How to keep your parts in good condition with In-Process Corrosion Protection - Part 1 of 2-
It’s often necessary to store parts between manufacturing operations and prior to assembly. Protecting parts from corrosion during storage is critical to maintaining process integrity and avoiding costly rework or scrap. In this 2 part series we discuss how to protect metal parts between manufacturing operations and assembly.
What is the storage protection period?
Let’s look at storage periods and the common options for each under indoor storage conditions:
Up to 3 months protection period
In many cases, residual metal cutting fluid or forming compounds from upstream operations may suffice as the protective medium if parts are to be stored only during weekends or relatively short periods of downtime. The caveats for use of these fluids as corrosion protectants are partly based on composition:
- Chlorinated lubricants may not protect as well as chlorine-free materials
- Low operating concentration of water mixable lubricants may not provide sufficient protection
- Contamination of the fluid, and consequently the residual film with dirt or biological growth may render it unsuitable for protection
The lubricant supplier should be able to advise on applicability of their product based on its chemistry and your plant’s process and lube maintenance practices. If residual lubricant is not suitable, parts must be cleaned prior to storage.
In a single stage spray or soak cleaning system, a well-chosen cleaner may be suitable for short term protection if the cleaning solution is consistently filtered or otherwise maintained in a dirt and oil free condition. FUCHS US water based solutions include RENOCLEAN 102 LK 6, RENOCLEAN 6513 RP, and RENOCLEAN 9009, among others.
RENOCLEAN OL 5 MS is a good oil based dual cleaning / corrosion protection option.
Two stage cleaning systems provide additional options. The simplest is to use the same material for both cleaning and corrosion protection, where Stage 1 does the cleaning and accumulates the dirt and oil load, and Stage 2 stays relatively clean and provides the protective film. Alternatively, Stage 1 contains the cleaning solution, and Stage 2 contains a water based corrosion protection that leaves a nearly imperceptible protective film such as synthetic oil free fluid ANTICORIT AQ 1961 or light oil film emulsion fluids such as ANTICORIT OS 5200.
Light duty solvent or oil based corrosion protectants may be used but are not common for short term storage. While more effective as protectants, they are also generally higher cost options compared to water based products.
Regardless of the chosen product type for protection, parts must be clean at time of application, and thoroughly dry before storage. Residual dirt or contaminating oil will interrupt the protective film, and wet parts will aggressively drive corrosion reactions.
3 months to 12 months protection period
