There’s more to lubrication than just oil
FUCHS Smart Services bring far more to the table than “just” a product.Instead, we combine performance fluids, digital technologies and a wide range of services into customised solutions.
Solutions that do not only fit your individual processes perfectly but strive for improvement – along every step of the way and beyond.
Pushing forward – with a reliable partner
At the very core of everything we do is a promise of reliability. We move your world – not just to keep things running at all times, but to improve your whole production process.
To do so, we constantly look ahead and at the big picture. A holistic approach that encompasses ecological, social and economic aspects.
The approach
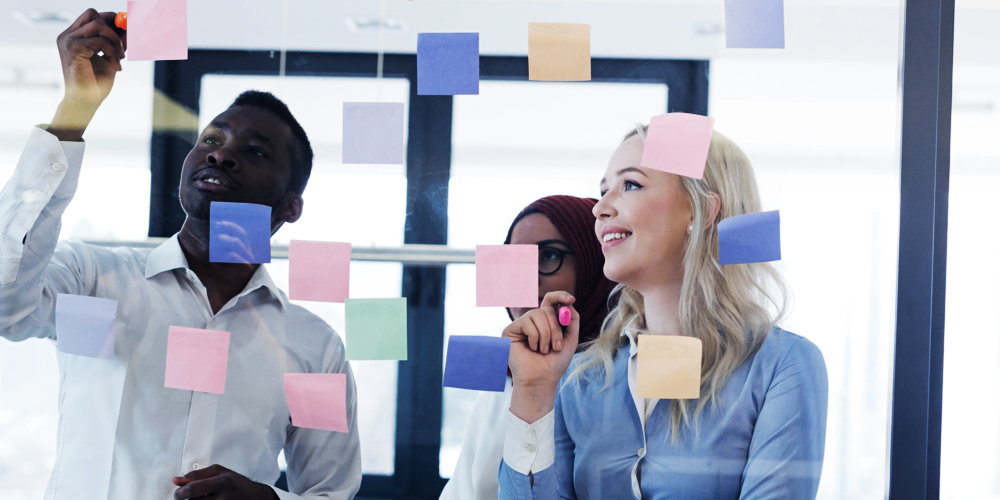
Let's assemble your solution
Start a partnership that will push your business forward.
FUCHS Smart Services
> smartservices@fuchs.com
Customised solutions
Modular is our standard
Our solutions’ basic pieces are completely modular and can be combined freely to suit your specific situation and goals.
Regardless of its constituents, your solution will always be based on the holistic FUCHS process.
- Lubricants
- Lubrication
- Equipment
- Digital tools
- Reliability
- Processes
- Automation
- Best practices
- Six Sigma
Manage options
No matter the circumstances you operate in or the challenges you face – we’ll find a suitable way to deliver our services, tools and lubricants.
In order to facilitate this level of customisation, the options to implement your solution range from one time visits – for instance to set up a piece of technology – to more long-term support.
For example, the continuous remote analysis of your lubricants condition or the on-site management of stocks and waste.
Modular solutions - Start assembling
Lubrication - Digitisation - Services
Combine from modules below to build your solution - encompassing services, tools and lubricants.
We will partner with you to select the best combination of modules to enable you to address, manage and control your lubrication and reliability needs.
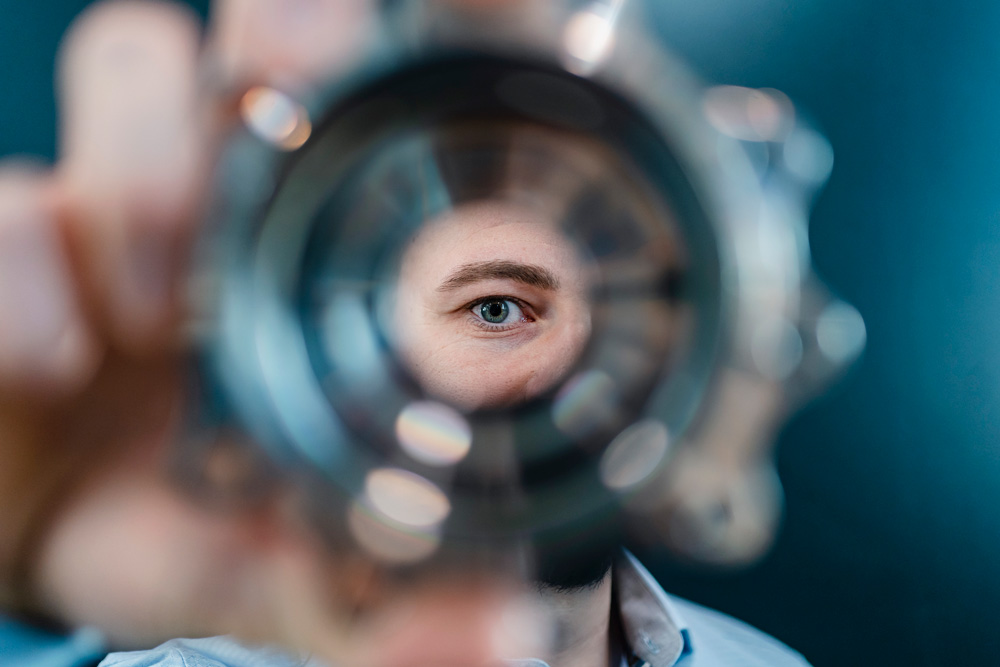
Understand
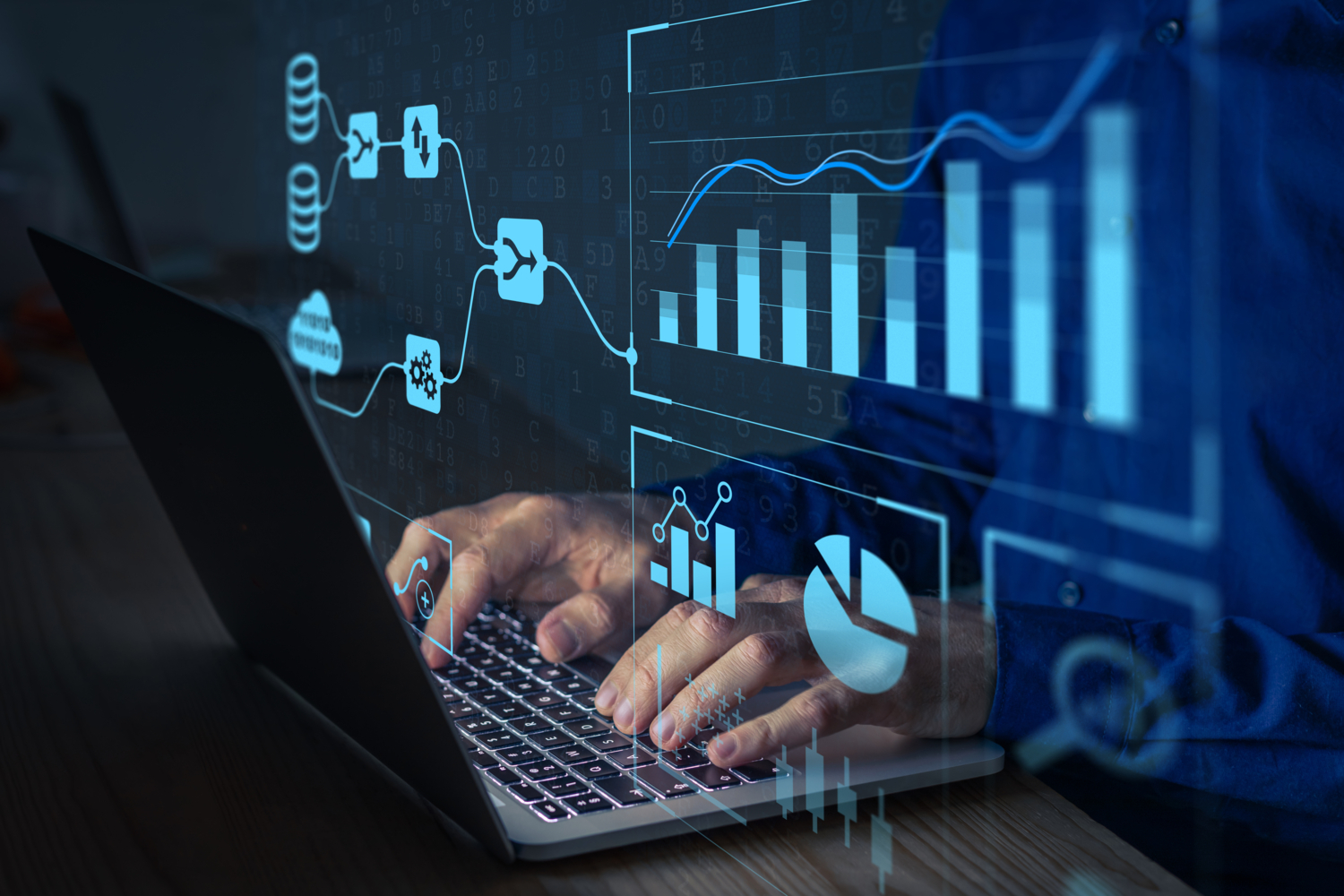
Analysis
FUCHS Smart Services combine performance fluids, digital technologies and a wide range of services into customised solutions.
Solutions that do not only fit your individual processes perfectly but strive for improvement – along every step of the way and beyond.
Four steps to a better solution
On the road to efficient lubrication solutions, we pursue an approach that is both uniform and holistic. This starts with an analysis of your situation and processes.
Together, we then create a solution that perfectly matches your goals. This might be an individual product, services (such as training or maintenance), a digital solution, or everything together as a complete package.
But we do not stop there. Whether it’s remote support, digital monitoring or on-site management, our teams will continue to support you – and they will never stop looking for improvements.
Read more...
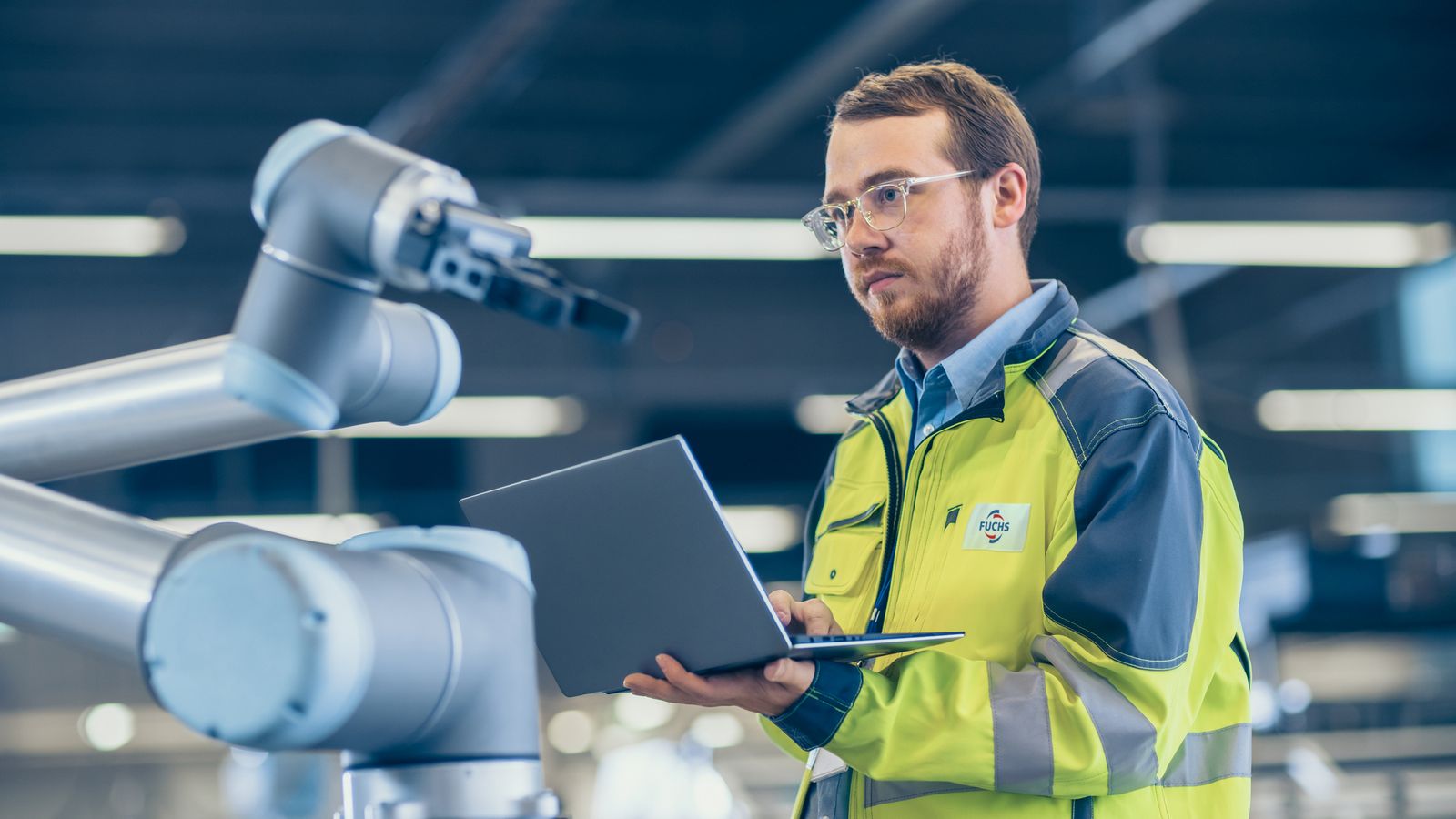
Lubrication Self-Assessment
FUCHS Smart Services offer this tool as a starting point to establish where your business is in terms of lubricants, lubrication management and reliability.
