What's missing from your winter workbench?
A workbench is an essential piece of equipment in any workshop or garage, providing a sturdy and stable surface for a variety of tasks. Whether you're a professional or a DIY enthusiast, having a good workbench can make a significant difference in your work quality and efficiency.
What you stock your workbench with is equally as important. FUCHS have a wide range of workshop maintenance products including maintenance sprays, pastes and cutting compounds that will make maintenance, assembly and production tasks all that much easier.
Which FUCHS products should be on your workbench this winter?
FUCHS offers a comprehensive range of high-performance solutions designed to tackle the toughest challenges in machining, lubrication, and corrosion prevention. Whether you’re working with intricate electronics, heavy machinery, or precision metal components, FUCHS has the perfect product to keep your operations running smoothly.
Explore the accordion section below to discover the must-have FUCHS products for your workbench.
Dewatering and penetrating fluids are specialized products essential in various industrial applications, designed to remove water, penetrate surfaces, and provide lubrication and rust prevention. These fluids play a crucial role in maintenance, enhancing the performance and longevity of equipment and materials.
Dewatering fluids are specifically formulated to eliminate water from surfaces or materials, preventing rust and corrosion. Common applications include:
- Metalworking: Removing moisture from machined parts to protect against rust.
- Construction: Managing water in excavation sites or during concrete curing processes.
- Wastewater treatment: Facilitating water removal from sludge.
Penetrating fluids are designed to penetrate into surfaces, offering multiple benefits such as lubrication, rust prevention, and cleaning. Their key uses include:
- Loosening rusted parts: Freeing stuck bolts and components.
- Lubrication: Providing long-lasting protection against friction and wear.
- Corrosion protection: Forming a barrier against moisture and contaminants.
By incorporating products such as > FUCHS MAINTENANCE SPRAY and > FUCHS SILKOPEN, industries can rely on advanced solutions for efficient water removal, enhanced lubrication, and superior corrosion resistance.
Wet and dry film lubricants are specialized products designed to reduce friction and wear, enhancing equipment performance, extending service life, and minimizing maintenance requirements. Both types of lubricants help enhance equipment performance, extend service life, and reduce maintenance needs. The choice between wet and dry film lubricants typically depends on the specific application and environmental conditions.
Wet film lubricants
Wet film lubricants are liquid-based products applied in a wet state to provide exceptional initial lubrication. They are particularly well-suited for applications where surfaces are exposed to moisture or require immediate lubrication, such as moving parts, gears, and chains. These lubricants penetrate and adhere effectively to surfaces, forming a protective layer that reduces friction and wear, ensuring optimal performance and durability in demanding conditions.
Dry film lubricants
Dry film lubricants create a solid coating on surfaces once dried, often utilizing solid lubricating agents such as graphite or molybdenum disulfide. They are ideal for high-temperature settings, dusty or dirty conditions, and situations where wet lubricants could attract contaminants, such as in bearings, locks, and sliding surfaces. These lubricants offer durable, long-lasting protection and lubrication while resisting the accumulation of dirt or debris, making them well-suited for use in demanding environments.
FUCHS products like > FUCHS SILICONE SPRAY, SUPERLUBE PLUS SPRAY, and GLEITMO 916 SPRAY offer reliable and efficient solutions for both wet and dry lubrication needs, ensuring optimal performance across a wide range of applications and conditions.
Selecting the right lubricant for chains and wire ropes is essential for ensuring longevity, reducing wear, and preventing corrosion. FUCHS offers high-performance products in this category designed to meet a variety of industrial needs including:
Oil-based lubricants:
- Mineral oils: Provide effective penetration and decent rust protection for general lubrication needs.
- Synthetic oils: Deliver superior temperature stability and friction reduction compared to mineral oils, ideal for demanding conditions.
Grease:
- Lithium grease: Offers excellent water resistance, making it suitable for heavy-duty and outdoor applications.
- Molybdenum Disulfide grease: Contains solid lubricants for outstanding load-bearing performance, ideal for high-pressure environments.
Penetrating lubricants:
Thin, oil-based lubricants that penetrate into tight spaces to reduce friction and prevent rust. Particularly effective for freeing stuck components.
Dry lubricants:
Graphite or PTFE. Non-greasy and clean, these options are suitable for environments where dirt and grime accumulation must be avoided.
Chain-specific products:
Formulated to cling to chain surfaces and resist fling-off during high-speed operation, ensuring consistent lubrication and protection.
Considerations and maintenance tips
When choosing a lubricant for chains and wire ropes, consider environmental factors like temperature, water exposure, and contaminants, as well as the application method—whether spray, brushing, or dipping. Regular maintenance and reapplication are crucial to extending their lifespan.
Always clean chains or ropes before applying new lubricant to remove dirt and residue. Follow manufacturer recommendations for product selection and reapplication intervals to ensure optimal performance.
