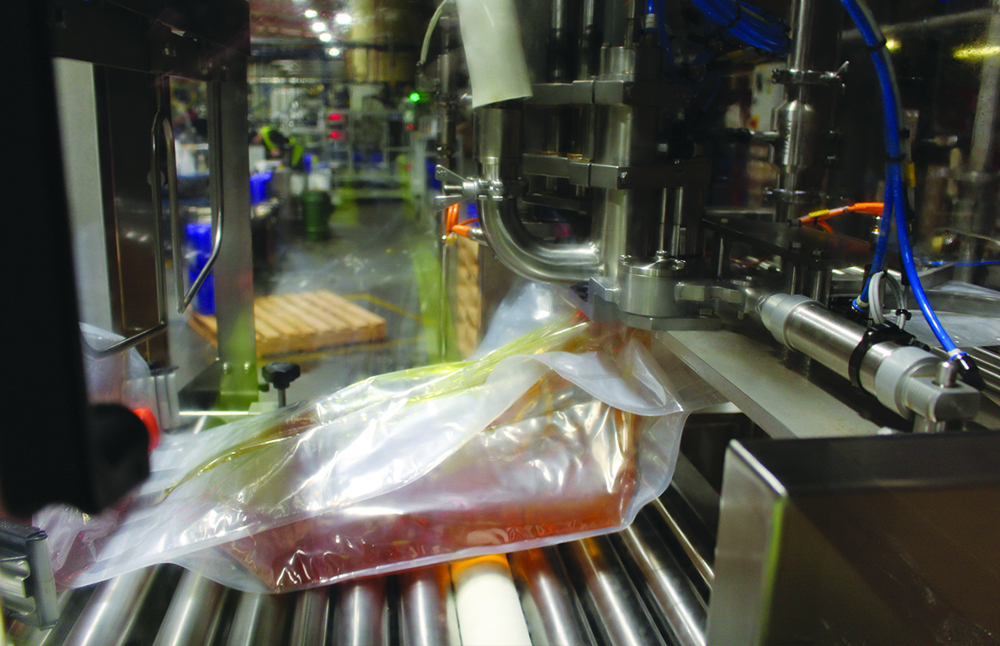
FUCHS UK has invested in multiple automatic Lube Cube filling machines to help with the increasing demand for our environmentally friendly innovative Lube Cube packaging concept.
Capable of filling six 20L Lube Cubes per minute, the machines increase productivity and streamline our filling lines.
The Lube Cube filling machines can be programmed to accommodate our full set of 4L, 5L and 20L cube sizes.
We have added an automatic shrink wrap machine and a palletiser to the end of our dedicated 4L and 5L tracks to finish the automatic manufacturing process, making the whole line fully automatic.
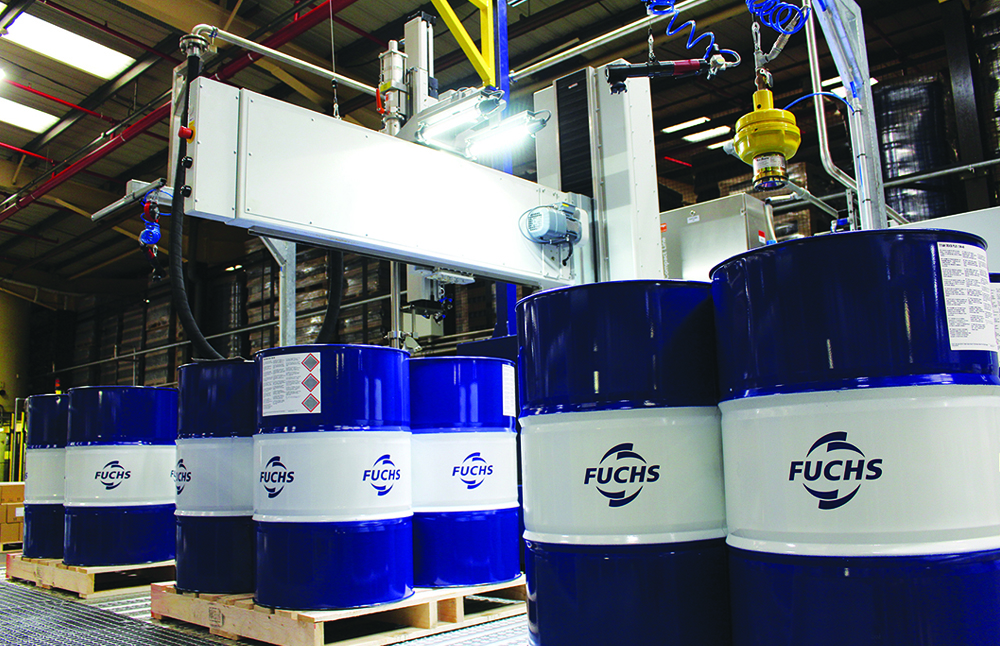
Investment in this new filling machine saves on flushing and manual handling making for a more efficient production.