Our dedicated team will work with you to review your needs through assessments built to find gaps in a lubrication program to help identify and tailor solutions. By holistically assessing the journey of the lubricant from orders to delivery, storage and handling, in-service lubricant asset evaluation, a final needs analysis report can document where you are today.
We will provide an interactive PDF document to complete for your business. The information will be scored and the results will form the basis of an improvement programme, made in conjunction with the FUCHS Smart Services team.
A projection can be forecasted based on your goals and aspirations for the business. The tool can then be used again at various stages of the journey to monitor what improvements have been made.
This can be done with a member of the Fuchs team or sent out as a self-assessment.
Assessment
The assessment will cover the following areas:
- Lubricant storage & handling
- Cleanliness of plant
- Highlight obvious issues
- Planning and scheduling
- Observe current practices, recommend improvements
- Strategy to Implement 6S standards
- Understanding goals and limitations
- Safety improvements
- Contamination control
- Offer lubricant best available technology (BAT) for the asset
- Asset improvements for extending lubricant life-cycle
Read more...
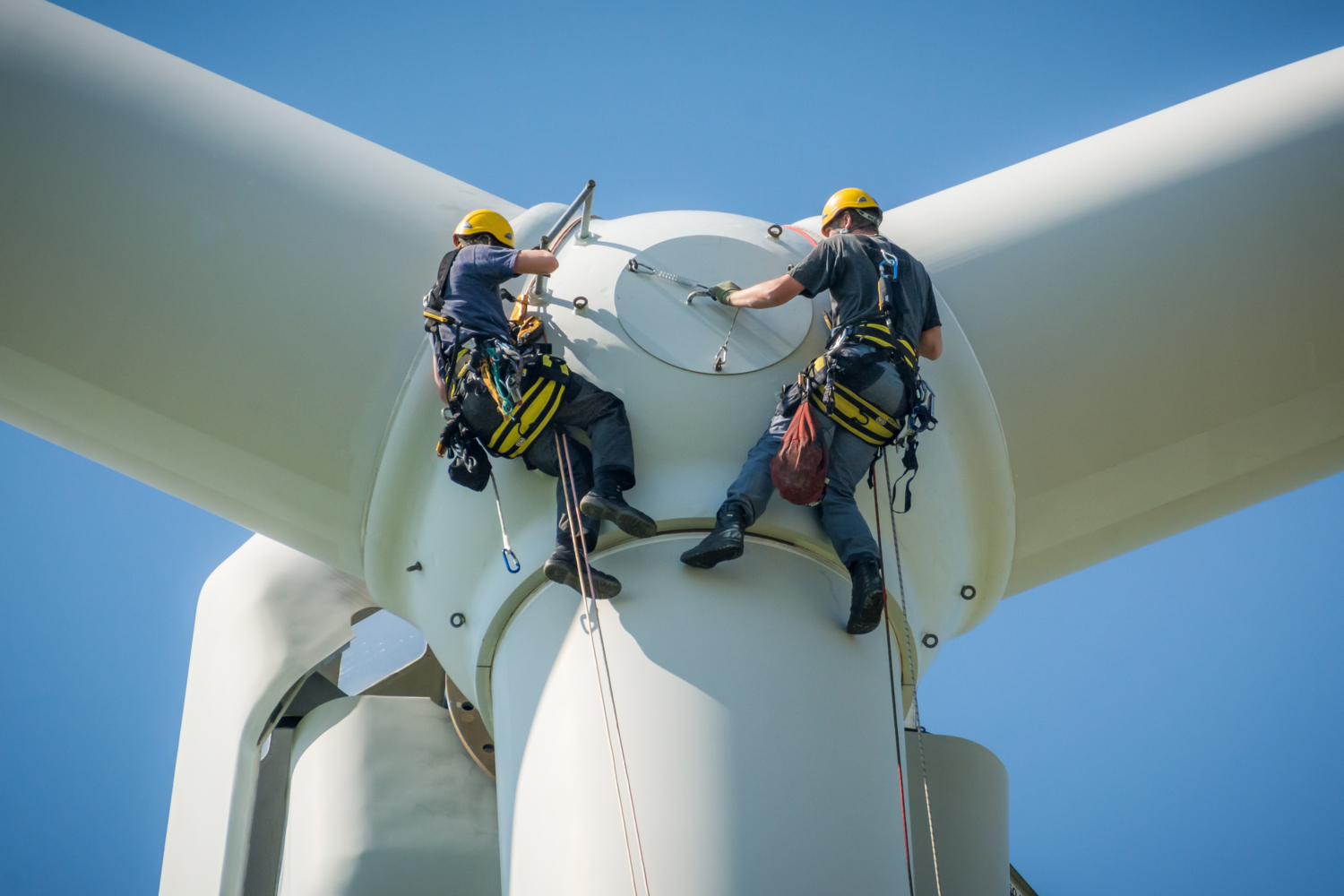
Risk Assessments
Risk assessments are an important and essential part of our process. No two businesses or production plants are the same, and each could host any number of hazards.
Prior to any work commencment, FUCHS Smart Services will conduct the nesessary risk assessments to ensure that hazards are identified, the risks assosiated are measured and suitable control measures are put into place. We will work along side your safety personnel to ensure that any undertaking by FUCHS is conducted in a safe manner.
Develop
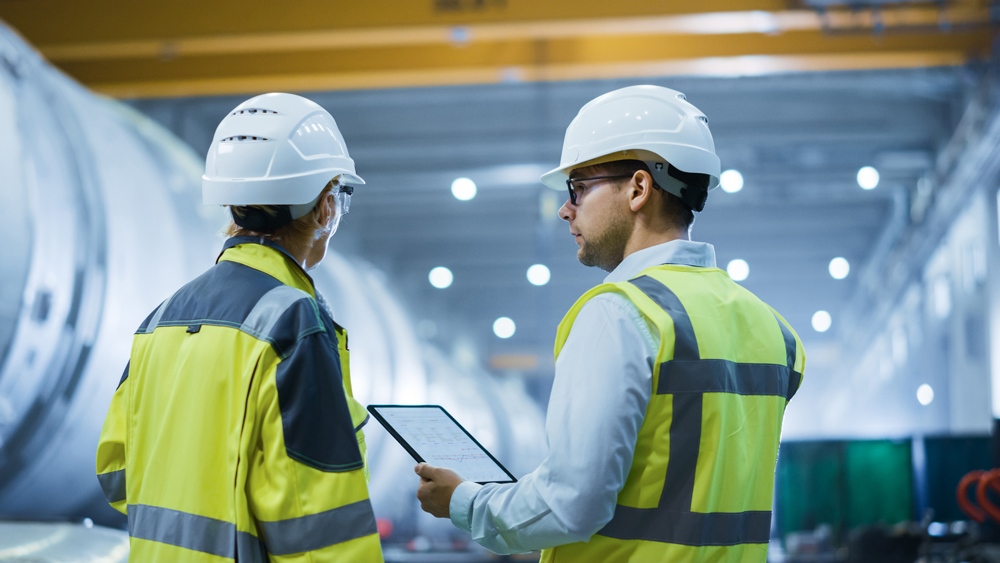
Consultation
As we have previously stated, ‘there is more to lubrication than just oil...' At the very core of everything we do is a promise of reliability.
We move your world – not just to keep things running at all times, but to improve your whole production process. To do so, we constantly look ahead and at the big picture. A holistic approach that encompasses ecological, social and economic aspects.
As part of this process we are able to offer consultation on a range of products, tools and services.
We hold a wealth of knowledge and experience and are able to provide reliable, in-depth information, support and knowledge transfer in the following areas:
- Lubricants
- Lubrication
- Equipment
- Digital tools
- Reliability
- Processes
- Automation
- Best practices
- Six Sigma
Read more...
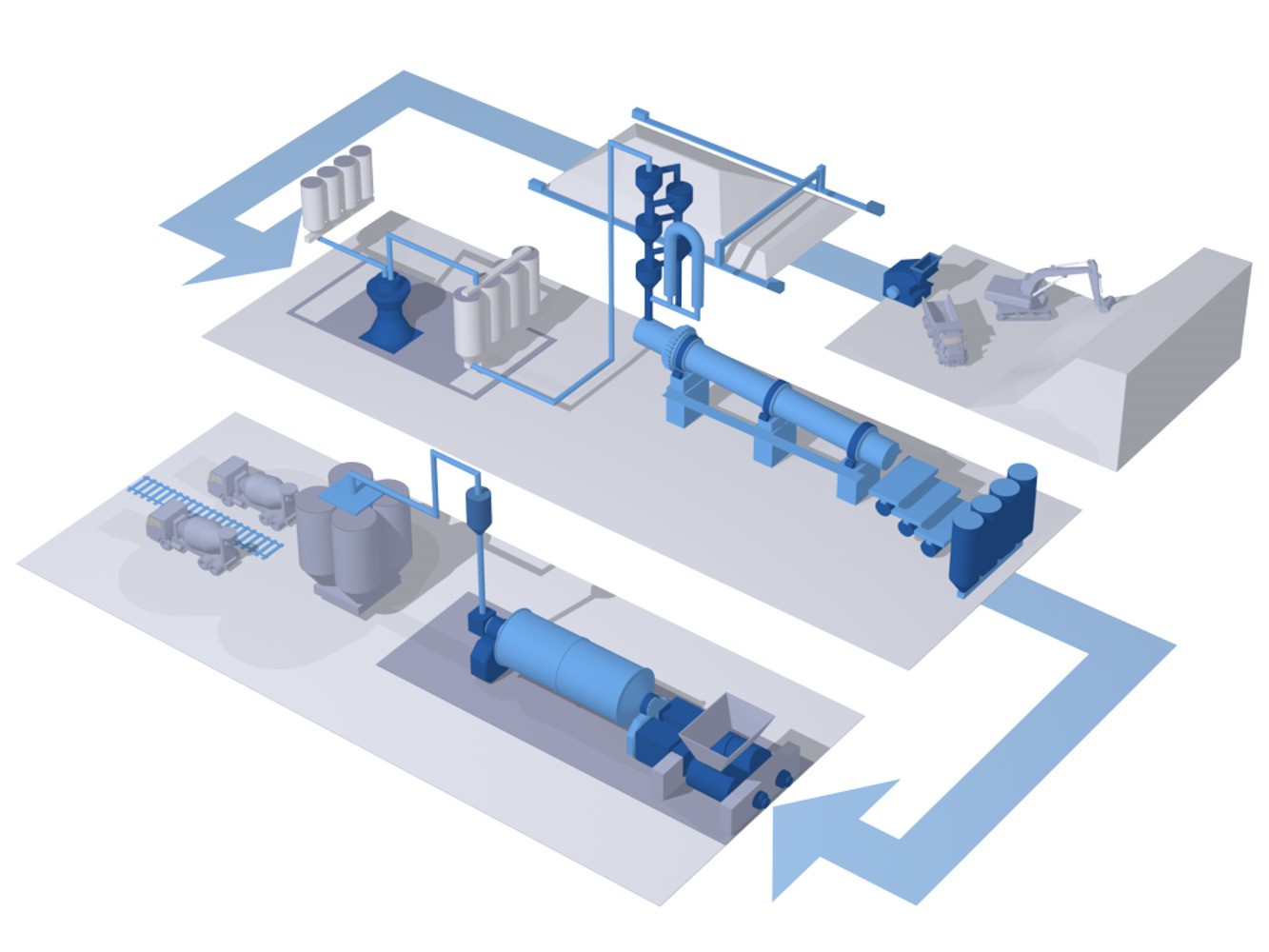
Lubrication Survey
As part of the FUCHS Smart Services programme we are able to undertake lubrication surveys for all, or part of your manufacturing operations.
