The specialist for gas engine oils
Particularly in the field of stationary gas engines, choosing the right engine oil and being able to call on competent support for continuous operation are critically important for reliable operation, high availability and efficiency, as well as a long service life.
Gases and their composition
In different applications of cogeneration units, different fuel gases can be used. Fuel gas is defined as an appropriate gas mixture for gas engines, which vary in composition, fuel value and knock resistance. The methane number of natural gas is for example 70 – 90 and decreases the knock resistance in comparison to gases like biogas, sewage or landfill gas with a methane number of 100 – 160. The gas quality and composition can vary during operation which can be compensated by using an adjusted facility and engine management. If the characteristics of the gas quality change or if dangerous substances increase, the lifetime, the reliability and the efficiency of the engine can be shortened. Fuel gases consist of components which provide the needed energy for the combustion process and impurities which influence reliable operation.
The main components define the most important fuel characteristics (e.g. knock resistance, fuel value, combustion temperature, flame propagation speed and ignition properties) involved in the engine operation and combustion process. The main important components are methane, the main contributor to the fuel value and energy content of the combustion gas, hydrogen and chained hydrocarbons such as propane and butane as well as inert gases like nitrogen and carbon dioxide.
The most usual impurities found in the different gas types are sulphur compounds or hydrogen sulphide, chlorine, fluoride, silicon compounds or dust. The effects of these impurities are proportional to the amount present in the engine during operation. The lower the fuel value of the combustion gas, the higher the amount of gas being used in the combustion process. With more gas being used there is a higher amount of impurities. In order to be able to