Keep your metalworking fluids in top condition this winter with FUCHS
> Metalworking fluids (MWFs) are essential in machining operations because they provide critical lubrication and cooling, reducing friction and heat during cutting processes. This not only enhances tool life and machining performance but also improves the quality of the finished workpiece by achieving smoother surfaces and preventing corrosion.
Additionally, MWFs help remove metal particles and debris, ensuring machines operate efficiently while minimizing wear on components. However, to reap these benefits, it’s vital to maintain the condition of your MWFs.
Why is it important to look after your metalworking fluids?
Proper maintenance of MWFs is essential to ensure their effectiveness. Regular monitoring and care help in controlling bacterial growth, maintaining optimal lubrication and cooling properties, and extending the fluid's lifespan. Neglecting MWF maintenance can result in health hazards for operators, reduced tool life, compromised workpiece quality, and increased operational costs due to machine downtime and fluid replacement.
Here's some more information on the key reasons to manage your metalworking fluids:
Water-based metalworking fluids (MWFs) are prone to bacterial and fungal growth if not properly maintained. This can pose health risks, such as skin irritation and respiratory problems, while also creating foul odors that contribute to an unpleasant work environment. Consistent maintenance of the fluid is essential to controlling bacteria levels and preventing these issues.
Additionally, operator health can be significantly impacted by exposure to contaminated or degraded MWFs. Skin irritation, dermatitis, and respiratory issues are common risks, but these can be minimized through regular fluid maintenance, ensuring the fluid remains clean and safe for workers.
The lubrication and cooling properties of MWFs are critical for reducing friction and heat during cutting processes. Without proper maintenance, these fluids lose their effectiveness, resulting in increased wear on cutting tools, shorter tool life, and suboptimal machining performance.
Maintaining the fluids enhances cutting efficiency by ensuring smooth operation, preventing binding, and keeping tools at optimal temperatures. This leads to improved cutting performance, greater precision, and extended tool longevity.
MWFs play a vital role in achieving high-quality surface finishes by reducing heat and wear during machining. However, if the fluid becomes contaminated or degrades, it can negatively impact the finished part's quality, causing issues such as surface rust, pitting, or dimensional inaccuracies that may necessitate additional finishing. Clean and well-maintained fluids support consistent machining, minimizing dimensional inaccuracies and scrap rates.
Proper fluid maintenance also prevents corrosion and staining on workpieces, ensuring defect-free results and reducing the need for rework.
Proper maintenance of MWFs prevents the buildup of contaminants such as swarf, bacteria, and other debris, which can clog filters, coolant lines, and even lead to machine failures due to overheating or poor fluid circulation.
Just as MWFs protect workpieces, they also safeguard machine components like pumps, tubing, and tool holders from corrosion and rust. Neglected fluids can accelerate equipment wear, while consistent maintenance minimizes downtime caused by unexpected breakdowns, ultimately supporting reliable production schedules and cost savings.
Regular maintenance of MWFs significantly reduces operational costs. By monitoring concentration, pH levels, and regularly filtering and refreshing the fluid, its lifespan is extended, saving on replacement costs.
Keeping fluids clean also reduces the risk of machine breakdowns, minimizing costly unplanned maintenance and downtime. Proper care prevents the frequent disposal of contaminated fluids, cutting down on disposal costs and contributing to more sustainable practices, which benefit both finances and the environment.
Maintaining MWFs effectively supports environmental sustainability by reducing waste. Regular maintenance extends fluid life and minimizes the need for disposal of contaminated fluids, decreasing the environmental footprint.
Furthermore, efficient fluid use aligns with sustainability initiatives, conserving resources and reducing the overall environmental impact of machining operations. Proper fluid care is not only cost-effective but also essential for fostering greener industrial practices.
What can you do to keep your metalworking fluids in top condition?
By regularly looking after your metalworking fluids, you can enhance machining efficiency, improve product quality, prolong the life of your equipment, protect the health of operators, and lower operational costs.
To help you with this, we’ve put together five simple steps for you to follow this winter and beyond.
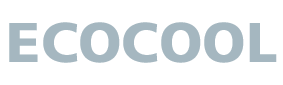
ECOCOOL GLOBAL - Water-Miscible Cooling Lubricants from FUCHS
Our ECOCOOL range of > DMG MORI approved water-miscible cooling lubricants is expertly designed for > metalworking applications, particularly machining processes.
With superior lubricating properties, ECOCOOL is engineered to improve operator safety and extend your sump life as well as ensuring exceptional cutting performance and enhancing process stability while minimizing skin irritation.
> ECOCOOL GLOBAL 1000
Premium water-miscible cutting and grinding fluid designed for the Aerospace, Medical, and Semiconductor industries. Designed for multi-metal applications, ECOCOOL GLOBAL 1000 is > approved by AIRBUS and meets stringent industry standards with the following approvals:
- AIRBUS: AIPS 00-00-010
- BOEING: BAC 5008 (tested)
- ROLLS ROYCE: CSS 129/131 Cat. 2
- SAFRAN: PR 6300 Ind A
> ECOCOOL GLOBAL 1500
Premium water-miscible, mineral oil-free cutting and grinding fluid tailored for the Aerospace and Automotive industries, suitable for multi-metal applications.
> ECOCOOL GLOBAL 2000
Premium water-miscible cutting and grinding fluid designed for the Automotive industry, offering excellent performance across multi-metal applications.
> ECOCOOL GLOBAL 2500
Premium heavy-duty water-miscible cutting and grinding fluid specifically formulated for aluminum applications, delivering exceptional performance and reliability.
> ECOCOOL GLOBAL 3500
Premium water-miscible cutting and grinding fluid designed for cast iron machining applications, providing excellent performance and durability.
> Find out more about our ECOCOOL range
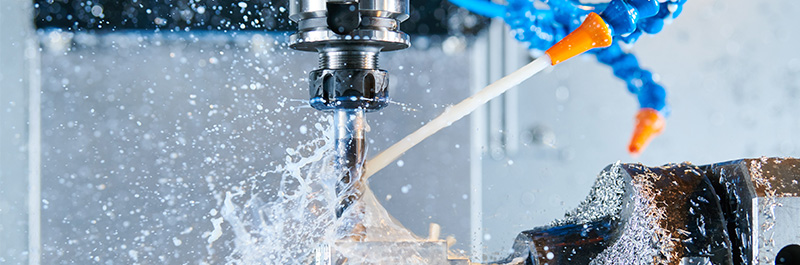
Winter maintenance made easy
For more information or product guidance, contact our team of experts using the form below.
ANY QUESTIONS?
Here at FUCHS UK, our teams of experts are always on-hand to answer any of your questions. With years of experience in industrial lubrication you can trust that you’re in safe and knowledgeable hands.
NEED TECHNICAL HELP?
Speak to our technical team today to learn more about how FUCHS products can help you.