Cement
All your needs covered. Your lubricants and solutions for all applications.
To meet the harsh demands of the cement industry, you need a lubrication partner with the expertise and in-depth knowledge required to support you throughout the manufacturing process and beyond. A partner that provides the full range of lubricants and solutions for all cement plant applications – around the globe. Highly dedicated and skilled experts that are always there for you whenever you need them. A wide range of services to ensure the performance, efficiency and process reliability of your equipment. You can focus on what you do best – manufacturing cement.
FUCHS - Your full-solution lubrication partner in the cement industry
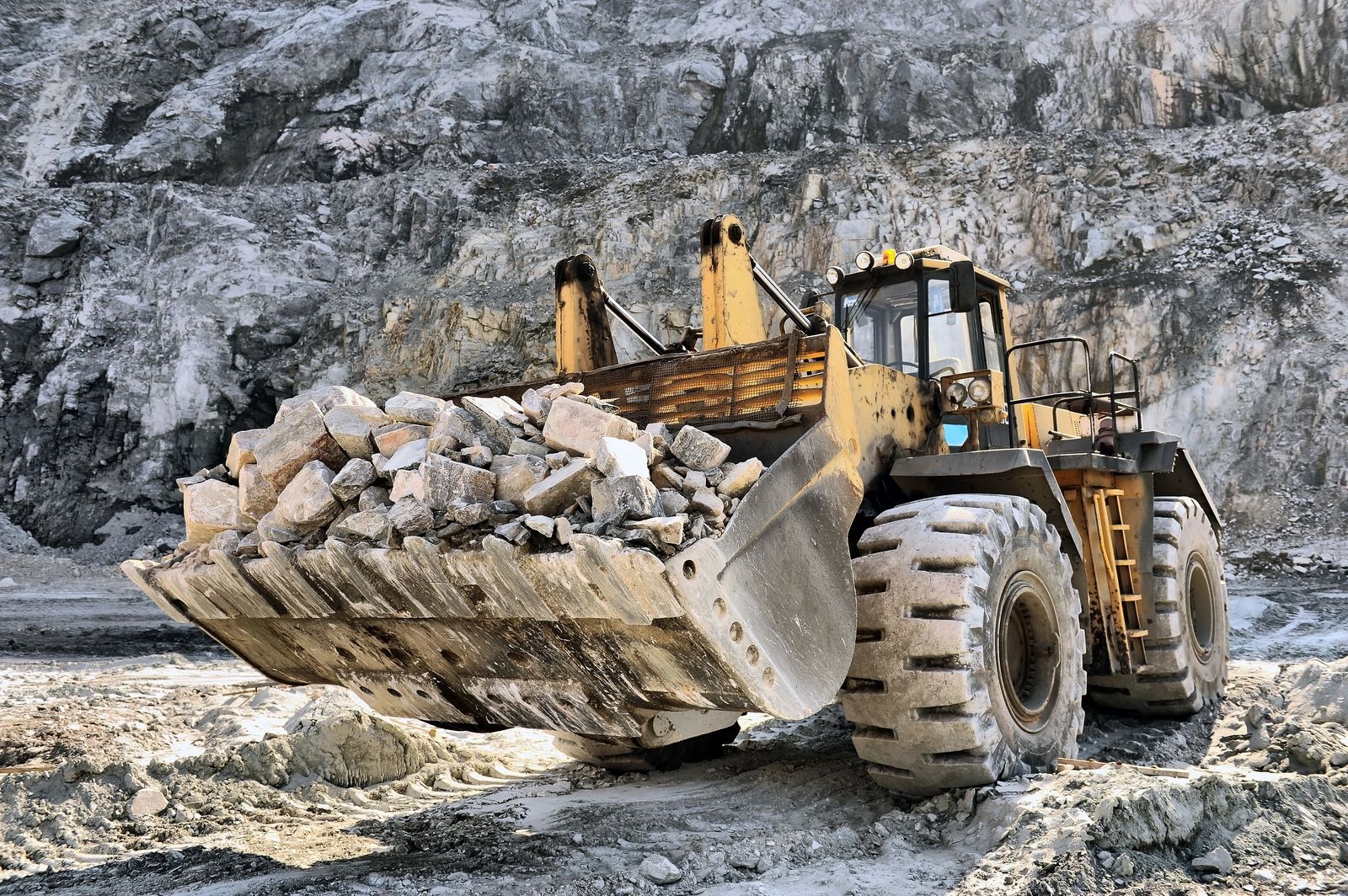
The whole range of lubricants
Whether your applications involve the lubrication of crushers, mills, grinding rollers, kilns or excavators, FUCHS is the strong and reliable partner for you, providing solutions for all requirements of the cement industry - including all relevant approvals.