evaluate and compare different gases even with identical concentrations of pollutant elements but with different energy content, the concentration of trace elements must be referenced to the fuel value of the combustion gases. Impurities such as sulphur compounds occur primarily on special gases so that the oxidation and the acidification proceed faster. Another difficulty of these gases is the varying composition and quality which can change continuously during operation. The engine and engine oils therefore have to meet different challenges depending on the gas type.
Change of the acidification of different fuel gas types – the same oil, same engine model
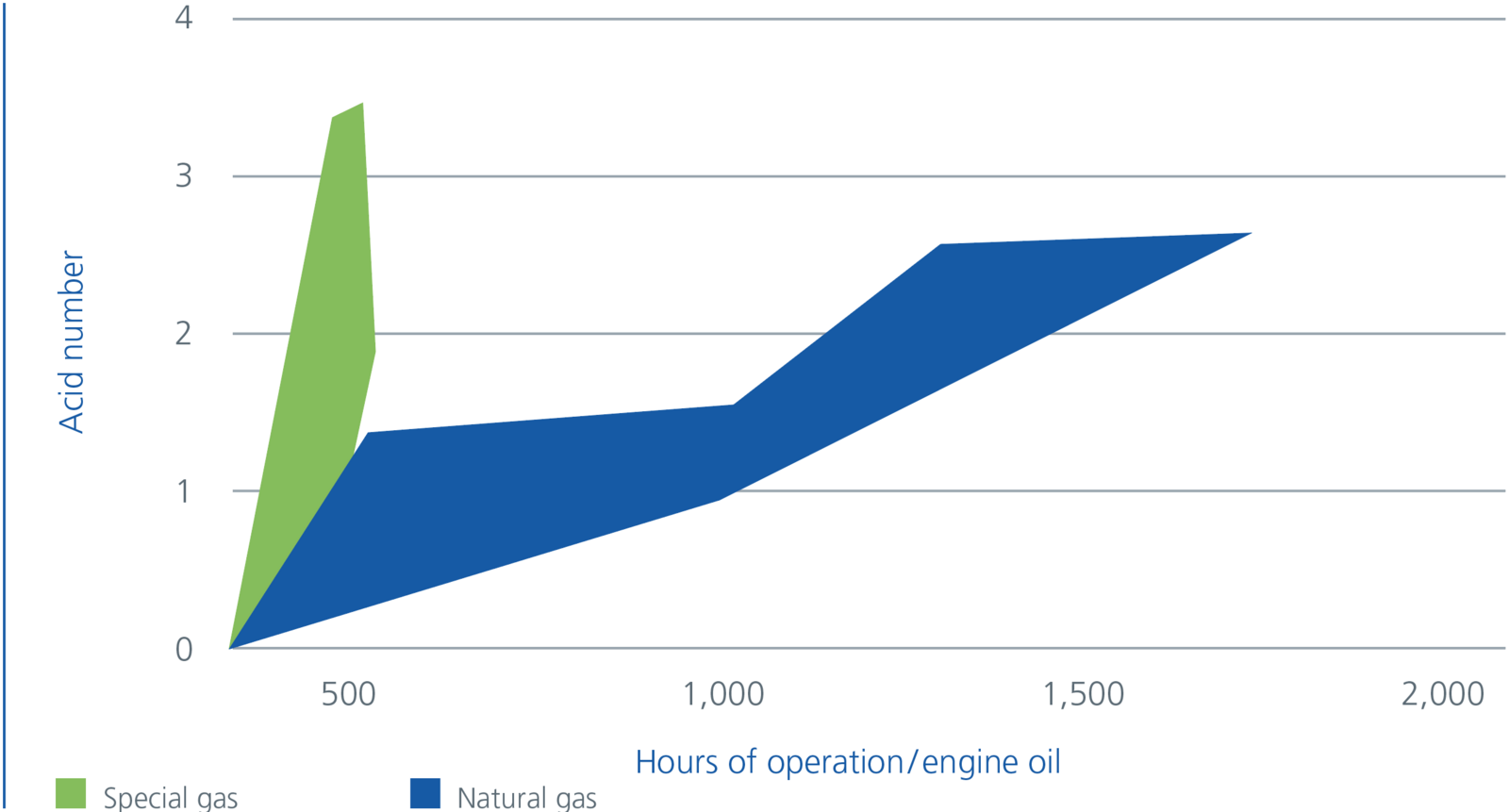
Where can I buy?
Speak to our team to find your local TITAN distributor.
> Telephone: +44 (0) 1782 203700
> Email: contact-uk@fuchs.com
I need help choosing.
Unsure which product best suits your application?
Requirements for gas engine oils
Gas engines used in power stations, landfill sites, sewage plants and biogas plants are characterised by continuous operation at full load. The good anti-knock properties of fuel gas causes high effective pressures in gas engines which again lead to very high combustion temperatures.
The result is an increased formation of NOX which reacts with the used engine oil and causes oxidation and nitration along with an increase in viscosity. The formation of acids (organic and inorganic) pose the danger of oil acidification and corrosive wear in the oil circuit.
Consequently, gas engine oils have to meet the following demands:
- High thermal stability
- High resistance to aging
- Good neutralisation properties
Depending on the application, the characteristics of engine oils have to be customized. It can be differentiated for example between applications with natural gas or cleaned biogas (reduced sulphur content) and applications with special gases.
The high performance engine oils of the TITAN GANYMET range
TITAN GANYMET engine oils from FUCHS were specially developed for stationary Otto and pilot injection gas engines and offer a broad spectrum of applications.
