How to keep your parts in good condition with In-Process Corrosion Protection - Part 2 of 2-
We previously discussed that it’s often necessary to store parts between manufacturing operations and prior to assembly. Protecting parts from corrosion during storage is critical to maintaining process integrity and avoiding costly rework or scrap. In Part 2 of this series we discuss how to protect metal parts between manufacturing operations and assembly.
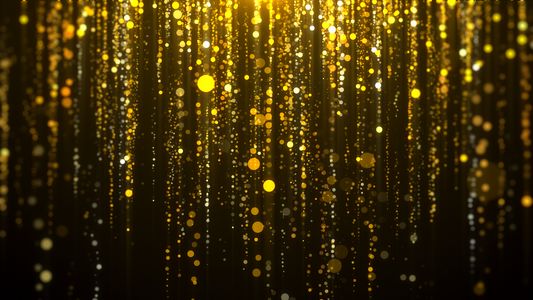
What are the storage conditions?
Not all indoor storage conditions are alike. Many parts of the country experience high humidity during the day and cool nights during certain seasons. In these conditions, warehouse workers often open roll doors to cool the building on cool nights. In doing so, the cool air may cause condensation of water from the humid indoor air onto any and every available surface – including parts stored near the open doors. Many corrosion preventives will protect against multiple condensation cycles. However, when the process is repeated night after night, week after week, the corrosion protection is challenged.
In these conditions, a workable solution is to use a fluid designed for the high end of the intended storage period – for instance using a fluid intended for 6-12 months for a 3-6 month protection period. Although the corrosion protection cost may be slightly higher, it is valuable insurance against warehouse condensation cycles.
Storage in coastal areas presents additional challenges. Unless indicated otherwise, most industrial corrosion preventives have recommended storage periods based on indoor, non-coastal storage, meaning no exposure to salt air. Coastal areas require that fluids intended for the high end of the intended protection period be used, or that additional measures such as VCI be taken.
How will the corrosion protectant be applied?
Solvent based and oil based fluids are typically applied by dip, drip or recirculating spray. Application decision points relate to two main areas:
Are the incoming parts wet or dry?
If the parts enter the application system wet with water, or cleaning solution, then ‘water displacing’ properties are advantageous. This means that the corrosion preventive has an extremely high affinity for metal surfaces and will push water away in order to coat, thereby eliminating water from the metal. A typical application requiring water displacement is steel tube manufacturing, where the protectant is often dripped onto wet tubing as it exits the mill. The protectant must migrate from point of dripping onto the tube, around the circumference, displacing water or metalworking coolant in the process in order to permit tight bundling and banding of the finished tube without trapping water.
Incoming dry parts will not benefit from water displacement properties.
Water separation properties are advantageous for dip or recirculating spray applications using wet parts. This property permits the water or cleaner to separate by gravity to the bottom of the tank, where it can be drained, maintaining clean corrosion preventive.
What happens next?
Consideration must be given to the disposition of the parts after storage. If they will be cleaned, the cleaning system must be sufficiently robust to remove the protectant. Water based, solvent based, and oil based fluids are easily removed in alkaline cleaning systems, bearing in mind, that oil load on the cleaner will increase with higher oil content protectants.
If the protectant is to be left on the parts, is it compatible with subsequent processing or ultimate use of the product? Will the product be painted or welded? If it is to be directly assembled without washing – are there other materials in the assembly that must be compatible with the residue?
Finally, what if the part is to be shipped outside of the US? Does the foreign customer require the corrosion protection residue to comply with their local EHS regulations in addition to our US regulations?
FUCHS global product ranges, including ANTICORIT DFO, ANTICORIT DFW, ANTICORIT BGI, have been designed to meet all major global country requirements and are available in most countries. Local products designed to meet domestic requirements are also available.
Summing it up
These are the basic considerations in selection of a corrosion protectant for metal part storage. Your FUCHS representative can assist with selection considering all of your unique requirements. Feel free to contact us at any time.
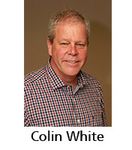
Subscribe to our blog
All Blog Posts
- Lubricants & Technology – SOLCENIC Success
- What you need to know about Food Safety Modernization Act (FSMA) and Lubrication
- Part 2 - How to keep your parts in good condition with In-Process Corrosion Protection
- How to keep your parts in good condition with In-Process Corrosion Protection
- Four rules of thumb in lubrication – your shortcut to savings!
- A gaze into the world of cutting fluids
- When lubricants ‘get chatty’
- Did you know…? About hydraulic fluids
- Did you know…? About vehicle lubrication
- The rapidly evolving automotive industry
- Higher productivity and profitability in four stages
- Ten tips that deliver big time