Advanced Lubrication Validation Testing for Vacuum Applications
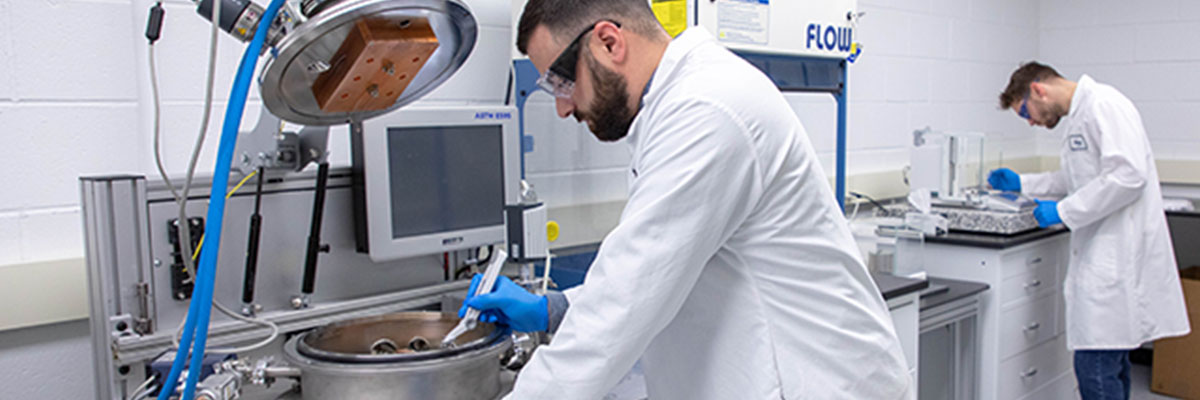
Measure twice, cut once. This old proverb often echoes in our minds before cutting an expensive piece of material. In the high-risk world of aerospace engineering, this double-check mentality is critical because once a spacecraft is launched, it is often impossible to repair failed components. With fabrication precision is now down to sub-10-nanometer level for many processes and even the smallest contaminants causing product defects and yield loss, semiconductor manufacturers are similarly risk adverse. Unplanned downtime in the semiconductor industry can cost millions of dollars, while spacecraft failures can jeopardize multi-billion-dollar missions.
While lubricants are often used to protect against wear related failures, a lubricant ill-suited to vacuum conditions can outgas and contaminate your system. In these high-stakes industries, it is critical to validate every system component, including the smallest amount of lubricant. For these reasons, a lubricant must be tested in a vacuum environment under specific temperatures, speeds, stress, and loads to understand how it will interact with a design.
Our Cutting-Edge Test Facility
As a leader in aerospace and semiconductor lubrication, FUCHS has dedicated itself to developing state-of-the-art facilities with the most advanced test equipment in the industry. Our one-of-a-kind test apparatuses designed and built by FUCHS engineers, along with other state-of-the-art test rigs, expose lubricants and components to extreme test conditions that replicate the challenges of aerospace and semiconductor manufacturing environments.
In-vacuum testing is inherently challenging, as testing mechanisms are extremely sensitive to factors like vibration and static. For example, something as small as static discharge from a person’s body can skew test results. The lab was designed specifically to minimize noise, foot traffic, and static, with features like wall-to-wall Electro-Static Discharge flooring, laminar flow sample prep hoods, and 6- and 7-digit microbalances for precise sample measurement.
Testing Capabilities
Here are some of the testing capabilities offered in the new VAST Lab:
Friction & Wear
- SRV Tribometer
- The SRV (Oscillating, Friction & Wear) test rig can run custom tests with options that include rotational and linear oscillatory motion, tests up to 2,000 N load, 2,000 RPM, and a maximum temperature of 180 °C. Specimens include ball on disc, pin on disc, cylinder on disc, and custom geometries.
- Mini Traction Machine (MTM)
- The Mini Traction Machine measures friction in a mixture of rolling/sliding contacts to simulate applications like rolling element bearings and gears. The MTM allows for the speed element to be a combination of sliding and rolling speed to produce the entrainment speed. The MTM provides a very good testing method for scuffing and galling of metal surfaces by allowing for the ball and disc to be driven in different directions (contrarotation). This produces a tribological test that can operate with high sliding / rolling speeds and low entrainment speed.
Relative Life
- Spiral Orbit Tribometer
- Originally developed by NASA, the Spiral Orbit Tribometer (SOT) produces relative lifetime calculations based on the number of orbits made below a friction level which is normalized to the amount of lubricant on the ball bearing. The testing is done in ultra-high vacuum and simulates a thrust bearing. The results indicate lubricant consumption, degradation, and life.
- Vacuum Bearing Test Rig
- Data from the Vacuum Bearing Test rig can determine the life expectancy of our lubricants on angular contact bearings in high vacuum environments. This rig can support customer supplied bearings to simulate how a lubricant will perform in a specific application. Our high vacuum test can assess performance at temperatures up to 200 °C and determine mass loss under specific operating conditions. The rig also uses electrical resistance across the bearing to determine which lubrication regime (boundary, mixed or elasto-hydrodynamic) our products qualify under, given the test parameters.
Cleanliness
- Particle Generation
- The Dynamic Particle Generator is used to classify lubricant particle generation into ISO and Federal cleanliness levels. It utilizes an ISO 3 clean air system, precision ball screw, and particle counter to characterize the number of particles down to 0.1 micron produced by various greases as the test is run.
- Outgassing
- Outgassing testing (per ASTM E595 Vacuum Stability) screens materials for volatile contamination. This test provides percent Total Mass Loss (TML) and percent Collected Volatile Condensable Materials (CVCM) data for our lubricants. Residual Gas Analysis can be used to determine the elemental species contained in the outgassing material. This testing provides customers with an understanding of the stability of our materials in a static vacuum environment and identifies which materials are outgassing.
- Vapor Pressure
- The Knudsen method is used to determine a lubricant’s vapor pressure (VP) and requires a small sample, reducing testing costs and efficiency. The sample is placed in a small, capped cell with an orifice in the cap of known diameter. The cell is then placed in one of the vacuum chambers, at a desired temperature and duration. The mass loss from the lubricant is factored into the Knudsen equation, along with the other known variables of temperature and time, to calculate the Knudsen VP of that material at that temperature.