Mining Roundtable: Mining Lubrication Challenges in 2024 and Beyond
We asked four of our mining experts your thought-provoking questions about the trends affecting the mining industry, how lubricants can help address them, and how you can get the most out of your lubrication plan.
Why is it important to work with a comprehensive lubrication solutions provider?
“When finding solutions for our customers it is critical to focus on more than just the lubricant. It is important that our mining sales and service representatives have practical operation and equipment knowledge. While the lubricant is the lifeblood of any piece of equipment, it is only one part of an extremely complicated system and operation. With a thorough knowledge of the operational expectations as well as the mechanical, hydraulic, and electrical systems, FUCHS can provide holistic solutions.
FUCHS aims to optimize our customers' productivity, availability, cost savings, and equipment lifecycle through a comprehensive, solutions-based strategy. Combining application-specific lubricants with our wide range of industrial solutions allows our team to develop a plan that aligns with our customer’s needs and expectations. We also offer a variety of services including lab analysis, equipment audits, training, filtration, new lubricant system installation support, condition monitoring, and more. Maintaining a single source supplier allows for a streamlined approach to customer service and supply chain management.”
"Maintaining a single source supplier allows for a streamlined approach to customer service and supply chain management.”
- Chris Mancini, Sales Director (Mining)

How have record-high temperatures impacted the mining industry and its lubrication requirements?
When is it appropriate to use a mineral oil-based lubricant and when should a synthetic-based lubricant be used?
“Higher operating temperatures increases wear potential on equipment. This can negatively impact equipment reliability and potentially increase in-use oil oxidation, resulting in shorter service intervals and higher sludge and varnish potential. Mining equipment therefore requires high efficiency lubricants that can handle wide operating temperatures.
In most cases OEMs recommend fluid viscosities and chemistries such as base oil type. Mineral oils are recommended for narrower operating temperature and ‘normal’ service intervals whereas synthetic based lubricants are recommended for much wider and extreme operating temperatures and significantly extended service intervals.”

"Mining equipment requires high efficiency lubricants that can handle wide operating temperatures.”
- John Perez, Product Manager (Industrial Oils)
Should all mining engines use OEM-approved oils?
Using OEM-approved oils for heavy-duty equipment engines in mining operations is highly recommended for several reasons.
First, there is protection and compatibility to consider. OEM-approved oils have undergone rigorous testing to meet the specific requirements set by the equipment manufacturer. This ensures that the oil provides optimal performance and protection for the engine.
Then there is OEM warranty compliance to think about. Using non-OEM-approved oils can sometimes void the equipment’s warranty. Manufacturers often require the use of approved oils to maintain warranty coverage.
OEM-approved oils also offer enhanced performance. These oils are formulated to work best with the specific engine design, leading to better performance, efficiency, and equipment longevity.
In demanding environments like mining, equipment reliability and safety are paramount. Using the right oils helps prevent breakdowns, reduces the risk of accidents, and decreases equipment downtime.
While some oils that meet the specifications might be suitable, OEM-approved oils provide an additional layer of assurance and peace of mind.”
"In demanding environments like mining, equipment reliability and safety are paramount. Using the right oils helps prevent breakdowns, reduces the risk of accidents, and decreases equipment downtime."
- Fatih Yucebilgic, Product Manager (Automotive)
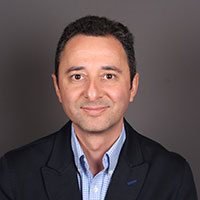
How can I maximize the performance and availability of my open gear systems?
Maximizing the performance and availability of open gear systems in mining requires a tailored approach due to the demanding and harsh operating environment.
Selecting a high-performance lubricant is key. In mining, gears are exposed to heavy loads, dirt, and moisture. The CENTAK OG and CEPLATTYN Series are specifically designed for high-load and high-contamination environments. These lubricants can be used in automatic lubrication systems to ensure consistent and optimal lubrication, reducing the risk of human error and downtime. Dust suppressants, temperature management systems, and other environmental controls can also help prevent contamination and premature lubricant degradation.
It’s important to get ahead of issues before they arise. Regular monitoring, oil analysis, and predictive maintenance help identify potential issues early, allowing for timely corrections to prevent failures and avoid unexpected downtime. FUCHS can assist by providing an oil analysis program designed to maximize the efficiency of your plant and equipment.
To minimize wear and extend the life of your open gear systems, its crucial to ensure gears are properly aligned and the load is distributed evenly. These areas should be evaluated regularly. If damage occurs, service engineers from FUCHS Application Engineers can assist you to identify the root cause. Lubricant storage and handling is just as important as the lubricant itself. Our team at FUCHS can also train your staff on best practices and standard operating procedures.
By implementing these elements, customers can significantly improve the performance and availability of open gear systems in their mining operations, leading to reduced downtime, lower maintenance costs, and enhanced operational efficiency.”

"It’s important to get ahead of issues before they arise. Regular monitoring, oil analysis, and predictive maintenance help identify potential issues early, allowing for timely corrections to prevent failures and avoid unexpected downtime."
- Kashif Zia, Product Manager (Grease)