Special high-performance additives with a high resistance to oxidation and nitration guarantee reliability even under extreme operating conditions. Our special formulations offer a maximum degree of wear protection and work against the formation of sludge, deposits, acids & corrosion.
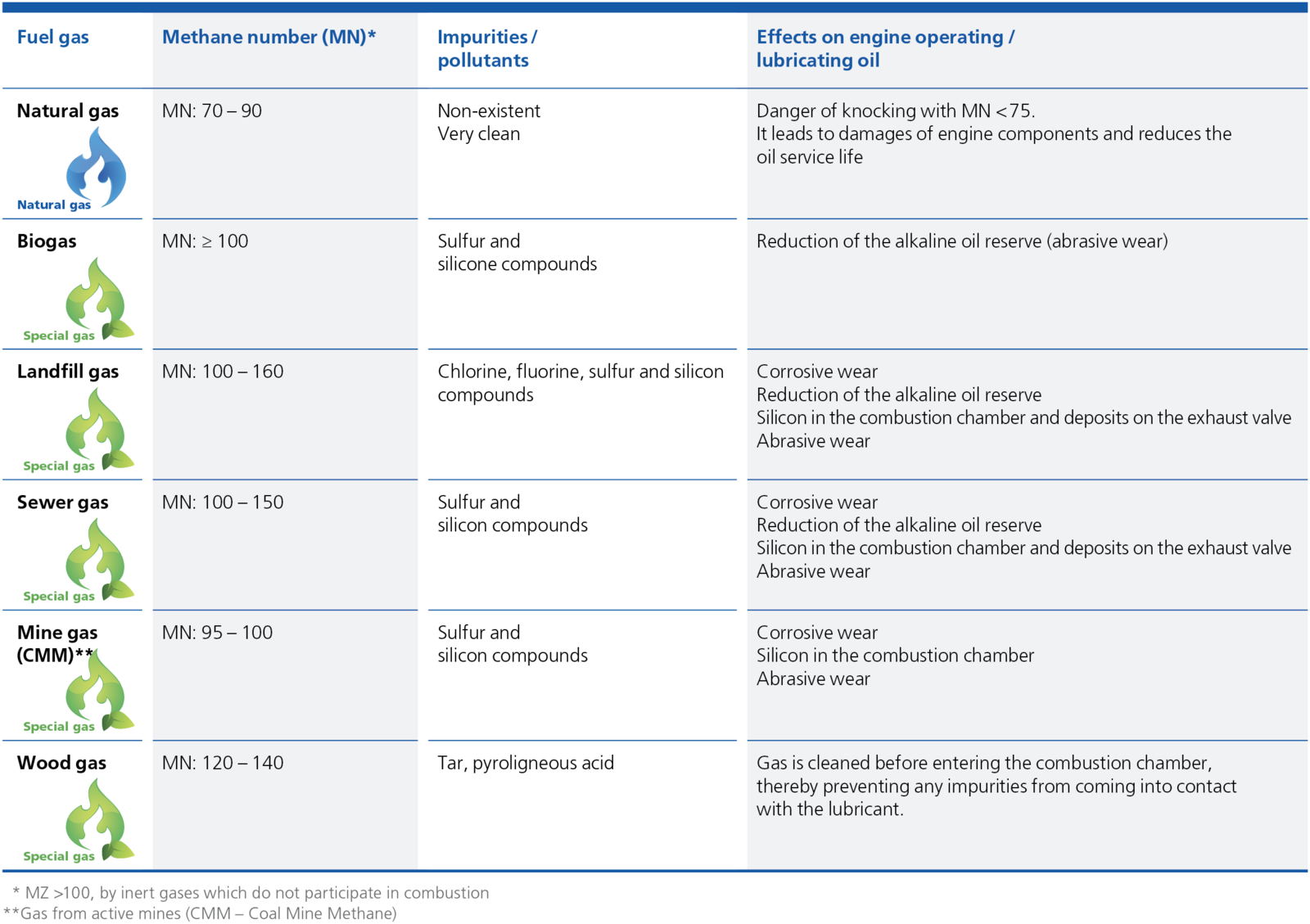
Technical background
In an engine oil, the sulphated ash (SA) is formed from certain additive (functional metallic) components in the oil. These ash-forming agents affect engine cleanliness, neutralisation capacity, ageing resistance and the anti-wear properties of the oil. The element zinc is one of these ash-forming agents and is usually found in conventional engine oils as a metalorganic compound in the form of ZnDTP (zinc dialkyldithiophosphates). This compound offers high protection against wear and corrosion as well as good antioxidation properties. However, this additive gets into the combustion chamber of the engine by passing the piston rings. When burnt, ash components are formed and build deposits on the pistons, cylinder head, valves and catalytic converter. These deposits cause wear of engine components and lead to a drop in performance and premature engine failure.
The following applies: The higher the proportion of ZnDTP, the greater the wear protection and antioxidation characteristics – but also the amount of sulphated ash.
Additives which contain calcium compounds are the principal constituent of socalled detergents. These play a significant role in avoiding coking deposits on the piston crown, rings and ring grooves. The deposits again have a grinding effect on the cylinder liners and lead to polished surfaces. The detergents are also responsible for the neutralisation capacity and alkaline reserve (expressed as the Total Base Number, TBN) of an engine oil and thus reduces acidity increase and thereby protects against corrosion.
The following applies: The higher the proportion of detergents and calcium compounds, the greater the engine cleanliness and the TBN – but also the proportion of sulphated ash formed.