The Feige filling machine is capable of filling 60L, 205L and IBC pack sizes which would have previously required separate production tracks.
This machine with a.i. determines the pack size to be filled and the automatic spout then fills to a desired weight before passing the pack to the next stage of production.
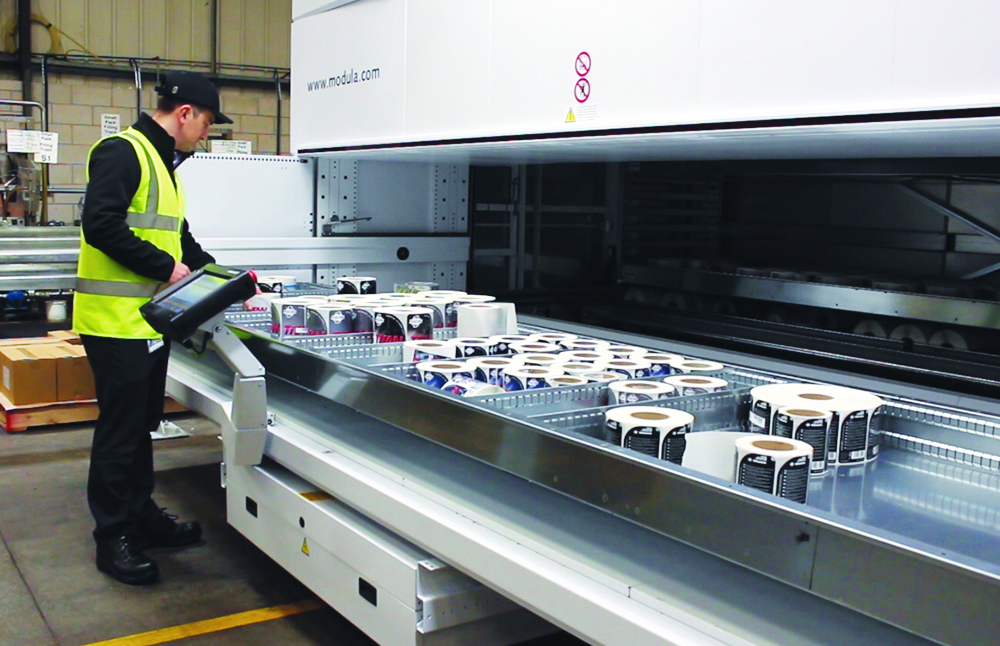
FUCHS UK invested in 2 MODULA storage tray machines. These enable easily organisation of hundreds of individual label reels whilst reducing the floorspace required compared to regular storage racking.
Our MODULA machines now operate a real-time inventory management system, providing essential information to assist with re-ordering.
Operators input their label code into the easy to navigate system and the tray holding the requested label reel will be called down for picking.
Once finished, trays are easily recalled to their storage position within the machine.