We want your machines to perform at high-level – every day. With FUCHS, you can enjoy the full range of high-performance lubricants from a single source – and your plant will also benefit from higher efficiency and productivity.
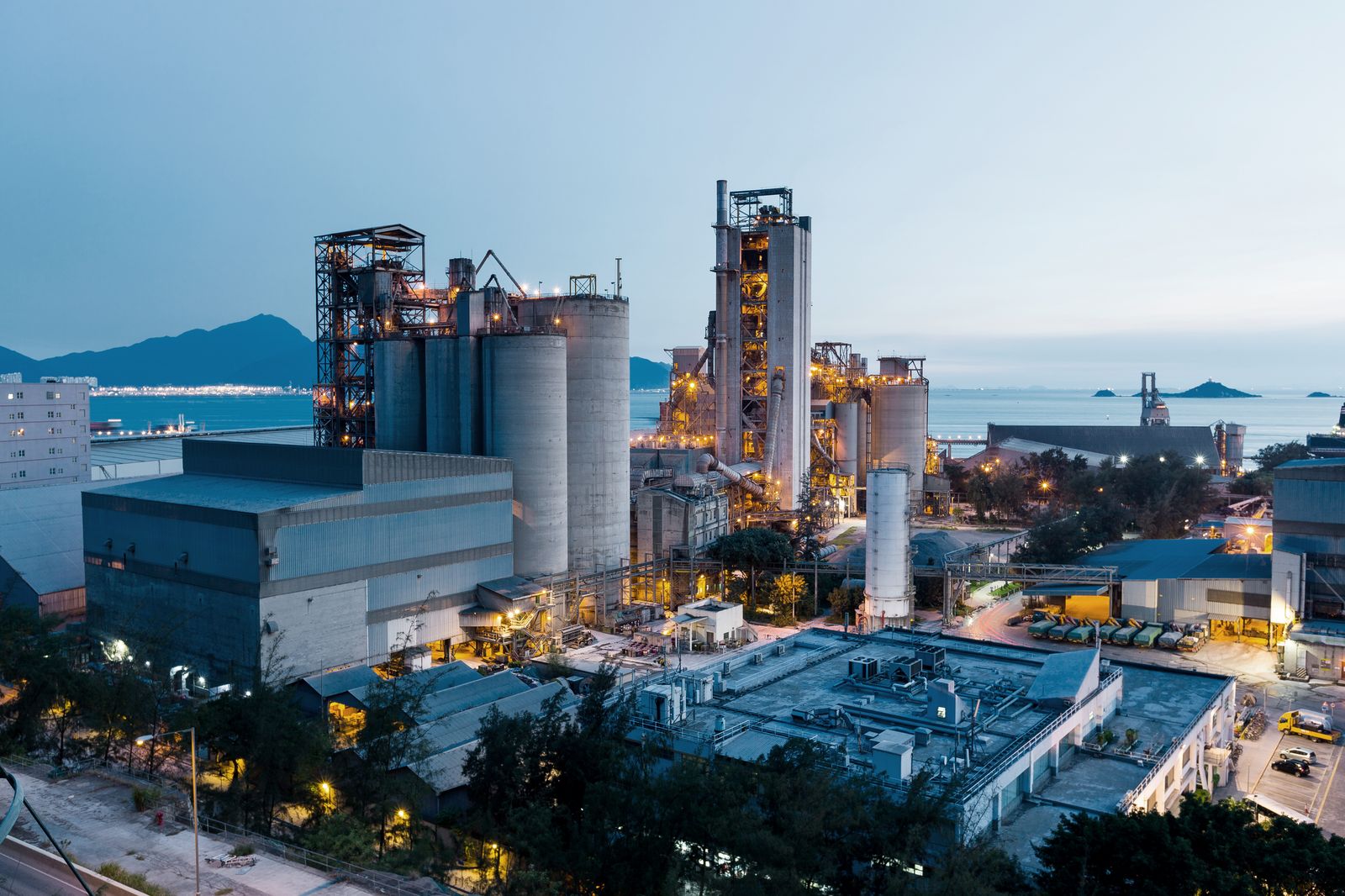
The whole world of cement
No matter where you are located, you benefit from our excellent industry know-how as an expert global leader. Close to your business in every step of the process, we provide timely solutions to all your needs, supporting you in mastering all your lubrication challenges throughout manufacturing and beyond.
