What is the Stribeck Curve?
The terms boundary, mixed, and hydrodynamic lubrication are commonly recognized in the lubrication industry, but what is the Stribeck Curve, and how does it relate to these lubrication regimes? The Stribeck Curve is a graphic depiction that highlights how friction (Y-Axis) and sliding speed (X-Axis) relate to the type of lubricating film that forms under varying loads and temperatures. The sliding speed is a function of the viscosity of the fluid (Z), the speed of sliding (N), and the pressure (P) applied between the two surfaces. The term ZN/P is equivalent to the lubricant film thickness. Film strength as well as film thickness decreases with increased pressure and increases when velocity and viscosity increase.
The formation of these films depends on the extent of surface contact, which determines the lubrication regime.
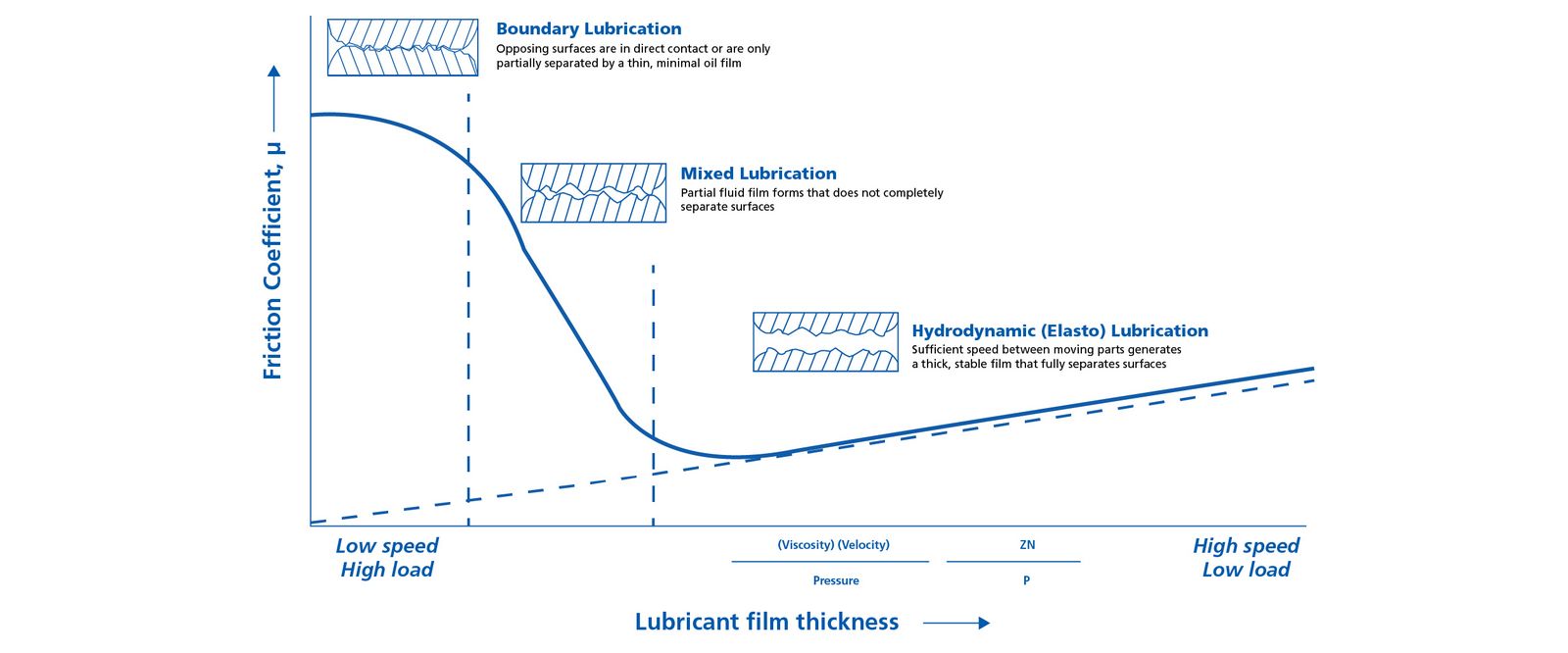
What are the Different Lubrication Regimes?