By using CHAIN LUBE AEROSOL, FLT LUBE AEROSOL, ROPE LUBE AEROSOL, or > WHITE GREASE AEROSOL, and adhering to maintenance best practices, you can ensure optimal performance, reduced wear, and extended service life for chains and wire ropes.
Assembly pastes and sprays are vital for ensuring smooth assembly and disassembly of mechanical components. They provide lubrication, prevent galling, and protect against corrosion, enhancing performance and reliability in a wide range of applications. FUCHS offers top-quality lubricants designed for superior performance in demanding conditions including:
Assembly pastes
- Anti-seize pastes are formulated with metal particles, such as copper or aluminum, suspended in a grease base. These pastes are applied to threads and joints to prevent galling and seizing, ensuring that components can be easily disassembled even after prolonged exposure to heat or moisture.
- Thread lubricants typically contain molybdenum disulfide or graphite, which reduce friction on threaded fasteners, improve torque accuracy, and minimize the risk of thread stripping. This ensures reliable clamping force in assemblies.
- High-temperature pastes are specifically designed for applications like exhaust systems, where components are exposed to extreme heat. These pastes retain their lubricating properties at high temperatures, preventing seizing and wear.
Assembly sprays
- Lubricating sprays, typically containing oils or silicone, provide a thin, penetrating layer of lubrication to reduce friction and protect surfaces. These are useful for hard-to-reach areas and can reduce friction in moving parts.
- Protective coating sprays form a protective layer, often made of wax or polymers, to shield components from rust and corrosion. These sprays are ideal for parts that will be stored or exposed to harsh environments.
- Bonding sprays include adhesives or sealants that create strong bonds between surfaces while allowing flexibility. These sprays are particularly useful in applications with significant vibration.
Considerations and maintenance tips
When choosing an assembly paste or spray, ensure compatibility with the materials involved, whether metals or plastics. Temperature range is critical; select products capable of withstanding the operating temperatures of your application. Finally, consider the application method—pastes may require brushing, while sprays offer quick and even coverage for convenience.
Always clean surfaces thoroughly before applying pastes or sprays to maximize adhesion and effectiveness. Apply only a thin, even layer to avoid excess, which could lead to contamination or interfere with component function.
By using products like > FUCHS COPPER ANTI-SEIZE and > FUCHS COPPER PASTE, you can enhance the efficiency and longevity of mechanical assemblies, ensuring reliable performance even in challenging conditions.
Electrical contact cleaners are essential solutions for maintaining the performance and reliability of electrical components by removing dirt, grease, oxidation, and other contaminants.
Types of electrical contact cleaners:
- Solvent-based cleaners are formulated with solvents like isopropyl alcohol, acetone, or specialized agents. They effectively dissolve oils, grease, and contaminants without leaving residue. These quick-drying cleaners are ideal for sensitive electronic components where rapid evaporation is essential.
- Non-flammable cleaners are designed with formulations that prioritize safety in high-risk environments. They clean electrical components effectively while significantly reducing fire hazards, making them suitable for areas where flammability is a concern.
- Contact cleaners with lubricants combine cleaning agents with lubricants to protect against wear. They are perfect for sliding contacts or components subject to friction, providing both immediate cleaning and long-term lubrication to reduce wear and extend component life.
- Foam cleaners feature foam-based formulations that allow precise application. They cling to vertical surfaces and penetrate hard-to-reach areas, minimizing overspray and waste while ensuring thorough cleaning for intricate components.
Uses of electrical contact cleaners
Electrical contact cleaners restore electrical conductivity by cleaning connectors and terminals, removing oxidation, and eliminating debris. For switches and relays, these cleaners ensure reliable operation by preventing contamination-related failures. Circuit boards benefit from safe, residue-free cleaning, protecting sensitive components from dust and grime. Automotive applications, such as cleaning ignition systems and battery terminals, also rely on these products to maintain efficient electrical connections.
Benefits of electrical contact cleaners
Using electrical contact cleaners enhances conductivity by removing barriers like oxidation and debris. These cleaners help prevent corrosion, extending the life of electrical components. Quick-drying formulations enable rapid reassembly and reduce downtime, while their non-corrosive properties ensure compatibility with sensitive electronic parts, including plastics.
Application tips
For optimal results, follow these application guidelines. Always read the manufacturer's instructions to ensure safe and proper use. Apply cleaners in well-ventilated areas to avoid inhaling volatile solvents. If there is any uncertainty about material compatibility, test the cleaner on a small, inconspicuous area before full application.
By choosing the right product, such as FUCHS CONTACT CLEANER, and applying it correctly, you can ensure optimal performance, longevity, and reliability for your electrical components.