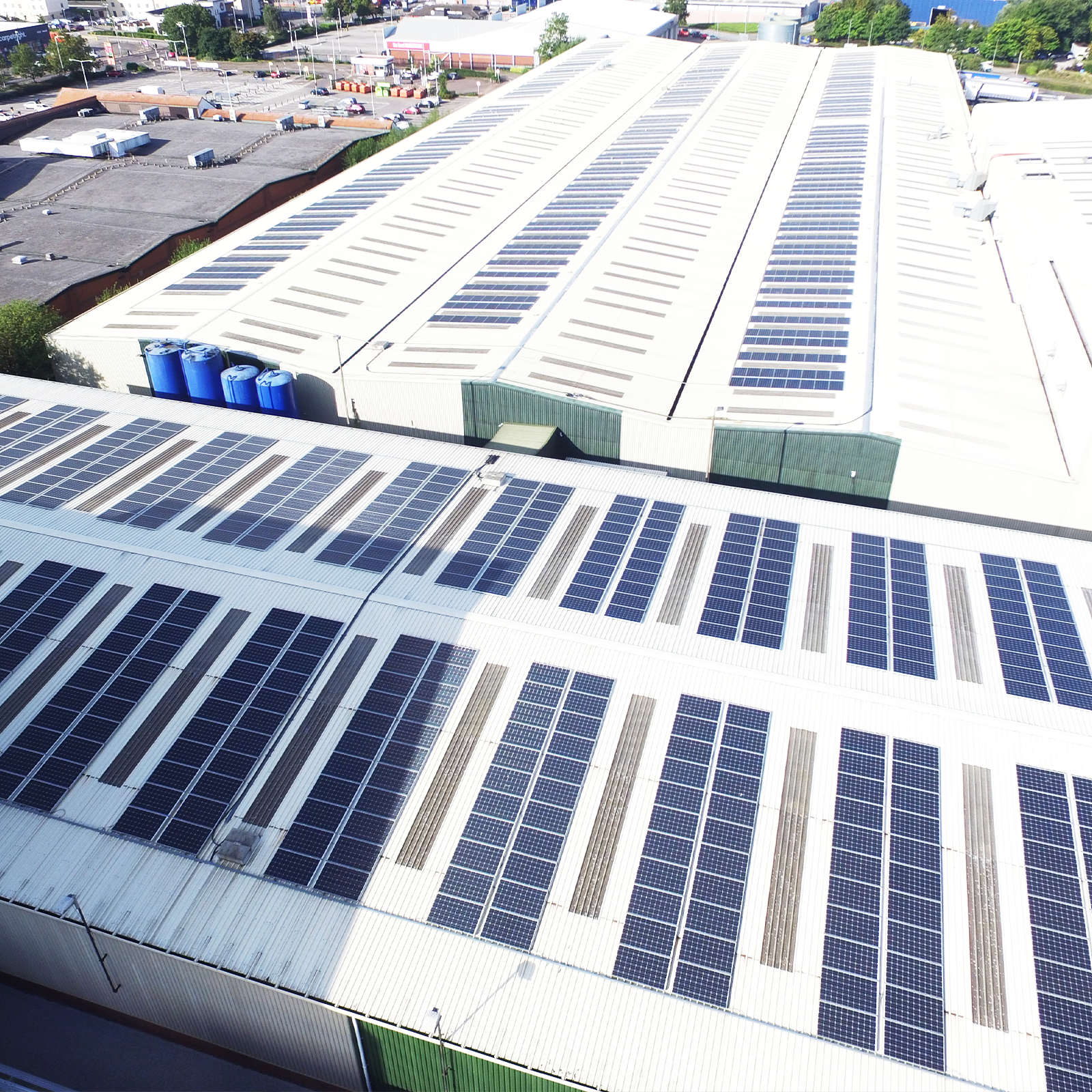
FUCHS UK installed 2,110 solar panels across the whole site which help generate 15% of our annual electricity.
The whole manufacturing plant has been fitted with a sprinkler system suitable for all production areas in order to ensure the safety of our staff, visitors and buildings.
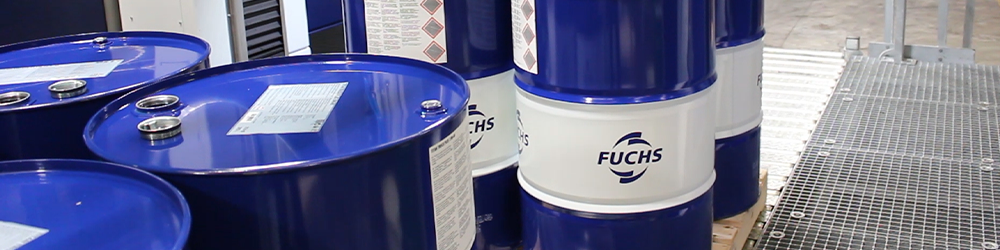
CONTACT US
Do you have specific product or delivery requirements?
Speak to our UK team to discover how our production agility can be a benefit to your business.
Please complete the simple enquiry form below or alternativly email: contact-uk@fuchs.com
Contact Us.
Do you have specific product or delivery requirements?
Speak to our UK team to discover how our production agility can be a benefit to your business.