Therefore carefully balanced formulations are required to enable the use of these additives: A higher proportion of detergents and ZnDTP in the oil results in greater neutralisation capacity, better wear protection and improved ageing resistance but also causes increased formation of sulphated ash. It is hence impossible to develop a universal product for all gas engines. As engine manufacturers recommend or prescribe various sulphated ash limits for different types of fuel gas, the possibilities of optimising single character istics of an oil are limited. Therefore it is important to select the most suitable gas engine oil for the specific application. Engine manufacturers generally recommend low-ash (SA <0.5 % wt) oils for engines running on relatively clean gases (e.g. natural gas) because they allocate greater importance to engine cleanliness than to high neutralisation capacity. Engine oils with a higher sulphated ash content (max. 1 % wt) however, are usually accepted when using gases with a higher degree of noxious components such as sulphur, chlorine and fluorine as an increased neutralisation capacity is required to achieve longer oil change intervals.
Clear advantage for zinc-free technology
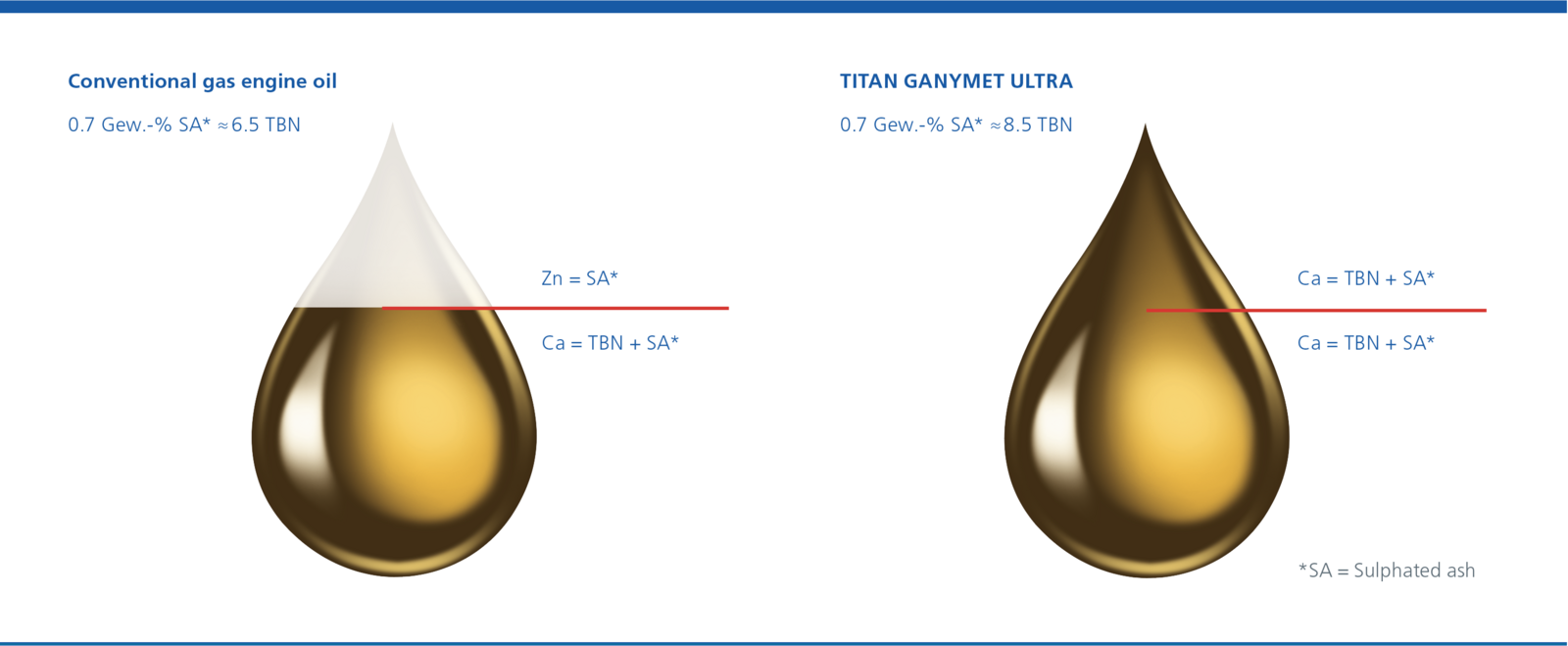
Why zinc-free?
Basically, it should be noted that ash formers also have to be distinguished from each other, as not all sulphated ash is the same. The decisive factor here is the choice of additives used in the engine oils. Ash deposits that are formed, for example, during the burning of calcium compounds are softer than precisely those that are formed during the burning of zinc. Consequently, the danger of abrasive wear in the engine is much lower.
