Mining and exploration
FUCHS has been a trusted partner of the global mining industry for more than 90 years. Our comprehensive range of lubricants for every mining application meets even extreme demands. Continuous product development and optimization underline our mission to achieve technical perfection.
As part of our commitment to technical excellence, we continually develop new products and optimize existing products to better serve your mining needs. Maintenance costs and breakdowns are reduced, and maximized up-time allows productivity increases and optimal value for your equipment.
FUCHS is uniquely qualified to be a true global partner with a focus on globally-controlled, company-owned local manufacturing and distribution coupled with a global support network to meet your specific mining needs.
Download our Brochure
Mining Services
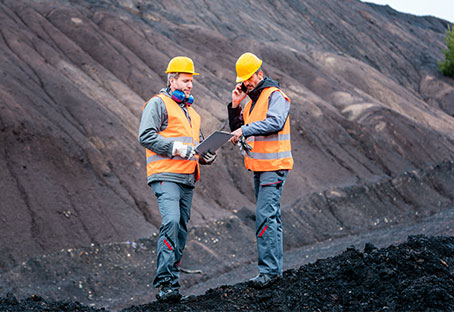
Our local experts contribute through their broad process-spanning expertise and on-site technical consultation to the performance, efficiency and process reliability of your entire application.
Knowledge: the key to success
We gain your trust through our expert lubricant knowledge, broad industry knowledge and comprehensive technological expertise. Together we strive towards 100% solutions for you.
To do so we practice a corporate culture of openness and an intensive, interdisciplinary exchange of views.
All process industries use lubricants as part of an effective preventative maintenance strategy. FUCHS can assist by providing an effective lubrication schedule designed to maximize the efficiency of plant and equipment.
Each lubrication survey is conducted with one simple principle in mind: achieving the FUCHS vision. Increasing control and technology, reducing complexity and cost through a plant review can:
- Improve plant productivity through lubricant technology
- Reduce risk
- Rationalize usage
- Control re-lubrication intervals
- Minimize down time
- Assist with audit compliance
- Minimize admin and maintenance tasks.
Each survey can include:
- A review of all the plant lubrication requirements
- A detailed photographic/ visual survey of the full mining facility
- A customized information folder
- Color coded identification of all lubrication points
- Recommendations for condition monitoring schedules
- Options for use of energy saving lubricants.
To assist our customers, FUCHS provides a number of plant management solutions, including storage and handling equipment, dispensing equipment, labeling of lubrication points and guidance on how to manage waste disposal.
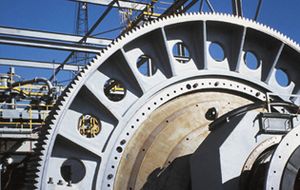
One of our core competencies is the inspection, maintenance and repair of open large gears in the primary industry. All over the world, experienced service engineers assist with the commissioning and running-in of plants and perform regular inspections over their entire lifetime. Thanks to the comprehensive service package in conjunction with our adhesive lubricants, running times of more than 40 years are possible.
Running-in of new Open Gears
Specially trained service engineers assist with the commissioning and running-in of the plant. They ensure that the drive is run-in optimally according to the principle of the MULTI-PHASE-LUBRICATION (M-P-L) with accurately defined application quantities of the appropriate CEPLATTYN adhesive lubricant.
Inspections – regular and free
For drive units that are lubricated with CEPLATTYN, our service engineers carry out regular inspections over the entire service life. They make written notes of the general operational status, ascertain the amount of wear on the load-carrying tooth flanks, check the spray lubrication and, if necessary, re-set it. In addition, the service engineer performs extensive measurements (oscillation speed, flank temperature etc.), which are recorded in the FUCHS LUBRICANTS INSPECTOR, a modern documentation system, and are always available to our customers.
Repairs in the case of damage
Our service engineers will help you with their know-how in any case of damage. We assist you with the search for the cause, the repairs, and with the restart.