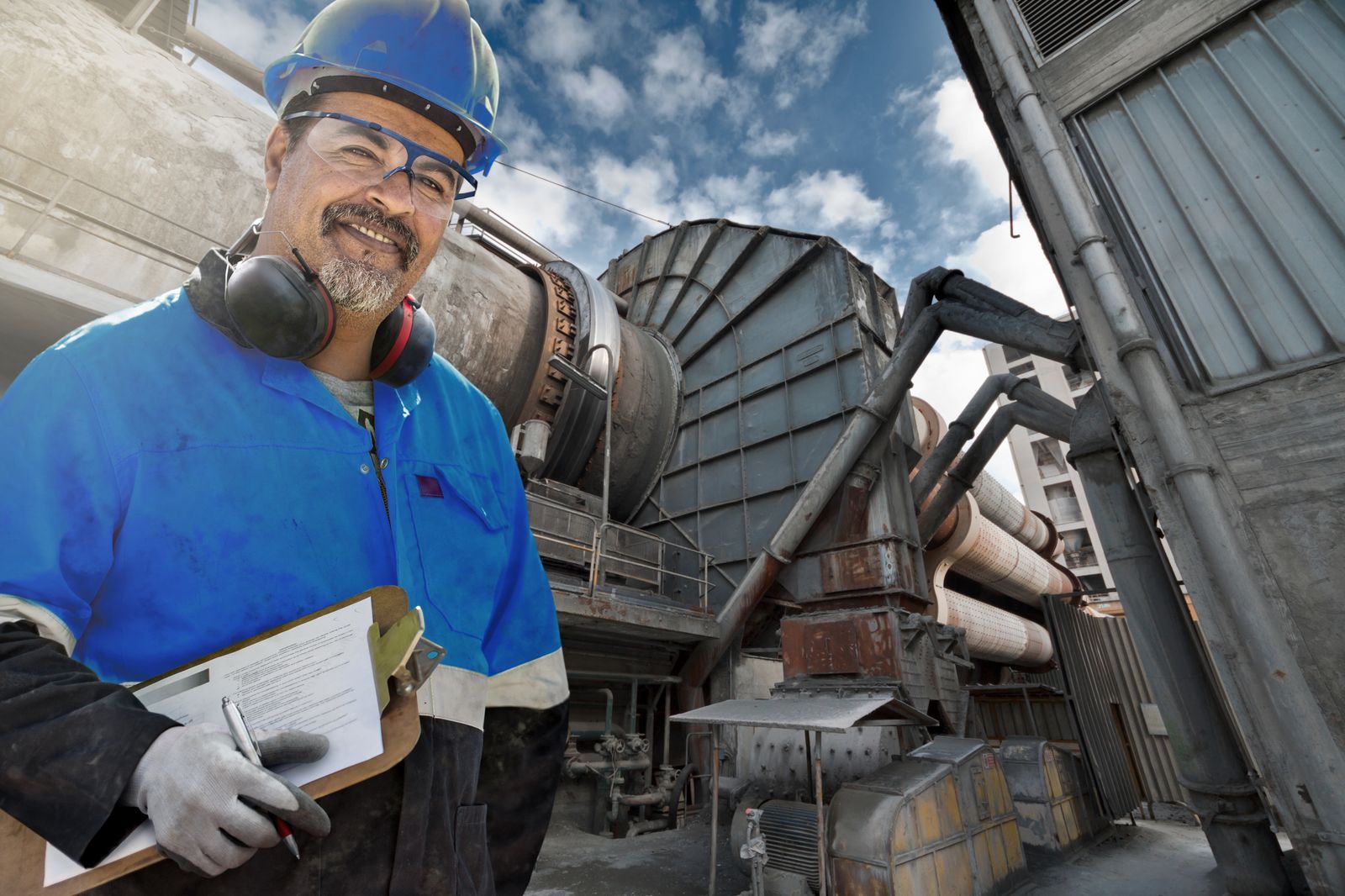
The whole scale of customer care
Your machines are exposed to a demanding environment. High-performance lubricants are crucial to your success. Ensuring maximum machine availability and productivity involves more - we are the partner to provide it. Our application specialists are on site to analyze, inspect and help to maintain your equipment. Exceptional know-how and specialized software in combination with training and advice keep your plant running smoothly. Take your business to the next level.
