How Grease is Supporting the Next-Generation of Connector Design
Autonomous vehicles will make hundreds of decisions per minute. Wearable medical devices will monitor patient care and give doctors insights that would have been unthinkable even 50 years ago. Data center capacity is expected to triple in the next six years to support the rise of artificial intelligence.
Innovation often means more. More power. More performance. More efficiency. Every aspect of a design must work together in harmony to achieve these goals. This is applicable not only on the system level but also down to the component and material level. Within electric systems, like in the applications mentioned above, connector design has become increasingly complex to support advanced and emerging technologies.
Connectors are now expected to be smaller and more durable all while offering faster data rates and higher power transfer. HDMI, FAKRA, micro USB and USB connections are just some of the small but mighty connector types that are making their way into a range of designs.
The goals connector manufacturers set out to achieve, however, can often be at odds with one another and the design of the connector itself is often not enough to ensure reliable performance. For example, higher voltage designs pose several engineering challenges including higher temperatures and higher rates of corrosion on the connectors, thus impacting reliability. So how can you get the best of both worlds? Connector grease.
CONNECTOR GREASE TO THE RESCUE
Whether your connector is going to go into e-mobility, construction, mining, heavy duty trucking, medical, power tools, appliances, consumer electronics, or any of the other numerous application areas connectors are found, grease can help add a layer of protection to ensure you meet your design goals without sacrificing reliability. Connector grease has four primary benefits.
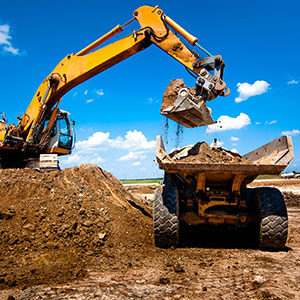
Prevents Corrosion
Think about all the dust and debris that mining and construction equipment are exposed to, or, consider heavy-duty trucks exposed to road spray and salts. These are just a few examples of highly corrosive environments that can negatively impact connector performance.
When a contact corrodes, insulative oxides form on the terminal surface which results in increased resistance, signal loss and component failure. The corrosion can also be conductive and builds up to a point where it bridges the distance between two terminals and creates a short circuit
Even with specially designed housings, there is a risk that dust, dirt, or another form of debris could find its way to the contact pin. When this happens, it can interfere with conductivity and lead to an incomplete connection. Harsh chemicals can also corrode the metal surface and eat away at the pin’s metal plating.
Grease creates an environmental barrier to keep dirt and debris away from the contact surface. PFPE lubricants are recommended to offer protection in the presence of harsh chemicals.
Keeps Out Moisture
Every day we rely on dishwashers, washing machines, and other household appliances to make our lives easier. Unfortunately, thermal-related appliance recalls do occur and connectors can often be at fault. Moisture can corrode the terminal surface over time or even cause an instantaneous short circuit. Moisture can take the form of water, detergents, humidity, or salt spray.
Connector grease repels water from the connector surface. Our connector grease is hydrophobic, meaning it stays in place rather than being washed away over time. Grease also prevents current leakage in conductive environments, such as water, to ensure consistent connectivity. A connector grease can also create a seal for the connector to prevent water ingress at the housing interface.
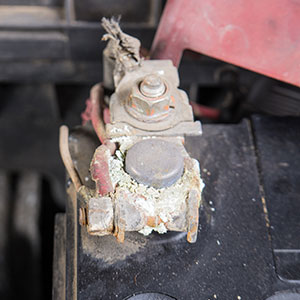
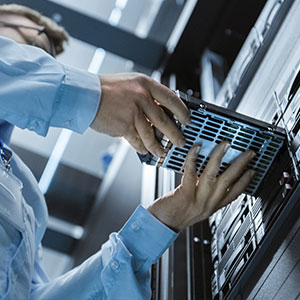
Protects Against Fretting Corrosion
Fretting corrosion is the result of micromotion caused by vibration and/or thermal expansion due to heating or cooling cycles. These micromovements wear As this oxide layer builds up and increases, the oxide film acts as an insulator between the contacts. This creates an open circuit resulting in voltage drop across the terminal and ultimately, power failure or signal loss.
Even engineers designing connectors used within stationary applications, like data centers or consumer electronics, must consider the effects of fretting corrosion. Grease reduces physical wear between the connecting surfaces as they undergo micromotions and fretting wear. This preserves the plating on the connectors, designed to prevent oxidation and minimize resistance.
Grease also protects the system from the surrounding environment, preventing the build-up of insulative oxide layers which are ultimately responsible for resistance increase and signal loss.
Reduces Mating Force
The battery pack on your cordless drill and the charging port of your electric vehicle are two examples of connectors that are subject to frequent remating. Increased mating force can cause misalignment during assembly and lead to an incomplete connection or damage to terminals.
Increased mating force can cause misalignment and/or wear at the metal plating. For multi-pin connectors, mating forces increase significantly which can create ergonomic and safety issues during assembly. A thin film of lubricant reduces friction to ease mating force by as much as 80 percent.
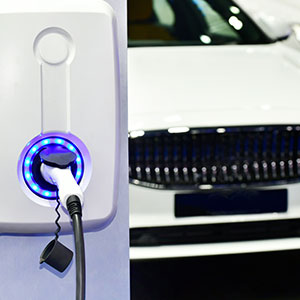
CONNECTOR GREASE IN ACTION: PROTECTING MEDICAL DEVICES AGAINST CORROSION
In order for connectors to do their job, they need to be properly protected. In hostile environments, like medical devices for example, this becomes more challenging as they can be exposed to cleaning agents and sterilization cycles that can accelerate corrosion. There is also the added complexity of ensuring all materials are biocompatible. This was the challenge presented to FUCHS by a leading fertility company that was experiencing early failure of their handheld diagnostic imaging device due to corrosion on their micro HDMI connector.
FUCHS was able to provide the customer with a sample of NYEMED® 7560, a biocompatible version of our industry standard connector lubricant, for internal performance testing and ETO exposure. FUCHS then provided a lab evaluation to verify that the integrity of the product was uncompromised. NYEMED® 7560 met all of the customer’s test requirements, protected the connectors against corrosion thus extending the life of the device, and remained stable following terminal sterilization conditions
NYOGEL 760G, the Industry Standard Connector Grease
Achieve your design goals without sacrificing reliability. NYOGEL 760G is the leading connector grease specified by leading OEMs across many industries to prevent common causes of electrical failure. Watch our video to learn more or, request a sample.