The extent of the survey can be tailored to suit your business requirements, ranging from a basic lubricants overview, through to a detailed lubrication assessment for each asset/point of application.
The information from the survey can then be used in a number of ways;
- Complement your existing lubrication records or Maintenance Management System
- Uploaded into our FluidsConnect web-based management tool to create lubrication schedules and routes
- Excel or PDF versions to be used for creating lubrication schedules etc.
Read more...
What is a Reliability Culture?
Lubricant budgets can typically range between 2-4% of a maintenance budget: but if managed incorrectly with bad practices, wrong product selection and employee awareness, that budget can unnecessarily diminish rather quickly through unplanned downtime.
At FUCHS, we believe the fundamental foundation of a reliability programme is well-planned lubrication and a best practice regime.
A holistic approach to lubrication management starting with the 6R’s principles will have a positive impact on the environment by consuming less energy, improving asset value with increased life cycles whilst maximising production availability.
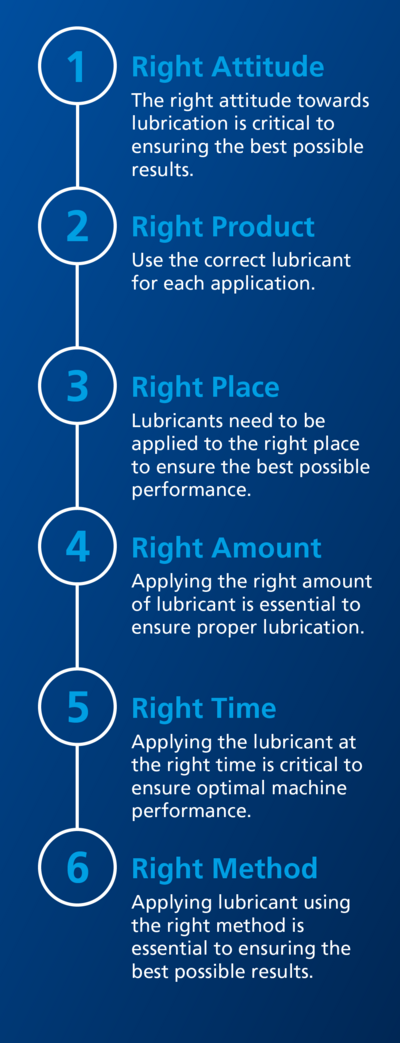
Read more...
Manage
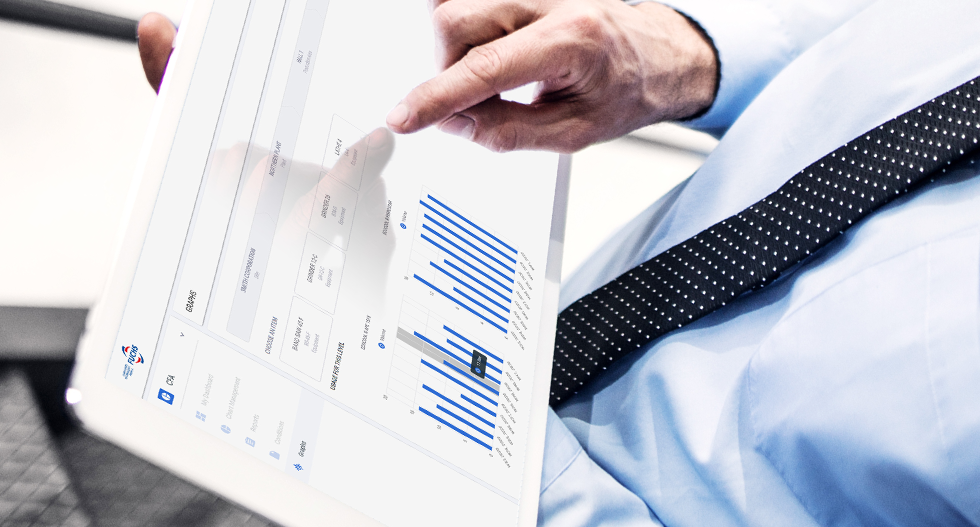
FluidsConnect
Web based management tool
FluidsConnect is an easy to navigate, web based, recording, tracking and reporting tool with integrated KPI measurements; to give maintenance and production engineers immediate and remote access to the current condition of fluids in use.
As an on-line platform, FluidsConnect offers software free centralised management of data, resulting in zero investment requirement from users.
Information can be updated instantly from the time of collection, giving users the latest information from which to make informed decisions on maintenance scheduling, production planning and other operational activities.
Stored data remains confidential and provides customers with a history of fluid usage, condition and concentration. This data further allows users to plan efficient maintenance strategies which will help reduce fluid usage expenditure.
Proactive use of the data allows for improved inventory control, reduced/simplified waste management activity and accurate analysis of fluid consumption by machine, cell or process.
Each data reporting system is designed and developed by the FUCHS team to the bespoke requirements of the user.
The recognised Market Leader
Complete Fluid Management
FluidsConnect helps link all of your FUCHS Service’s together for a more efficient work-flow. By streamlining operations and being able to refer to all your latest data, decisions can be made to help increase productivity, reduce downtime and ultimately reduce costs.
- Individually designed dashboards
- Track & trend fluid conditions
- Remote real-time access to key operating data
- Eliminates unforeseen production problems
- Assists in preventative maintenance planning
- Reduces fluid consumption & expenditure
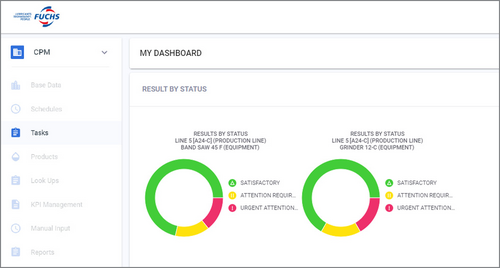
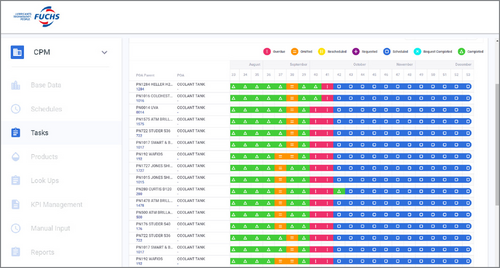
For more information on FluidsConnect,
please contact your FUCHS representative or contact us at contact-uk@fuchs.com
Already registered with FluidsConnect, login here: https://fluidsconnect.fuchs.com
Downloads
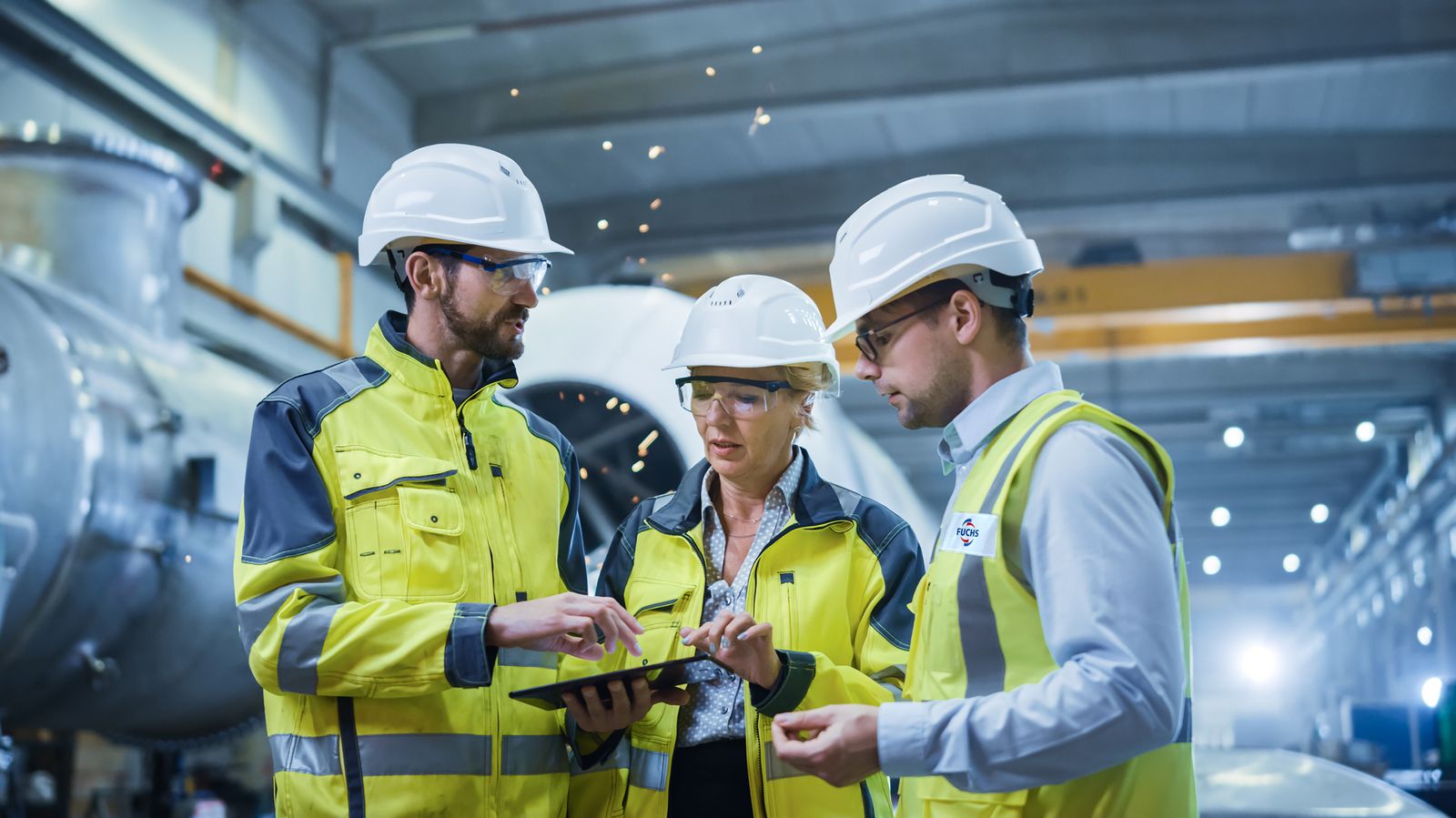
What is Complete Fluid Management?
FUCHS’ Complete Fluid Management is a complete lubricant supply programme which is unique and flexible to meet the requirements of your business. Complete Fluid Management is a carefully managed, structured system of operations in which all aspects and consequences of fluid usage are monitored and assessed.
Expert support
We provide expert support in the areas of fluid supply, distribution, monitoring, maintenance, assessment and disposal, allowing the customer to concentrate on what they know best. Full technical support is provided by a dedicated team of production fluid specialists and extensive laboratory facilities, incorporated into regular site visits to ensure maximum efficiencies.
Why use the Complete Fluid Management service
Our commitment to achieving agreed performance targets that are quantifiable and sustainable, through lowering the direct and indirect costs associated with fluid usage, can only be demonstrated through proven experience and the positive vision that FUCHS brings to all of its Complete Fluid Management customers.
Our programmes are successfully operating in a wide spectrum of industries, including aerospace, foundries, press and body, automotive component manufacture, and food processing plants.