In Detail – Our Full-Lubrication-Package
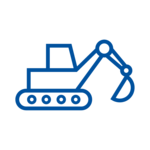
Excavators and Trucks
Excavators and trucks work in very harsh conditions. Vibration, dust load, and environmental conditions are the highest challenges facing the lubricated parts. FUCHS lubricants from the TITAN, RENOLIT, and LAGERMEISTER range offer optimum protection of pins & bushes, slewing rings, hydraulics, and the drivetrain.
Greases
Pins & Bushes:
RENOLIT CSX ULTRA 15
RENOLIT UNIWRL 2
Slewing rings:
RENOLIT CSX ULTRA 15
CEPLATTYN KG 10 HMF (gear only)
RENOLIT UNIWRL 2
Oils
Hydraulics:
RENOLIN B Range
RENOLIN MR Range
Engines* for trucks/excavators:
TITAN TRUCK PLUS SAE 15W-40
TITAN CARGO SAE 15W-40
Engines* for passenger cars:
TITAN SUPERSYN LL 5W-40
Gears:
TITAN SUPERGEAR SAE 80W-90
Crusher
Crushing can be done by, for example, an impact crusher, a cone crusher, or hammer crusher. The bearings of these crushers are exposed to extreme vibration loads, dust, and environmental conditions. Therefore, greases with extreme working stability, extreme pressure resistance, and good sealing capabilities are to be used.
RENOLIT CXS-GSM/S fulfills these demands. Even at low temperatures, they are pumpable in central lubrication systems. RENOLIT CXS-GSM/S also ensures safe running conditions at maximum service intervals.
Dust Suppression
Especially in dry climates, the environmental impact of dust from the quarry can be immense.
A standard method to reduce dust is spraying water with a water truck. In order to reduce water consumption and to prolong spraying intervals, FUCHS developed RENOCLEAN AIR HOLD-DOWN. Designed to be diluted into water-based applications.
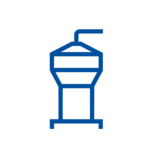
Blending Beds
No other moving parts in the cement industry are exposed to dusty environments and their highly abrasive nature as much as conveyor chains of blending beds. That causes extreme wear on chain links, chain bolts, and sprocket wheels. Chain oils with minimum dust attraction but good lubrication properties are necessary to prolong the lifetime and maintenance cycles of this equipment.
RENOLIN CHAINLUBE G 1000 provides very good creeping properties to reach and lubricate the inner chain. Friction and wear are drastically reduced. Throwoff losses are minimal. The graphite content of RENOLIN CHAINLUBE G 1000 offers excellent emergency running properties.
Vertical Mills and Grinding Rollers
Vertical mills are commonly used for raw material and clinker grinding. In terms of lubrication, the most critical parts of vertical mills are the bearings of the grinding rollers, the separator bearings, and the gearbox. The bearings of the grinding rollers are exposed to extremely high vibrations (short-time overloads), elevated temperatures, and, depending on their design, the dust-loaded environment within the grinding chamber.
RENOLIN PG 680 and 1000 were specially developed for the lubrication of such highly loaded bearings. They are based on a fully synthetic oil, thus ensuring the highest lubrication films under extreme temperatures and loads.
