E-Mobility Roundtable – How FUCHS is Preparing for Future Mobility Challenges
We sat down with three of our lubrication experts to ask them how FUCHS is responding to the ever-changing electric vehicle landscape with solutions for manufacturing, metalworking, and components.
How do the manufacturing requirements differ for electric vehicles compared to traditional gas-powered cars? How has FUCHS adapted to provide lubricants that are required during these processes?
The advancement of electric and hybrid transportation has provided many manufacturing opportunities and challenges, all of which influence the formulation, as well as how the lubricants, cleaners, and related fluids are used and maintained.
In metal forming the need for lighter but stronger parts equates to challenges with new alloys and also a higher degree of difficulty in drawing and stamping operations. The demand for products that perform at higher loads and friction while also considering improvements in cost, substrate compatibility, regulatory issues, sustainability, and improved work environments means that FUCHS is investing even more in R&D, diversity of our portfolio, partnerships with our suppliers, and working more closely than ever with our customers. Metal cutting, cleaning, corrosion protection, and lubrication of production and handling equipment are all similarly affected.
At FUCHS, we are confident that the ultimate support we can provide to our existing and future customers is to stay close to all of these changes in substrates and applications. We continue to sharpen our focus further to provide solutions that are comprehensive with regard to innovative, sustainable, and cost-efficient products and services. We are working hard each day to unlock value by better understanding our customers’ challenges and by providing and maintaining optimum lubricant technology.
We do all of this on a local, regional, and global basis that provides first choice knowledge and technology from the hundreds of scientists, engineers, and field personnel that make us the market leader for future mobility.
"We are working hard each day to unlock value by better understanding our customers’ challenges and by providing and maintaining optimum lubricant technology."
- Troy Prasek | Director- Key Accounts & Business Development
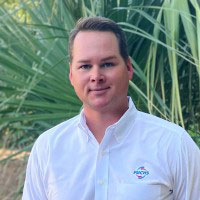
What materials are being used to develop electric vehicles and their batteries? What challenges come along with this and how can FUCHS solutions help?
First, materials being used to develop electric vehicles (EV) and their batteries have less to do with electrical power than they do with a continued focus on light-weighting. Aluminum is a key material due to its light weight, durability, and infinite recyclability. Even before EV’s were manufactured, there was a push to use aluminum to meet mile per gallon minimum requirements under The Corporate Average Fuel Economy (C.A.F.E.) standards. The aluminum industry worked hard to develop stronger alloys that could be used in vehicle components, body panel formation, and battery housings. Lastly, there is more demand for aluminum wire which is used in recharging stations. On a smaller but still significant scale, higher alloy, thinner gauge steel has been developed to provide similar benefits to aluminum. Additional metals including increased magnesium content and copper use in batteries and windings have also become more of a consideration. All these metals provide their own challenges when it comes to forming the final parts.
How can FUCHS help? To understand this, we really need to understand how each metal reacts with the additives in the forming fluid and flows through the forming processes.
Aluminum is a very soft and gummy metal. It does not interact with traditional extreme pressure (EP) additives such as phosphorus, sulfur, and chlorine like traditional ferrous metals do. Therefore, we had to take a different approach when designing forming lubricants for aluminum in general and even more so when moving to the severe forming conditions for body panels, structural parts, and battery housings and trays. Body panels are big, very detailed, and have a tendency for edge cracking. Battery housings are a difficult deep draw and require very straight sides. Forming these parts puts a considerable strain on the fluid, especially when traditional chemistries are ineffective. With much innovation and research, FUCHS has identified the key to making parts with aluminum is the use of innovative polar additives and base-stocks. These fluids have a strong affinity to the surface of the aluminum to provide boundary lubrication during forming operations. Hot and warm forming of aluminum can increase formability by 20% – 80% by improving the flowability of the metal during the process. This presents a challenge for the lubricant as well, considering some natural sources for polar base-stocks are not stable at elevated temperatures. At FUCHS, we've used careful selection and testing of these base-stocks to select ones that perform under these conditions as well as inclusion of additives to help improve thermal stability. Magnesium and copper metals are similar to aluminum in their formability and tendency to get draggy or gummy, therefore they require very similar fluid solutions as mentioned above.
At FUCHS we have always provided metal forming fluids that dominate the market. Our focus is sharpening further to stay just as dominant with our innovation while increasing the sustainability of our products – all while providing lubrication and service solutions to allow our customers to achieve their goals with ever-increasing challenges in the metals they use, and the constant need for efficient processes and cost control. We are moving the world of metal forming.
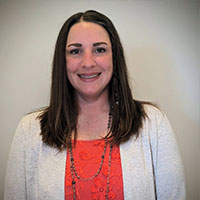
"Our focus is sharpening further to stay just as dominant with our innovation while increasing the sustainability of our products. We are moving the world of metal forming."
- Jenn Lunn | Product Manager, Metal Forming Lubricants
What kind of challenges does electrification pose for automotive components? How can specialty lubrication solutions help address these challenges?
Electrification does present challenges for automotive components, and many times, lubricants can offer solutions. A traditional internal combustion engine typically creates more noise and vibration than an electrical drivetrain. With less noise and vibration being masked by the engine, other less quiet parts of a vehicle become more noticeable. Not only can the proper lubricant significantly dampen these noises, but the correct grease can also impart an important tactile feel element to components that is directly perceived by the consumer as ‘high value’.
We are still in the infancy of electric vehicles, and getting the range needed to prevent loss of power during a long trip still exists, especially if a full recharge takes hours to achieve. Choosing the proper grease or oil for an application will prevent unnecessary power draw due to inefficient churning losses and shear when actuating a component, while still providing the needed wear prevention. This is even more critically important at low temperatures when lubricant viscosities naturally increase, and vehicle batteries struggle to maintain and deliver the same power density as during milder temperature days.
Passenger cars, and especially electric vehicles, are incorporating greater and greater numbers of connectors to support various componentry such as new features, control systems, sensors, and actuators. Many of these are safety critical, and even more so as we move to fully autonomous vehicles, these circuit pathways cannot fail. They must be robust and resist fretting wear and corrosion, failure modes that are all too common on separable connectors that do not incorporate a connector grease.
Lubricants are critical in the overall functioning of a component, and engaging with lubricant professionals early in the design process will save money, create better overall part quality, and increase end customer satisfaction.
"Lubricants are critical in the overall functioning of a component, and engaging with lubricant professionals early in the design process will save money, create better overall part quality, and increase end customer satisfaction"
- Erik Reis | Director of Business Development, OEM
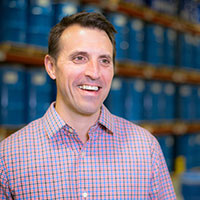