There are four distinct lubrication regimes
1. Boundary Lubrication
During boundary lubrication, opposing surfaces are in direct contact or are only partially separated by a thin, minimal oil film. In this state, surface asperities (microscopic rough spots) may come into direct contact, but damage to the surfaces is minimized by the presence of protective additives in the lubricant. These additives form a thin, protective layer that reduces the likelihood of surface asperities "welding" together, ensuring smooth sliding and preventing wear. Boundary lubrication is common in situations where machines operate under slow speeds (like during start-up or slow down), high pressures, or both.
2. Hydrodynamic Lubrication
Whereas in boundary lubrication the lubricant/additives have an affinity for metal surfaces that provides a boundary layer between the metal surfaces, in hydrodynamic lubrication there really is no affinity to metal. Hydrodynamic lubrication occurs when there is sufficient speed between the moving parts to generate a thick, stable film of lubricant that fully separates the surfaces. In this regime, the pressure exerted by the fluid film is strong enough to prevent contact between the asperities of the surfaces, effectively reducing wear and friction.
Hydrodynamic lubrication is most commonly found in high-speed applications, such as engines or turbines, where the relative velocity between parts creates the necessary conditions for the fluid film to maintain separation. This regime is typically associated with lower friction and minimal wear.
Whereas as in boundary lubricant/additives have an affinity for metal surfaces that provides a boundary layer between the metal surfaces, in hydrodynamic lubrication there really is no affinity to metal. Instead, the viscosity of the fluid provides a separation between the metal surfaces similar to the fluids between the joints in our body.
3. Mixed Lubrication
Mixed lubrication occurs in the transitional zone between boundary and hydrodynamic lubrication and provides benefits from both regimes. In this regime, both boundary lubrication and hydrodynamic lubrication are present at the same time. At moderate speeds and loads, a partial fluid film forms, but it is not thick enough to completely separate the surfaces. As a result, the asperities of the surfaces may intermittently come into contact, causing some level of friction and wear. For example, with hydraulic oils, the viscosity is important for the hydrodynamic between pistons and the cylinders, and the anti-wear additives (zinc, phosphorous, nitrogen, etc.) provide the boundary lubrication due to attraction to the metal surfaces.
Mixed lubrication typically occurs during the acceleration or deceleration phases of machinery operation, when the conditions fluctuate between the two extreme regimes.
4. Elastohydrodynamic Lubrication
Elastohydrodynamic lubrication occurs under high-pressure conditions, where the lubricant film becomes extremely thin. However, despite the reduced thickness, the film still prevents direct contact between the surfaces. In this regime, the lubricant undergoes a significant change in viscosity due to the high pressure, and the surfaces may undergo elastic deformation due to the load. The film is thin but effective in maintaining separation and reducing wear, even under extreme conditions. Elastohydrodynamic lubrication is often observed in situations involving rolling contact, such as in gears and bearings, where both high pressures and high velocities are present.
How Can the Stribeck Curve Be Used to Optimize Lubrication?
By analyzing the Stribeck curve, engineers and suppliers can optimize lubricants to enhance efficiency and reduce wear.
Screening Lubricants for Optimal Performance: Helps assess if lubricant will provide protection at specific speeds and friction levels. Indicates conditions where lubricant prevents direct surface contact to maintain machine longevity.
Identifying Failure Points & Adjusting Formulations: Highlights when fluid film becomes too thin, leading to increased friction and wear. Adjustments to the viscosity, additives, and other properties can be made to maintain an effective film and optimal protection.
Guiding Lubricant Selection Based on System Requirements: Helps suppliers tailor lubricant recommendations based on the machine's speed, load, and temperature.
Proactive Prevention of Wear and Tear: Engineers can adjust machine operation (e.g., speed or load) to maintain the ideal lubrication regime, reducing wear, improving performance, and lowering maintenance costs.