Vertical Mills, Separator Bearings, and Gearboxes
Separator bearings of vertical mills face a critical combination of load, revolutions, and size. In addition, they are positioned in the airstream and thus heavily exposed to increased temperatures and dust.
URETHYN MP 2 was especially developed to lubricate these bearings. It provides a good pumpability and guarantees excellent lubricity under elevated temperatures and loads.
RENOLIN CLP 320 as well as RENOLIN UNISYN CLP 320 are widely approved by the manufacturers of gearboxes for vertical mills.
FUCHS also provides fully synthetic gear oils in order to achieve oil changing intervals of up to three years and beyond. These products are RENOLIN UNISYN 320 and GEARMASTER SYN 320.

Kiln and Open Gear
Most kilns and in particular kilns with more than two roller stations are equipped with an Open Gear drive. The tooth flanks of kiln gears are exposed to radiation heat from the kiln shell and, compared to other Open Gears, are subjected to axial movements. Due to slow sliding movements between the tooth flanks, solid lubricant containing Open Gear lubricants are the optimum solution.
In general the CEPLATTYN KG 10 HMF range containing graphite as well as the light-colored CEPLATTYN GT range are the best solutions for Open Gear lubrication on kilns.
Because of their high solid lubricant content and their elevated base oil viscosity, both CEPLATTYN grades provide excellent wear protection even under critical running conditions.
Kiln, Tyre Ring
Tyre rings on kilns have to compensate the heat extension of the kiln shell, keep the kiln shell in its circular shape, and prevent the kiln from bending. As a kiln tyre is never entirely fixed to the kiln shell, it needs to be lubricated to avoid it from seizing up and wearing between the tyre pads and the tyre itself. Any moving parts of semifixed tyres have to be lubricated as well.
CEPLATTYN HT is the most reliable lubricant for this task. It is easy and safe to apply using conventional spray units. The product penetrates into the inner tyre ring, its base fluid evaporates slowly, and the high content of solid lubricants stays in the tyre for safe, long-term dry film lubrication.
Traveler Grate/Cooler
Depending on its design, a traveler grate can be equipped with many bearings operating under exposure to the radiation heat from the hot clinker. To keep these bearings running, high volumes of standard greases have to be used. However such greases fail frequently because they harden in the feeding lines.
RENOLIT CXS CCG 2 was especially developed to meet these requirements. It will not harden under elevated temperatures; its high-temperature thickener system combined with its increased base oil viscosity guarantees reliable lubrication with a minimum amount of grease.
In addition, RENOLIT CXS CCG 2 is used as a high-performance multipurpose grease for all considerably thermally loaded bearings.
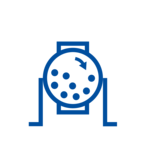
Roller Press
Roller presses are used for raw material preparation and finish grinding. The high-pressure grinding bed built between the two rollers leads to a significant reduction of energy consumption compared to common ball mills. Bearings of roller presses are subject to extremely high shock loads and, especially in the finish-grinding process, to elevated temperatures. In terms of lubrication, grease-lubricated bearings have to be distinguished from oil-lubricated bearings.
In grease-lubricated bearings, the grease is fed in relatively high volumes using conventional lubrication systems. The high volumes are necessary to provide a sufficient sealing effect on the bearing to prevent the backflow of dust from the grinding chamber into the bearing.
Greases for the grinding bearings have to be extremely stress resistant and have to provide a good damping effect to “cushion“ the bearings. In addition to that, a good self-sealing effect is required to prevent dust backflow from the grinding chamber to the inner bearing. STABYL HD is the most suitable and widely approved lubricant for these bearings. Its high base oil viscosity and its content of solid lubricants provide the ideal combination for these extremely challenging conditions.
Oil-lubricated bearings are equipped with a fully sealed circulation system. GEARMASTER SYN is the synthetic oil for these systems.
Ball Mill
Even though ball mills are gradually being replaced by vertical mills and roller presses, they are still the most common grinding systems in today’s cement plants. The majority of ball mills are driven by Open Gears. Some have central drives or enclosed gear/bearing arrangements.
CEPLATTYN is the first choice for spray, bath, and circulation lubrication of Open Gears. It is available as black graphite containing grease, light-colored fluid, or as fluid with white reactive solid lubricants.