> Email: contact-uk@fuchs.com
UK Site Images
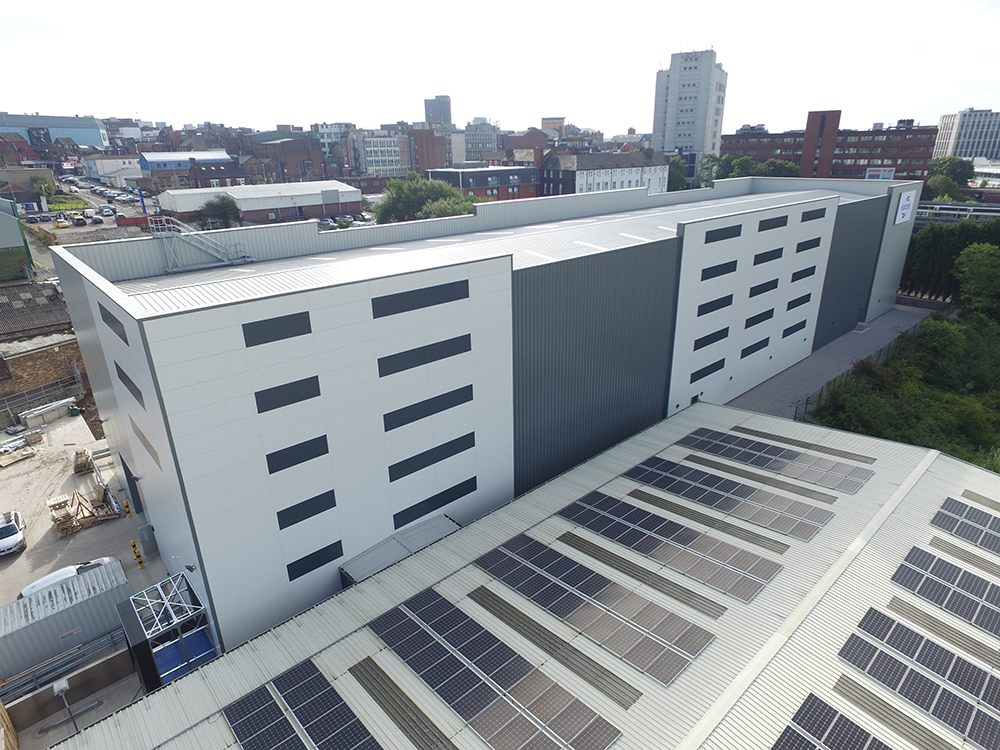