Drilling, tapping, and cutting compounds are indispensable for optimizing machining operations, reducing friction, extending tool life, and ensuring cleaner, more precise cuts. FUCHS provides advanced solutions for these applications, each designed to enhance machining performance.
Drilling Compounds
Drilling compounds are essential for lubricating and cooling drill bits during operations. Oil-based lubricants, often made from mineral or synthetic oils, offer excellent lubrication and cooling properties, while water-soluble coolants are ideal for high-speed operations, mixing with water to provide both lubrication and cooling. Aerosol sprays are highly convenient, delivering a fine mist that penetrates tight spaces, ensuring precision and ease of application.
Tapping Compounds
Tapping compounds are formulated to minimize friction and enhance chip removal during tapping. Paste formulations provide maximum lubrication, clinging to the tap and workpiece for effective performance. Liquid lubricants offer easy application and are often water-soluble for simple cleanup. Aerosol tapping fluids allow precise application directly to the tap and workpiece, enhancing efficiency and performance.
Cutting Compounds
Cutting compounds are used in machining processes like milling, turning, and grinding to reduce friction and improve surface finish. Cutting oils, typically mineral-based, deliver superior lubrication and cooling, while synthetic fluids offer excellent cooling properties without petroleum, making them suitable for environmentally sensitive applications. Emulsifiable oils mix easily with water and are versatile for a variety of machining operations, providing effective lubrication and cooling.
Benefits of Using Compounds
The use of drilling, tapping, and cutting compounds brings significant advantages such as reducing tool wear by minimizing heat and friction, extending tool life. Improved surface finishes result from reduced chatter and better chip removal, ensuring high-quality machined surfaces. Effective chip control prevents clogging, leading to smoother and more efficient operations, while lower operating temperatures protect both the workpiece and the tools from heat-related damage.
Application Tips
To maximize effectiveness, choose the appropriate compound based on the material and specific machining operation. Apply generously to ensure adequate lubrication and cooling, particularly in high-speed applications. After use, clean tools and surfaces thoroughly to prevent residue buildup and maintain the longevity of equipment.
By incorporating products like FUCHS SILKUT SPRAY, SILKUT LIQUID 1000, and SILKUT COMPOUND 1000, you can enhance machining performance, achieve better results, and extend tool longevity, making them essential for efficient and effective machining processes.
Corrosion preventatives are essential for protecting metal surfaces and components from rust, oxidation, and environmental damage. By forming a protective barrier, these products help extend the life of equipment and materials, ensuring reliability and performance in a variety of industrial and environmental conditions. FUCHS offers a range of high-quality corrosion preventatives tailored to meet diverse protection needs.
Benefits of corrosion preventatives
- Long-lasting protection: Forms a barrier to prevent rust and corrosion, even in harsh conditions.
- Versatility: Suitable for a wide range of applications, from equipment maintenance to component storage.
- Enhanced equipment life: Reduces the risk of failure due to rust, improving overall reliability and reducing maintenance costs.
Application tips
- Clean the surface: Ensure the metal is clean and dry before applying the corrosion preventative for maximum adhesion and effectiveness.
- Apply evenly: Use sprays for consistent coverage, especially in hard-to-reach areas.
- Reapply as needed: Regular maintenance ensures ongoing protection, especially in environments with high humidity or corrosive elements.
By using products like > FUCHS MAINTENANCE SPRAY, > FUCHS MAXILUBE, and > ANTICORIT CPX 3373 SPRAY, you can provide exceptional protection for metal surfaces and components, extending their service life and maintaining peak performance across various industrial and environmental applications.
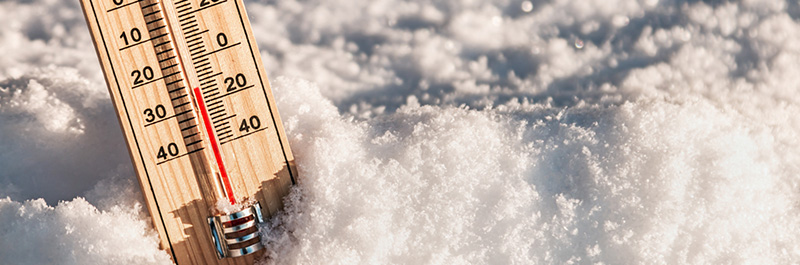
Winter maintenance made easy
Using the right products for the job ensures that your equipment remains in top condition, reducing the risk of breakdowns and extending the lifespan of your machinery.
For more information or product guidance, contact our team of experts using the form below.
ANY QUESTIONS?
Here at FUCHS UK, our teams of experts are always on-hand to answer any of your questions. With years of experience in industrial lubrication you can trust that you’re in safe and knowledgeable hands.
NEED TECHNICAL HELP?
Speak to our technical team today to learn more about how FUCHS products can help you.