In the drop diagram above, two different formulation technologies are illustrated in a highly simplified way. The drop on the left illustrates the conventional formulation technology, the right drop illustrates the zinc-free Low SAPS technology developed by FUCHS – both in terms of ash-forming components and TBN contribution.
The drop volume represents the sulphated ash contribution of each formulation. As the sulphated ash contribution was set at 0.7 wt% for both formulation technologies to allow a performance comparison between the two technologies, the volume of both droplets is identical.
The main difference between the two additive technologies is that in the zinc-free formulation the zinc was replaced by specially adapted calcium compounds. In order to be able to maintain the necessary wear and corrosion protection as well as the antioxidation properties, for which the zinc was previously responsible, new types of ash-free additives were used. The great advantage of these new additives is that they do not influence the sulphated ash contribution and thus an almost unlimited addition is possible.
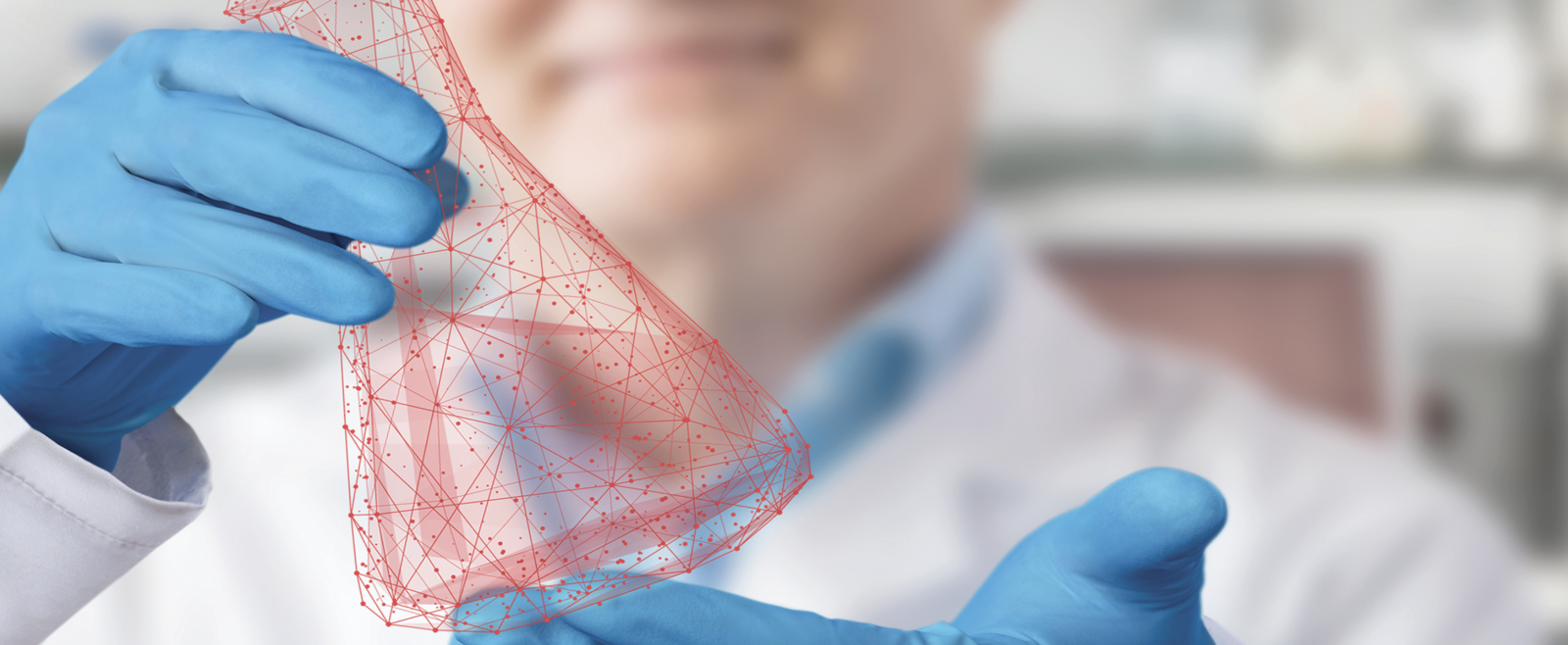
Minimal losses of phosphorus
Phosphorus is an important component of anti-wear additives used in engine oils. During the combustion process, however, a certain amount of phosphorus is burned and enters the catalytic converter via the exhaust gases. There it can lead to poisoning effects on the catalytic surfaces and consequently to a loss of function. Thus, the performance and service life of the catalytic converters depend, among other things, on the amount of phosphorus contained in the exhaust gas.