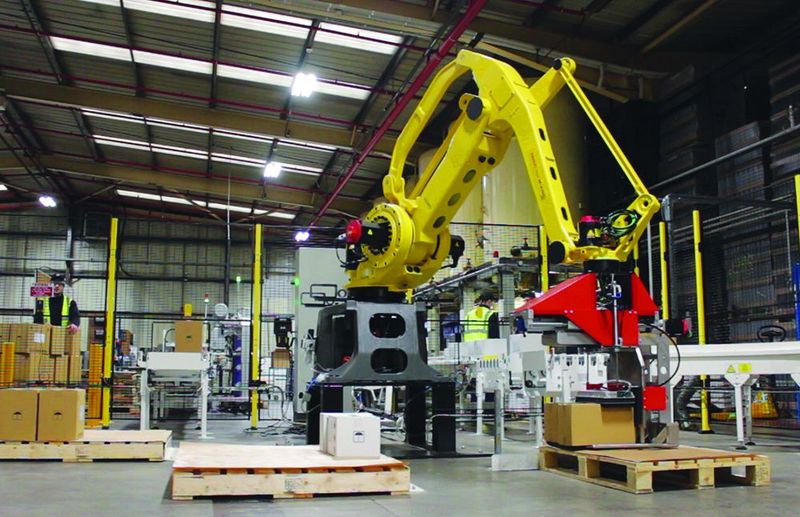
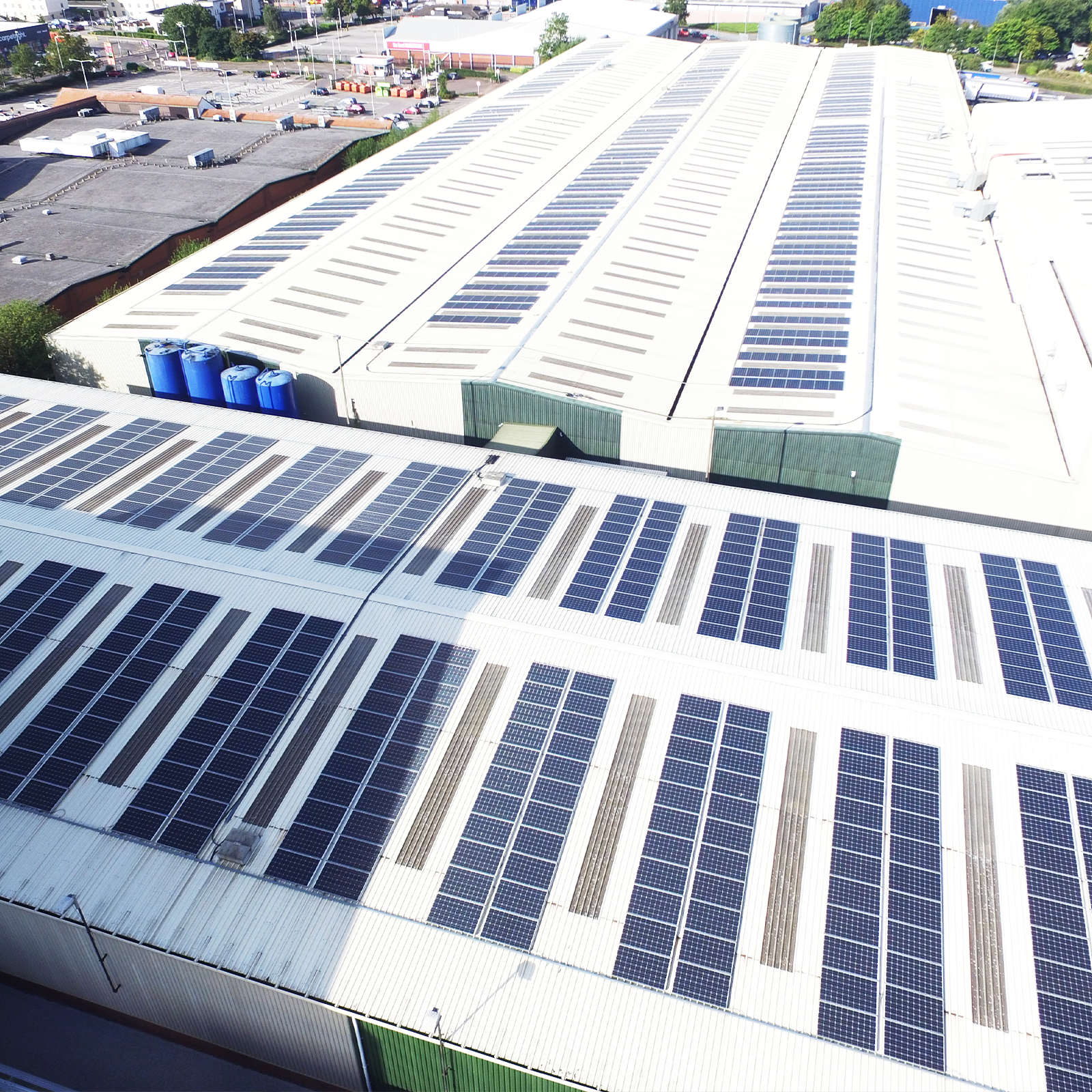