Included in the Complete Fluid Management programme
The Complete Fluid Management programme provides a wide range of services to help your business, some of the services offered include:
- Site-wide fluid management
- Rationalisation programmes
- Environmental compliance assistance
- Advice on best practice and risk assesments
- Waste management and equipment
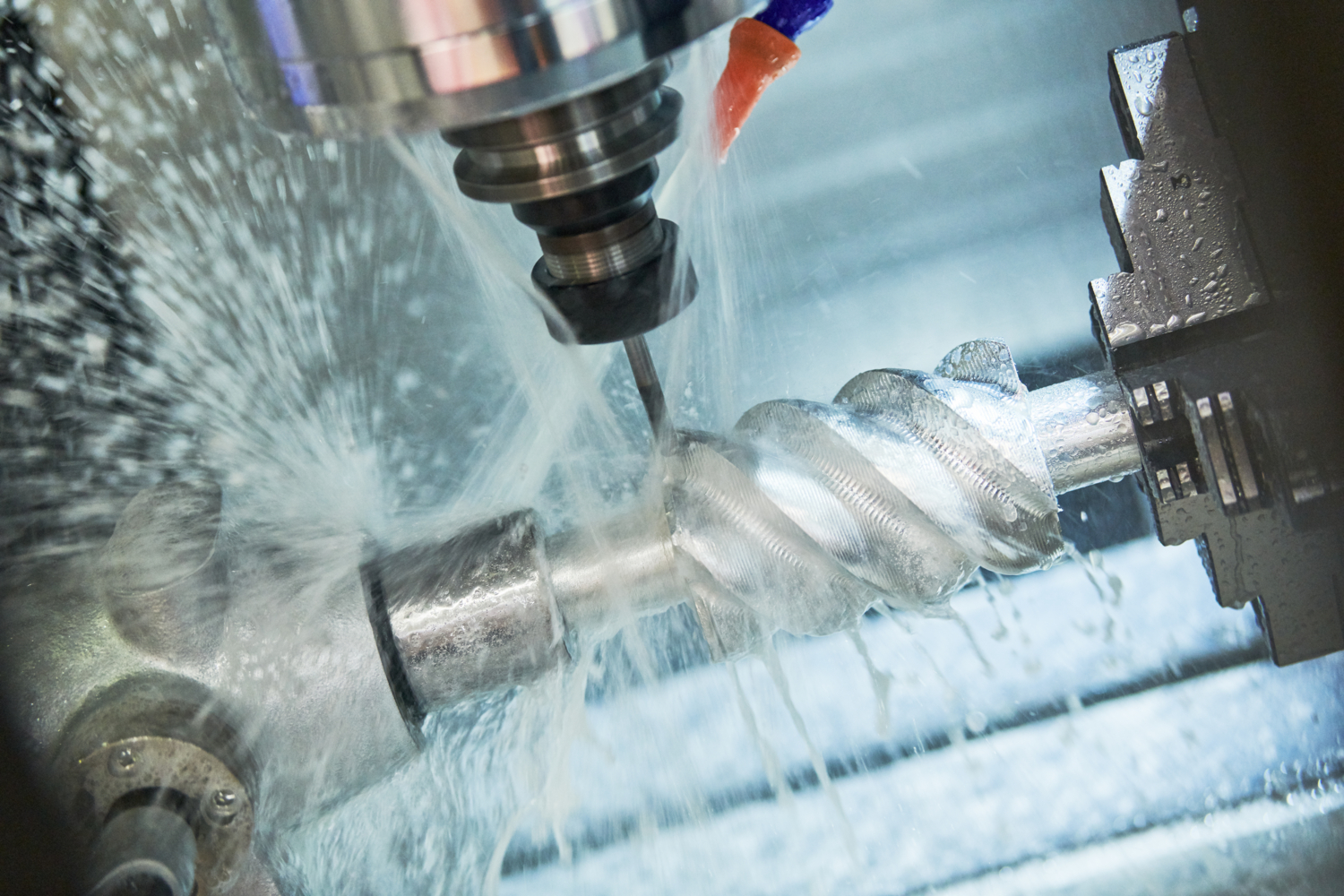
What is Metalworking Fluid Management?
For many leading manufacturers, FUCHS provides a technical support package for supply and management of ECOCOOL/ ECOCUT cutting fluids. Effective coolant management provides reductions on your total cutting fluid spend.
Significant manufacturing efficiencies are provided through:
- Greater asset utilisation
- Reduced downtime
- Improved production rates
- Reduced rejection rates
- Extended tool life
- Reduced coolant usage
- Reduced waste disposal costs
Coolant Management Surveys
FUCHS offers an initial in depth manufacturing site survey carried out by metalworking fluid technicians and fluid management consultants. The survey looks at all operations and processes impacted by the cutting fluid, resulting in a detailed plan of potential improvements using FUCHS technology. The survey provides a plan of how costs can be saved across the full manufacturing process, rather than simply look at “cost per litre” savings. During the survey process, our engineers will look at:
- Fluid technology on site
- Emulsion strength
- Tooling spend
- Waste management
- Maintenance costs
- Downtime minimisation
- Health and safety requirements
- Training on coolant ‘best practices’ to employees
Following each site visit we will provide customers with instructions of necessary actions as well as all of the necessary HSE compliant support documents to ensure that you are able to get an immediate overview of fluid condition.
Equipment Support
As part of our customer support, we assist customers with the equipment required for careful maintenance and handling of cutting fluids including:
- Oil skimmers
- Mixing units
- Dip slides and incubation units
- Storage bunds
- Spill equipment
- Bespoke fluid and water recycling units
- Design and installation of distribution and central systems
Fluid Disposal
We can advise of contractors for the safe collection, transportation and disposal of waste oil.
Read more...
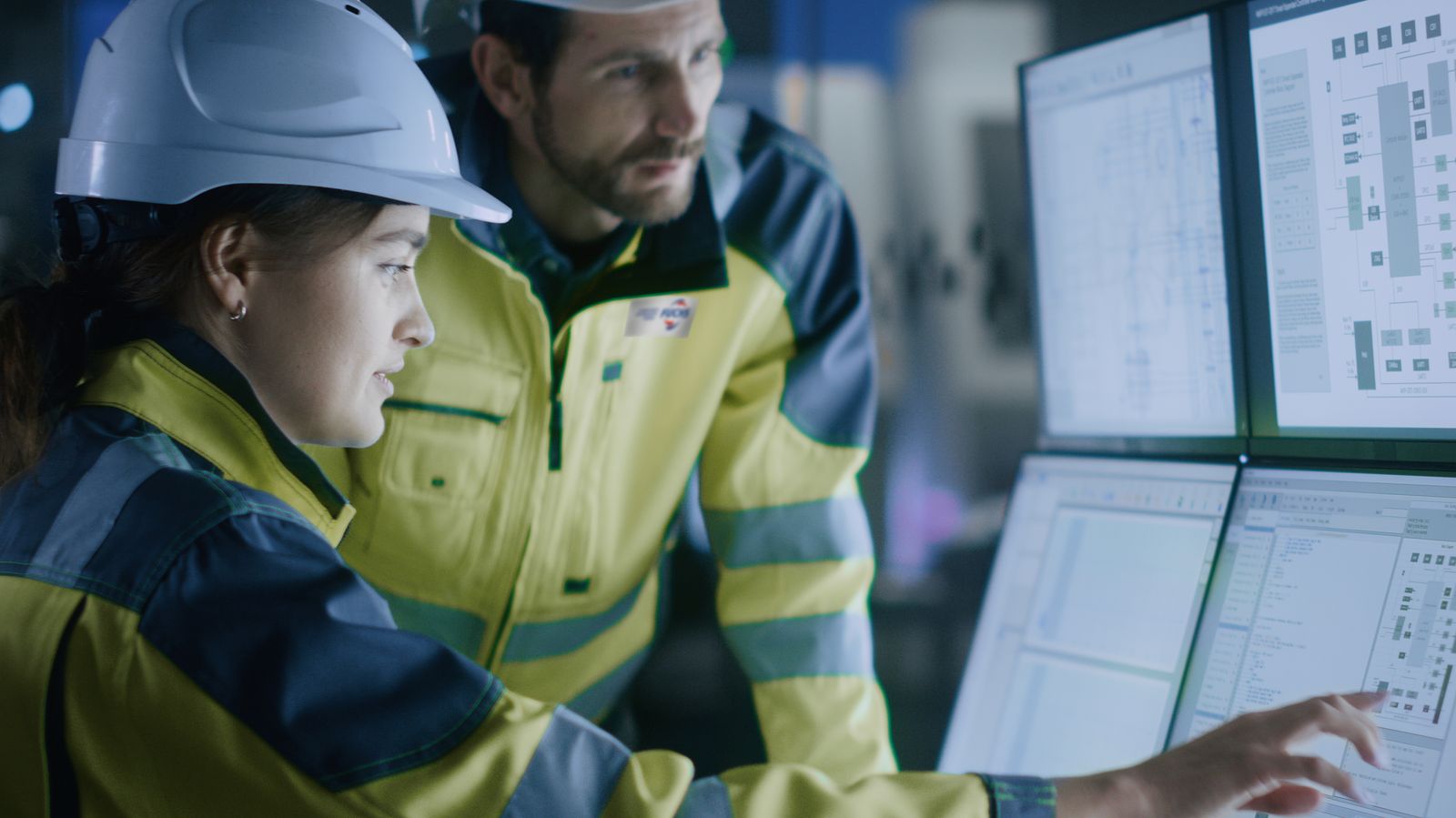
What is Lubrication Management?
All process and manufacturing industries use lubricants as part of an effective preventative maintenance strategy. FUCHS can assist by providing an effective lubrication schedule designed to maximise the efficiency of the plant and equipment.
The FUCHS DNA is to maximise the value for our customers by increasing control and technology, reducing complexity and cost, through a plant review.
Lubrication management survey
The survey can include:
- Improved plant productivity through
- lubricant technology
- Reduce risk
- Rationalise usage
- Control re-lubrication intervals
- Minimise unplanned downtime
- Assist with audit compliance
- Minimise admin and maintenance tasks
- Improve in-service lubricant life cycle
- Individual asset assessment
- Stores management assessment with colour coded identification of all lubrication points
- Catalogue improvements
- Recommendations for condition monitoring/predictive maintenance
- Optional detailed photographic/visual survey of the full manufacturing facility
- Optional use of ‘Fluids Connect’ lubrication management software
To assist our customers, FUCHS provides a number of plant management solutions, including storage and handling equipment, dispensing equipment, labelling of lubrication points and waste disposal management.
Chemical Process Management (CPM)
FUCHS has a dedicated team of experts and engineers who have a wealth of industry knowledge and experience. We have 30 years experience of working at our customers' sites, providing high levels of technical service and support. FUCHS engineers can be based at a customer’s site to assist with all areas of plant lubrication, including:
- Intimately understanding the customer’s requirements and needs
- Providing a personalised site plan
- Implementing cost saving initiatives.
- Ensure adequate stock levels are held
- Providing advice and support on lubricant machinery requirements and modifications
- Carry out condition monitoring and lubricant assessments
- Schedule regular meetings to discuss progress and future opportunities
Read more...