The entire CEPLATTYN range is the life insurance for an Open Gear drive. For mills driven by central-gear drives or closed-gear arrangements, the GEARMASTER CLP range and the RENOLIN CLP are the widely approved choice.
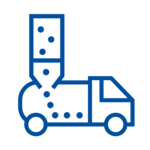
Silos/Packaging/Loading
Within the cement storage and packaging section, different machine parts need to be lubricated. Silos are equipped with small, open running-gear drives for the discharging unit. They have to be lubricated by CEPLATTYN BL if applied via automatic greasers, or by CEPLATTYN 300 if applied manually.
Bearings and conveyors and various parts of bag packaging machines are to be lubricated with an extreme pressure (EP) grease such as RENOLIT UNIWRL 2.
RENOLIT CSX ULTRA 15 provides a state-of-the-art multi purpose option. Its stable thickener system and elevated base oil viscosity allow RENOLIT CSX ULTRA 15 to be widely used as a multipurpose grease within a cement plant where moderate to high temperatures or medium to high loads are to be covered. It is compatible with most other greases.
Bearings in general (Grease Lubricated)
For the general lubrication of bearings and as a general-purpose solution for a wide range of applications in a cement plant, RENOLIT CSX ULTRA 15 is the optimum solution. Its stable thickener system and its compatibility with most other greases allow its use in most bearings.
The standard extreme pressure grease RENOLIT UNIWRL 2 provides a good solution for low- to medium-loaded bearings.
Gears in general
FUCHS covers the complete range of industrial gear oils based on mineral oils and synthetic base oils (poly-alphaolephine, polyalkylene glycol, and ester).
RENOLIN and GEARMASTER gear oils ensure the latest additive technology and are approved by key gear manufacturers and bearing manufacturers as well as component and machine manufacturers within the cement industry.
With its latest development, RENOLIN UNISYN provides the most advanced technology for energy savings and extended oil changing intervals.
In Detail – Our Full-Solution-Package
Regular Inspection of Open Gears
For Open Gear units, our service engineers carry out regular inspections over the entire service life. All findings are saved in the FUCHS LUBRICANTS INSPECTOR, an online documentation system where data, trends, and comments are available at any time.
This consists of, for example:
- Measuring vibrations of pinion bearings
- Dynamic check of contact patterns
- Measuring tooth flank temperatures
- Video thermography
- Checking lubrication system
Extended Service
Repair and optimization of damaged tooth flanks on Open Gear drives is part of the extended service offered by FUCHS. Such work is primarily a matter of the mechanical treatment of the working tooth flanks by grinding pittings, smoothing scuffings, and forced running-in and assistance with alignment of the transmission gears. On heavily worn-out or damaged tooth flanks, FUCHS provides complete re-profiling of the entire gear set.
Academies
In-house and on-site seminars for:
- Basics of lubricants
- Basics of lubrication systems
- Calculation of lubrication volumes and intervals
- Root causes of gear and bearing damage
- Oil and grease sampling/reading of analysis
Survey
On-site lubrication and application survey in order to:
- Improve current lubrication routine
- Reduce number of lubricants
- Reduce lubricant consumption
- Optimize lubricant storage
- Reduce cost of lubrication
Analysis
CENT oil analysis
- State-of-the-art preventive maintenance tool
- Indicates, for example, wear additive level, and source of contamination
Management
Inventory/procurement management*
- Provide consignment stock (inventory management)
- Procurement and purchasing of all lubricants
- Reduction of lubricant variety
- Centralized organization of all documents
*All services subject to local conditions and in consultation with local FUCHS entity
Repair Service
Open Gear repair
- Pitting grinding
- Assistance in alignment
- Re-Profiling
Monitoring
On-Site Machine Monitoring
- Check environment
- Check lubrication systems
- Monitor temperatures and vibrations
- Documentation and Trending
Software
CENT oil analysis
- Condition data
- Recommendations
- Trends
FUCHS LUBRICANTS INSPECTOR
- Condition check of Open Gears
- Vibrations/temperatures
- Infrared images/videos
- Trends
- Recommendations