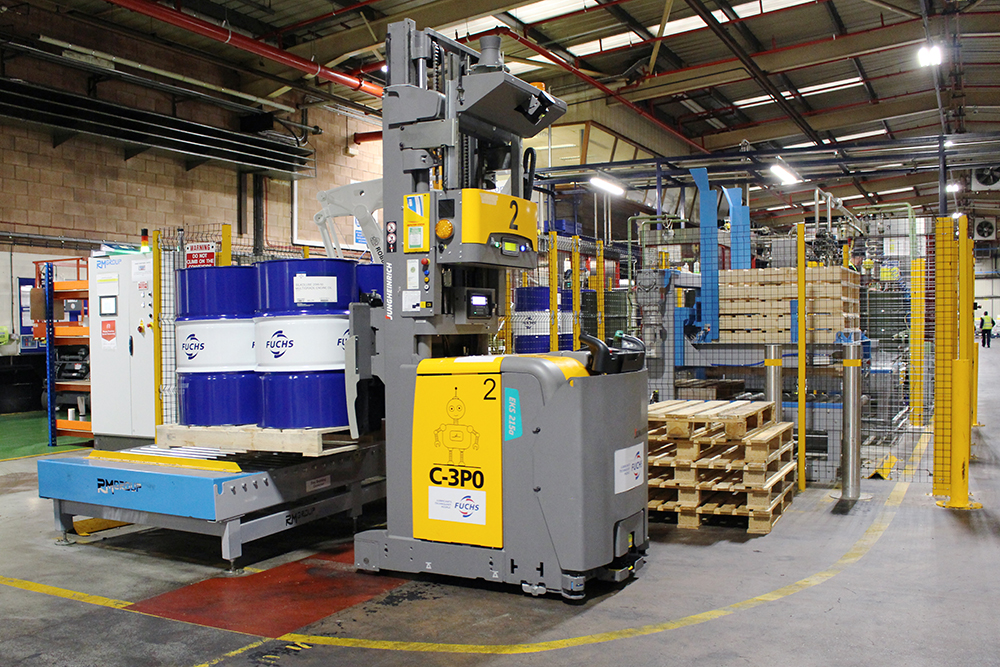
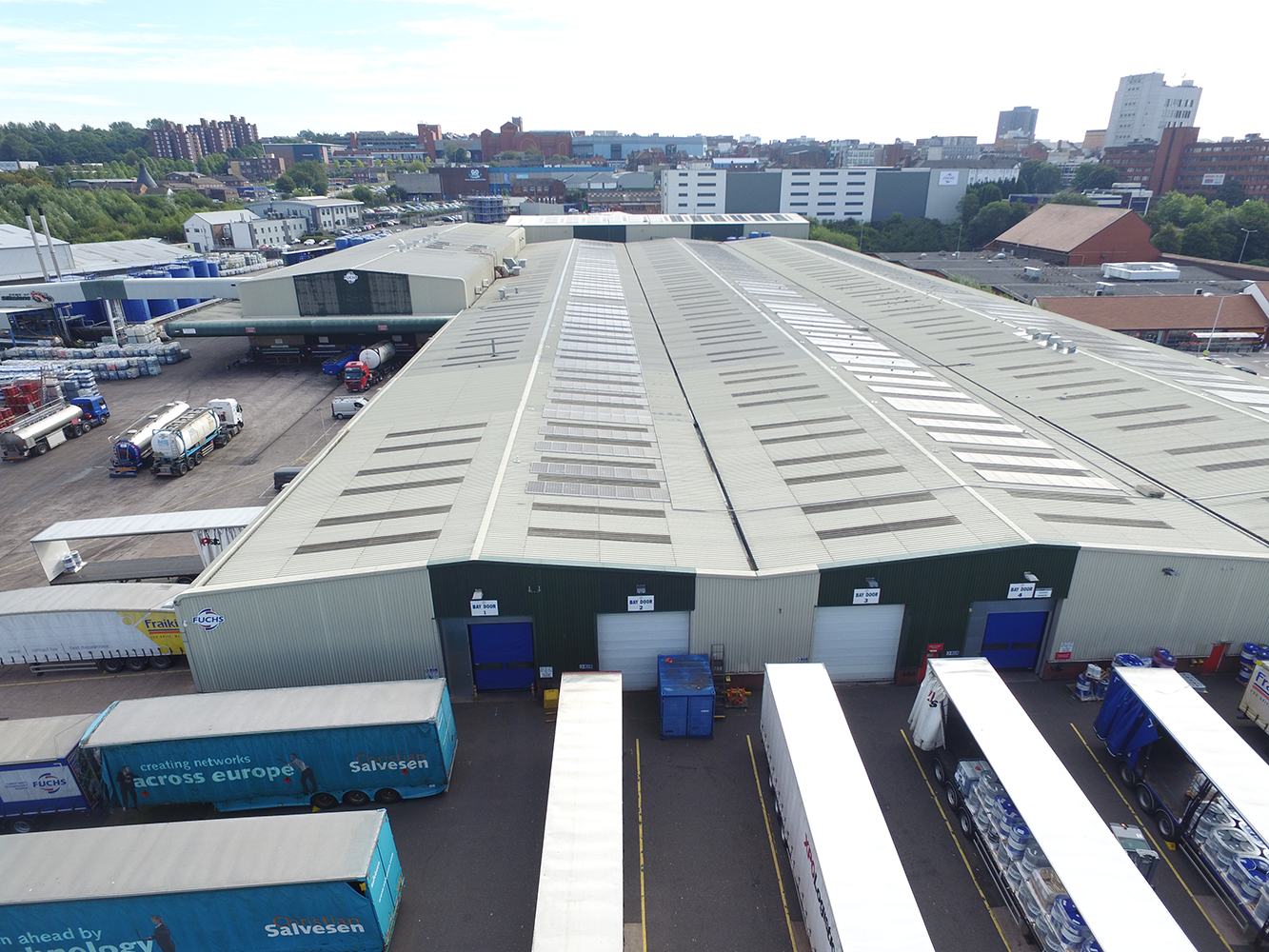