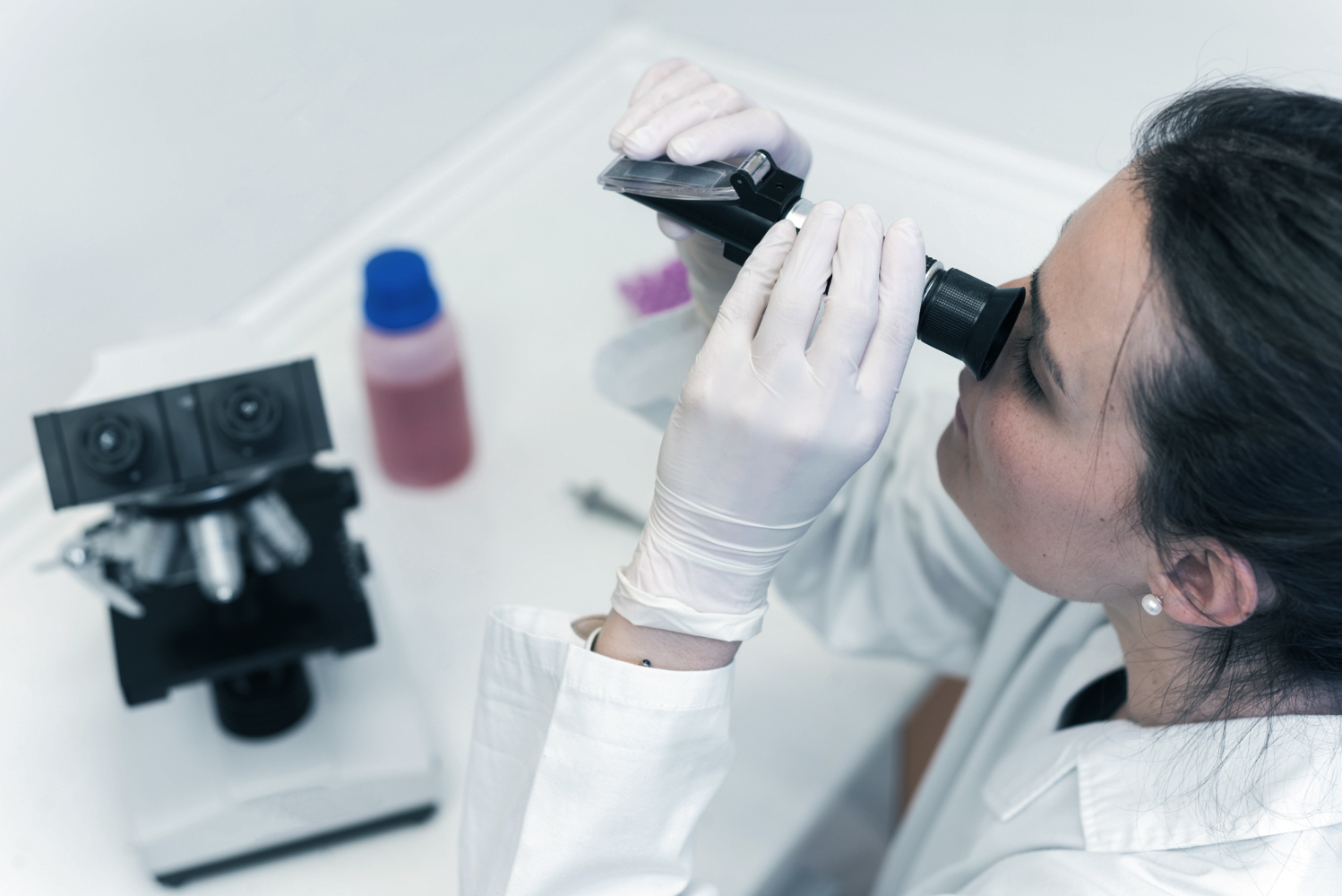
Metalworking Fluid analysis
FUCHS Smart Services offer a complete Metalworking Fluid care programme. Ranging from regular / schedules site visits, through to complete Metalworking Fluid Management with site-based technicians. Additional supported is available from our technical and laboratory teams based at our UK based manufacturing facility.
By their very nature metalworking fluids require constant monitoring and management. We can carry several essential tests on your fluids on site, or at our laboratory testing facilities. This can range from a one-off sample to regular testing to help you to comply with HSE guidelines.
Typical test suites can include:
- Concentration by refractometer
- Concentration by acid titration
- pH value
- Bacteria count
- Fines
Results for each asset can be uploaded into our ‘FluidsConnect’ web-based portal to give you real-time monitoring including tracking, trending history recording etc.
Read more…
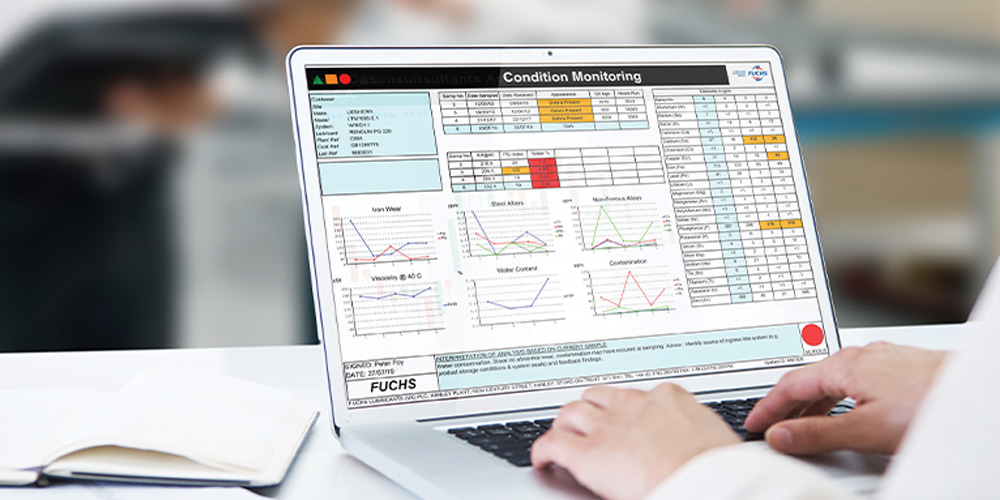
What is Oil Based Condtion Monitoring?
The CENT condition monitoring service is a state-of-the-art production management tool that indicates wear trends, additive levels and sources of contamination.
The advantages brief
- The CENT System is a customised, predictive condition monitoring programme which will reduce maintenance costs and improve reliability.
- Simple to implement, easy to use and no investment in personnel or technology necessary. The CENT System is ready to use with no teething problems.
- Clear, precise feedback in the form of graphs and reports along with suggestions for remedial action. This eliminates time consuming in-house examinations. The CENT Report "Traffic Lights" show immediately if your plant or machinery is in satisfactory condition, and if not, what action is required.
- Immediate telephone or email if the analysis indicates cause for concern. An early warning system you can count on!
How can FUCHS Smart Services help you?
FUCHS Specialists will design a tailor-made, condition monitoring programme for your plant and equipment. FUCHS will recommend sampling points, methods and frequencies. Information on your plant and equipment will be programmed into the CENT Metallurgical database to increase the accuracy of analysis.
Clear and precise feedback is given to the customer in a regular, accurate, detailed report that highlights status indicators in graphical trend format.
CENT has a proven track record in improving efficiency and reliability of machinery across many industries – saving our customers money!
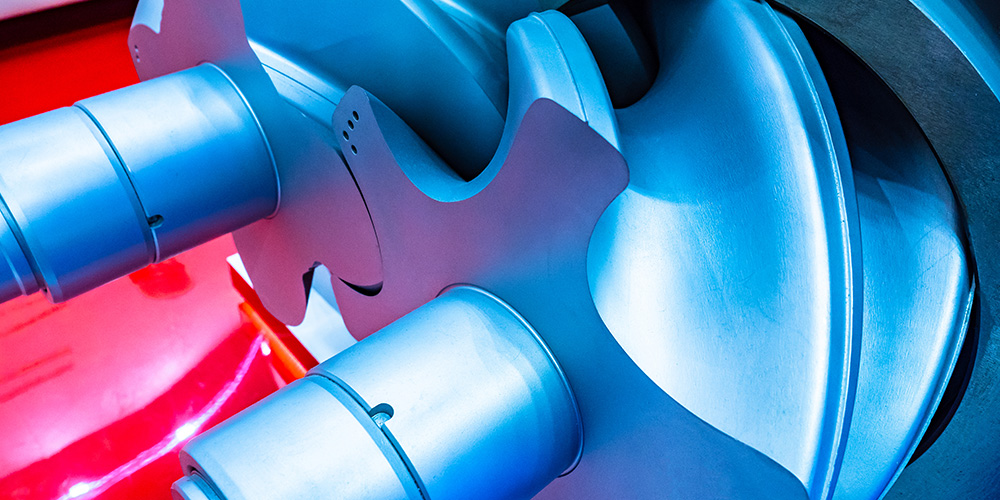
Energy and Cost Savings by using Air Leak Detection Services
Compressed air is easily manufactured, but typically one of the most expensive utilities and largest energy consumers in an industrial facility.
It’s estimated that up to 40% of compressed air is lost to leaks, affecting the reliability of the system and increasing overall operational costs of your business.
The solution is simple - reduce the compressed air leaks.
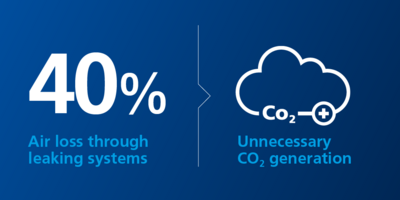
Why reduce compressed air leaks?
There are many important reasons why it is worth investing time and effort to reduce compressed air leaks.
Rising energy costs are affecting everyone across the globe. What impact is it having on your business?
By reducing compressed air leaks you can:
- Save energy and money by identifying and eliminating unnecessary waste.
- Improve the reliability and performance of the compressed air system.
- Reduce environmental impact through reduced electricity consumption and consequently lower carbon dioxide (CO2) emissions.
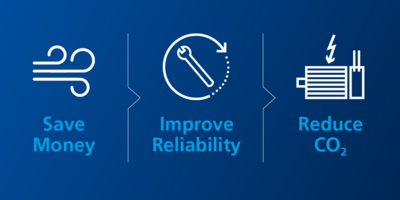
The Solution?
We utilise modern leak detection technology that adopts ultrasound to detect the turbulence caused by even the smallest leaks.
It enables the capture of high-frequency directional turbulence that may otherwise go undetected.
Ultrasound goes undetected by the human ear, which has an audible range typically between 15Hz and 17kHz.
The Results
By detecting, clearly tagging via a smart-phone app, and reporting, the leaks are easily identified for the maintenance team to prioritise.
Once actioned, year on year savings can be achieved and maintained. This demonstrates a commitment to both ISO 50001 energy management and ISO 14001 environmental performance to control and continually improve processes and products.
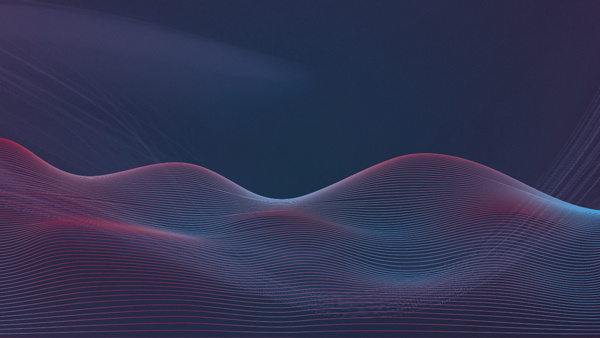
Vibration Analysis - Remote Monitoring
FUCHS Smart Services aim to unlock the full potential of your industrial rotating assets with our cutting-edge vibration analysis services. The technique not only detects machinery defects early but also provides precise diagnoses of any issues, empowering your maintenance team to act before costly failures occur.
Through our modular approach, we seamlessly integrate vibration analysis with our top-tier lubrication and condition monitoring services. Whether you need route-based or sensor-based programs, we tailor our solutions to fit your specific needs.
By harnessing our expertise and advanced technology, we ensure your equipment performs at its peak, minimise unexpected downtime, and boost overall operational efficiency.
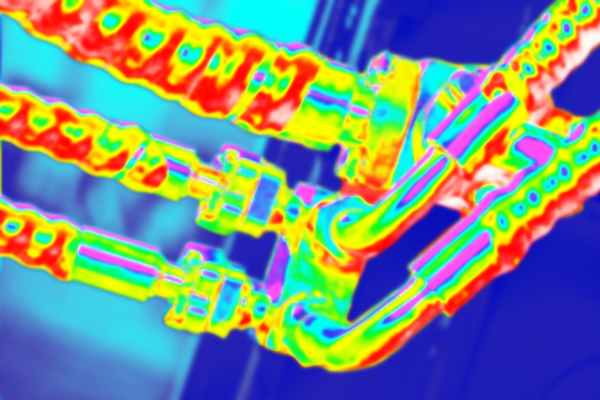
Thermography
A range of technology solutions can be combined to complement identification of early-stage defects to prevent unplanned failures with thermography, oil analysis, ultrasound testing and vibration monitoring for monitoring of rotating and electrical equipment.
Lubrication can be carried out at time-based intervals with combined technology to track condition and trend friction, ensuring critical assets are running at optimum potential with the right amount of lubricant at the right interval.
Combining Thermography and Ultrasound technologies for monitoring your mechanical and electrical assets will ensure defects don’t to go undetected. By identifying potential issues early, maintenance activities can be planned efficiently without unscheduled downtime and more importantly improve safety of the workforce.