Various scientific test procedures have shown that the use of zinc-free additive technology results in less phosphorus in the exhaust gases. Consequently, both the wear protection of the lubricant and the service life of the catalytic converter can be sustainably extended.
All advantages at a glance
- Significantly longer oil change interval due to higher neutralisation capacity (approx. 25% higher TBN) with the same sulphated ash content.
- Improved wear protection and higher oxidation stability due to new, ashless additives.
- Lower abrasive wear due to zinc-free sulphated ash deposits.
- Higher engine cleanliness.
- Minimisation of phosphorus losses and thus extension of wear protection and performance as well as catalytic converter life.
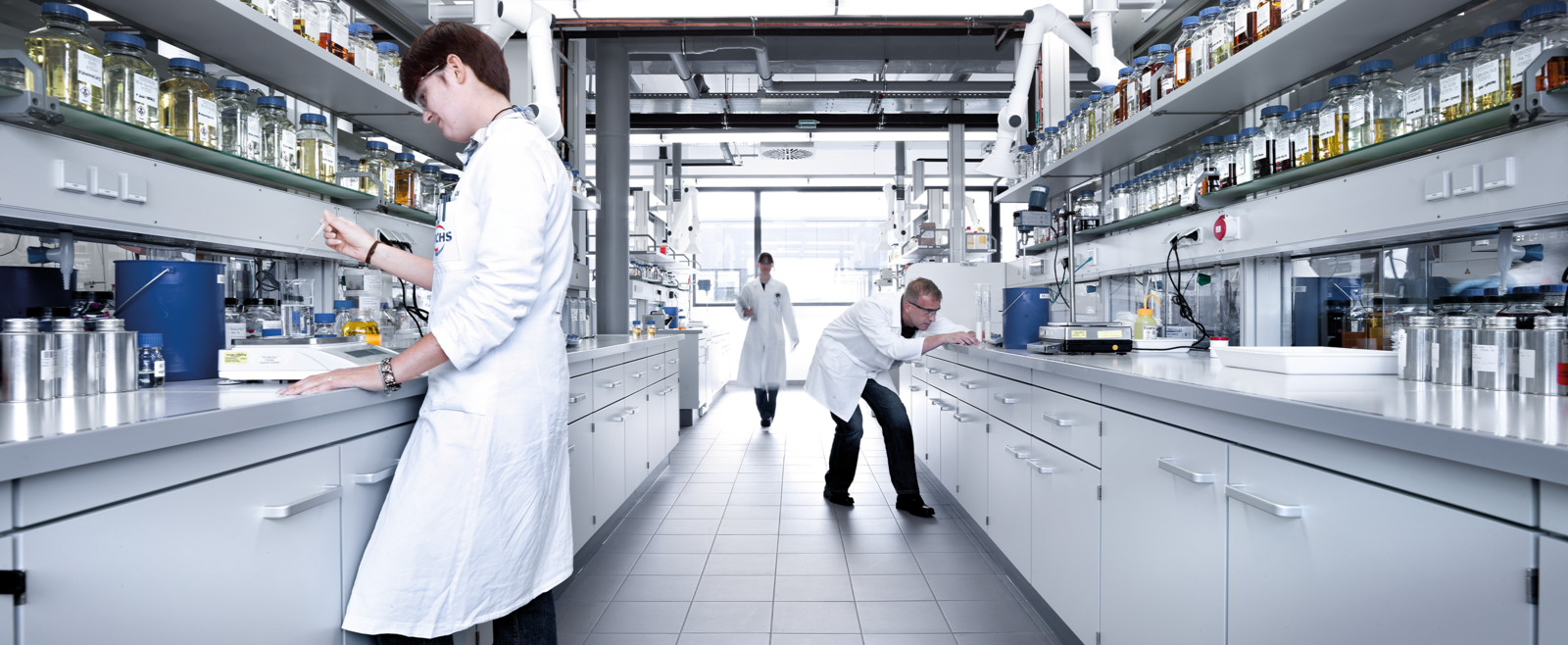
Condition monitoring of the engine oil
Monitoring and laboratory analysis
When a gas engine is commissioned, the oil change intervals are initially determined by the recommendations of the engine manufacturer.