Water based products may be an option for the shorter end of this storage period range, provided the storage environment is near optimal.
In many cases, a chemical barrier tightly adhered to the metal surface, carried by mineral oil or solvent, is necessary. These products are usually solvent or light viscosity mineral oil in the range of 105°F to 350°F flash point as a carrier for the active chemistry. Hence, the categories for these products: solvent based and oil based corrosion preventives.
While most of these products contained surface active chemistry for protection, older generation products are also reliant on a physical film of oil for protection. While effective, the oil film is also problematic due to dripping and for making parts slippery to handle, and creating a high contaminating oil load for subsequent cleaning operations.
Modern fluids such as the ANTICORIT DFO range are optimized for high reliance on chemical surface protection and very low oil content. Parts coated with these products are easy to handle, avert housekeeping issues, and place only light loads on subsequent cleaning operations, without compromising protection.
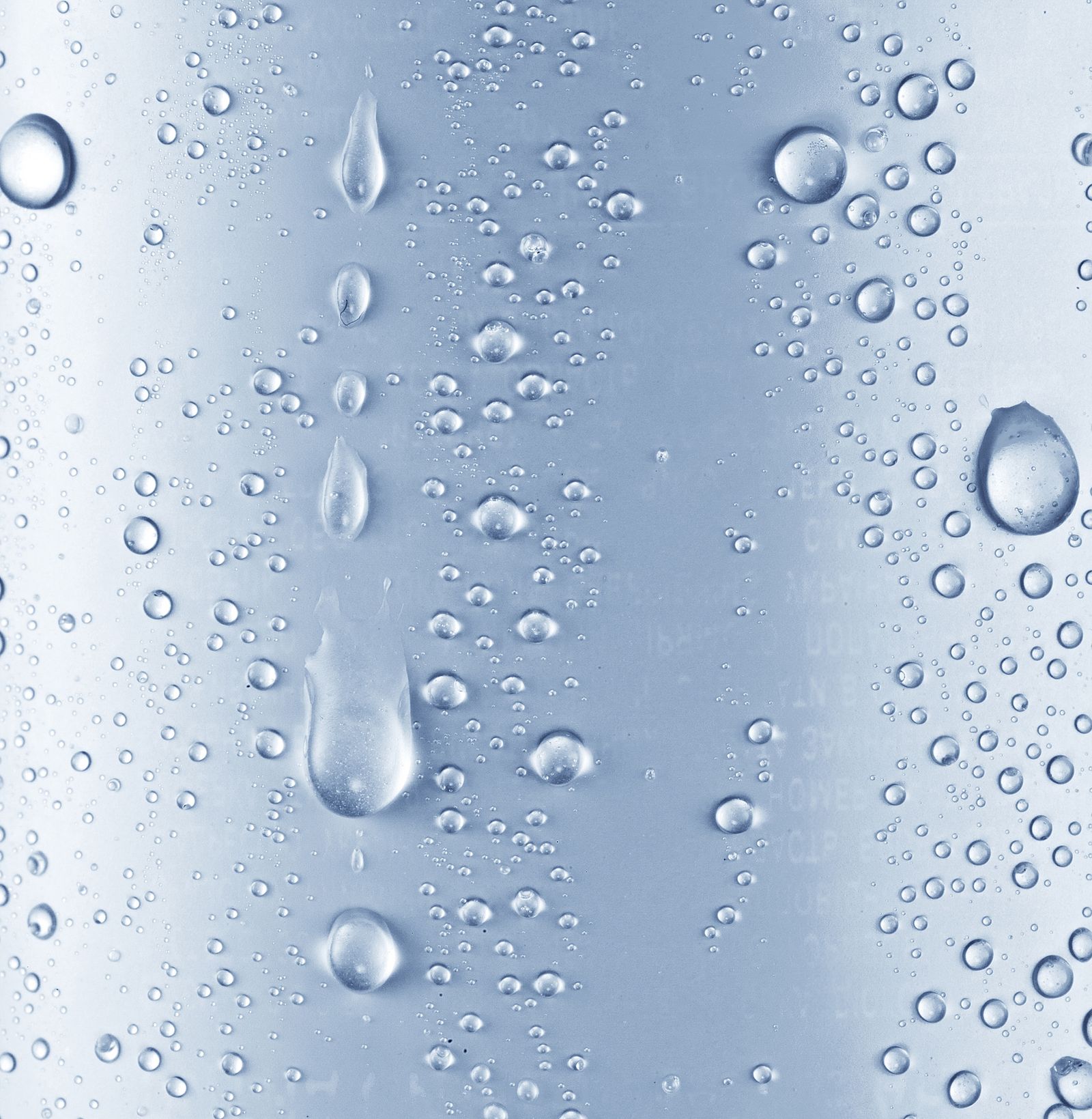
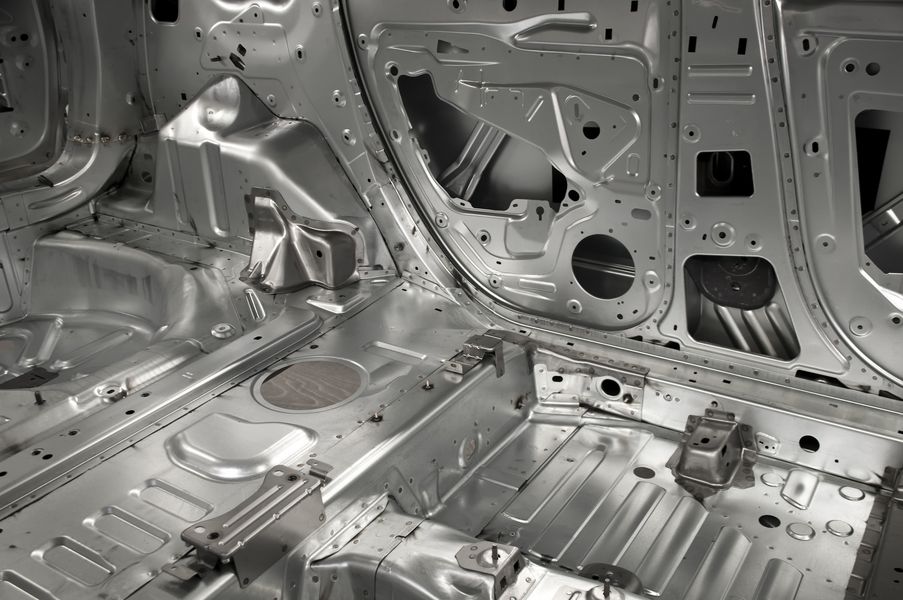
Longer than 12 months protection period
Extended protection can be imparted by oil based or solvent based fluids up to 2 years or longer under near optimal conditions. Often, oils containing vapor phase protectants, such as ANTICORIT OL 7616 or ANTICORIT BGI 21 US may be used to impart additional corrosion protection to parts in packaging such as plastic wrapping that totally seals the parts from the external environment. These oils often provide the necessary protection that otherwise would be imparted by costly VCI paper or VCI bags, at lower cost and at reduced packaging process complexity.
Wax films as provided by ANTICORIT SV 7 X are also an option for long indoor storage periods. These materials use surface active chemistries for protection, coupled with a waxy film that provides a stronger physical barrier than do oil films.
Next week we will be publishing part 2 of this series to discuss storage conditions and subsequent processing. Your FUCHS representative can assist with selection considering all of your unique requirements. Feel free to contact us at any time.
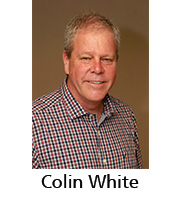
Subscribe to our blog
All Blog Posts
- Lubricants & Technology – SOLCENIC Success
- What you need to know about Food Safety Modernization Act (FSMA) and Lubrication
- Part 2 - How to keep your parts in good condition with In-Process Corrosion Protection
- How to keep your parts in good condition with In-Process Corrosion Protection
- Four rules of thumb in lubrication – your shortcut to savings!
- A gaze into the world of cutting fluids
- When lubricants ‘get chatty’
- Did you know…? About hydraulic fluids
- Did you know…? About vehicle lubrication
- The rapidly evolving automotive industry
- Higher productivity and profitability in four stages
- Ten tips that deliver big time