Mechanical Condition Monitoring
Production output relies on healthy rotating assets. You can monitor the condition of your plant’s machinery to trend and analyse ultrasound, vibration, temperature, and RPM.
Electrical Testing
Improve employee safety against threats of partial discharge and arcing while monitoring the health of your electrical systems.
Steam System Monitoring
Identify faulty steam traps to increase safety and energy efficiency while lowering costs and carbon footprint.
Valve Monitoring
Ensure efficient process valves are working correctly. Regular inspection quickly identifies which valves are leaking/passing and which ones are closed.
Read more…
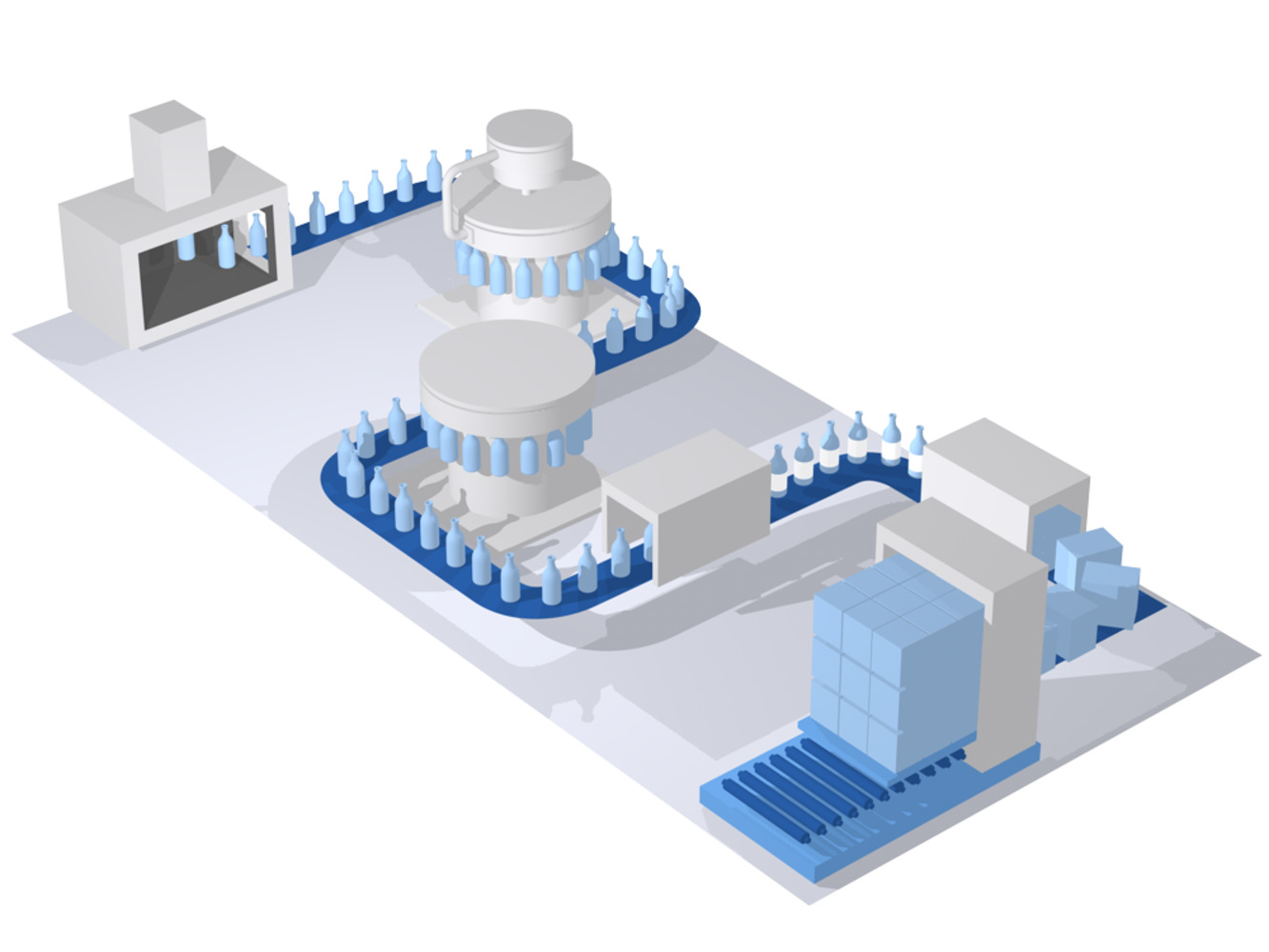
We believe that providing the right assistance to customers is just as important as providing high quality lubricants. By building a strong relationship with our customers, we can ensure the right level of technical support is provided to each manufacturing site including 24 hour technical help, assistance with Lubrication Critical Control Point (LCCP) surveys, oil condition monitoring and much more.
Our CASSIDA food grade lubricant (LCCP) surveys can be used by customers towards their Hazard Analysis and Critical Control Points (HACCP) audit compliance.
Following on from a site visit from one of our trained technical team, customers will be provided with a report on each lubrication point, including any areas for improvement, and the report will be discussed in full. Customers will be assisted with improving plant efficiency, reliability and safety.
Lubrication Compliance Manuals
Customers are provided with a personalised Lubrication Compliance Manual which contains a list of food grade lubricants on site, technical and safety data sheets, NSF registration letters and ISO 21469 and other manufacturing plant certificates. Our CASSIDA Lubrication Compliance Manuals assists users with audit compliance.
Dispensing and Storage Solutions
Our dispensing and storage solutions assist customers with best lubricant practices and meeting audit requirements. Our CASSIDA Lube Centre holds all the small pack lubricants, allowing them to be easily stored and displayed.
To further aid identification, we are able to supply colour coded aerosols, grease cartridges and grease nipple colours. Dispensing pumps, grease guns and oil safe containers can be supplied to customers to facilitate ease of usage.
Optimise
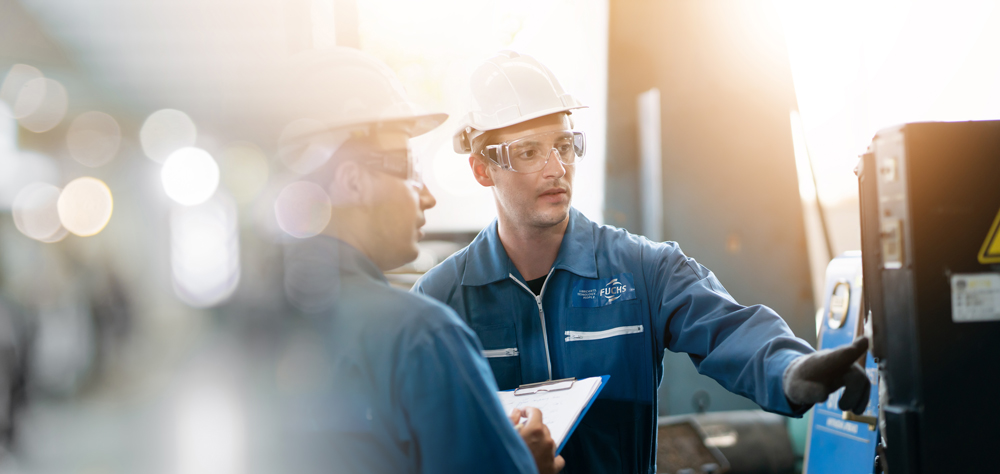
Training Overview
FUCHS Smart Services bring far more to the table than “just” a product. Instead, we combine performance fluids, digital technologies and a wide range of services into customized solutions.
One of those solutions is to equip your teams with lubrication knowledge, lubrication application and best practice. Training should be an integral part of any proactive maintenance plan.
To this end, we have pooled our expertise and experience from a wide range of application areas and industries to develop a lubrication programme to share with our customers.
FUCHS training packages can be tailored to meet the specific requirements of any manufacturing company or organisation, with the goal of increasing knowledge, reliability and efficiency.
Our goal: to keep our customers‘ world in motion. Efficient, sustainable, reliable. Today and tomorrow.
What can we move for you?
Who should attend?
FUCHS Smart Services can tailor the content to enable a wide range of attendees, ranging from apprentices, through to machine operators and experienced maintenance teams.
Why should you attend?
At FUCHS Smart Services, lubricants and lubrication solutions is our world. We develop and manufacture world class lubricants, and we want you to get the most out of what you use as part of your world. We can offer knowledge and know-how straight from the source.
Typical Courses
- Principles of Lubrication - an Introduction to Lubricants & Lubrication
- Metalworking Fluids & Best Practice
- Oil Analysis
- Lubrication Management
- Lubrication Storage
- Lubrication Best Practice
- Food Industry Lubricants & Compliance
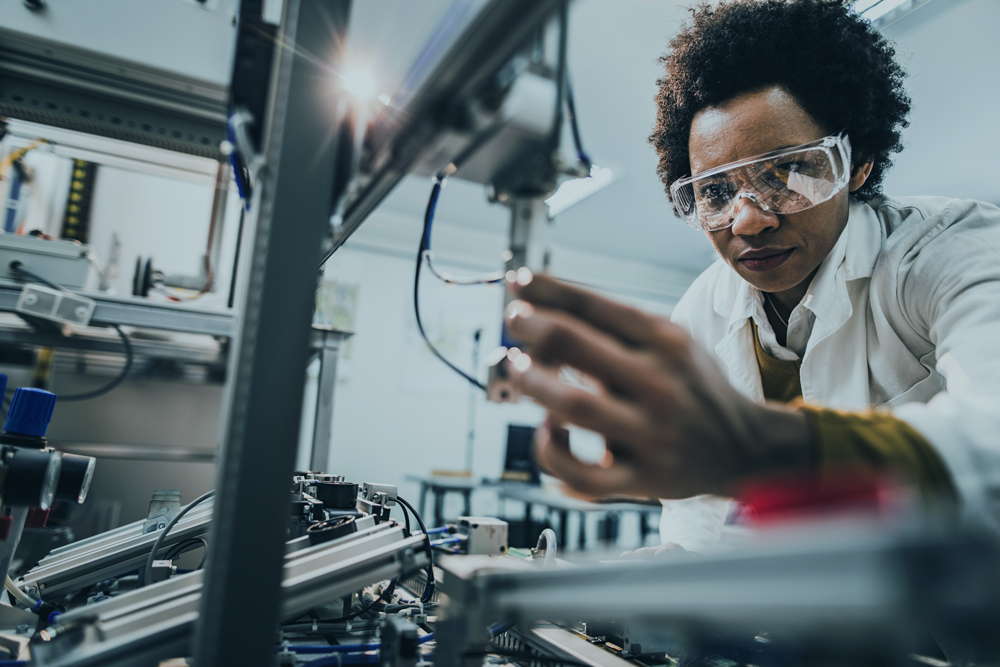
Product trials
At FUCHS Smart Services, MOVING YOUR WORLD means to constantly push forward. To strive for novel solutions that not only keep your machines running today but unfold the potentials of tomorrow.
Standing still is not an option, that is why we constantly strive to develop new lubricants using the best base oils and additive technology, to ensure optimum performance and energy saving potential.
We actively engage in product trails and aim to work in partnership with you to find the optimum products for your industry and applications.