It is therefore necessary to monitor the condition of the engine oil with routine oil analyses (see chart) and then to set individual oil change intervals for every engine.
The lubricant’s life and the optimum oil change intervals are however dependent on:
- Gas quality
- Lubricating oil quality
- Environmental conditions
- Modes of engine operation
Regular analyses of used oil show the rate of degradation
in all the measured parameters. So deviations in gas quality or different operating modes can be compensated quickly.
This avoids potential engine damage and corresponding repair costs.
Make use of our fast, professional and complete service for oil analysis. Your engine will benefit.
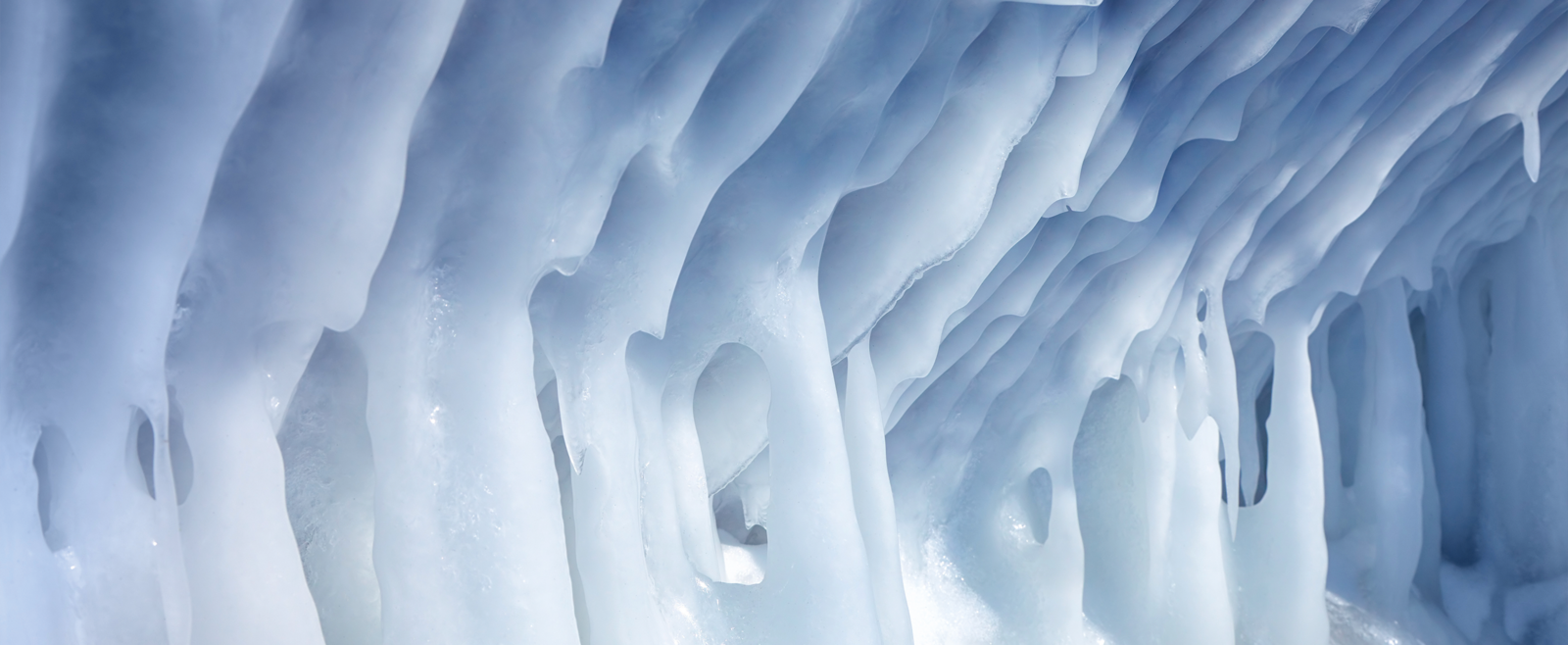
MAINTAIN antifreeze coolants for gas engines
Gas engines create large amounts of heat during the combustion process. As the engine and its components can only release heat slowly, additional coolants are necessary, so that the engine does not break down due to overheating.
Our “ready-mixed” anti-freeze coolants are especially easy to use on stationary engines. No on-site mixing is needed.