Read more…
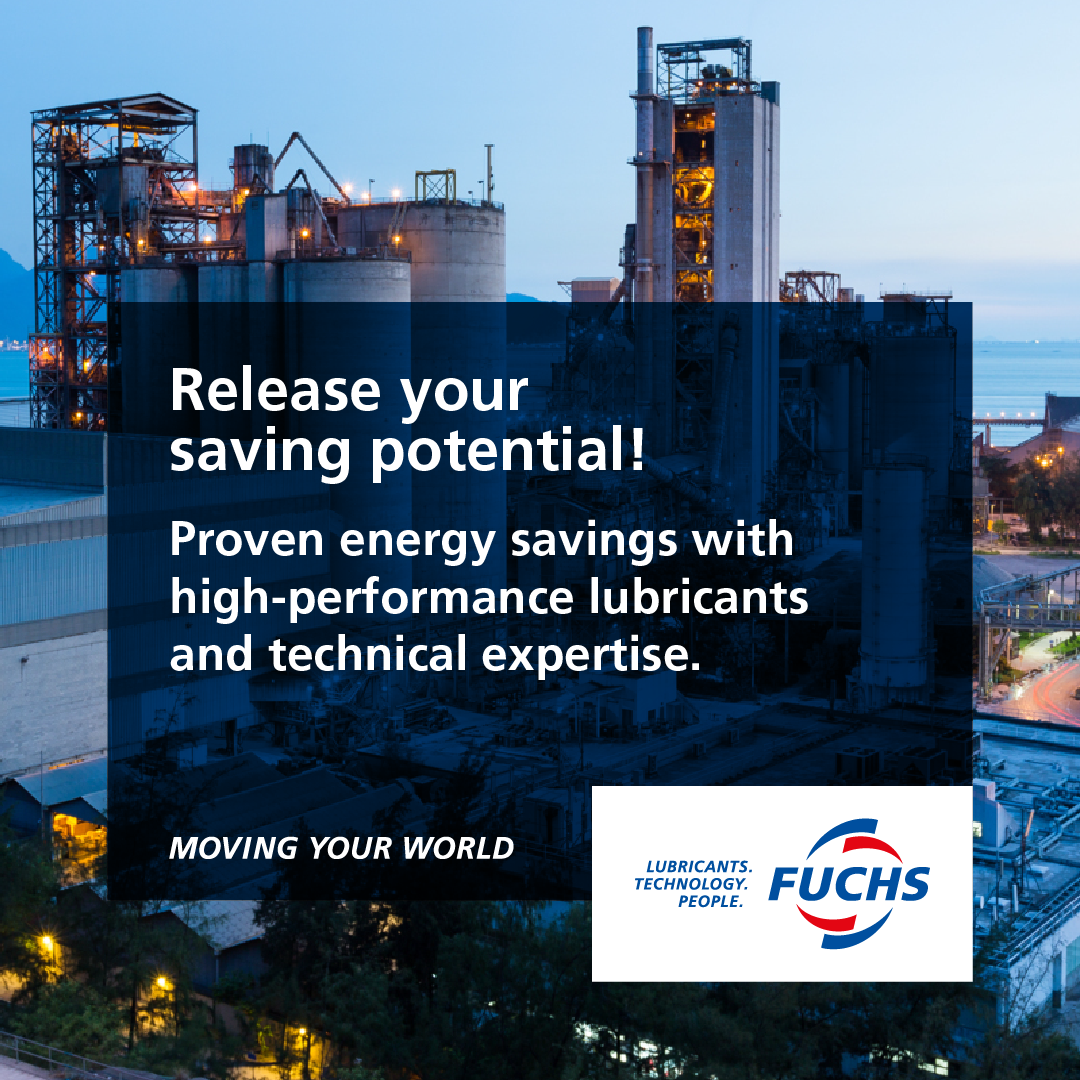
Release your saving potential!
Combat rising energy and fuel costs with proven high-performance lubricants from FUCHS. We can help you to select the best lubricants to reduce energy consumption and increase productivity.
With the latest sensor technology, we can help you to monitor your assets energy consumption in real-time. Once your energy consumption is established, suitable lubricants can then be selected and trialed to demonstrate potential savings.
We have demonstrated tangible savings in a number of industrial applications, from mobile plant to fixed production assets.
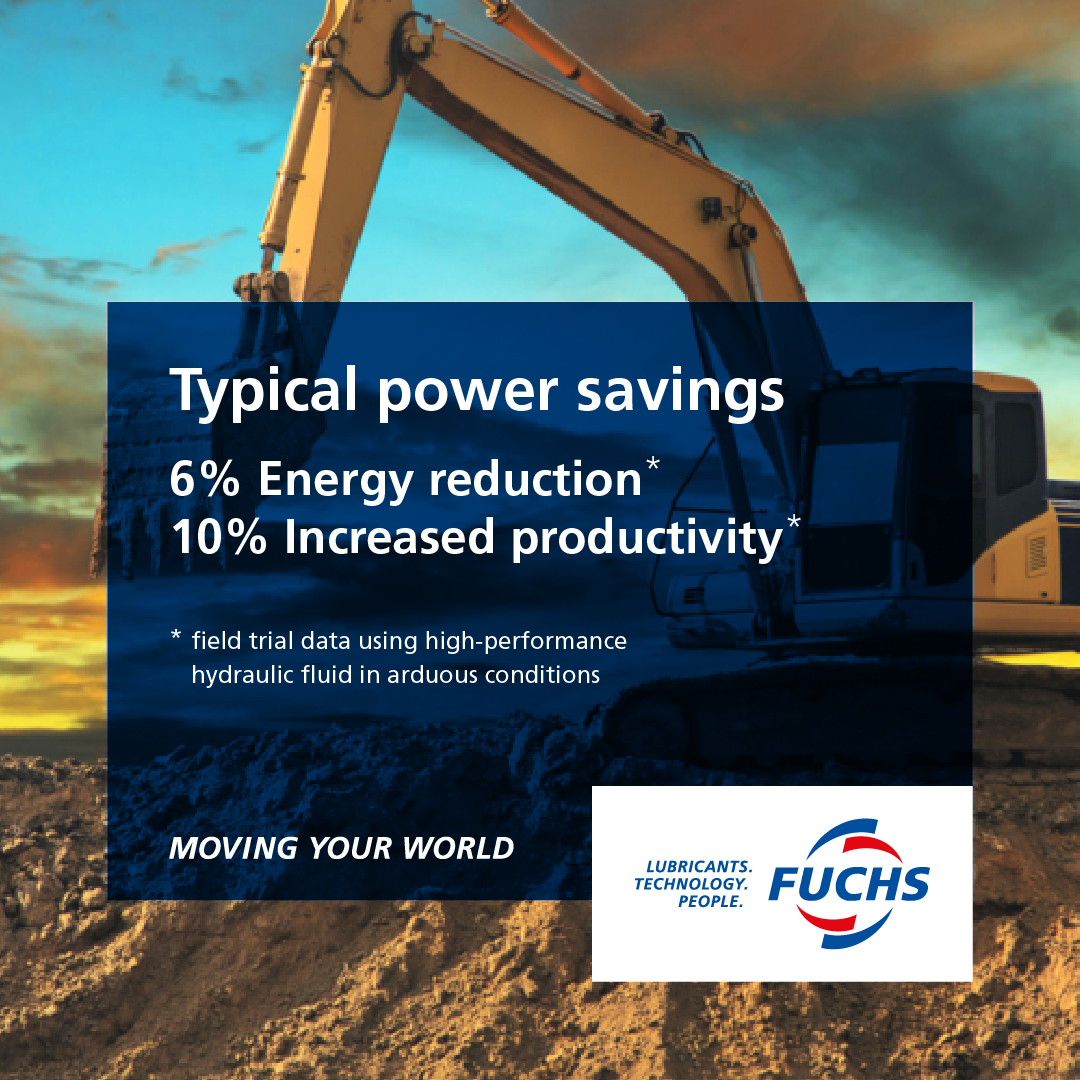
Read more...
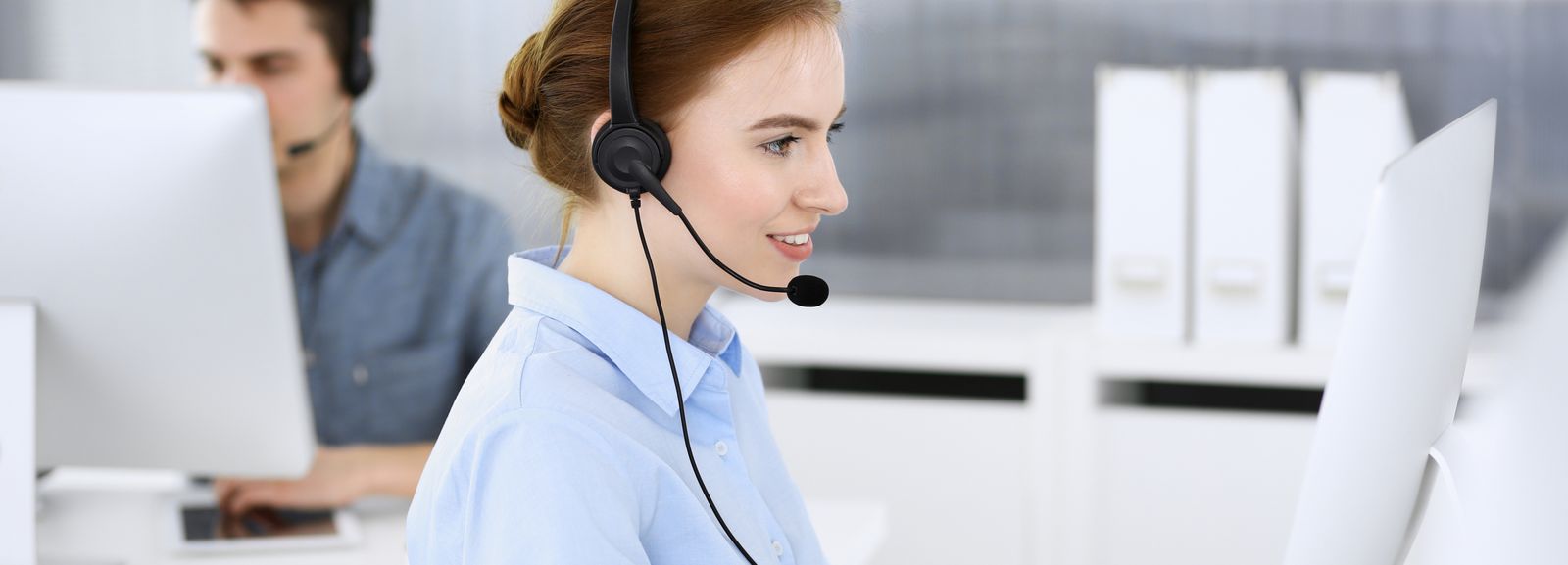
FUCHS LUBRICANTS (UK) plc has a wealth of knowledge and experience, from our laboratory technicians and office-based experts, to our field team who have first-hand experience of many lubrication systems and application.
As part of the FUCHS GROUP, we can also find answers through our global team or offer environmental specific solutions. Within the group, there are not many questions we haven't answered before!
Alongside our extensive product portfolio, we are proud to be a knowledge base in the lubricants industry and have been helping our customers develop their operations for many years through accurate product recommendations, efficiency updates and smart services.
Email: uktechnicalenquiries@fuchs.com
Emergency out-of-hours contact: Telephone: +44 (0) 1782 203 700
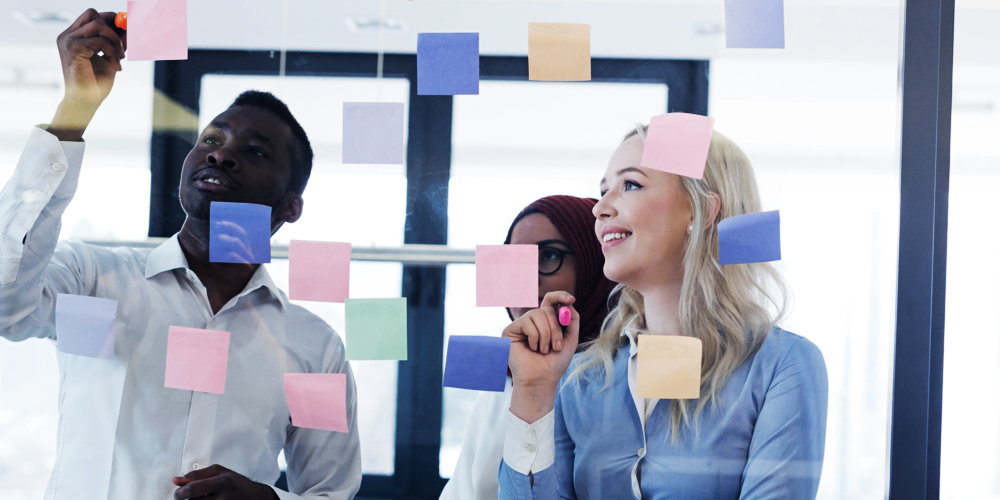
Let's assemble your solution
Start a partnership that will push your business forward.
FUCHS Smart Services
> smartservices@fuchs.com
What drives our process
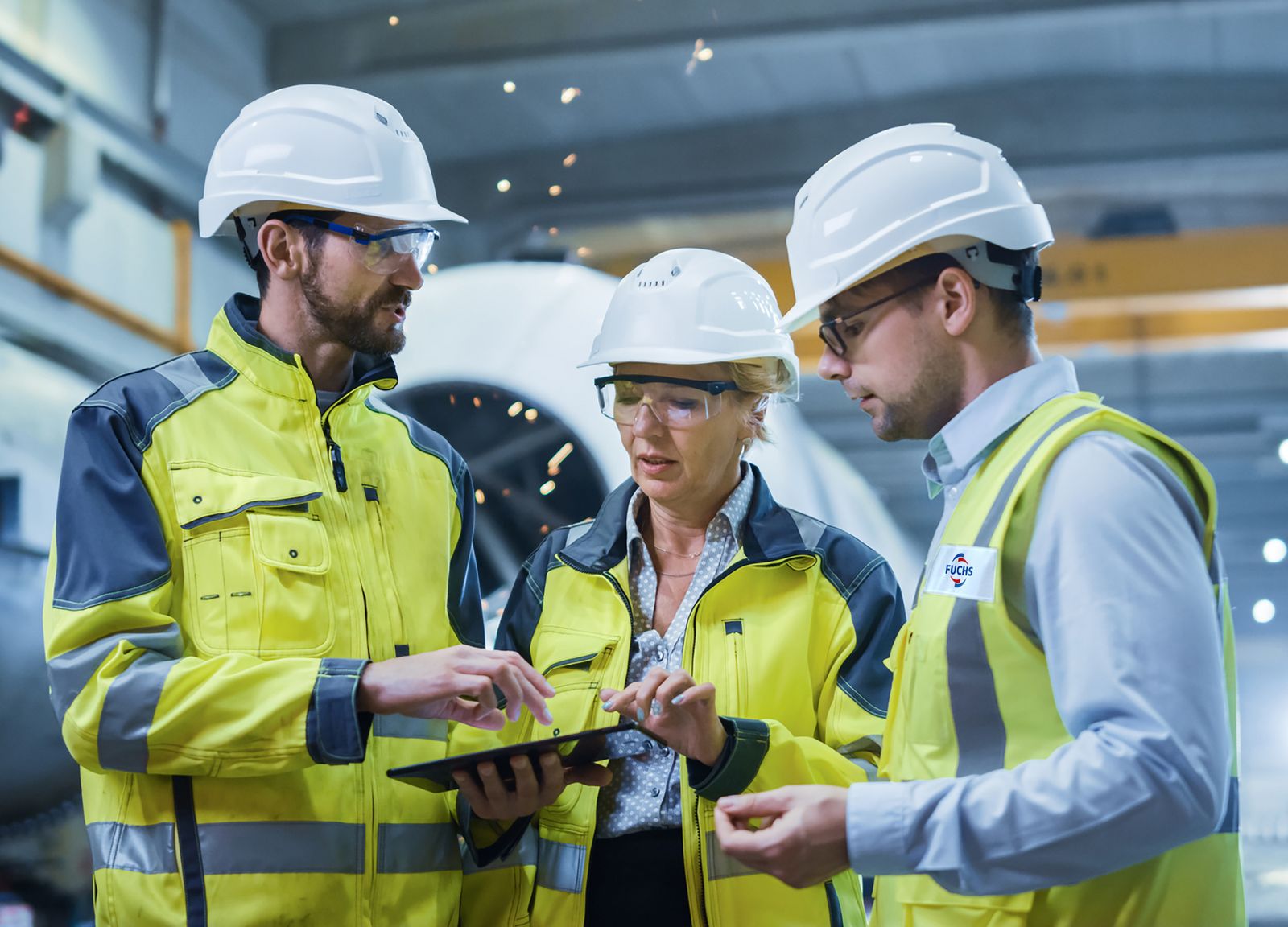
In order to move your world, we believe it‘s essential to become an integral part of it. Sharing not only data but also new ideas, technologies and processes. In turn, this allows us to integrate our expertise and tools into your business as well as your equipment. For example with experienced on-site technicians or remotely connected experts but also through ready-made sensor based solutions and sophisticated software for self-service. All to identify and prevent problems before they arise.
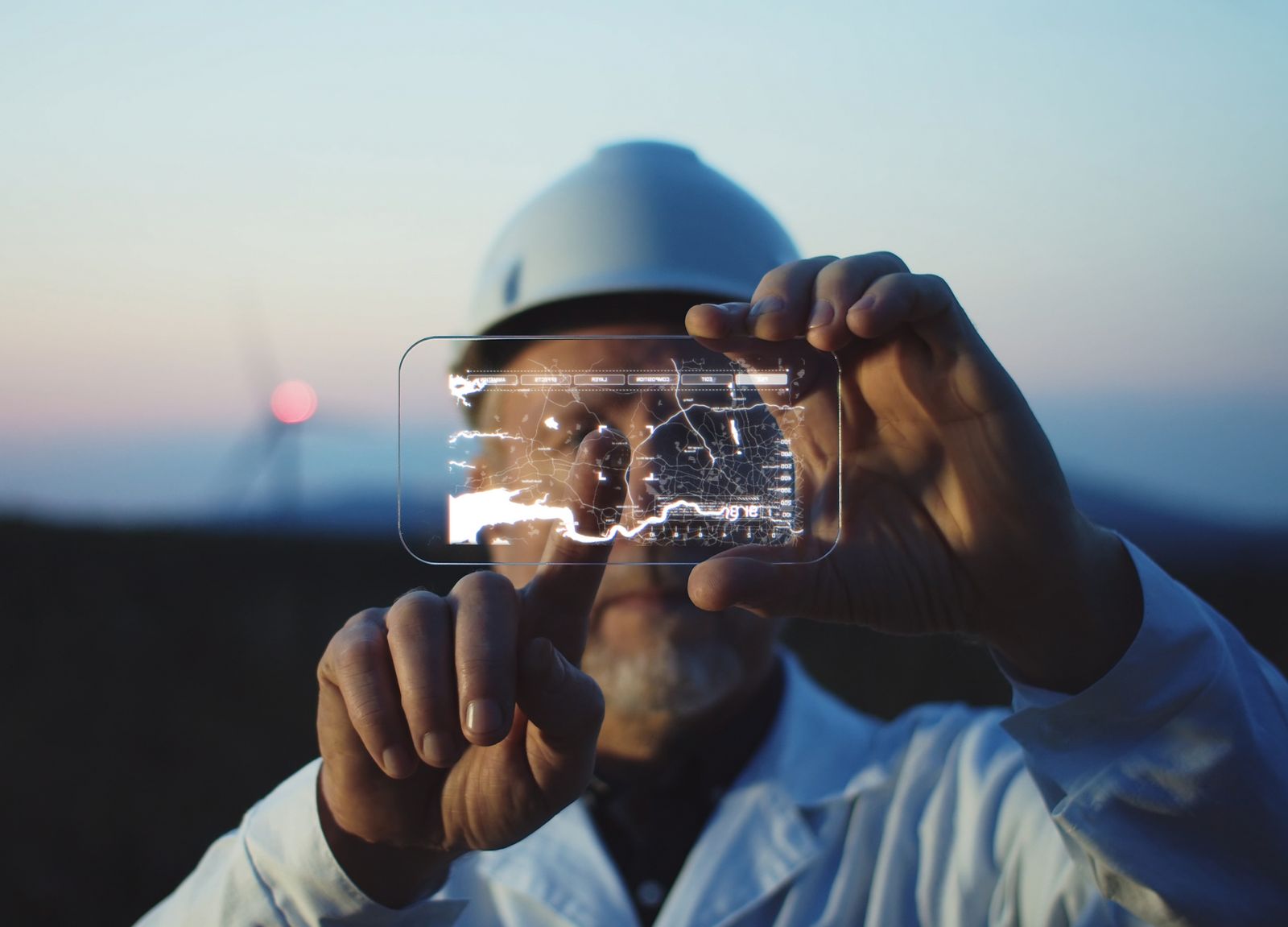
Transparency and insight are key to everything we do. Established with precise data and expert review, they allow us to identify untapped potentials – and work together more closely in order to achieve them – for example by monitoring the condition of products and machines or improving your processes.
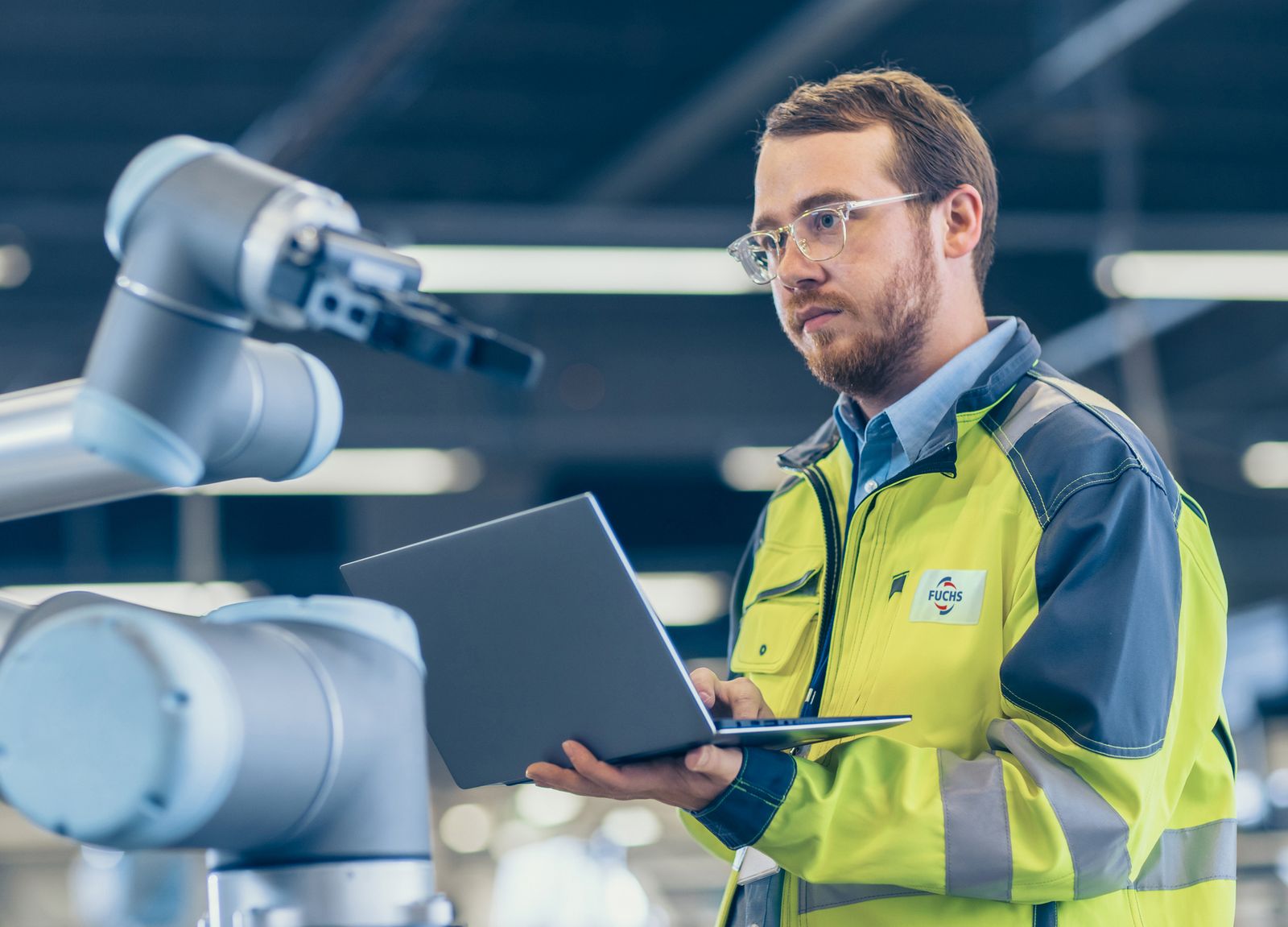
Maximum machine availability and minimized total cost of ownership are what we strive for. To achieve these goals, we leverage a solution-driven mindset and interdisciplinary expert knowledge along the entire lifecycle. An approach that enables us to take care of everything from air-leaks to zero-waste policies.
Digital solution
Information as a service
Data collection, integration and aggregation
Software as a service
Information access, visualization and analysis
Management as a service
Remote service and on-site management support